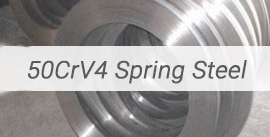
فولاد 100Cr6 چیست و چه مشخصاتی دارد؟
ترکیب شیمیایی این فولاد باعث افزایش سختیپذیری، مقاومت به سایش و پایداری ابعادی بالا میشود. این فولاد پس از عملیات حرارتی به سختی 62–66 HRC میرسد، که به دلیل تشکیل فاز مارتنزیتی و پراکندگی یکنواخت کاربیدهای کروم (Cr₇C₃) است . کروم موجود در این آلیاژ چقرمگی و مقاومت خستگی را در شرایط بارگذاری متناوب افزایش میدهد.
به دلیل این خواص، فولاد100Cr6 انتخاب اول در ساخت اجزای دوار پرسرعت و با دقت بالا است. این فولاد در تولید بلبرینگهای صنعتی، ساچمهها، رولرها، محورهای دقیق، قطعات پمپهای هیدرولیکی، ابزارهای اندازهگیری و حتی قطعاتی در صنعت خودرو و هوافضا کاربرد گسترده دارد. عملکرد آن در شرایط اصطکاکی شدید، همراه با پایداری حرارتی تا حدود 150 درجه سانتیگراد، آن را به یکی از پرکاربردترین فولادهای ابزار دقیق و تحمل بار دینامیک تبدیل کرده است. با این حال، محدودیتهایی مانند حساسیت به ترکهای حرارتی در فرایندهای تولید وجود دارد که نیاز به کنترل دقیق دارد.
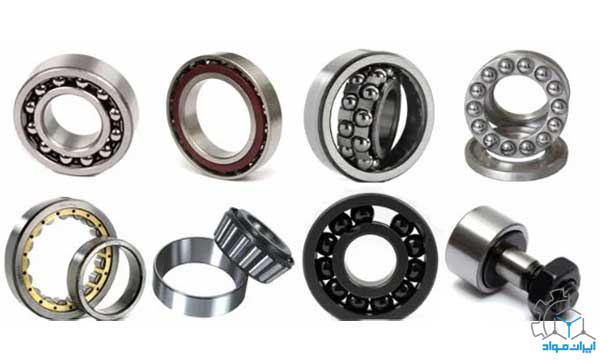
ترکیب شیمیایی
فولاد 100Cr6، با شماره 1.3505 در استاندارد DIN EN ISO 683-17 و معادل AISI 52100 در ASTM A295 شناخته شده است. درصد بالای کربن و کروم به همراه مقادیر کنترلشده منگنز و سیلیسیم، خواص متالورژیکی متمایزی ایجاد میکند. شکل زیر ترکیب شیمیایی این فولاد را بر اساس استاندارد DIN EN ISO 683-17 نشان میدهد:
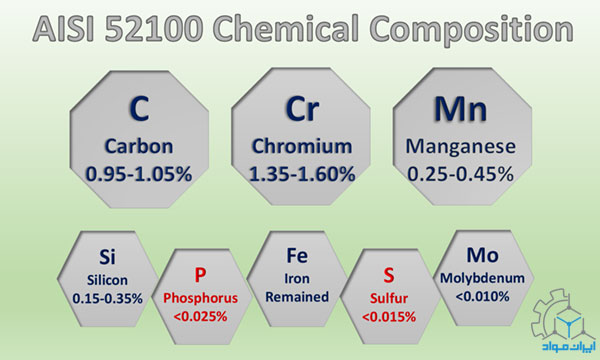
نقش عناصر در خواص فولاد
کربن با تشکیل کاربیدهای مقاوم، ساختار مارتنزیتی را تقویت میکند.
در مقابل، کروم عمق نفوذ سختی را افزایش داده و پایداری کاربیدها را زیاد میکند.
افزودن منگنز (0.25–0.45%) استحکام را بالا برده و شکنندگی را کاهش میدهد.
سیلیسیم (0.15–0.35%) خاصیت الاستیک و پایداری ساختاری را افزایش میدهد.
فسفر (≤0.025%) و گوگرد (≤0.015%) به حداقل میرسند تا از شکنندگی و نقصهای سطحی جلوگیری شود.
مولیبدن (≤0.10%) تأثیر محدودی دارد، اما آهن بهعنوان پایه اصلی، ماتریس فولادی را تشکیل میدهد
خواص فیزیکی فولاد 100Cr6
خواص فیزیکی فولاد 1.3505 نقش مهمی در عملکرد آن در شرایط کاری مختلف دارند. جدول زیر برخی از این خواص را بر اساس استاندارد DIN EN ISO 683-17 و منابع علمی نشان میدهد:
ویژگی | مقدار | توضیح مفهومی |
چگالی (Density) | 7.81 g/cm³ | مشابه سایر فولادهای پرکربن، مناسب برای قطعاتی با اینرسی مکانیکی زیاد مثل بلبرینگها |
ضریب انبساط حرارتی (20–100°C) | 10.5 × 10⁻⁶ /K | نشاندهنده پایداری ابعادی در دماهای متوسط |
هدایت حرارتی (Thermal conductivity) | 30–35 W/(m·K) در 20°C | انتقال حرارت متوسط؛ مناسب برای انتقال حرارت در کاربردهای دینامیک و جل.گیری از تمرکز تنش حرارتی |
ظرفیت گرمایی ویژه (Specific heat) | 460 J/kg·K | نشاندهنده رفتار حرارتی پایدار |
نقطه ذوب (Melting point) | حدود 1420–1460 °C | قابل استفاده در کاربردهای تا دمای 150°C بدون افت عملکرد |
خواص مکانیکی فولاد 100Cr6
جدول زیر خواص مکانیکی کلیدی این فولاد را بر اساس استانداردهای DIN EN ISO 683-17 و ASTM A295 و منابع علمی نشان میدهد:
خاصیت | مقدار | شرایط یا توضیحات |
استحکام کششی (Tensile Strength) | 2000–2200 MPa | پس از کوئنچینگ و تمپرینگ در 160–200°C |
استحکام تسلیم (Yield Strength) | 1700–1900 MPa | وابسته به دمای تمپرینگ |
استحکام خستگی (Fatigue Strength) | 1000–1200 MPa | در تست خستگی تماسی (Rolling Contact Fatigue) |
ضریب اصطکاک (Coefficient of Friction) | 0.1–0.15 | در شرایط روانکاریشده، تماس غلتشی |
توضیحات و نکات کلیدی
- استحکام کششی و تسلیم: مقادیر استحکام کششی (2000–2200 MPa) و تسلیم (1700–1900 MPa) نتیجه تشکیل ساختار مارتنزیتی و توزیع یکنواخت کاربیدهای کروم در طی کوئنچینگ و تمپرینگ است. این یعنی فولاد 1.3505 برای تحمل بارهای سنگین در یاتاقانهای غلتشی و قطعات دقیق مناسب است.
- استحکام خستگی: استحکام خستگی بالا (1000–1200 MPa) در تستهای خستگی تماسی، توانایی این فولاد را برای مقاومت در برابر چرخههای بارگذاری مکرر نشان میدهد. این ویژگی برای کاربردهایی مانند رولبرینگهای پرسرعت حیاتی است.
- ضریب اصطکاک: ضریب اصطکاک پایین (0.1–0.15) در شرایط روانکاریشده، اتلاف انرژی را در قطعات دوار کاهش میدهد. این رفتار به دلیل پراکندگی کاربیدهای Cr₇C₃ است که سطح تماس را بهینه میکند. در دماهای بالاتر از 150 درجه سانتیگراد، انتخاب روانکار مناسب برای حفظ این عملکرد ضروری است.
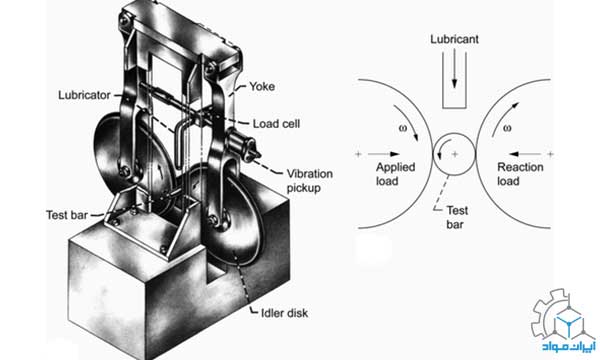
عملیات حرارتی و میکروساختار
عملیات حرارتی فولاد 100Cr6 برای دستیابی به خواص مطلوب یاتاقانها حیاتی است. در کوئنچینگ، فولاد تا دمای 830–870°C گرم شده و در روغن سرد میشود تا فاز مارتنزیتی غالب تشکیل شود که پایهای برای ساختار مقاوم است. سپس، تمپرینگ در دمای 160–200°C انجام میشود تا تنشهای داخلی کاهش یابد و کاربیدهای کروم (Cr₇C₃) بهصورت یکنواخت توزیع شوند، که باعث پایداری ساختاری میشود. این فرایندها میکروساختار مارتنزیتی با کاربیدهای ریز را ایجاد میکنند، اما دمای نامناسب یا خنکسازی ناکافی ممکن است منجر به آستنیت باقیمانده یا ترکهای ریز شود. محدودیت دمایی 150°C این فولاد به دلیل نرم شدن ساختار مارتنزیتی و کاهش پایداری کاربیدهای کروم (Cr₇C₃) در دماهای بالاتر است. در دمای بیش از 150°C، مارتنزیت تمپرشده شروع به تبدیل به فازهای نرمتر (مانند فریت) میکند و کاربیدها ممکن است درشت یا تجزیه شوند، که باعث کاهش سختی (HRC) و مقاومت به سایش میشود.
کاربردهای صنعتی
فولاد AISI 52100 در صنایع مختلف کاربردهای متنوعی دارد. در ادامه، کاربردها در صنایع کلیدی ارائه میشوند:
- صنعت خودروسازی: در این صنعت، AISI 52100 برای بلبرینگهای چرخ (مانند خودروهای تویوتا کمری) و شفتهای گیربکس (مانند گیربکسهای دستی در فورد فوکوس) استفاده میشود، زیرا دقت ابعادی بالا و توانایی تحمل تنشهای تماسی را فراهم میکند. این فولاد به دلیل پایداری در بارهای سیکلی در یاتاقانهای موتور نیز به کار میرود، .
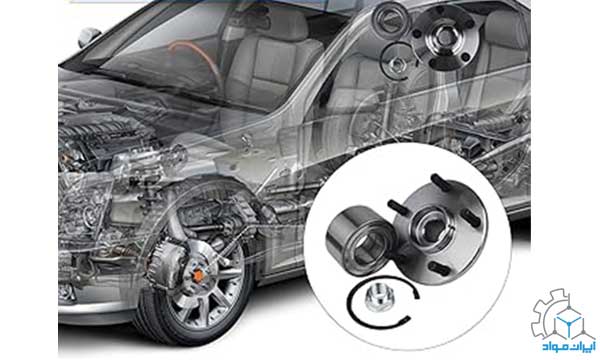
- صنعت هوافضا: 100Cr6 در یاتاقانهای توربین (مانند موتورهای جت بوئینگ 737) به دلیل تحمل تنشهای دینامیکی بالا استفاده میشود. این فولاد برای محورهای دقیق در سیستمهای ناوبری نیز مناسب است، زیرا پایداری ابعادی دارد.
- صنعت ماشینآلات صنعتی: در پمپهای هیدرولیکی (مانند پمپهای بوش رکسروث) و ماشینهای CNC، فولاد 1.3505 به دلیل مقاومت در برابر بارهای متناوب در رولرها و محورها به کار میرود. در قالبهای تزریق پلاستیک برای تولید قطعات دقیق، این فولاد به دلیل دوام در برابر تنشهای مکانیکی انتخاب میشود.
- صنعت ابزار دقیق: AISI 52100 در کولیسهای دیجیتال و ابزارهای اندازهگیری (مانند محصولات میتوتویو) استفاده میشود.
- محدودیتها: عملکرد AISI 52100 در دماهای بالای 150°C کاهش مییابد و نیاز به روانکاری مناسب برای جلوگیری از فرسودگی در شرایط اصطکاک شدید دارد.
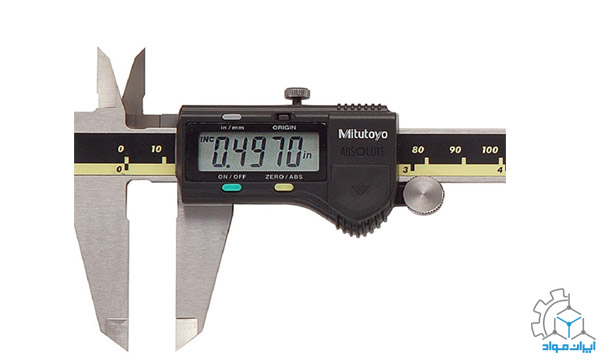
مقایسه با فولادهای جایگزین
فولاد Cr6 100با فولادهای دیگری که خواص مشابهی دارند و میتوانند جایگزین شوند، مقایسه میشود. جدول زیر این مقایسه را با فولادهای 440C (فولاد زنگنزن) و M50 (فولاد ابزار) نشان میدهد:
فولاد | استاندارد | کاربردهای مشابه | مشخصات کلیدی و محدودیتها |
100Cr6 | DIN EN ISO 683-17 | بلبرینگها، محورها، قالبهای دقیق | هزینه مناسب، خلوص بالا، مناسب برای تنشهای تماسی، حساس به دمای بالا، دمای کاری: تا 150°C |
440C | ASTM A276 | یاتاقانهای دریایی، ابزار جراحی | مقاومت به خوردگی عالی: 100 ساعت در تست اسپری نمک، دمای کاری تا 200°C ، هزینه بالاتر و سختیپذیری کمتر |
M50 | AMS 6491 | یاتاقانهای هوافضا، ابزارهای برش | پایداری در دمای بالا، دمای کاری: تا 400°C، اما پیچیدگی تولید و هزینه بیشتر |
توضیحات : فولاد 100Cr6 با هزینه نسبی پایین و دمای کاری تا 150°C برای یاتاقانهای استاندارد بهینه است. فولاد 440C با مقاومت به خوردگی بالا (100 ساعت در تست اسپری نمک) برای محیطهای مرطوب (مانند یاتاقانهای دریایی) مناسب است، اما هزینه آن 1.5–2 برابر 100Cr6 است. فولاد M50 به دلیل تحمل دمای 400°C در یاتاقانهای هوافضا (مانند موتورهای جت) برتری دارد، اما هزینه 2.5–3 برابر و فرایند تولید پیچیدهتر، کاربرد آن را محدود میکند.
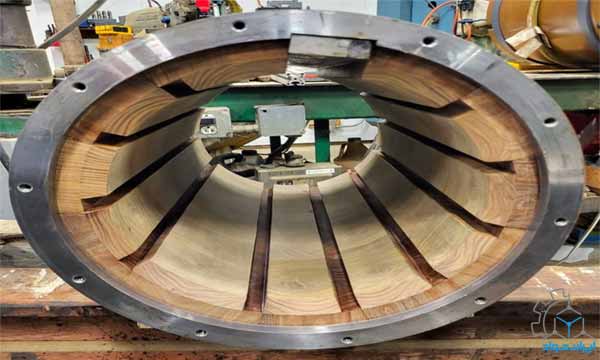
تحقیقات اخیر
تحقیقات جدید درباره فولاد 100Cr6 به بهبود عملکرد آن در شرایط خاص و گسترش کاربردهایش پرداختهاند. این پیشرفتها در سه دسته اصلی بررسی میشوند:
- پوششهای جدید برای محافظت بهتر: پژوهشها نشان دادهاند که افزودن پوششهای تنگستندار (W-DLC) به 1.3505، مقاومت آن را در برابر زنگزدگی در آب دریا افزایش میدهد. این پوشش ضریب اصطکاک را به 0.105 کاهش داده و مقاومت به خوردگی را تا 2 برابر بهبود میبخشد (پتانسیل خوردگی: -172 mV در مقابل -477 mV بدون پوشش)، که برای یاتاقانهای کشتیها مفید است . اما هزینه بالای پوشش یک چالش است.
- روشهای شکلدهی پیشرفته: تیکسوفورمینگ، روشی جدید برای شکلدهی فولاد در حالت نیمهجامد، قطعات پیچیده با سطح صافتر تولید میکند. این روش نقصهای داخلی را تا 30% کاهش میدهد، اما نیاز به کنترل دقیق دما دارد تا از مشکلات ساختاری جلوگیری شود . این برای قطعات دقیق هوافضا کاربرد دارد.
- افزودن عناصر جدید: افزودن عناصر خاکی کمیاب (مانند سریم) به 100Cr6، دانههای فولاد را ریزتر کرده و مقاومت در برابر زنگزدگی را در محیطهای شور (مانند محلول 0.1 mol/L NaCl) تا 1.5 برابر بهبود میدهد. این ویژگی برای توربینهای بادی در مناطق ساحلی مناسب است.
انواع یاتاقان های صنعتی و کاربرد آن
یاتاقان (Bearing) از مهمترین اجزای مکانیکی در سیستمهای صنعتی و تجهیزات دوار ا...معادلهای فولاد 100Cr6 در استانداردهای جهانی
فولاد 100Cr6، یک فولاد پرکربن و پرکروم برای یاتاقانها، در استانداردهای مختلف جهانی با نامهای متفاوتی شناخته میشود. جدول زیر معادلهای این فولاد را در استانداردهای رایج نشان میدهد، که همگی خواص مشابهی برای کاربردهای یاتاقانی و قطعات دقیق دارند.
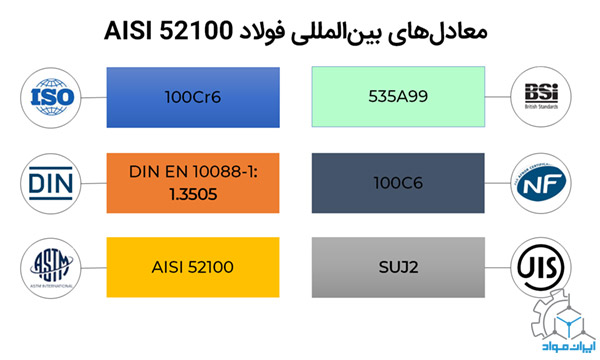
تمامی گریدهای فوق دارای ترکیب شیمیایی نزدیک (حدود 0.95–1.05% کربن و 1.35–1.65% کروم) و خواص مشابه برای کاربردهای یاتاقانی هستند. تفاوتهای جزئی در حداکثر گوگرد یا فسفر (مانند ≤0.015% در 100Cr6 در مقابل ≤0.020% در SUJ2) ممکن است روی کیفیت سطح یا فرایند تولید تأثیر بگذارد .برای انتخاب گرید مناسب، استاندارد محلی و الزامات کیفی پروژه باید بررسی شوند.
نتیجهگیری
فولاد 100Cr6 به دلیل ترکیب پرکربن و کروم، مادهای کلیدی برای یاتاقانهای غلتشی در صنایع خودروسازی و هوافضا است. عملیات حرارتی مانند کوئنچینگ و تمپرینگ، ساختاری مقاوم با کاربیدهای پایدار ایجاد میکند که برای قطعات تحت تنش مناسب است. این ویژگیها 100Cr6 را به گزینهای پرکاربرد برای بلبرینگها و محورهای دقیق تبدیل کرده است.
این فولاد در خودروها (مانند بلبرینگهای چرخ تویوتا) و ماشینآلات (مانند پمپهای هیدرولیکی) به دلیل دوام در برابر تنشهای تکراری استفاده میشود، اما عملکرد ضعیف در دماهای بالای 150°C یک محدودیت است. تحقیقات جدید، مانند پوششهای W-DLC، مقاومت در برابر زنگزدگی را برای کاربردهای دریایی بهبود داده و تیکسوفورمینگ قطعات دقیقتری تولید میکند.
دیدگاه کاربران