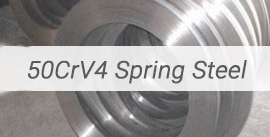
چدن خاکستری چیست و چه ویژگیهایی دارد؟
خواص مکانیکی و رفتاری این ماده به شدت تحت تأثیر ساختار گرافیتی آن قرار دارد که در مقاطع شکست، رنگ خاکستری منحصربهفردی را ایجاد میکند. استانداردهای معتبر مانند DIN EN 1561 نیز ترکیب شیمیایی و خواص مکانیکی چدن خاکستری را مشخص کردهاند و انواع آن را بر اساس میکروساختار و ویژگیهای عملکردی طبقهبندی میکنند.
در این مقاله، با بهرهگیری از استانداردهای معتبر و منابع علمی، به بررسی جامع جنبههای مختلف چدن خاکستری پرداخته خواهد شد و جایگاه آن در مقایسه با دیگر چدنها و آلیاژها مورد تحلیل قرار خواهد گرفت.
چدن خاکستری چیست؟
چدن خاکستری (Gray Cast Iron) یک آلیاژ آهنی-کربنی است که در آن کربن به شکل گرافیتهای ورقهای رسوب میکند. مطابق با استاندارد ISO 185، چدن خاکستری آلیاژی به میگویند که در مقطع شکست خود، رنگ خاکستری دارد که ناشی از حضور گرافیتهای صفحهای در ساختار آن است. این گرافیتها علاوه بر تأثیر بر خواص مکانیکی، به دلیل هدایت حرارتی و جذب ارتعاش بالا، عملکرد قابلتوجهی در صنایع مختلف ایجاد میکنند.
ساختار میکروسکوپی این آلیاژ از گرافیتهای ورقهای پراکنده در زمینهای ماتریسی (که میتواند فریتی، پرلیتی یا ترکیبی از این دو باشد) تشکیل شده است. اندازه، توزیع و جهتگیری گرافیتها تأثیر مستقیمی بر خواص مکانیکی چدن خاکستری دارد که بر اساس استاندارد ASTM A247 به دستههای مختلف تقسیمبندی میشود.
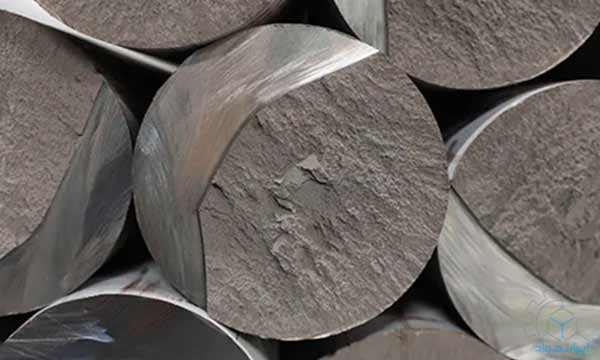
تاریخچه
چدن خاکستری یکی از قدیمیترین آلیاژهای آهن است که استفاده از آن به قرون وسطی بازمیگردد. اولین مستندات تولید چدن در چین و هند ثبت شده است. با ظهور انقلاب صنعتی در قرن 18 میلادی و پیشرفت فناوریهای ریختهگری، تولید چدن خاکستری در اروپا گسترش چشمگیری یافت.
مطابق با گزارشهای تاریخی، چدن خاکستری به طور گسترده در ساخت قطعات ماشینآلات صنعتی، لولههای انتقال آب و دیگهای بخار استفاده میشد. استانداردسازی ترکیب و فرآیند تولید این آلیاژ برای اولین بار در اواخر قرن 19 توسط اتحادیههای صنعتی انجام شد و توسعه آن با معرفی استانداردهایی مانندDIN EN 1561 و ASTM A48 ادامه یافت.
در طول دهههای اخیر، به دلیل خواص مکانیکی قابل تغییر و قابلیت ریختهگری بالا، چدن خاکستری همچنان به عنوان یکی از پرکاربردترین آلیاژهای آهنی در صنایع خودروسازی، ساخت ماشینآلات و ابزارهای صنعتی باقی مانده است. این آلیاژ در میان تمام چدنها، بالاترین میزان تولید جهانی را دارد و مطابق گزارشهای World Foundry Organization (WFO)، بیش از 50 درصد قطعات چدنی تولیدشده در جهان به چدن خاکستری اختصاص دارد.
امروزه، با پیشرفت فناوریهای ریختهگری و کنترل دقیق ساختار میکروسکوپی، تولید چدن خاکستری با کیفیت بالا برای کاربردهای پیشرفتهتری ممکن شده است. این پیشرفتها شامل توسعه فرآیندهای بهینه برای کاهش ترکخوردگی، بهبود استحکام و افزایش مقاومت به سایش است که در استانداردهای مدرن منعکس شده است.
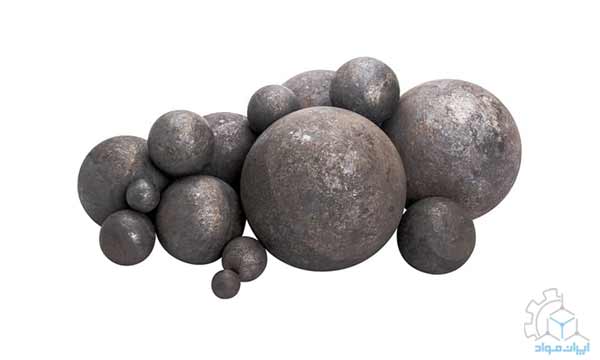
اثر ساختار گرافیتی بر روی ظاهر و خواص چدن
چدن خاکستری به دلیل ظاهر خاص سطح مقطع شکست خود به این نام شناخته میشود. وقتی یک قطعه چدن خاکستری شکسته میشود، سطح شکست آن رنگ خاکستری تیره یا روشن دارد. این رنگ ناشی از حضور گرافیتهای ورقهای در ساختار آن است که نور را به طور نامنظم بازتاب میدهند.
ساختار گرافیتی چدن خاکستری یکی از مهمترین ویژگیهای آن است که به دلیل نحوه توزیع و شکلگیری گرافیت در هنگام انجماد، این رنگ خاکستری پدیدار میشود. در مقابل، سایر انواع چدن مانند چدن سفید، به دلیل نبود گرافیت و حضور کاربید آهن (Fe₃C)، سطح شکست سفیدرنگ و براق دارند. این تفاوت ظاهری یکی از سادهترین روشها برای تمایز میان انواع چدن است.
چدن سفید چیست و چه انواعی دارد؟
چدن یکی از مهمترین گروههای آلیاژی آهنی است که به دلیل خواص متنوع خود در صنایع ...این ساختار علاوه بر رنگ، خواص مکانیکی خاصی مانند جذب ارتعاش و هدایت حرارتی بالا را نیز ایجاد میکند. برخلاف چدنهای سفید و نشکن، گرافیتهای ورقهای در چدن خاکستری تمرکز تنش را افزایش میدهند که منجر به کاهش استحکام کششی میشود اما در عوض مقاومت به سایش و قابلیت ریختهگری آن را بهبود میبخشند.
در نتیجه، چدن خاکستری نه تنها از لحاظ ظاهری بلکه از نظر خواص ساختاری و مکانیکی نیز با دیگر چدنها تفاوت دارد و این ویژگیها باعث شده است که این ماده در کاربردهایی که نیاز به جذب ارتعاش و ریختهگری پیچیده دارند، ارجحیت پیدا کند.
ترکیب شیمیایی چدن خاکستری
چدن خاکستری آلیاژی چندجزئی است که عناصر اصلی آن آهن، کربن، و سیلیسیم هستند. علاوه بر این، حضور عناصر آلیاژی مختلف میتواند برای بهبود خواص مکانیکی، ریختهگری، و میکروساختار آن تنظیم شود. ترکیب شیمیایی دقیق این آلیاژ، بر اساس استانداردهای معتبر مانندISO 185 و ASTM A48 تعیین میشود.
عنصر | درصد وزنی (تقریبی) | تأثیر در خواص و ساختار |
کربن (C) | 2.5-4 | -عامل تشکیل گرافیت یا کاربید در ساختار. -افزایش میزان کربن، شکلگیری گرافیتهای ورقهای را تسهیل میکند. |
سیلیسیم (Si) | 1.0-3.0 | -تقویت تشکیل گرافیت و جلوگیری از تشکیل سمنتیت. -بهبود قابلیت ریختهگری و کاهش دمای انجماد. |
گوگرد (S) | ≤ 0.1 | در مقادیر بالا باعث تشکیل کاربید آهن و کاهش انعطافپذیری میشود. |
فسفر (P) | ≤ 0.1 | بهبود قابلیت ماشینکاری، اما در مقادیر بالا شکنندگی را افزایش میدهد. |
منگنز (Mn) | 0.5-1.0 | کنترل تشکیل کاربیدها و بهبود استحکام و سختی. |
عناصر آلیاژی به منظور بهبود خواص مکانیکی، مقاومت در برابر خوردگی و کنترل ساختار میکروسکوپی به چدن خاکستری اضافه میشوند. این عناصر شامل موارد زیر هستند:
عنصر | درصد وزنی (تقریبی) | نقش در خواص چدن خاکستری |
نیکل (Ni) | 0.5-2.0 | – بهبود استحکام و مقاومت در برابر ضربه. – کاهش ترکپذیری در قطعات بزرگ. |
کروم (Cr) | 0.1-0.5 | افزایش مقاومت به سایش و خوردگی. |
مولیبدن (Mo) | 0.1-0.3 | افزایش مقاومت به خستگی حرارتی و پایداری ساختاری. |
مس (Cu) | 0.5-1.0 | بهبود استحکام کششی و مقاومت به خوردگی در محیطهای مرطوب. |
آلومینیوم (Al) | 0.01-0.05 | بهبود کیفیت سطح و کاهش تخلخل در قطعات ریختهگری. |
تأثیر ترکیب شیمیایی بر ساختار و خواص
- نسبت کربن به سیلیسیم (C/Si ratio) تعیینکننده حضور گرافیت ورقهای یا کاربید آهن در ساختار است.
- افزایش سیلیسیم باعث تسهیل تشکیل گرافیت و کاهش ترکپذیری میشود.
- عناصر نیکل، کروم و مس معمولاً برای قطعاتی با نیاز به مقاومت بالا به خوردگی یا دماهای بالا اضافه میشوند.
- فسفر و گوگرد باید در مقادیر بسیار کم کنترل شوند، زیرا مقادیر بالای آنها شکنندگی را افزایش میدهد.
ترکیب شیمیایی گریدهای چدن خاکستری بر اساس استانداردASTM A48
استاندارد ASTM A48 برای چدن خاکستری طیفی از کلاسهای مختلف را بر اساس حداقل استحکام کششی آنها (برحسبpsi) طبقهبندی کرده است. جدول زیر ترکیب شیمیایی عمومی این کلاسها را نشان میدهد. توجه داشته باشید که در ASTM A48 به طور مستقیم محدوده دقیق ترکیب شیمیایی برای هر کلاس ارائه نشده است، اما مقادیر زیر به عنوان محدودههای معمول در صنایع ریختهگری پذیرفته شدهاند:
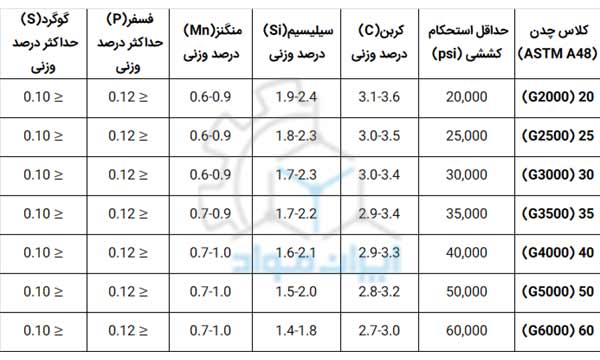
توضیحات جدول 3
- حداقل استحکام کششی: عدد کلاس مانند G2000به استحکام کششی حداقل در واحد psi اشاره دارد. برای مثال، کلاس G2000 دارای حداقل استحکام کششی 20,000 psi است.
- کربن و سیلیسیم: مقادیر کربن و سیلیسیم به طور تقریبی محدودههای مورد استفاده در صنایع هستند و ممکن است با توجه به کاربرد نهایی و فرآیند تولید تغییر کنند.
- فسفر و گوگرد: مقادیر فسفر و گوگرد در تمام کلاسها باید پایین نگه داشته شوند تا شکنندگی و تشکیل کاربید آهن (Fe₃C) کنترل شود.
انواع چدن خاکستری
چدن خاکستری به دلیل تنوع در ترکیب شیمیایی، میکروساختار و خواص مکانیکی، در دستههای مختلفی طبقهبندی میشود. این طبقهبندی میتواند بر اساس ساختار میکروسکوپی (زمینه ماتریس)، شکل گرافیت، و کاربردهای صنعتی انجام شود. در ادامه، انواع چدن خاکستری را بر اساس این معیارها بررسی میکنیم.
1- طبقهبندی بر اساس میکروساختار (زمینه ماتریسی)
زمینه ماتریسی چدن خاکستری شامل فازهای اصلی مانند فریت و پرلیت است که با کنترل ترکیب شیمیایی و سرعت سرد شدن حین ریختهگری شکل میگیرند.
نوع چدن خاکستری | ویژگیهای میکروساختار | خواص مکانیکی | کاربردها |
فریتی | گرافیتهای ورقهای در زمینهای عمدتاً فریتی | انعطافپذیری بالا، استحکام کم | ساخت قطعات کمفشار مانند پوستهها و قابها |
پرلیتی | گرافیتهای ورقهای در زمینهای عمدتاً پرلیتی | استحکام کششی و سختی بالا، چقرمگی کمتر | دیسکهای ترمز، چرخدندهها، قطعات مقاوم به سایش |
فریتی-پرلیتی | ترکیبی از زمینههای فریتی و پرلیتی | تعادل بین استحکام و انعطافپذیری | قطعات با خواص چندمنظوره، مثل سرسیلندرها |
تمپرشده (Annealed) | گرافیتهای ورقهای در زمینهای اصلاحشده با عملیات حرارتی | کاهش تنشهای داخلی و افزایش چقرمگی | قطعات ریختهگری پیچیده و مقاوم به شوک حرارتی |
2- طبقهبندی بر اساس شکل گرافیت
مطابق استاندارد ASTM A247، گرافیت موجود در چدن خاکستری میتواند از لحاظ اندازه، توزیع و شکل طبقهبندی شود. این ویژگیها تأثیر مستقیمی بر رفتار مکانیکی و فیزیکی ماده دارند.
نوع گرافیت | ویژگیهای گرافیت | تأثیر بر خواص | کاربردها |
نوع A(یونیفرم) | گرافیتهای ورقهای یکنواخت و منظم | استحکام کششی و انعطافپذیری مطلوب | دیسکهای ترمز، بلوکهای موتور |
نوع B (روزیتهای) | گرافیتهای روزیتهای و پراکنده | سختی بیشتر، استحکام کمتر | قطعاتی با نیاز به سختی سطحی |
نوع C (گرافیتی) | گرافیتهای درشت و پراکنده | هدایت حرارتی و جذب ارتعاش بالا | قالبهای ریختهگری، صفحات ماشینآلات |
نوع D (گرافیت ریز) | گرافیتهای ریز و پراکنده | استحکام کششی و سختی بالا | قطعات ظریف با نیاز به دقت بالا |
نوع E (غیر یکنواخت) | گرافیتهای ورقهای نامنظم | خواص متغیر، شکنندگی بیشتر | قطعات کماهمیت یا اقتصادی |
3- طبقهبندی بر اساس کاربرد و عملکرد
چدن خاکستری بر اساس کاربرد و نیازهای عملکردی، در دستههای مختلفی قرار میگیرد:
دستهبندی کاربردی | ویژگیها | نمونه کاربردها |
چدن خاکستری استاندارد | خواص مکانیکی عمومی، تولید آسان | بلوکهای موتور، پوستههای ماشینآلات |
چدن خاکستری مقاوم به سایش | افزودن عناصر آلیاژی (مانند کروم و نیکل) برای مقاومت بیشتر | دیسکهای ترمز، چرخدندهها، لنتهای صنعتی |
چدن خاکستری مقاوم به خوردگی | حاوی مس یا نیکل برای مقاومت به زنگزدگی | پمپهای صنعتی، لولههای انتقال سیالات خورنده |
چدن خاکستری برای جذب ارتعاش | گرافیتهای بزرگ و توزیع یکنواخت | پایههای ماشینآلات، میزهای تراشکاری |
خواص مکانیکی چدن خاکستری
چدن خاکستری به دلیل وجود گرافیت ورقهای در ساختار خود، خواص مکانیکی منحصربهفردی دارد که آن را برای کاربردهای خاص صنعتی مناسب میسازد. این خواص تحت تأثیر عوامل مختلفی از جمله ترکیب شیمیایی، میکروساختار زمینه، و اندازه و توزیع گرافیت قرار دارند. در ادامه، ویژگیهای مکانیکی اصلی چدن خاکستری به تفصیل ارائه شده است.
1- استحکام (Strength)
-استحکام کششی (Tensile Strength):
استحکام کششی چدن خاکستری بر اساس کلاسهای استاندارد ASTM A48 تعیین میشود. این مقدار از 20,000 psi برای کلاس G2000 تا 60,000 psi برای کلاس G6000 متغیر است.
- چدنهای با زمینه پرلیتی استحکام بالاتری دارند.
- گرافیتهای ورقهای تنش را متمرکز میکنند، که این ویژگی استحکام کششی را نسبت به فولاد کاهش میدهد.
-استحکام فشاری (Compressive Strength):
چدن خاکستری استحکام فشاری بالایی دارد که معمولاً 3 تا 4 برابر استحکام کششی آن است. این خاصیت باعث میشود برای قطعاتی مانند پایههای ماشینآلات ایدهآل باشد.
2- سختی (Hardness)
سختی چدن خاکستری عمدتاً به میکروساختار زمینه آن بستگی دارد:
- چدنهای فریتی: سختی پایین (170 تا 220 برینل).
- چدنهای پرلیتی: سختی بالاتر (200 تا 300 برینل).
سختی چدن به راحتی با افزودن عناصر آلیاژی یا عملیات حرارتی قابل تغییر است که برای چدنهای سختکاری شسده با عملیات حرارتی تا 400 برینل هم میرود.
3- چقرمگی (Toughness)
چدن خاکستری به دلیل حضور گرافیت ورقهای در ساختار خود، چقرمگی پایینتری نسبت به دیگر آلیاژهای آهنی دارد. گرافیتهای ورقهای به دلیل ایجاد تمرکز تنش در نقاط مختلف، باعث کاهش مقاومت در برابر تنشهای ناگهانی میشوند. با این حال، نوع ساختار میکروسکوپی (زمینه فریتی یا پرلیتی) میتواند تأثیر قابلتوجهی بر میزان چقرمگی داشته باشد:
چدن با زمینه فریتی: چدنهای فریتی، به دلیل نرمتر بودن زمینه و انعطافپذیری بیشتر، چقرمگی بهتری دارند. محدوده انرژی ضربه قابلجذب در این نوع چدن معمولاً 5 تا 10 ژول است.
چدن با زمینه پرلیتی: چدنهای پرلیتی، به دلیل استحکام بالاتر زمینه، چقرمگی نسبی بیشتری نشان میدهند. محدوده چقرمگی آنها میتواند به 15 تا 20 ژول (برای آزمون شارپی) برسد. این نوع چدن برای کاربردهایی که نیاز به استحکام و چقرمگی بالاتر دارند (مانند دیسکهای ترمز و چرخدندهها) مناسبتر است.
چدن با زمینه ترکیبی (فریتی-پرلیتی): چدنهای با زمینه ترکیبی تعادلی میان چقرمگی و استحکام ارائه میدهند و برای قطعاتی که نیاز به خواص چندمنظوره دارند (مانند سرسیلندرها)، انتخاب ایدهآلی هستند.
عوامل مؤثر بر افزایش چقرمگی
- استفاده از گرافیتهای ورقهای یکنواخت (نوع A مطابق استاندارد ASTM A247) میتواند تمرکز تنش را کاهش داده و چقرمگی را بهبود بخشد.
- افزودن مقادیر کمی از عناصر آلیاژی مانند نیکل و مولیبدن میتواند چقرمگی را در چدنهای پرلیتی افزایش دهد.
- کاهش فسفر و گوگرد در ترکیب شیمیایی به کنترل شکنندگی و افزایش چقرمگی کمک میکند.
چدنهای پرلیتی به دلیل چقرمگی نسبی بالاتر، برای کاربردهایی که نیاز به مقاومت در برابر ضربه دارند، مناسبتر هستند. در مقابل، چدنهای فریتی به دلیل انعطافپذیری بالا، در قطعاتی که تنش کمتری تحمل میکنند، ارجحیت دارند.
4- رفتار در برابر ضربه (Impact Resistance)
مقاومت به ضربه چدن خاکستری نسبت به فولاد یا چدن نشکن کمتر است. این خاصیت به شدت به اندازه و توزیع گرافیتها بستگی دارد.
- گرافیتهای بزرگتر (در چدنهای کلاس پایینتر) مقاومت به ضربه کمتری ایجاد میکنند.
مقدار انرژی ضربه قابل جذب معمولاً در محدوده 5 تا 15 ژول (برای آزمون شارپی) است.
5- رفتار در برابر خستگی (Fatigue Resistance)
چدن خاکستری مقاومت خستگی کمتری نسبت به فولاد دارد، زیرا تمرکز تنش در اطراف گرافیتهای ورقهای، رشد ترک را تسریع میکند. معمولاً مقاومت خستگی چدن خاکستری در حدود 35 تا 50 درصد استحکام کششی آن است.
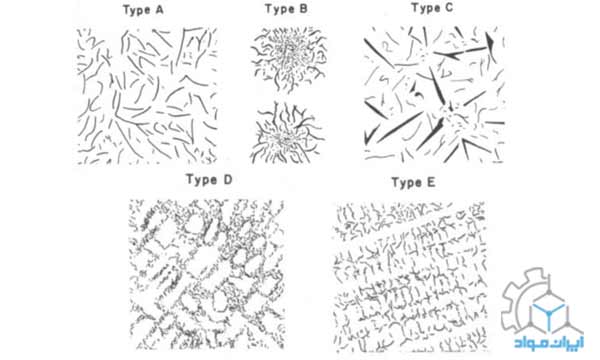
فرآیند تولید چدن خاکستری
تولید چدن خاکستری شامل مجموعهای از مراحل از ذوب مواد اولیه تا ریختهگری و سرد کردن محصول است. هدف اصلی در این فرآیند، دستیابی به ساختار میکروسکوپی مطلوب (گرافیت ورقهای در زمینهای فریتی یا پرلیتی) و کنترل خواص مکانیکی مورد نیاز است.
ذوب مواد اولیه
یکی از مراحل مهم در تولید چدن خاکستری، ذوب مواد اولیه است. مواد اولیه شامل آهن خام، فولاد قراضه و مواد آلیاژی مانند سیلیسیم، منگنز، و در برخی موارد نیکل یا کروم هستند. این مواد در کورههای القایی یا کورههای کوپل ذوب میشوند. دمای ذوب چدن خاکستری معمولاً در بازه 1200 تا 1300 درجه سانتیگراد قرار دارد. کنترل دقیق دمای ذوب بسیار حیاتی است، زیرا دمای نامناسب میتواند منجر به تشکیل کاربید آهن (Fe₃C) شود که باعث کاهش انعطافپذیری و خواص مکانیکی ماده میگردد. حفظ تعادل مناسب بین کربن و سیلیسیم در این مرحله برای تشکیل ساختار گرافیتی مطلوب ضروری است.
اصلاح ترکیب شیمیایی
در این مرحله، ترکیب شیمیایی چدن برای دستیابی به خواص مکانیکی و ساختاری مطلوب تنظیم میشود.
افزودن سیلیسیم به مذاب به منظور تسهیل تشکیل گرافیت و جلوگیری از تشکیل کاربید انجام میشود.
منگنز برای کنترل تشکیل کاربیدها و بهبود سختی چدن اضافه میشود.
مقادیر فسفر و گوگرد نیز باید به دقت کنترل شوند، زیرا این عناصر میتوانند شکنندگی را افزایش دهند.
یکی از تکنیکهای مهم در این مرحله، دانهزایی (Inoculation) است. در این فرآیند، موادی مانند فروسیلیس یا کربناتها به مذاب اضافه میشوند تا تعداد جوانههای گرافیتی افزایش یافته و توزیع یکنواختتری در ساختار ایجاد شود. این تکنیک به بهبود خواص مکانیکی و کاهش نقصهای ساختاری کمک میکند.
ریختهگری و انجماد
نحوه ریختهگری و سرعت انجماد در تعیین ساختار نهایی چدن خاکستری نقش مهمی دارد.
سرعت سرد شدن آهستهتر باعث تشکیل گرافیتهای ورقهای نوع A میشود که توزیع یکنواختتری دارند و خواص مکانیکی بهتری ایجاد میکنند.
سرد شدن سریع ممکن است منجر به تشکیل کاربیدها شود که باعث افزایش سختی اما کاهش چقرمگی و انعطافپذیری میشود.
همچنین، محیط سرد شدن نقش مهمی ایفا میکند. ریختهگری در قالبهای ماسهای به دلیل سرد شدن آهستهتر، برای تولید ساختار گرافیتی مطلوب مناسبتر است، در حالی که قالبهای فلزی سرعت سرد شدن بالاتری دارند و ممکن است خواص متفاوتی ایجاد کنند.
عملیات حرارتی (در صورت نیاز)
برای بهبود خواص نهایی، ممکن است عملیات حرارتی روی چدن خاکستری انجام شود.
بازپخت (Annealing): این فرآیند تنشهای داخلی را کاهش میدهد و چقرمگی را بهبود میبخشد.
سختکاری سطحی: برای قطعاتی که نیاز به مقاومت به سایش دارند، سختکاری سطحی روی چدن پرلیتی انجام میشود.
استانداردها و کنترل کیفیت
برای اطمینان از کیفیت چدن خاکستری تولیدشده، آزمایشهای مختلفی مطابق با استانداردهای بینالمللی انجام میشوند:
آنالیز شیمیایی: با استفاده از روشهای اسپکتروسکوپی، درصد عناصر کلیدی مانند کربن، سیلیسیم، منگنز، فسفر و گوگرد اندازهگیری میشود.
آزمون میکروسکوپی: توزیع، شکل و اندازه گرافیتها طبق استاندارد ASTM A247 بررسی میشود.
آزمون خواص مکانیکی: ویژگیهایی مانند استحکام کششی، سختی و مقاومت به ضربه طبق استاندارد ASTM A48 اندازهگیری میشوند.
کنترل دقیق ترکیب شیمیایی، شرایط ریختهگری، و مراحل انجماد برای دستیابی به خواص مکانیکی و میکروسکوپی مطلوب در چدن خاکستری ضروری است. با استفاده از تکنیکهای مدرن ریختهگری و رعایت استانداردهای کیفی، میتوان چدن خاکستری را با خواص بهینه برای کاربردهای متنوع صنعتی تولید کرد.
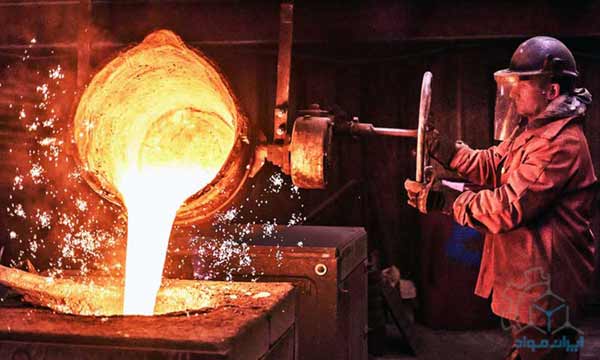
نامگذاری چدن خاکستری در استانداردهای مختلف
چدن خاکستری در استانداردهای بینالمللی مانند ASTM، DIN، و ISO به طور دقیق طبقهبندی و نامگذاری شده است. این استانداردها خواص مکانیکی، ترکیب شیمیایی و میکروساختار چدن خاکستری را تعریف و کدهای مشخصی برای شناسایی آن ارائه میدهند. در ادامه، جزئیات استانداردهای اصلی برای چدن خاکستری در قالب جدول آورده شده است.
استاندارد | معیار اصلی طبقهبندی | روش نامگذاری | توضیحات |
ASTM A48 | حداقل استحکام کششی | GXXXX مانند G3000 | XXXX نشاندهنده حداقل استحکام کششی بر حسب psi است. مثلاً G3000 به چدنی با حداقل استحکام 30,000 psi اشاره دارد. |
ISO 185 | حداقل استحکام کششی | EN-GJL-XXXX | EN-GJL نشاندهنده چدن خاکستری است. XXXX مقدار حداقل استحکام کششی بر حسب MPa است. |
DIN EN 1561 | حداقل استحکام کششی | EN-GJL-XXXX | همانند ISO 185 از EN-GJL برای چدن خاکستری استفاده میشود. استحکام کششی بر حسب MPa است. |
JIS G5501 (ژاپن) | حداقل استحکام کششی | FC-XX | FC نشاندهنده چدن خاکستری است. XX مقدار حداقل استحکام کششی را به کیلوگرمبرمیلیمتر مربع نشان میدهد. |
مقایسه خواص چدن خاکستری با دیگر چدنها
چدن خاکستری از لحاظ ساختار، خواص و ظاهر سطح شکست، تفاوتهای بارزی با دیگر انواع چدن دارد:
- چدن سفید: در چدن سفید، کربن به صورت کاربید آهن (سمنتیت) حضور دارد و نه به شکل گرافیت. این ساختار باعث میشود که سطح شکست بسیار سخت و سفیدرنگ باشد. چدن سفید استحکام فشاری بالایی دارد، اما شکنندهتر است و به دلیل سختی بالا، کمتر در کاربردهای ضربهای استفاده میشود.
- چدن نشکن (داکتیل): در چدن نشکن، گرافیت به صورت کروی (گرافیت کروی) توزیع شده است. این توزیع باعث بهبود خواص مکانیکی مانند استحکام کششی و چقرمگی میشود. برخلاف چدن خاکستری، چدن نشکن هنگام شکست ظاهر سیاه یا خاکستری تیرهتری دارد، زیرا ساختار گرافیتی آن به صورت کروی، نور را کمتر بازتاب میدهد.
- چدن مالیبل: چدن مالیبل (Malleable Cast Iron) نیز دارای گرافیتهای گلولهای است که از طریق عملیات حرارتی روی چدن سفید تولید میشود. این نوع چدن انعطافپذیری بیشتری دارد و سطح شکست آن به دلیل گرافیت گلولهای، کمتر خاکستری و بیشتر به رنگ سیاه یا خاکستری تیره دیده میشود.
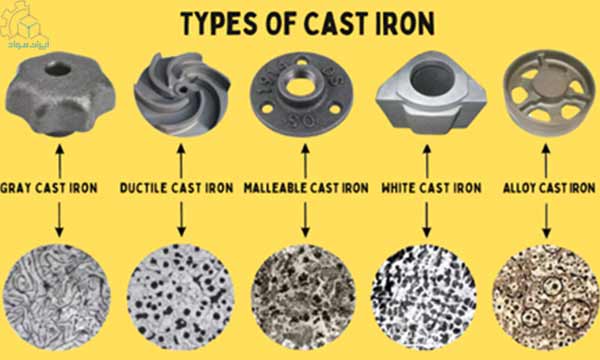
چدن خاکستری با دیگر چدنها از نظر خواص مکانیکی، ساختار و کاربرد مقایسه شده است.
در جدولهای زیر، خواص مکانیکی، مزایا و محدودیتها و کاربردهای رایج چدنهای مختلف با استفاده از محدودههای عددی مشخص شده است. این اعداد بر اساس استانداردهای موجود ارائه شدهاند.
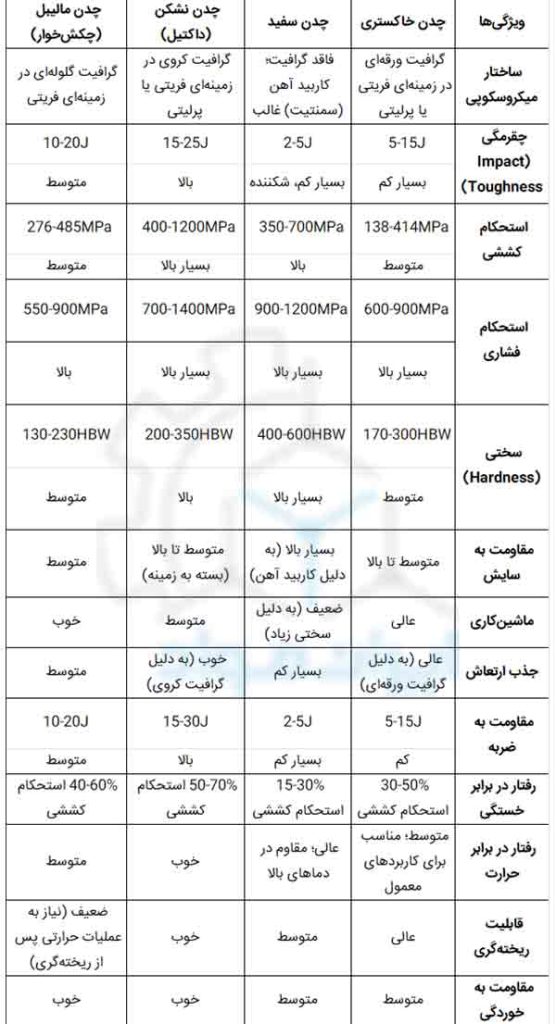
مزایا | محدودیتها |
جذب ارتعاش عالی، مناسب برای کاربردهای ماشینی | استحکام کششی و چقرمگی پایین در مقایسه با چدن نشکن |
ماشینکاری ساده و اقتصادی | مقاومت کم در برابر ضربه و تنشهای ناگهانی |
ریختهگری آسان و قابلیت تولید قطعات بزرگ | مقاومت خستگی پایین در شرایط تنش متناوب |
هزینه تولید پایین | چقرمگی کم در مقایسه با چدن مالیبل و نشکن |
نوع چدن | کاربردهای رایج |
چدن خاکستری | بلوک موتور، دیسکهای ترمز، میزهای ماشینآلات، پوستهها و قابهای صنعتی |
چدن سفید | رولهای آسیاب، لنتهای صنعتی، قطعات مقاوم به سایش |
چدن نشکن | قطعات خودرو (میللنگ، بازوهای تعلیق)، پمپها و شیرآلات، قطعات تحت ضربه |
چدن مالیبل | قطعات کوچک مقاوم به ضربه، ابزارهای کشاورزی، بستهای چدنی، اجزای سازهای |
در نهایت، چدن خاکستری به دلیل هزینه پایین تولید، جذب ارتعاش عالی و ماشینکاری ساده، برای کاربردهایی که نیازی به استحکام یا چقرمگی بالا ندارند، ایدهآل است. در مقابل، چدن سفید برای مقاومت به سایش، چدن نشکن برای استحکام و چقرمگی، و چدن مالیبل برای کاربردهای ضربهای و چکشخوار مناسبتر هستند.
انواع چدن با قابلیت ماشینکاری بالا
چدنها از جمله آلیاژهای صنعتی کاربردی هستند که به دلیل ویژگیهای فیزیکی و مکانیک...کاربردهای چدن خاکستری و دلایل انتخاب آن
چدن خاکستری به دلیل خواصی مانند ماشینکاری آسان، جذب ارتعاش عالی، هدایت حرارتی مناسب، و هزینه تولید پایین، در صنایع مختلف بهطور گستردهای استفاده میشود. گرافیت ورقهای موجود در ساختار آن، علاوه بر بهبود خواص مکانیکی، ویژگیهایی همچون کاهش سر و صدا و ارتعاشات را فراهم میکند، که در کاربردهای زیر نقش کلیدی دارند:
- صنعت خودروسازی:
- بلوکهای موتور و سرسیلندرها: چدن خاکستری به دلیل مقاومت به حرارت، جذب ارتعاش بالا، و هدایت حرارتی مناسب، در قطعات موتور استفاده میشود.
- دیسکهای ترمز و درامها: هدایت حرارتی بالای چدن خاکستری به پخش سریعتر گرما در دیسکهای ترمز کمک میکند. این خاصیت از تجمع حرارت در یک نقطه جلوگیری کرده و خطر تغییر شکل یا خرابی ناشی از گرمای زیاد را کاهش میدهد. همچنین، انتقال حرارت مطلوب باعث افزایش طول عمر دیسک و کاهش خستگی حرارتی میشود.
- ماشینآلات صنعتی:
- میزهای ماشینآلات و پایهها: خاصیت جذب ارتعاش چدن خاکستری که ناشی از وجود گرافیت ورقهای در ساختار آن است، باعث کاهش لرزش و نویز در ماشینآلات میشود. این ویژگی دقت عملکرد دستگاه را بهبود میبخشد و از آسیب به قطعات مکانیکی جلوگیری میکند.
- چرخدندهها و پوششها: مقاومت به سایش چدن خاکستری، آن را برای قطعاتی که در تماس دائمی با سطوح دیگر هستند، مانند چرخدندهها یا پوششهای محافظ، مناسب میسازد. این ویژگی باعث کاهش هزینههای تعمیر و نگهداری میشود.
- صنعت لوله و انتقال سیالات:
- لولهها و اتصالات: مقاومت به خوردگی داخلی و هزینه پایین تولید، چدن خاکستری را برای لولههای انتقال آب و فاضلاب ایدهآل کرده است.
- صنایع انرژی و زیرساخت:
- دیگهای بخار و قابهای بزرگ: استحکام فشاری چدن خاکستری برای تحمل تنشهای ناشی از فشار در بلوکهای موتور یا دیگهای بخار ضروری است. این خاصیت به قطعات اجازه میدهد در شرایط عملیاتی سخت، پایداری مکانیکی خود را حفظ کنند.
- ابزارهای روزمره و قطعات کمفشار:
- پوستهها و قابهای تجهیزات: قابلیت ماشینکاری بالا، تولید قطعات پیچیده مانند قابها و پوستههای صنعتی را با هزینه پایین و دقت بالا امکانپذیر میسازد. این ویژگی به ویژه در کاربردهایی که نیاز به تولید انبوه دارند، اهمیت دارد.
در نتیجه، چدن خاکستری در صنایع مختلف، بهویژه در قطعاتی که خواص مکانیکی متوسط همراه با هزینه تولید کم مورد نیاز است، انتخابی ایدهآل است.
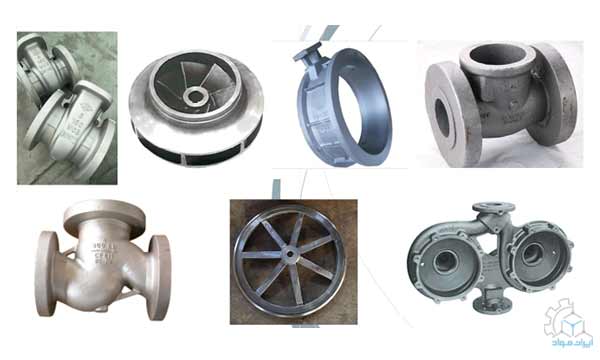
آینده و نوآوریها در چدن خاکستری
چدن خاکستری با وجود قدمت زیاد، همچنان در صنایع مدرن جایگاه خود را حفظ کرده است و با پیشرفت فناوری، اصلاحاتی در ترکیب شیمیایی و فرآیند تولید آن ایجاد شده است تا بتواند در کاربردهای نوین نیز رقابت کند.
1– اصلاحات جدید در ترکیب و فرآیند
- افزودن عناصر آلیاژی پیشرفته: استفاده از عناصر آلیاژی مانند مس، نیکل، و مولیبدن برای افزایش مقاومت به خوردگی، استحکام حرارتی، و طول عمر قطعات.
- کنترل دقیق ساختار گرافیتی: با بهرهگیری از فناوریهای پیشرفته دانهزایی (Inoculation)، توزیع گرافیتها یکنواختتر شده و خواص مکانیکی بهبود یافته است.
- فناوری ریختهگری دقیق: استفاده از قالبهای مدرن و شبیهسازی انجماد برای کاهش نقصها و تولید قطعات پیچیدهتر.
2– استفاده در صنایع نوین
- صنایع خودروسازی پیشرفته: چدن خاکستری در تولید بلوکهای موتورهای سبک و کممصرف همچنان جایگاه دارد و با بهبود ترکیب آن، وزن قطعات کاهش یافته و بهرهوری سوخت افزایش مییابد.
- انرژیهای نوین: در توربینهای بادی و تجهیزات مرتبط با انرژیهای تجدیدپذیر، به دلیل جذب ارتعاش بالا و دوام، از چدن خاکستری استفاده میشود.
- فناوری چاپ سهبعدی (Additive Manufacturing): آزمایشهایی در حال انجام است تا از چدن خاکستری در فرایندهای تولید افزایشی برای تولید قطعات سفارشی بهرهبرداری شود.
- صنایع الکترونیک و حملونقل ریلی: استفاده در تولید قابهای تجهیزات سنگین و قطعات مقاوم به ارتعاش، با تمرکز بر طول عمر بالا و کاهش هزینهها.
جمعبندی
چدن خاکستری به عنوان یکی از پرکاربردترین آلیاژهای آهنی، به دلیل خواصی مانند جذب ارتعاش عالی، هدایت حرارتی مناسب، ماشینکاری آسان و هزینه تولید پایین، همچنان نقش کلیدی در صنایع مختلف ایفا میکند. ساختار گرافیتی ورقهای این ماده علاوه بر تأثیر بر خواص مکانیکی، ویژگیهایی چون کاهش نویز و ارتعاش را بهبود میبخشد و آن را برای کاربردهایی همچون قطعات خودرو، تجهیزات صنعتی و لولهکشی ایدهآل میسازد. با پیشرفت فناوریهای ریختهگری و بهبود ترکیب شیمیایی، چدن خاکستری در حوزههای جدیدتر از جمله انرژیهای نوین و تولید قطعات پیچیده نیز به کار گرفته میشود. این مزایا، همراه با تطبیقپذیری بالا، جایگاه این آلیاژ را در صنایع مدرن تثبیت کرده است.
دیدگاه کاربران