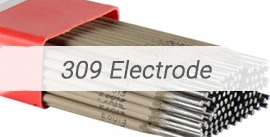
“فولاد” چیست؟ چه انواعی دارد؟
فولاد از چه چیزی درست شده؟
فولاد را در گذشته به صورت آلیاژی از آهن و کربن توصیف می کردند اما امروزه بر اساس تعریف استاندارد، فولاد ماده ای است که مقدار آهن در آن از هر عنصر دیگر بیشتر است و عموما میزان کربن آن کمتر از ۲ درصد بوده و نیز شامل عناصر دیگری باشد. تعداد محدودی از فولادهای کروم دار ممکن است بیش از دو درصد کربن داشته باشند اما ۲ درصد کربن، مرز بین فولاد و چدن است.
7 تفاوت اساسی فولاد و چدن
بسیاری از افراد تصور میکنند چدن و فولاد تفاوت چندانی با یکدیگر ندارند و صرفاً ن...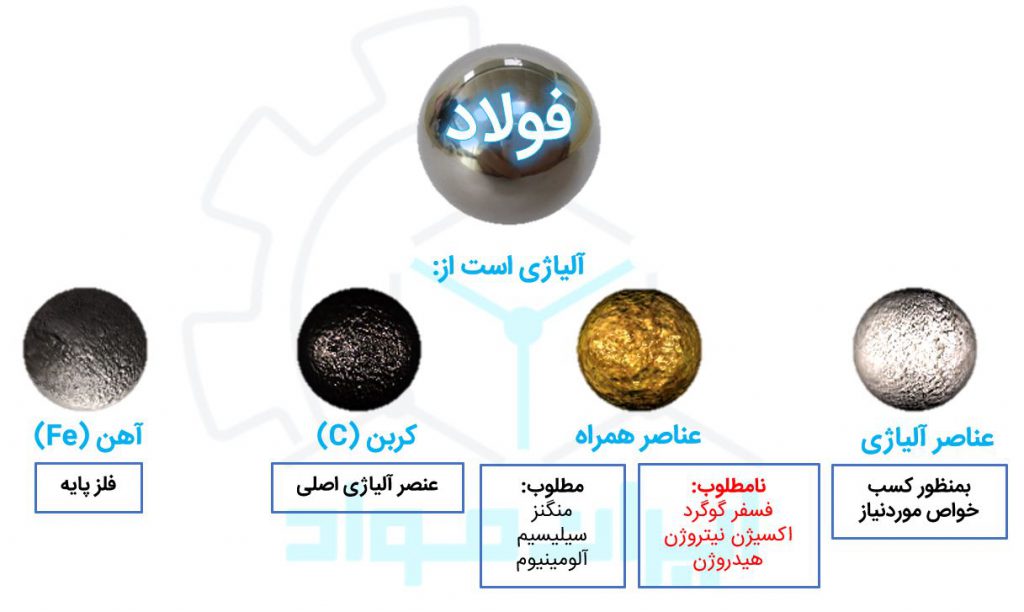
اهمیت فولاد
هم اکنون بیش از ۹۰ درصد تولید جهانی فلزات به فولاد اختصاص دارد و ویژگی های منحصر به فردش مانند: استحکام، نرمی، انعطاف پذیری، قیمت مناسب و قابلیت بازیافت آن را به فلزی بدون جایگزین و بی رقیب تبدیل کرده است. اینها دلایلی هستند تا همانطور که در نمودار زیر آمده است، تولید فولاد همواره روندی افزایشی داشته باشد.
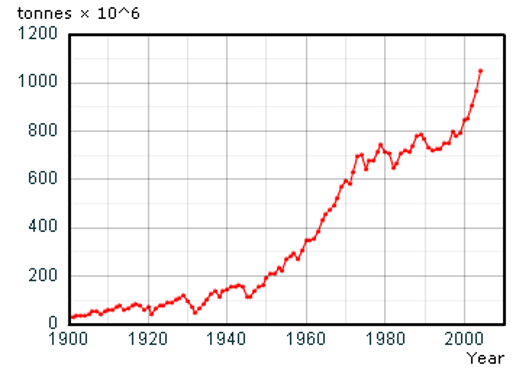
تاریخچه فولاد
نخستین مورد استخراج آهن به حدود سال ۱۳۰۰ پیش از میلاد باز می گردد. نخستین تولید مهم فولاد، با استفاده از روشی که پیش از آن مصریان باستان می شناختند، در هند آغاز شد. این روش، فرآیند «ووتس» نام دارد و محصول آن فولاد اسفنجی است. از حدود ۱۵۰۰ میلادی تا میانه سده نوزدهم، پیشرفت متالورژی بیشتر متوجه تکنولوژی های تولید آهن و فولاد بود. در همین دوران بود که کک وارد صنایع متالورژی شد. در واقع کشف امکان تبدیل زغال سنگ به کک در سال ۱۷۰۹ میلادی، انقلابی در صنایع متالورژی آهن و فولاد بوجود آورد. باید به نام «بسمر» نیز اشاره کنیم که با روش ابداعیش در سال ۱۸۹۰ میلادی، تولید فولاد را در مقیاس صنعتی انجام داد.
در این بخش توجه شما را به فیلم کوتاهی که در خصوص معرفی این آلیاژ شگفت انگیز تهیه شده، جلب می کنیم.
جایگاه فولاد در اقتصاد جهانی
در گذشته میزان تولید فولاد خام هر کشور به عنوان یکی از شاخص های صنعتی بودن در نظر گرفته می شد و این رویکرد همچنان البته با تغییراتی وجود دارد. کشور ما همواره در زمره ی کشورهایی بوده که سعی در بهبود رتبه خود در بین کشورهای تولید کننده فولاد داشته است.
بر اساس آمار منتشر شده میزان تولید فولاد جهان در سال ۲۰۱۸ برابر ۱٫۸ میلیارد تن بوده است. در این میان کشور چین با میزان تولید ۹۲۸ میلیون تن در این سال از این لحاظ رکورددار تولید فولاد در جهان است.
کشور ایران با توجه به ظرفیت های عظیم معادن و کارخانه های بزرگ تولید فولاد نظیر فولاد مبارکه، فولاد خوزستان و فولاد هرمزگان در این سال با تولید ۲۵ میلیون تن فولاد رتبه سیزدهم جهان را به خود اختصاص دهد. در این سال نرخ رشد فولاد ایران نسبت به آمار جهانی ۴ برابر رشد داشته است.
هم چنین ایران با تولید ۲۵/۵ میلیون تن آهن اسفنجی در این سال رتبه دوم جهان را در اختیار داشته است. در اینفوگرافی های زیر شما با وضعیت فعلی تولید فولاد در ایران و جهان آشنا می شوید.
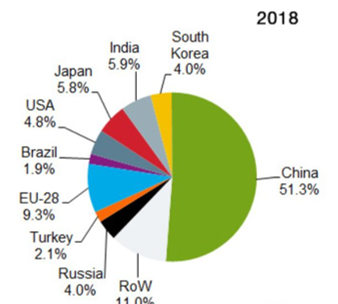
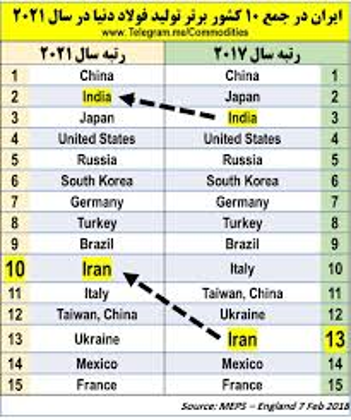
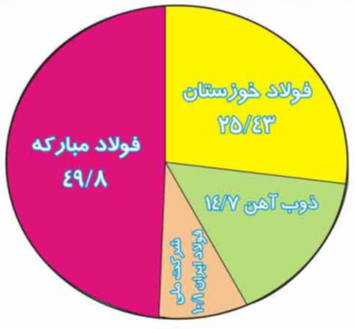
انواع فولادها
فولادها را از جنبه های مختلفی می توان دسته بندی کرد. مهم ترین دسته بندی فولادها، بر اساس عناصر آلیاژی موجود در آن هاست. از لحاظ عناصر آلیاژی فولادها به دو دسته فولادهای کربنی ساده و فولادهای آلیاژی طبقه بندی نمود.
خواص فولادهای کربنی ساده معمولا بستگی به مقدار کربن موجود در آن ها دارد در حالی که خواص فولادهای آلیاژی به نوع و میزان عناصر آلیاژی موجود در آن ها بستگی دارد.
فولادهای ساده کربنی
رایج ترین نوع فولاد، فولاد کربنی ساده (plain carbon steel) است که معرف فولادی شامل آهن و کربن به همراه مقادیر اندکی منگنز، سیلیسیم یا آلومینیوم بوده و به سه دسته ی کم کربن – کربن متوسط و پر کربن طبقه بندی می شود.
- فولادهای کم کربن: فولادهایی که درصد کربن موجود در آن ها کمتر از ۰/۲ درصد باشد. این فولادها انعطاف پذیری و چقرمگی مناسبی داشته و به خوبی شکل داده می شوند. هم چنین این فولادها جوش پذیری مناسبی دارند و از آن ها در صنایع الکتریکی و ماشین سازی نظیر سیم، لوله و ورق های فولادی نظیر ورق های ST52 استفاده می شود.
- فولادهای کربن متوسط: درصد کربن این فولادها بین ۰/۲ تا ۰/۶ درصد متغیر است. سختی و استحکام کششی این فولادها نسبت به نوع کم کربن بالاتر است اما انعطاف پذیری و جوش پذیری آن ها کم است. از این نوع فولادها در ساخت دیگ های بخار، ابزار و پیچ و شفت استفاده می شود.
- فولادهای پر کربن: این فولادها بیش از ۰/۶ درصد کربن دارند. افزایش درصد کربن باعث افزایش سختی و استحکام کششی فولاد می شود. اما انعطاف پذیری آن به شدت کاهش می یابد. این فولادها تقریبا جوش کاری نمی شوند. از این فولادها در ساخت ابزار سخت نظیر ابزار برشی، فنرها و کارد و چنگال استفاده می شود.
فولاد ساده کربنی ؛ پدر فولادهای صنعتی
فولاد مادر آلیاژهای صنعتی و یکی از ارکان علوم مهندسی به ویژه مهندسی متالورژی است...فولادهای آلیاژی
یکی دیگر از انواع مهم فولادها ، فولاد آلیاژی است که علاوه بر عناصر ذکر شده در بالا، مقادیر قابل توجهی از عناصری مانند کرم، نیکل و مولیبدن آن را از فولاد کربنی ساده متمایز می کند. فولاد آلیاژی می تواند کم آلیاژ، پر آلیاژ یا میکرو آلیاژی (HSLA) باشد. بخش خاصی از فولادهای آلیاژی، فولادهای زنگ نزن (stainless steel) هستند که حداقل ۱۱٫۵ درصد کرم دارند.
فولاد زنگ نزن یا استنلس استیل (Stainless Steel)
در میان فولادهای آلیاژی، فولاد زنگ نزن نامی آشنا محسوب می شود که تاکنون بارها نا...فولادهای ابزار (tool steels) فولادهایی هستند که برای ساخت ابزار مورد نیاز جهت برش، شکل دهی و سایر فرآیندهای مورد نیاز برای تبدیل مواد فلزی و غیر فلزی به اشکال مورد نظر بکار می روند.
فولاد ابزار Tool Steel
بسیاری از اشیائی که در زندگی روزمره با آنها سر و کار داریم از فولادهای ابزار به...ذکر این نکته لازم است که برخی فولاد ها به شکل فولاد ریختگی (steel castings) مورد استفاده قرار می گیرند اما روی بیشتر قطعات فولادی کار مکانیکی انجام می گردد تا به شکل نهایی برسند و بدین جهت به محصولات کارشده (wrought products) موسوم هستند.
در کاربردهای خاص، فولادهای ساده کربنی پاسخگوی نیاز ما نیستند. بعنوان مثال زمانی که مقاومت به خوردگی، یا مقاومت به سایش، یا خواص مکانیکی بالا موردنیاز باشند. به همین دلیل برای رفع محدودیت ها و بهبود خواص فولادها، عناصر آلیاژی به آن اضافه می کنند که به این دسته از فولادها، آلیاژی می گویند.
عناصر آلیاژی با توجه به خواص و کاربردی که از فولاد انتظار می رود، اضافه می شوند. مهم ترین این عناصر آلومینیوم، مس، کروم، نیکل، مولیبدن، سیلیسیوم، کبالت، سرب، بور، بیسموت، گوگرد، تیتانیوم، تنگستن، گوگرد، وانادیوم و نیوبیوم هستند. با تغییر درصد هر کدام از این عناصر، امروزه شاهد تولید و عرضه هزازان نوع فولاد آلیاژی هستیم.
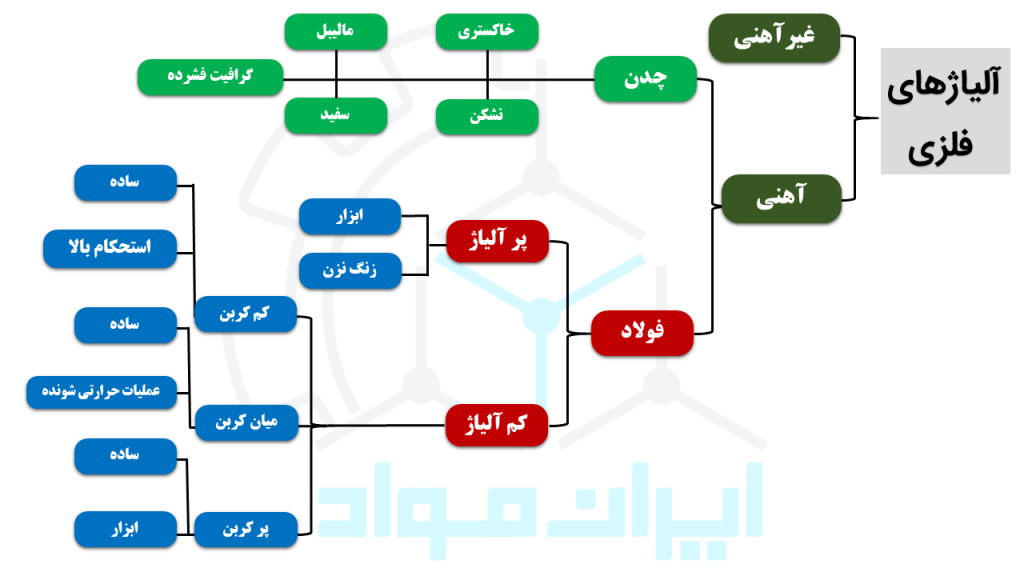
تولید فولاد
به طور کلی مراحل تولید فولاد شامل موارد زیر است:
- بخش اول: تولید گندله، زینتر و سوخت
- بخش دوم: تولید آهن خام
- بخش سوم: روش BOF
- بخش چهارم: کوره قوس الکتریکی
- بخش پنجم: ریخته گری مداوم و نورد گرم
- بخش ششم: نورد سرد و عملیات حرارتی
بطور کلی دو روش مرسوم در دنیا برای تولید فولاد وجود دارد:
روش کوره بلند
در این روش سنگ آهن پس از استخراج از معدن، خرد و الک می شود. سنگ آهن خرد شده به همراه مقداری پودر کک و سنگ آهک وارد کوره بلند شده و همراه آن ها هوای داغ به داخل کوره دمیده می شود. در حضور هوای داغ سنگ آهن احیا شده و با توجه به دمای بالای کوره ذوب شده و در قسمت پایین کوره جمع می شود. محصول به دست آمده در این بخش آهن خام (Pig Iron) نام دارد.
در مرحله بعد آهن خام به کنورتور حمل شده و در کنورتور با خروج کربن و سایر ناخالصی های آن به کمک اکسیژن فولاد خام (Crude Steel) به دست می آید و فولاد آماده ذوب ریزی می شود.
روش احیا مستقیم (کوره قوس الکتریکی)
در روش احیای مستقیم، سنگ معدن را تغلیظ کرده و آن را به گندله تبدیل می کنند. پس از جدا کردن گندله های ریز باقی را یه واحد احیای مستقیم منتقل می کنند. در واحدهای احیای مستقیم، کربن سنگ آهن گرفته شده و به محصولی به نام آهن اسفنجی تبدیل می شود.
آهن اسفنجی به دست آمده از این بخش با درصدی از آهن قراضه جهت ذوب وارد کوره قوس الکتریکی می شود. در این مرحله ناخالصی موجود در آهن اسفنجی همراه مقدار کمی اکسید آهن به صورت سرباره از فولاد مذاب جدا شده و مذاب فولاد آماده بار ریزی می شود.
تبدیل مذاب فولاد به شکل نهایی
فولادها به حالت مذاب تولید می شوند و پیش از انجام فرآیندهای بیشتر باید جامد گردند. در روشهای صنعتی انجماد به دو روش مختلف انجام می گیرد. در روش اول فولاد مذاب داخل قالب های مستطیل شکل ریخته می شود تا به صورت شمش (ingot) جامد گردد. این شمش ها توسط فرآیندهای دیگری نظیر نورد گرم به محصولات نیمه نهایی (semi finished) دیگری به نام های شمشه (bloom) و شمشال (billet) یا تختال (slab ) بر اساس ابعادشان تبدیل می شوند.
در روش دوم که رایج تر است، شمشه، شمشال یا تختال مستقیما از آهن مذاب و توسط روش ریخته گری مداوم (continuous casting) تولید می شوند. در این فرآیند فولاد مذاب در قسمت بالای قالبی که انتهای آن باز است و توسط جریان آب خنک می شود، ریخته می شود به طوری که فولاد جامد به طور پیوسته از انتهای قالب خارج می گردد. فولاد نیمه نهایی به محصولات کارشده (wrought) نهایی نظیر میله (bar)، ورق (sheet)، نوار (strip)، صفحه (plate)، مقاطع ساختمانی، سیم، ریل و لوله توسط روش هایی مانند نورد سرد و گرم ، کشش ، آهنگری (forging) و اکستروژن تبدیل می شوند. برای رسیدن به خواص مطلوب برای کاربردهای خاص مهندسی، بیشتر محصولات نهایی به ترکیبی از عملیات حرارتی و عملیات شکل دهی نیازمندند.
کاربردهای فولاد
همانطور که در دو تصویر زیر می بینید با استفاده از نورد گرم و سرد، دامنه وسیعی از محصولات فولادی شامل ورق، زر ورق، لوله، تیوب، مقاطع، میلگرد، سیم و … بدست می آید که یا مستقیما استفاده می شوند یا با فرآیندهای تولید تکمیلی به اشکال مورد نیاز در می آیند. از سوی دیگر فرآیند ریخته گری هم داریم که با کمک آن طیف گسترده ای از محصولات پر کاربرد تولید می شوند.
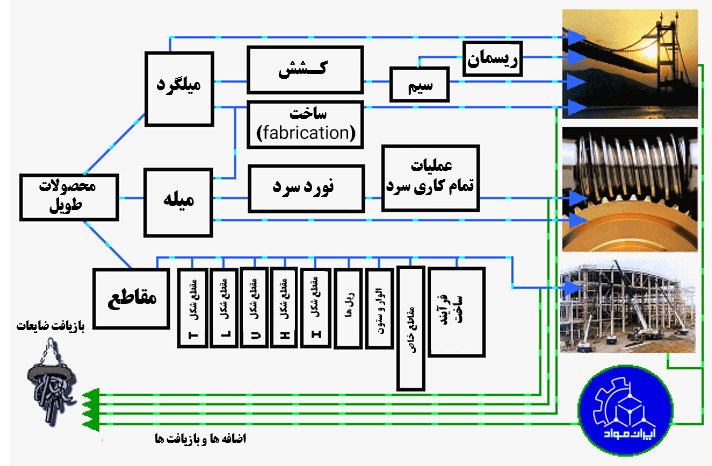
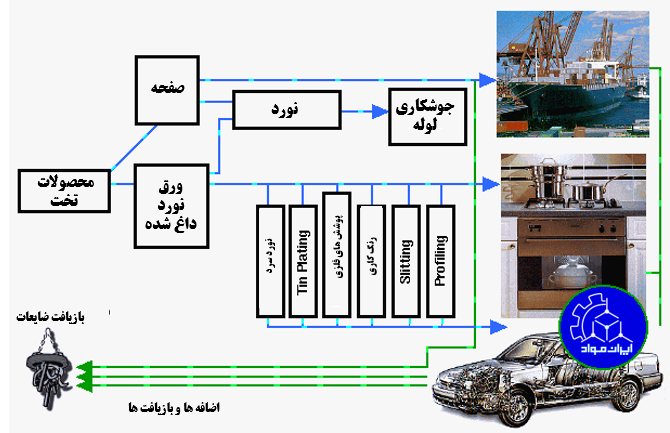
دانستن این نکته مهم است که قطعات فولادی باید به هم متصل شوند که یکی از پرکاربردترین روشهای اتصال دهی روش های جوشکاری است. هر چه کربن فولاد کمتر باشد قابلیت جوشکاری (weldability) بهتر می شود. به همین خاطر اکثر فولادهای صنعتی، کربن کمنر از سه دهم درصد دارند و به اینها فولاد کم کربن گفته می شود. با افزایش درصد منگنز و نیز افزودن اندکی نایوبیوم می توان استحکام مکانیکی این دسته از فولادها را افزایش داد.
اگر میزان کربن فولاد از سه دهم درصد بیشتر شود،از آن محصولاتی مانند پیچ و شفت و چرخ دنده و میل لنگ می سازند که نیاز به جوشکاری ندارد.برای این دسته از فولادها از انواع روشهای عملیات حرارتی برای دستیابی به استحکام و ویژگی های مطلوب، استفاده می شود.
فولادهای پرکربن که استحکام مکانیکی بالایی دارند مناسب ساخت ابزارهایی مانند اره و تیغه و فنر هستند. البته همانگونه که در بالاتر اشاره کردیم، در دسته فولادهای آلیاژی گروهی به نام فولاد ابزار (tool steel) وجود دارند که با اضافه شدن عناصر کبالت، تنگستن،مالیبدن و وانادیوم به مناسبترین کاندیدای ساخت ابزار تبدیل می شوند.
فولاد کربنی ساده تا حدود ۴۰۰ درجه سانتیگراد قابل کاربرد است و برای دماهای بالاتر تا ۷۰۰ درجه سانتیگراد کروم و مولیبدن افزوده می شوند. برای دماهای باز هم بالاتر سراغ فولادهای زنگ نزن (stainless steel) می روند. اگر روی قاشق یا چنگال دقت کنید شاید ۸-۱۸ را ببینید که منظور فولاد زنگ نزن ۳۰۴ با ۱۸ درصد کروم و ۸ درصد نیکل است.این فولاد ۹۵۰ درجه سانتیگراد را تاب می آورد اما برای دماهای بالاتر (تا ۱۱۵۰ درجه) سراغ گریدهای دیگر زنگ نزن مانند ۳۱۰ می روند.
به خاطر داشته باشیم برای دماهای کمتر از منفی ۳۰ درجه، فولاد کربنی ساده گزینه ی مناسبی نیست. با افزودن تا ۹ درصد نیکل می توان فولاد را تا منفی دویست درجه سانتیگراد بدون مشکل به کار برد. البته در دماهای پایین، فولادهای زنگ نزن همیشه می توانند استفاده شوند. البته قیمت آنها تقریبا سه برابر فولاد کربنی است.
«کلید فولاد» مرجع ارزشمندی است که فولادها را بر اساس کاربردشان دسته بندی کرده است. حتما نگاهی به آن بیندازید و کشف کنید که فولادی که در ساخت تیغه چاقو استفاده شده است چه تفاوت هایی با فولادی دارد که مثلا از آن ستون چادر سفری را می سازند.
جمع بندی
در این مطلب سعی شد تا فولاد به عنوان مهم ترین آلیاژ مورد استفاده در صنعت معرفی شده و دید مناسبی بر طبقه بندی آن ارائه شود. به طور کلی فولادها را از چندین جنبه می توان طبقه بندی کرده و مورد بررسی قرار داد که یکی از مهم ترین آن ها، طبقه بندی بر اساس نوع عناصر آلیاژی است. بر این اساس فولادها به دو گروه اصلی فولادهای ساده کربنی و فولادهای آلیاژی طبقه بندی می شوند که با تغییر در عناصر آلیاژی می توان صدها نوع فولاد به دست آورد. کتاب کلید فولاد مهم ترین مرجع برای طبقه بندی و شناسایی فولادها بوده که تقریبا غالب فولادهای مصرفی در صنعت را در خود جای داده است. از این رو آموزش نحوه استفاده از این کتاب برای تمامی مهندسین و صنعتگران لازم است.
دانلود فقط با IP ایران امکانپذیر است. در صورت عدم مشاهده باکس قرمز رنگ دانلود، VPN خود را خاموش نموده و صفحه را رفرش کنید.
پسورد فایل فشرده : www.iran-mavad.com
دیدگاه کاربران