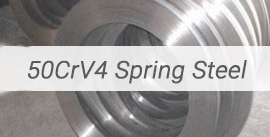
مقایسه تخصصی لولههای A106 و A53؛ کدام انتخاب بهتری برای پروژههای شماست؟
فولاد A106 طبق استاندارد ASTM بهعنوان یک لوله مانیسمان بدون درز (Seamless) شناخته میشود که برای دمای بالا و فشار بالا طراحی شده است و اغلب در دیگهای بخار، مبدلهای حرارتی، و خطوط بخار به کار میرود. در مقابل، فولاد A53 هم بهصورت بدون درز و هم درزدار (Welded) تولید میشود و کاربرد آن در شرایط دمای پایینتر و فشارهای معمولی مانند لولهکشی آب، هوا، بخار کمفشار و گاز شهری رایج است.
در این مقاله، سعی داریم با رویکردی کاملاً علمی، فنی و صنعتی به بررسی تفاوتهای این دو نوع فولاد بپردازیم. این بررسی شامل استانداردها، ترکیب شیمیایی، خواص مکانیکی، جوشپذیری، تفاوتهای ساختاری و کاربردهای واقعی در صنایع مختلف خواهد بود. هدف نهایی، کمک به انتخاب دقیق و منطقی بین این دو فولاد در پروژههای صنعتی، با تأکید بر عملکرد، ایمنی و بهینهسازی اقتصادی است.
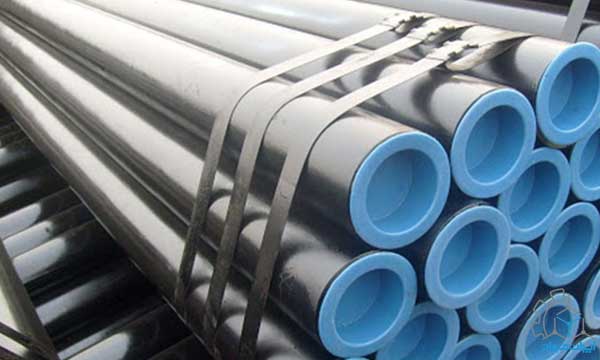
ترکیب شیمیایی – تفاوت تحلیلی بین فولاد A106 و A53
فولاد A106 و A53 هر دو در دسته فولادهای کمکربن قرار میگیرند، اما تفاوتهایی در ترکیب شیمیایی آنها باعث تفاوت عملکرد در شرایط سرویس میشود. مهمترین تفاوت بین این دو، در مقدار کنترلشدهتر عناصر در A106 نسبت به A53 است. فولاد A106 بهویژه در گریدهای B و C، با درصد کربن بیشتر (تا 0.35%) و گوگرد و فسفر کمتر نسبت به A53 ساخته میشود. این موضوع موجب افزایش استحکام در دمای بالا، و کنترل بهتر رفتار در برابر ترکزایی میشود.
در مقابل، فولاد A53 معمولاً مقدار گوگرد و فسفر بالاتری دارد (حداکثر 0.05%) که برای لولههای کمفشار قابل قبول است اما ممکن است در جوشکاری یا سرویس طولانیمدت در شرایط خورنده، مشکلاتی مانند ترک گرم یا ترک ناشی از تنش پسماند ایجاد کند. از طرف دیگر، محدوده منگنز در A53 وسیعتر و در بعضی موارد بیشتر است که میتواند سختی را افزایش دهد، اما پایداری خواص مکانیکی در دمای بالا را کمتر از A106 تضمین میکند.
لولههای فولادی ASTM A106؛ ستون فقرات خطوط انتقال سیالات داغ
لولههای ASTM A106 که با نام "لوله بویلری کربنی" یا "لوله فشار قوی بدون درز" نیز...همچنین، A106 بهصورت خاص برای کاربردهای دمای بالا طراحی شده و از نظر کنترل ناخالصیها مانند عناصر آلیاژی ردیابی (نیکل، کروم، مولیبدن) هم استاندارد سختگیرانهتری دارد. این کنترل دقیق، باعث میشود A106 در مبدلهای حرارتی، خطوط بخار و دیگهای تحت فشار، عملکرد قابل اطمینانتری داشته باشد.
نتیجه: فولاد A106 از نظر ترکیب شیمیایی، دارای کنترل بیشتر بر عناصر کلیدی است که آن را برای دمای بالا، فشار بالا و محیطهای بحرانیتر مناسبتر میکند. در حالیکه A53 برای کاربردهای عمومی و غیر بحرانیتر مانند انتقال آب، گاز یا هوا طراحی شده است.
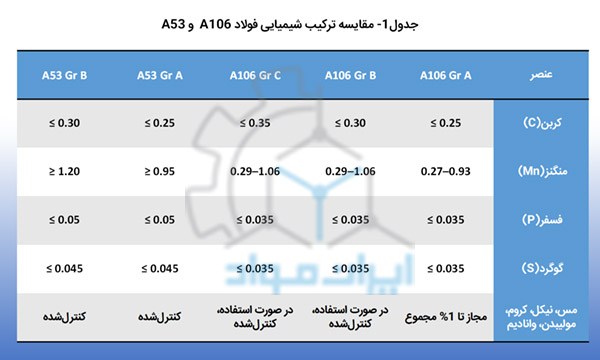
تفاوت در ساختار و شکلگیری لولهها
یکی دیگر از تفاوتهای اصلی بین فولاد A106 و A53 در نوع ساخت لولهها نهفته است. فولاد A106 فقط بهصورت لوله بدون درز (Seamless) تولید میشود، در حالیکه لوله کربن استیل A53 میتواند بهصورت بدون درز (Type S)، درزدار الکتریکی (Type E)، یا جوشکاری کورهای (Type F) تولید شود. این تفاوت در ساخت، اثر مستقیم بر استحکام ساختاری، یکنواختی خواص مکانیکی و پایداری عملکرد در شرایط بحرانی دارد.
در لولههای بدون درز مانند A106، هیچ ناحیهای با ریسک ضعف ساختاری مثل درز جوش وجود ندارد. این باعث میشود توزیع تنش در طول لوله یکنواختتر باشد و احتمال ترک، نشت یا شکست در اثر فشار داخلی یا حرارت بالا کاهش پیدا کند. به همین دلیل، لولههای A106 انتخاب استاندارد برای خطوط فشار بالا، دمای بالا، بخار سوپر هیت و مبدلهای حرارتی هستند. همچنین، نبود درز باعث میشود مقاومت به خستگی حرارتی و سیکلی در این لولهها بیشتر باشد.
در مقابل، A53 در نوع درزدار (مخصوصاً Type E و Type F) دارای خط جوش طولی است که حتی با تست و بازرسی غیرمخرب، همچنان ضعیفترین نقطه ساختاری لوله باقی میماند. این نوع لولهها در فشار پایین یا کاربردهای استاتیک مانند انتقال آب، هوا یا گاز شهری عملکرد قابل قبولی دارند، اما در فشار یا دمای بالا، ناحیه درز ممکن است به مرور زمان دچار خرابی شود، بهویژه اگر فرایند جوشکاری صنعتی ضعیف انجام شده باشد.
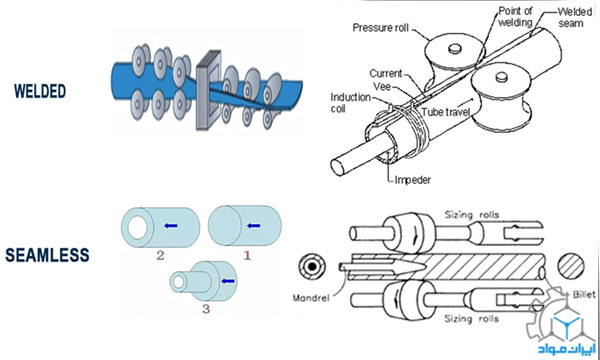
خواص مکانیکی، جوشپذیری و ماشینکاری
خواص مکانیکی
از نظر خواص مکانیکی، تفاوت کلیدی بین فولاد A106 و A53 در تحمل دما و فشار بالاست. فولاد A106 مخصوصاً در گرید B و C، بهطور خاص برای استفاده در شرایط سرویس با دماهای بالاتر از 400 درجه سانتیگراد طراحی شده است. در مقابل، فولاد A53 عمدتاً برای شرایط دمای محیط یا دمای پایین طراحی شده و در سیستمهایی با فشار متوسط و کنترلشده، مثل خطوط آب یا گاز شهری، مورد استفاده قرار میگیرد. از نظر عددی، هر دو در گرید B دارای استحکام کششی مشابه (حدود 415 مگاپاسکال) هستند، اما عملکرد A106 در دماهای بالا پایدارتر و قابلاعتمادتر است.(بر اساس استاندارد ASME B31.1 Power Piping)
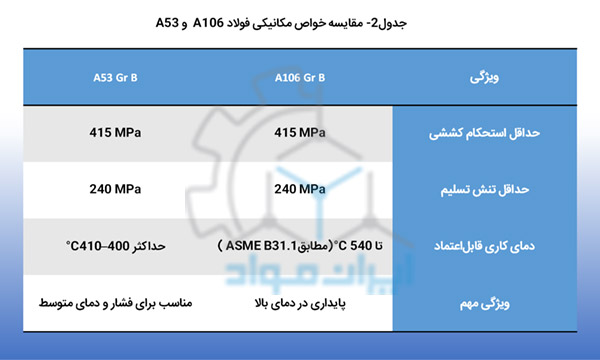
جوشپذیری
از لحاظ جوشپذیری، هر دو فولاد قابلیت خوبی دارند، اما فولاد A106 به دلیل کنترل دقیقتر ترکیب شیمیایی، بهویژه در زمینه مقدار کمتر فسفر و گوگرد، در برابر ترکزایی در جوش یا حساسیت به شکست ترد مقاومت بیشتری دارد. این موضوع باعث شده در پروژههایی که نیاز به جوشکاری سنگین دارند یا فشار و دمای سرویس بالا است، انتخاب اول مهندسان باشد. در عوض، فولاد A53 در نسخههای درزدار (خصوصاً Type F) ممکن است در ناحیه جوش یا درز طولی دچار ضعف ساختاری شود، به همین دلیل برای جوشکاری در شرایط بحرانی توصیه نمیشود.
ماشینکاری و فرمپذیری
در مورد ماشینکاری، فولاد A53 به دلیل درصد نسبتاً بالاتر گوگرد، کمی راحتتر ماشینکاری میشود و برای عملیات تراش و رزوهزنی در کارگاههای عمومی مناسبتر است. با این حال، A106 با ساختار همگنتر، برای فرمدهی گرم، خمکاری و انبساطهای تحت فشار در خطوط لوله صنعتی پایدارتر و قابل اعتمادتر است، بهویژه در مواردی که لوله تحت تنش حرارتی قرار میگیرد یا تغییر شکل مکانیکی مکرر دارد.

کاربردهای صنعتی
تفاوت بین فولاد A106 و A53 در صنعت نهتنها تئوریک، بلکه کاملاً اجرایی و تعیینکننده در انتخاب لوله مناسب برای هر پروژه است. هرکدام از این دو نوع فولاد، دامنهای مشخص از کاربردها دارند که بر اساس شرایط دما، فشار، نوع سیال و حساسیت عملکردی سیستم تعیین میشود.
شاید علاقمند باشید:
لوله API 5L چه کاربردی دارد؟
لولههای API 5L یکی از پرکاربردترین و مهمترین انواع لولهها در صنایع نفت، گاز، ...A106- انتخاب اول در شرایط بحرانی
لولههای فولادی A106 به دلیل ساختار بدون درز و خواص مکانیکی پایدار در دمای بالا، در بسیاری از پروژههای حساس و بحرانی استفاده میشوند. از کاربردهای کلیدی این فولاد میتوان به موارد زیر اشاره کرد:
- خطوط بخار فشار بالا در نیروگاهها (بخار سوپرهیت یا فوقداغ با دما بالای 450°C)
- مبدلهای حرارتی و دیگهای بخار در پتروشیمی و پالایشگاهها
- خطوط لولهی تحت فشار برای سیالات داغ (نفت خام، گاز ترش، آب اشباع)
- سیستمهای فرایندی پالایشگاهی که در آن تنش حرارتی و فشار متناوب وجود دارد
مثال صنعتی واقعی:
در پروژههای نیروگاه سیکل ترکیبی، خطوط انتقال بخار خروجی از بویلر به توربینها، به دلیل دمای بسیار بالا و سیکل کاری دائم، همیشه از لولههای A106 Gr B یا C استفاده میشود. مهندسان طراح در استاندارد ASME B31.1 توصیه صریح به استفاده از A106 در این موارد دارند.
A53 – مناسب برای خطوط انتقال عمومی و سرویسهای سبک
در مقابل، فولاد A53 به دلیل قیمت پایینتر و تنوع نوع (درزدار و بدون درز)، در کاربردهایی بهکار میرود که فشار، دما و ریسک عملکرد پایینتر است. موارد اصلی عبارتاند از:
- خطوط لوله آب سرد، گرم یا تصفیهشده در ساختمان و صنعت
- سیستمهای هوای فشرده و خنککاری در کارخانجات
- انتقال گاز شهری در خطوط کمفشار
- لولهکشی فاضلاب، زهکشی، تخلیه صنعتی و پوشش کابل
مثال صنعتی واقعی:
در پروژههای تأسیسات شهری مثل انتقال گاز خانگی، معمولاً از لوله A53 Type E یا Type F استفاده میشود، چرا که فشار کاری سیستم پایین است و اولویت با کاهش هزینه و سهولت دسترسی است، نه عمر عملکرد در شرایط سخت.
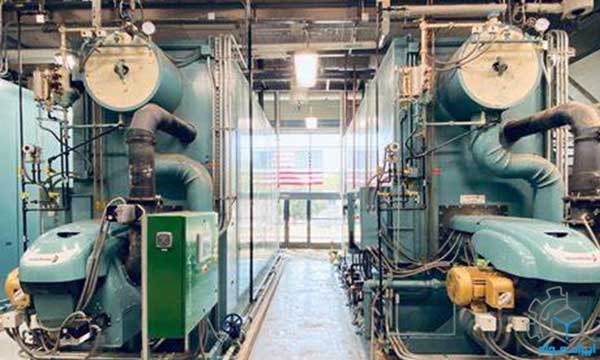
قیمت و در دسترس بودن در بازار
مقایسه قیمت و موجودی در بازار
از نظر قیمت، فولاد A53 بهوضوح گزینه ارزانتر است. دلیل اصلی آن، امکان تولید بهصورت درزدار (Welded) با هزینه ساخت کمتر، و پیچیدگی کمتر در کنترل کیفیت شیمیایی و حرارتی است. در مقابل، A106 بهعنوان یک لوله بدون درز (Seamless) با کیفیت بالاتر و دقت تولید بیشتر، دارای قیمت بالاتری بهخصوص در گرید C و قطرهای بالا است.
- طبق دادههای بازار بینالمللی (2023)، تفاوت قیمت بین A106 Gr B و A53 Gr B معمولاً ۱۰ تا ۳۰ درصد است، بسته به نوسانات مواد اولیه، نرخ ساخت، گرید و سایز لوله.
- در بازار ایران، A53 بهدلیل واردات گسترده چین، هند و ترکیه بهراحتی در دسترس است. A106 نیز موجود است، اما در قطرهای خاص یا گرید C ممکن است نیاز به واردات سفارشی یا خرید از منابع محدود داخلی داشته باشد.
تحلیل اقتصادی پروژهمحور
از دید اقتصادی، انتخاب بین این دو فولاد باید بر اساس ریسک عملیاتی و شرایط کاری باشد، نه فقط قیمت واحد.
- در پروژههایی مانند نیروگاهها، خطوط بخار، پالایشگاهها و دیگهای تحت فشار، هرگونه شکست یا نشتی میتواند منجر به خسارت چند ده میلیاردی و توقف تولید شود؛ در این شرایط، افزایش ۲۰ درصدی در هزینه لوله A106 کاملاً توجیهپذیر و حتی ضروری است.
- در مقابل، در پروژههای لولهکشی ساختمان، انتقال گاز شهری یا سیستمهای آبرسانی کمفشار که شرایط کار ملایم است، استفاده از A53 باعث کاهش چشمگیر در هزینه کلی پروژه میشود، بدون اینکه ریسک جدی ایجاد کند.
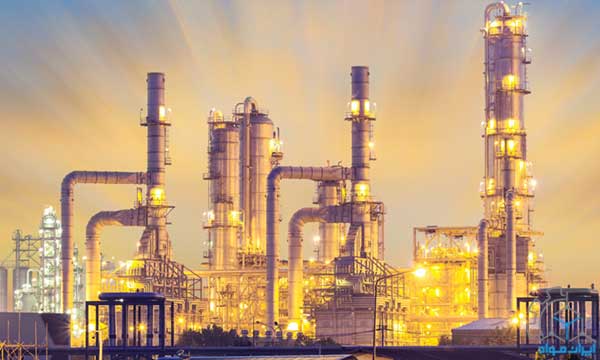
نتیجهگیری
فولادهای A106 و A53، هر دو از پرکاربردترین مواد در سیستمهای لولهکشی صنعتی به شمار میروند، اما تفاوتهای آنها در ترکیب شیمیایی، خواص مکانیکی، ساختار تولید و ردهبندی کاربرد باعث میشود که انتخاب بین آنها یک تصمیم کاملاً فنی و حیاتی باشد. فولاد A106، بهویژه در گریدهای B و C، به دلیل کنترل دقیق ترکیب شیمیایی، ساختار بدون درز و مقاومت بهتر در برابر دما و فشار بالا، در شرایط کاری سخت و حساس ترجیح داده میشود. از سوی دیگر، A53 بهعنوان گزینهای اقتصادیتر و در دسترستر، در کاربردهای عمومی و با فشار کاری محدود، عملکرد قابل قبولی دارد.
از لحاظ خواص مکانیکی و ساختاری، A106 به دلیل عدم وجود خط درز، پایداری بالاتری در برابر تنشهای حرارتی و مکانیکی دارد و انتخاب اول در صنایع نیروگاهی، پتروشیمی، پالایشگاهی و خطوط بخار است. در مقابل، A53 (بهویژه نوع درزدار) در پروژههایی مثل لولهکشی گاز شهری، انتقال آب و سیستمهای ساختمانی عملکرد خوبی دارد و مقرونبهصرفهتر است، بهویژه وقتی فشار و دمای سیستم در محدوده ایمن باقی میماند.
در نهایت، انتخاب بین A106 و A53 باید بر اساس شرایط واقعی سرویس، تحلیل ریسک، طول عمر پروژه و بودجه مهندسی انجام شود. برای کاربردهای حساس، A106 با وجود قیمت بالاتر، گزینهای مطمئن و ماندگار است. اما در کاربردهای غیر بحرانی و عمومی، A53 انتخابی هوشمندانه از نظر اقتصادی خواهد بود. مهندسی دقیق یعنی درک این تفاوتها و اتخاذ تصمیم فنی بهینه برای هر کاربرد خاص.
دیدگاه کاربران