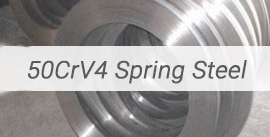
فروسیلیس و کاربردهای آن
سیلیسیم (Si) پس از اکسیژن فراوانترین عنصر روی کره زمین است که در طبیعت به صورت کوارتز یافت میشود. از این عنصر آلیاژها و فروآلیاژهای مختلفی ساخته شده که هر کدام با توجه به ترکیب شیمیایی کاربردهای مختلفی پیدا کردهاند. فروسیلیس یا فروسیلیسیم (Ferrosilicon) یکی از این آلیاژهاست که در این مقاله سعی داریم تا شما را با خواص این فروآلیاژ و نحوهی انتخاب یک فرو سیلیس مرغوب آشنا کنیم.
فروسیلیس آمیژانی از عنصر سیلیسیم و آهن است که به منظور افزایش سیلیس در مذاب استفاده میشود و معمولا از طریق حرارت دادن، احیا و ذوب سنگ آهن و کوارتز با استفاده از کربن تولید میشود.
این فروآلیاژ بیشتر در صنایع فولاد به منظور تولید فولاد و چدن مورد استفاده قرار میگیرد و ترکیب آن نیز با توجه به نوع کاربرد آن تعیین میشود. مقدار سیلیس موجود در ترکیب فرو سیلیس بین ۱۰ تا ۹۰ درصد متغیر است و مابقی ترکیب آن را آهن تشکیل میدهد. گرچه ترکیباتی از کروم، منگنز، گوگرد، فسفر و آلومینوم نیز در این فروآلیاژ مشاهده میشود. در شکل زیر محدودهی ترکیبات سازندهی فروسیلیس را مشاهده میکنید.
فروسیلیس به چه صورتی تولید میشود؟
برای تولید این فروآلیاژ از کوره قوس الکتریکی یا کوره القایی استفاده میگردد. مواد اولیه پس از توزین و اختلاط توسط لولههای مخصوص به درون کوره شارژ میشوند. این مواد در داخل کوره تحت دمای بسیار بالا (حدود ۲۵۰۰ درجه سانتیگراد) ذوب میشوند و پس از ذوب شدن از طریق مجرای تخلیهی کوره خارج و به سمت مسیرهای ریختهگری هدایت میشوند. در نهایت پس از سرد شدن و انجماد، قطعات درشت با استفاده از سنگ شکن خرد میشوند.
در تولید فرو سیلیس از سه گروه مواد حامل سیلیسیم، مواد احیا کننده و مواد حامل آهن استفاده میگردد. فرایند تولید این آلیاژ یک فرایند بدون سرباره است و تمام عناصر موجود در مواد اولیه وارد محصول میشود. در نتیجه این مسئله اهمیت استفاده از مواد خالص را بالا میبرد. به طور مختصر به این سه گروه ماده اشاره میکنیم:
مواد حامل سیلیسیم
از کوارتز و کوارتزیت به عنوان منابع اصلی تامین سیلیسیوم یاد میشود. بیش از ۹۷% ترکیب این کانیها را سیلیس (SiO2) تشکیل میدهد. برای حذف ناخالصیها و مواد ریز، باید مخلوط اولیه شست و شو شود. دانهبندی مناسب برای فرآوری کوارتز در محدوده ۱۵-۱۰۰ میلیمتر است.
مواد احیا کننده
احیای سیلیس در کوره توسط کربن انجام میشود. برای تامین منبع کربن مورد نیاز از ترکیبی از مواد نظیر کک، زغال سنگ، زغال قهوهای و آنتراسیت استفاده میگردد. مواد کربنی مورد استفاده باید ویژگیهای زیر را داشته باشند:
- میزان خاکستر آنها کم باشد، در غیر اینصورت مقدار ناخالصی افزایش مییابد.
- استحکام مکانیکی و پایداری حرارتی بالایی داشته باشند تا در حین جابجایی و شارژ کوره خرد نگردند.
- مقاومت الکتریکی آنها بالا باشد تا بازدهی کوره افزایش یابد.
- واکنشپذیری بالایی داشته باشند تا از تلفات سیلیسیم جلوگیری شود.
مواد حامل آهن
برای تامین آهن مورد نیاز شارژ مصرفی باید از مواد حامل آهن استفاده کرد. ترکیبات آهنی مورد استفاده باید ناخالصی بسیار پایینی داشته باشند تا محصول نهایی حداقل ناخالصی را داشته باشد. برای این کار از موادی نظیر سنگ آهن با خلوص بالا، گندله، براده تراشکاری و قراضه آهن به عنوان منبع تامین آهن استفاده میشود.
کورهی قوسی تولید فروسیلیس
همانطور که در ابندای مقاله اشاره کردیم، تولید فروسیلیس توسط کورههای القایی و یا قوسی انجام میشود. در عمل کورههای قوس الکتریکی مخفی (Submerged Electric Arc Furnace) بیشترین کاربرد را در تولید سیلیسیوم و فروسیلیس دارند. به همین دلیل بد نیست مروری بر قسمتهای مختلف این کورهها داشته باشیم. برای مطالعه بیشتر درباره کورههای قوسی مطالعه مقاله کوره قوس الکتریکی را به شما پیشنهاد میکنیم.
هود (کلاهک کوره)
وظیفهی اصلی هود جمعآوری گاز و غبار متصاعد شده از سطح شارژ و انتقال آن به سمت دودکش است.
الکترود
الکترودها وظیفهی هدایت جریان الکتریکی به فضای کاری کوره و ایجاد قوس را بر عهده دارند. الکترودها به دو نوع پیشپخته و خودپز تقسیم میشوند. از الکترودهای پیشپخته به دلیل محدودیت ابعادی و قیمت بالای آن در صنایع فروآلیاژ استفاده نمیگردد. الکترودهای خودپز از کربن تشکیل میشوند و شامل پوسته فولادی بوده و در حین کار کوره آماده و پخت میشوند. قطر این الکترودها به بیش از ۲ متر نیز میرسد و قیمت کمتری نسبت به الکترود پیشپخته دارند.
سیستمهای الکتریکی
در این کورهها دو نوع سیستم تکفاز و سهفاز وجود دارد. نوع تکفاز شامل یک یا دو الکترود و نوع سه فاز دارای سه یا شش الکترود است. راندمان سیستم سه فاز بیشتر بوده و در صنعت استفاده میگردد.
بوته یا آتشدان
از نظر وضعیت قرارگیری بوته، کورههای استوانه ای الکتریکی به دو دستهی ثابت و چرخان تقسیمبندی میشوند. در کوره ثابت بدنهی کوره هیچ حرکتی ندارد و جهت تخلیه ذوب از دریچهی مخصوص استفاده میشود. اما در کوره چرخان بدنه در دوجهت و به صورت آرام میچرخد و این عمل باعث شارژ و یکنواختی شارژ میگردد. در کورههای بزرگ با قطر بوته ۱۰ متر یک دور گردش حدود ۳۰۰-۵۰ ساعت طول میکشد.
از مهمترین نکاتی که در هنگام تولید باید رعایت نمود، تلاش برای عدم تشکیل سربارهها و مواد اکسیدی است. در نتیجه باید استفاده از مواد با خلوص کم و سربارهزا را محدود نمود.
کاربرد های فرو سیلیس
- عامل اکسیژن زا از مذاب فولاد
- عامل جوانه زا در ریخته گری چدن
- تولید الکترود گرافیتی در جوشکاری
- تولید فولاد و چدن آلیاژی پرسیلیس
- تولید آمیژان فروسیلیکو منیزیم (FeSiMg) و فروسیلیکومنگنز (FeSiMn)
- عامل کنترل ترکیب شیمیایی در تخلیه مذاب از کوره به پاتیل
- عامل نشکنساز در ساخت چدن نشکن
- منبع سیلیکون در صنعت برق و مس
محصول جانبی تولید فروسیلیس
یکی از محصولات جانبی که از تولید این فروآلیاژ به دست میآید، میکروسیلیکا (Microsilica) است که مادهای بدون بو و غیرقابل احتراق بوده و خاصیت پوزولانی دارد. به ازای تولید یک تن فرو سیلیس، حدود ۳۰۰ کیلوگرم میکروسیلیکا به دست میآید که در واقع حاصل جمعآوری کیسههای سیستم غبارگیر است. این محصول در بتنسازی، صنایع دیرگداز، صنایع رنگ و پلیمر به کار میرود.
تولید فروسیلیس در ایران و جهان
تولید فروسیلیس یک فرایند دشوار است و بستگی به عوامل زیادی دارد که میتوان به تجهیزات تولیدی، تجهیزات آزمایشگاهی و و پشتیبانی، کیفیت مواد اولیه (غبار بالا، خاکستر کم، واکنش پذیری و مقاومت مکانیکی بالا)، کنترل کیفی و میزان شارژ مخلوط اولیه و عملکرد نیروی انسانی اشاره کرد.
شرکتهای Elkem نروژ و Demag SmS آلمان از شرکتهای پیشگام در تولید این فروآلیاژ در جهان هستند که بیشترین میزان تولیدی را در جهان دارند. پس از آن کشورهای چین، برزیل، روسیه و هند در تولید این محصول پیشتاز هستند.
اولین کارخانه صنعت فروآلیاژ در ایران در لرستان با ظرفیت حدود ۷۵۰۰۰ تن در سال راهاندازی شد. پس از آن کارخانه تولید فرو سیلیس در سمنان شروع به تولید نمود که ظرفیت تولید آن ۲۵۰۰۰ تن در سال است. سومین واحد تولید کننده فرو سیلیس در ایران در شهرستان ملایر قرار دارد که سالانه ۱۲۰۰۰ تن محصول تولید میکند. واحدهای دیگری نیز در اشتهارد و کاشان در حال تولید هستند.
مصرفکنندگان فروسیلیس در ایران
از مهمترین مصرف کننده این محصول میتوان به صنایع فولاد اشاره کرد که در در طول یک سال حدود ۳۸ هزار تن میکروسیلیس مصرف میکنند. پس از صنعت فولاسازی، صنایع ریختهگری بیشترین مصرفکننده این فروآلیاژ هستند.
در هنگام خرید فروسیلیس به چه نکاتی توجه کنیم؟
- فرو سیلیسهای بازار عموما در سه سایز اندازه ۰-۳ میلیمتر، ۳-۱۰ میلیمتر و ۱۰-۶۰ میلیمتر عرضه میشوند. در صنایع ریختهگری مداوم و فولاد سازی از اندازه ۶۰-۱۰ میلیمتر استفاده میشود و دانههای ریزتر برای کامل شدن انحلال در آلیاژ مناسب هستند. میزان سیلیس موجود در فروسیلیسهای بیان شده ۱۵، ۴۵، ۶۵، ۷۵ و ۹۵ درصد است.
- فرو سیلیس با توجه به درصد خلوص به ۴ دسته خلوص استاندارد (شامل حداکثر ۲% آلومینیوم)، گرید کم آلومینیوم (شامل حداکثر ۵/۰% آلومینیوم)، گرید کم کربن و گرید با خلوص بالا (حاوی Ti) تقسیم میشود.
- مقدار اکسید آهن در این فروآلیاژ باید کمتر از %۳/۰ باشد. در غیر این صورت باعث کاهش پایداری حرارتی میکروسیلیس میشود.
- رنگ فرو سیلیس به صورت خاکستری مایل به خاکستری تیره است. هر چه درصد اکسید آهن بیشتر باشد رنگ محصول تیرهتر است.
دانلود فقط با IP ایران امکانپذیر است. در صورت عدم مشاهده باکس قرمز رنگ دانلود، VPN خود را خاموش نموده و صفحه را رفرش کنید.
پسورد فایل فشرده : www.iran-mavad.com
دیدگاه کاربران