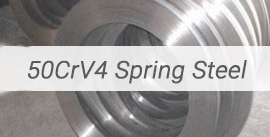
الکترود 309؛ انتخاب اول مهندسان برای اتصال فولادهای متفاوت
الکترود استیل 309 یک نوع الکترود آستنیتی با پایه نیکل-کروم است که معمولاً دارای حدود 23% کروم و 12% نیکل بوده و برای جوشکاری فولادهای متفاوت یا در شرایط حرارتی و خوردگی بالا طراحی شده است. اهمیت این الکترود نه تنها بهخاطر پایداری حرارتی و مقاومت به خوردگی بالا، بلکه بهدلیل قابلیت ایجاد اتصال با ساختارهای ناهمگون فلزی است. در اتصال فولاد زنگنزن به فولاد کربنی، الکترود 309 با ترکیب خاص خود، از ترکهای ناشی از تفاوت انبساط حرارتی جلوگیری میکند و گزینهای مطمئن محسوب میشود.
در این مقاله، ابتدا ترکیب شیمیایی و خواص متالورژیکی الکترود 309 بررسی میشود، سپس کاربردهای صنعتی و ملاحظات جوشکاری آن ارائه میگردد تا دانشجویان و مهندسان با این الکترود و اهمیت آن آشنا شوند.
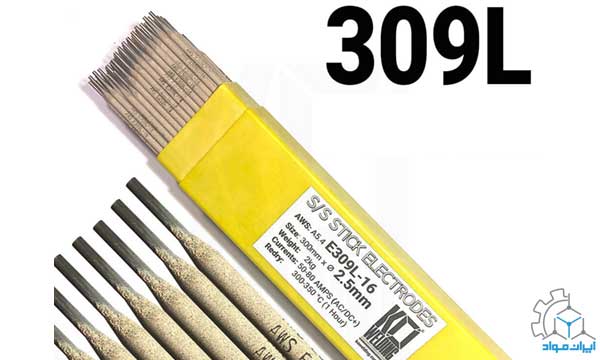
ترکیب شیمیایی الکترود 309 بر اساس استاندارد AWS A5.4
الکترودهای جوشکاری استنلس استیل نوع E309 و E309L مطابق با استاندارد بینالمللی AWS A5.4: Specification for Stainless Steel Electrodes for Shielded Metal Arc Welding تعریف شدهاند. این الکترودها برای جوشکاری فولادهای ناهمجنس، فولادهای نسوز و کاربردهای دمای بالا به کار میروند. استانداردهای AWS A5.4 و ASME SFA 5.4 مشخصات دقیق این الکترودها را تعریف میکند و کیفیت آنها را برای کاربردهای حساس تضمین میکند.
عنصر | E309 (%) | E309L (%) | نقش در جوشکاری |
کروم (Cr) | 22-25 | 22-25 | تقویت مقاومت به خوردگی و اکسیداسیون |
نیکل (Ni) | 12-14 | 12-14 | تثبیت ساختار آستنیتی، افزایش چقرمگی |
کربن (C) | ≤0.15 | ≤0.04 | کاهش خطر خوردگی بیندانهای در E309L |
منگنز (Mn) | 0.5-2.5 | 0.5-2.5 | بهبود پایداری قوس و استحکام |
سیلیسیم (Si) | ≤1.0 | ≤1.0 | افزایش سیالیت فلز جوش |
فسفر (P) | ≤0.04 | ≤0.04 | کاهش ناخالصیها |
گوگرد (S) | ≤0.03 | ≤0.03 | کاهش خطر ترک گرم |
- الکترود 309L به دلیل درصد بسیار پایین کربن، برای کاربردهایی که حساسیت به خوردگی بیندانهای (ضعف فلز در مرز دانهها به دلیل رسوب کاربید کروم در دماهای بالا)و ترک گرم وجود دارد، ترجیح داده میشود.
- در استاندارد AWS A5.4، برای برخی از الکترودهای استنلس استیل از جمله E309/E309L، حضور مقادیر جزئی مولیبدن (Mo) و مس (Cu) به صورت اختیاری (optional) در محدوده حداکثر 75% مجاز است. اگرچه این عناصر در ترکیب اصلی E309 الزامی نیستند، اما برخی تولیدکنندگان با توجه به کاربرد خاص (مثلاً جوشکاری محیط اسیدی یا خورنده)، مقادیر کمی از این عناصر را بهصورت کنترلشده در فرمولاسیون اضافه میکنند. حضور بیش از حد این عناصر ممکن است باعث تغییرات نامطلوب در ساختار فازی یا افت چقرمگی شود؛ بنابراین در محدوده مشخص استاندارد کنترل میشوند.
- مولیبدن(Mo): افزایش مقاومت به خوردگی بهویژه در محیطهای حاوی کلر یا اسیدهای کاهنده، بهبود مقاومت خزشی در دمای بالا
- مس(Cu): بهبود مقاومت به خوردگی موضعی مانند خوردگی حفرهای (pitting) و خوردگی شکافی، بهبود قابلیت ماشینکاری در برخی کاربردها
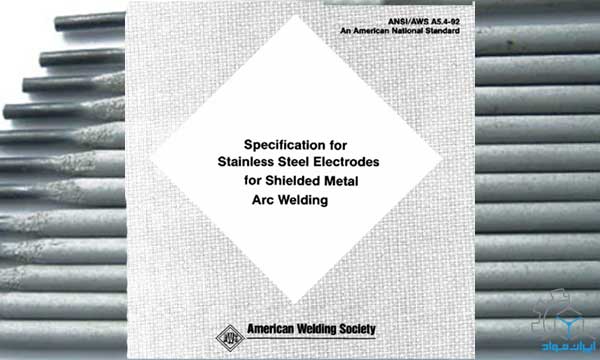
خواص مکانیکی و فیزیکی الکترود 309
الکترودهای E309/E309L در حالت جوشخورده، ساختاری آستنیتی-فریتی(ساختاری که ترکیبی از فاز آستنیت انعطافپذیر و فریت مقاوم به ترک است) (duplex-like) دارند که موجب ترکیبی از مقاومت مکانیکی بالا، چقرمگی حرارتی، و پایداری در دمای بالا میشود.
ویژگی مکانیکی | مقدار معمول |
استحکام کششی نهایی (UTS) | حداقل 550MPa |
استحکام تسلیم (Yield Strength) | حدود 350 MPa |
ازدیاد طول (Elongation) | ≥ 30% |
سختی تقریبی (Brinell) | 170 – 190 HB |
دمای کاری توصیهشده | تا 1000–1100°C (وابسته به کاربرد) |
توضیح بیشتر:
- ساختار آستنیتی با مقدار کنترلشده ای فریت δ کمک میکند تا مقاومت به ترک گرم (Hot Cracking) افزایش یابد.
- درصد کروم و نیکل بالا باعث میشود تا فلز جوش در برابر اکسیداسیون و حرارت بالا پایدار باقی بماند.
- استحکام کششی جوش در دمای اتاق مناسب بوده و در دماهای بالا نیز افت مقاومت کمی دارد.
ویژگی فیزیکی | مقدار |
چگالی | حدود 7.9 g/cm³ |
ضریب انبساط حرارتی | ~ 15.3 × 10⁻⁶ /°C (از 20 تا 100°C) |
هدایت حرارتی | حدود 14 W/m·K در دمای اتاق |
مقاومت الکتریکی ویژه | ~ 0.75 μΩ·m در دمای اتاق |
نقطه ذوب | 1400–1455°C |
نکات کاربردی:
- ضریب انبساط حرارتی نسبتاً بالا در این آلیاژ باید هنگام جوشکاری فولادهای کربنی مدنظر قرار گیرد، زیرا تفاوت رفتاری در برابر حرارت میتواند تنش حرارتی و احتمال ترک را افزایش دهد.
- مقاومت حرارتی بالا این آلیاژ را برای کاربردهایی در کورهها، صنایع پتروشیمی و نیروگاهها ایدهآل میسازد.
انواع الکترودهای فولادی کم آلیاژ برای جوشکاری قوس الکتریکی دستی
الکترود فولادی کم آلیاژ خانواده ای از الکترود جوشکاری است که برای جوشکاری قوس ال...کاربردهای صنعتی الکترود استیل 309
الکترود E309 به دلیل ترکیب شیمیایی خاص و خواص متالورژیکی ممتاز، گزینهای مناسب برای جوشکاری در شرایط سخت صنعتی است؛ بهویژه زمانی که اتصال بین فلزاتی با خواص متفاوت مورد نیاز باشد. در ادامه، مهمترین کاربردهای صنعتی این الکترود همراه با مثال عملی شرح داده میشود:
1- جوشکاری فولادهای غیرهمسان (Dissimilar Metal Welding)
الکترود 309 معمولاً برای جوشکاری فولاد زنگنزن آستنیتی به فولاد کربنی یا کمآلیاژ بهکار میرود. بهدلیل تفاوت زیاد در ترکیب شیمیایی و ضریب انبساط حرارتی این دو فلز، استفاده از فلز جوش آستنیتی با ترکیب بالای Cr و Ni (یعنی الکترود 309) باعث جلوگیری از ایجاد ترک حرارتی و افزایش دوام اتصال میشود. الکترود 309 در دماهای تا 900°C مقاومت به اکسیداسیون بالایی نشان داده و نرخ خوردگی آن در محیطهای گوگرددار کمتر از 0.1 میلیمتر در سال است (بر اساس استاندارد ASTM G31).
مثال عملی: در تعمیرات لولههای بخار در نیروگاهها که بدنه اصلی لوله فولاد کربنی (A106) و فلنج از فولاد زنگنزن 304 است، از الکترود 309 برای ایجاد اتصال مقاوم در برابر حرارت و تنش استفاده میشود.
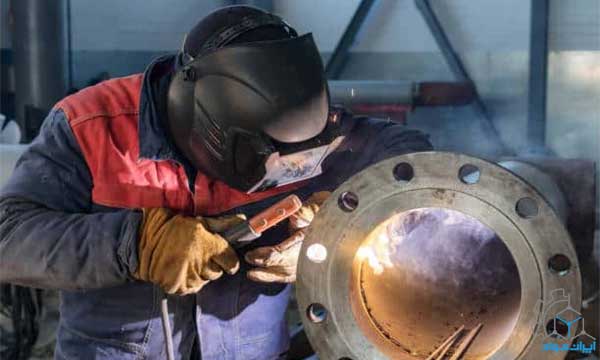
2- صنایع پتروشیمی، پالایشگاه و نفت و گاز
در بخشهایی از پالایشگاه که تجهیزات در معرض دماهای بالا، محیطهای اسیدی یا گوگرددار قرار دارند، الکترود 309 برای جوشکاری قطعات فولادی با روکش یا بخشهایی از فولاد ضدزنگ بهکار میرود. این الکترود در محیطهای اسیدی با pH بین 2 تا 4، مقاومت به خوردگی حفرهای تا 5 سال را تضمین میکند.
مثال عملی: در ساخت مبدلهای حرارتی که بدنه اصلی از فولاد کربنی و لولهها از استیل ضدزنگ (316L یا 304L) هستند، جوشکاری با الکترود 309 انجام میشود تا اتصال از خوردگی و شوک حرارتی آسیب نبیند.
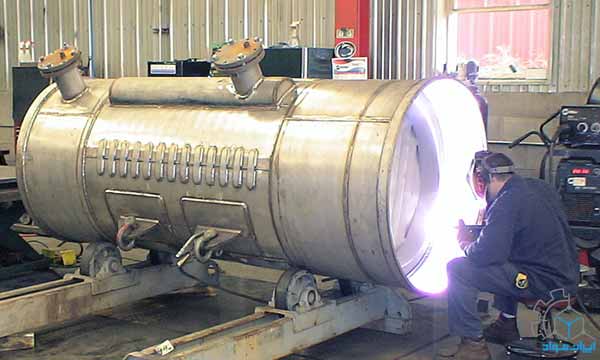
– کاربرد در صنایع نیروگاهی (دمای بالا)
الکترود 309 مقاوم به اکسیداسیون و پایداری حرارتی تا 1100°C دارد، که آن را برای جوشکاری قطعاتی که تحت دمای بسیار بالا و تنشهای حرارتی متناوب قرار دارند، مناسب میسازد.
مثال عملی: در کورههای صنعتی یا بویلرها، هنگام اتصال عایق حرارتی فولاد نسوز به صفحات فولادی معمولی، الکترود 309 انتخاب میشود تا اتصال در برابر پوسته شدن سطحی (scaling) و ترک مقاوم باشد.
4- صنعت خودروسازی و تجهیزات اگزوز
در ساخت قطعات اگزوز که ترکیبی از فولاد ضدزنگ و فولاد معمولی هستند (برای بهینهسازی قیمت)، نیاز به جوش مقاوم در برابر خوردگی گازهای خروجی و شوکهای حرارتی ناشی از سرد و گرم شدن ناگهانی وجود دارد.
مثال عملی: در اتصال فلنج فولاد معمولی اگزوز به بدنه فولاد زنگنزن لوله خروجی در خودروهای دیزلی، از الکترود 309L استفاده میشود تا دوام حرارتی و خوردگی تضمین شود.
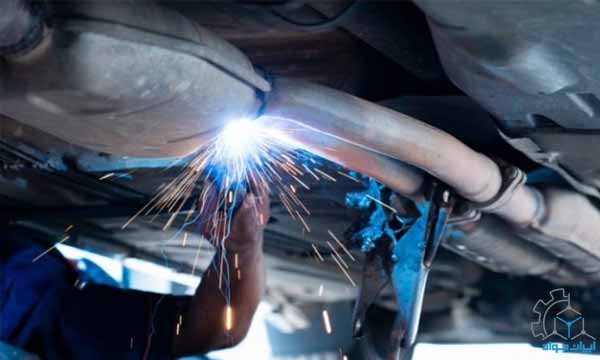
5- شرایط عملیاتی شدید (اکسیداسیون، خوردگی، شوک حرارتی)
الکترود 309 در تجهیزاتی استفاده میشود که نیاز به تحمل همزمان حرارت، خوردگی، و سیکلهای ترموشوک (Thermal Cycling) دارند؛ مثلاً در کارخانههای سیمان، شیشه، فولادسازی یا ریختهگری.
مثال عملی: در تعمیر یا اتصال مشعلهای صنعتی (burners) که بهطور مداوم دچار گرم و سرد شدن هستند، الکترود 309 بهدلیل خواص متالورژیکی پایدارش استفاده میشود.
با وجود مزایای متعدد الکترود 309، محدودیتهایی نیز دارد. هزینه تولید این الکترود به دلیل درصد بالای کروم و نیکل، گرانتر از الکترودهای 308 است. همچنین، کنترل دقیق حرارت ورودی (بین 0.8 تا 1.5 kJ/mm) برای جلوگیری از تشکیل فازهای شکننده در منطقه متأثر از حرارت ضروری است.
انواع الکترودهای فولاد ساده کربنی برای جوشکاری SMAW
بدون شک اگر شما یک مهندس متالورژ باشید، با فولادهای ساده کربنی آشنایی دارید. دست...مقایسه خواص الکترود 309 با الکترودهای مشابه (308 و 310)
الکترود 309 از نظر ترکیب شیمیایی بین الکترودهای 308 و 310 قرار دارد. الکترود 308 حاوی درصد نیکل و کروم کمتری است (حدود 20% Cr و 10% Ni) و عمدتاً برای جوشکاری فولاد زنگنزن نوع 304 و 304L به کار میرود. در مقابل، 310 دارای مقدار بسیار بالاتری از کروم (~25%) و نیکل (~20%) است که آن را برای کاربردهای در دمای بسیار بالا (تا 1200°C) و شرایط اکسیدکننده شدید مناسب میسازد.
اما 309 ترکیب متعادلی دارد (23% Cr و 13% Ni) و برای جوشکاری فولادهای غیرهمسان یا اتصالاتی که هم مقاومت حرارتی و هم قابلیت مقابله با خوردگی نیاز است، گزینهای بهینه است. بهطور خلاصه:
308 برای کاربردهای عمومی در فولاد زنگنزن مشابه،
309 برای اتصالات غیرهمسان یا حرارتی میانه،
و 310 برای دمای بسیار بالا و اکسیداسیون شدید طراحی شدهاند.
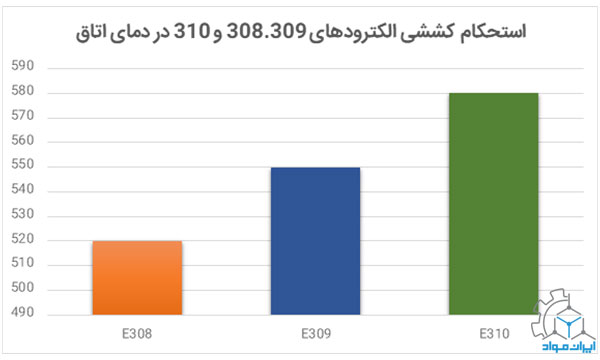
معادلهای الکترود 309 در سایر استانداردها
این تطابقها به مهندسان و کاربران کمک میکند در پروژههایی با استانداردهای مختلف (اروپایی، ژاپنی، آلمانی و…)، معادل صحیح را انتخاب کنند.
الکترود E309/E309L بر اساس استاندارد AWS A5.4 شناخته میشود، اما در استانداردهای دیگر مانند ISO، DIN، EN و JIS نیز معادلهایی برای آن تعریف شده است:
استاندارد | نوع الکترود / شماره معادل | توضیح |
AWS (آمریکا) | E309 / E309L | مرجع اصلی – جوشکاری قوس دستی |
ISO 3581 | E 23 12 L R / B | بر پایه درصد کروم و نیکل؛ L نشاندهنده کمکربن |
DIN 8556 (آلمان) | E 23 12 L- R / B20 | الکترود با پوشش روتیلی برای جوش دستی |
EN ISO 3581-A | E 23 12 L R | استاندارد اروپا، معادل دقیق E309L |
JIS Z 3221 (ژاپن) | D309-16 / D309L-16 | الکترودهای مشابه با پوشش روتیلی یا اسیدی |
UNS (شماره مواد) | S30900 / S30909 | شماره استاندارد جهانی UNS برای مواد مصرفی جوشکاری |
توجه:
- عدد 23 12 نشاندهنده تقریباً 23% کروم و 12% نیکل در فلز جوش است.
- پسوند “L” در همه استانداردها به معنی Low Carbon یا کمکربن است که برای کاهش خطر خوردگی بیندانهای و ترک حرارتی استفاده میشود.
پارامترهای مهم در فرایند جوشکاری با الکترود 309
- نوع جریان و قطبیت مناسب: الکترودهای E309 و E309L برای جوشکاری دستی (SMAW) طراحی شدهاند و میتوان آنها را هم با جریان متناوب (AC) و هم با جریان مستقیم با قطبیت مثبت (DC+ یا DCEP) استفاده کرد. با این حال، در بیشتر کاربردهای صنعتی، جریان مستقیم با قطبیت مثبت (DCEP) ترجیح داده میشود؛ زیرا باعث نفوذ بهتر جوش، قوس پایدارتر و تشکیل گل (slag) کمتر میشود.
- تمهیدات پیشگرم و پسگرم: برای فولادهای زنگنزن معمولاً پیشگرم توصیه نمیشود مگر در موارد خاصی که پایهی کار فولاد کربنی یا ضخیم باشد؛ در این حالت، پیشگرم 100–150°C ممکن است لازم باشد برای جلوگیری از ترک ناشی از شوک حرارتی.
پسگرم یا عملیات تنشزدایی نیز معمولاً انجام نمیشود، زیرا میتواند باعث رسوب کاربید کروم در مرز دانهها و کاهش مقاومت خوردگی بیندانهای شود، مگر آنکه فولاد پایه خاص باشد یا شرایط طراحی ایجاب کند. - پدیدههای متالورژیکی مهم حین جوشکاری
- تشکیل میکروترکها (Microcracks): در مناطق متاثر از حرارت (HAZ) مخصوصاً در اتصالات فولاد کربنی به زنگنزن، در اثر تنشهای حرارتی و ترکیبهای ناهمگن ممکن است ترکهای ریز بیندانهای ایجاد شود. انتخاب درست پارامترهای حرارتی و استفاده از الکترود 309L (کمکربن) میتواند این خطر را کاهش دهد.
- نفوذ حرارتی زیاد (Heat Input): اگر حرارت بیش از حد باشد، باعث گسترش بیش از حد منطقه HAZ و رسوب فازهای ثانویه در جوش میشود که خواص مکانیکی و مقاومت خوردگی را کاهش میدهد. بنابراین باید از پاسهای نازک و کنترل نرخ حرارت ورودی استفاده شود.
- تشکیل فاز فریتی کنترلشده (δ-ferrite): مقدار کم فریت δ در فلز جوش کمک میکند از ترک گرم (Hot Cracking) جلوگیری شود. کنترل ترکیب شیمیایی برای حفظ حدود 5–10% فریت در ساختار جوش مطلوب است.
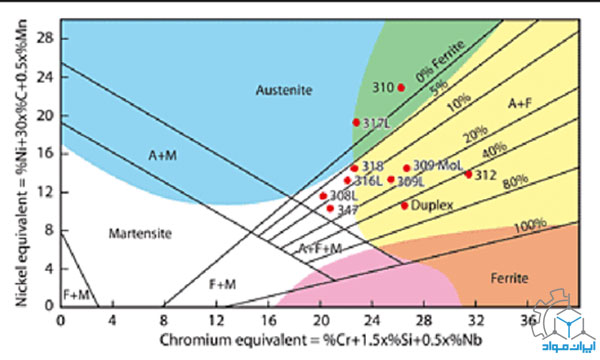
نمودار فازی Schaeffler برای پیشبینی ساختار فلز جوش در فولادهای زنگنزن طراحی شده است. این نمودار بر اساس ترکیب شیمیایی (معادل کروم و نیکل) مشخص میکند که فلز جوش پس از انجماد چه فازهایی خواهد داشت. نقطه مشخصشده مربوط به الکترود 309 در ناحیه “آستنیت + فریت” قرار دارد. این ترکیب ساختاری باعث میشود جوش حاصل علاوهبر پایداری حرارتی بالا، در برابر ترک گرم نیز مقاوم باشد و چقرمگی خوبی از خود نشان دهد.
شاید علاقمند باشید:
انواع الکترود جوشکاری و کاربرد آنها
نتیجهگیری
الکترودهای استیل 309 به دلیل ترکیب شیمیایی متعادل و خواص مکانیکی برجسته، گزینهای مناسب برای جوشکاری فولادهای غیرمشابه و کاربردهای صنعتی در دماهای بالا هستند. مقاومت بالای آنها در برابر خوردگی بیندانهای و استحکام کششی 550-650 مگاپاسکال، این الکترودها را برای صنایع پتروشیمی و تولید انرژی مناسب می کند.
در مقایسه با الکترودهای 308 و 310، الکترود 309 تعادل بهتری بین مقاومت حرارتی و جوشپذیری ارائه میدهد، اما نیاز به کنترل دقیق پارامترهای جوشکاری دارد. با این حال، حساسیت به ترک حرارتی (به دلیل تفاوت ضریب انبساط حرارتی در جوشکاری غیرمشابه) و مقاومت ضعیف در برابر کربوریزاسیون (نفوذ کربن در دماهای بالا) باید در طراحی و کاربرد این الکترودها مدنظر قرار گیرد.
از دیدگاه مهندسی مواد، الکترود 309 بهدلیل پایداری ساختاری و رفتار قابل پیشبینی در شرایط پیچیده، نقشی کلیدی در پیشرفت فناوریهای نوین جوشکاری ایفا میکند. استاندارد ASTM A262 برای ارزیابی مقاومت به خوردگی بیندانهای الکترود 309 استفاده میشود و کیفیت آن را در محیطهای خورنده تضمین میکند.
تحقیقات ارائهشده در کنفرانس TMS 2023 (Smith et al., Abstract SPG-29) پتانسیل این الکترودها را در کاربردهای نوین مانند تولید افزودنی (ساخت قطعات با چاپ سهبعدی فلزی) نشان دادهاند. آینده این الکترودها به توسعه آلیاژهای جدید با مقاومت بالاتر در برابر کربوریزاسیون و استفاده از فناوریهای نوین مانند جوشکاری قوسی با افزودنیهای نانویی وابسته است.
دیدگاه کاربران