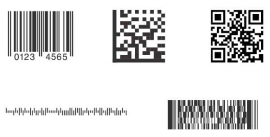
فروآلیاژها را تا چه حد می شناسید؟
فروآلیاژ چیست؟
به آلیاژی از آهن و عناصر دیگر که سهم عناصر دیگر در آلیاژ بیشتر از آهن باشد، فروآلیاژ (Ferroalloy) گفته می شود. البته این یک تعریف عمومی است و همواره صادق نیست. مثلا ممکن است در آلیاژ فروسیلیس، سهم سیلیسیم 15 درصد باشد.
سال های زیادی است که از فرو آلیاژها به عنوان آمیژان و مواد افزودنی به مذاب فلزات و فولادها در صنایع ریخته گری استفاده می شود تا تغییرات مورد نیاز را در خواص نهایی قطعه ایجاد کنند. طبق آمار سال 2014، مهم ترین تولید کنندگان فروآلیاژ در جهان، چین، آفریقای جنوبی، هند و روسیه و اوکراین بوده اند که حدود 84 درصد از کل عرضۀ جهانی (52.8 میلیون تن) سهم این کشورها بوده است.
تولید فروآلیاژ؛ از کوره های زمینی تا کوره قوس الکتریکی
تولید فروآلیاژها تا قبل از قرن 19 میلادی، با ذوب كانه های آهن يا سنگ های منگنزی آهن دار، در بوته های گرافيتی و یا کوره های زمينی انجام می شد. فرایند ذوب در این تولیدات، معمولا همراه با كک و ساير مواد احیاکننده انجام می شد.
قطعات تولیدی در این فرایندها، از نظر کیفیت و کارکرد، فقط در موارد معدودی ارزش صنعتی داشتند. در روش های قدیمی، فروآلياژهايی كه دمای ذوب بالایی داشتند، به علت نرسيدن به دماهای مناسب، باعث تولید قطعاتی غير یکنواخت می شدند.
تا سال 1920 آهن خام فقط در كوره بلند توليد می شد. از این رو در كوره بلند در عوض شارژ كردن كانه های آهن خالص، كانه های آهن منگنز دار، كروم دار و يا تيتانيم دار شارژ می شد. این فروآلیاژها معمولا عیار کمی داشتند.
با ساخته شدن ژنراتورها و توسعۀ نيروی برق، توليد فروآلياژها بهبود یافت و فرو آلیاژهایی مانند فروسيليسيم به توليد صنعتی رسيدند. به اين ترتيب، استفاده از كوره های قوس الكتريكی برای توليد فرو آلیاژها بهترين روش شناخته شد. امروزه کورۀ تولید فرو آلیاژ موسوم به کوره قوس الکتریکی زیر شارژی (Submerged Arc Furnace) بهترین گزینه برای تولید بسیاری از فروآلیاژها محسوب می شود.
کوره قوس الکتریکی (EAF)
یکی از روش های مهم تولید فولاد و چدن، ذوب و پالایش قطعات قراضه در کوره قوس الکتر...فروآلیاژها چگونه تولید می شوند؟
امروزه فرو آلیاژها با دو روش متداول تولید می شوند. تولید ذوبی در کورۀ بلند، یا در کورۀ قوس الکتریکی. با آغاز قرن بیستم میلادی، استفاده از کورۀ بلند کاهش یافت و به دنبال آن کوره های قوسی مورد توجه قرار گرفتند. اما هنوز هم برخی فرو آلیاژ ها مانند فرومنگنز در کورۀ بلند تولید می شوند.
آن چه به تولید اکثر فروآلیاژها منجر می شود، واکنش های کربوترمیک است. در این واکنش ها اکسیدهای موجود در مواد اولیۀ ذوب، با کربن موجود در کک و در حضور آهن احیا می شوند و فروآلیاژها را تشکیل می دهند. برخی از این آلیاژها نیز با اضافه کردن عناصر مورد نظر به آهن مذاب تولید می شوند.
برخی فروآلیاژها را می توان از طریق احیای مستقیم (Direct Reduction) نیز تولید کرد. برای مثال، در کشور ژاپن از فرایندی موسوم به krupp-renn برای تولید فرونیکل استفاده می شود که اساس آن احیای مستقیم مواد اولیۀ نیکل و آهن دار است.
چگونه می توان از فروآلیاژ استفاده کرد؟
متداول ترین عناصری که برای تولید فروآلیاژها به آهن اضافه می شوند عبارتند از سیلیسیم، منگنز، کروم، مولیبدن، وانادیوم، تیتانیوم، کبالت، نیکل، تنگستن و… اما شاید این سوال برای شما به وجود آمده باشد که چرا این عناصر را به شکل خالص به فولاد یا چدن اضافه نمی کنند؟
افزودن این عناصر به صورت خالص به آلیاژهای آهن (فولاد و چدن) به دو دلیل مهم زیر انجام شدنی نیست.
- این عناصر به صورت خالص بسیار گران هستند و هزینۀ تهیۀ آن ها اصلا صرفۀ اقتصادی ندارد.
- نقطه ذوب این عناصر در حالت خالص بسیار بیشتر از حالت آلیاژی است. تامین درجه حرارت مورد نیاز برای ذوب، علاوه بر ایجاد هزینه های بیشتر برای تولید، مشکلات فنی و دستگاهی نیز به دنبال دارد.
از این رو تولیدکنندگان مجبورند مثلا از فروآلیاژ سیلیسیم استفاده کنند برای این که سیلیسیم را به فولاد اضافه کنند. فروآلیاژها معمولاً نسبت به عناصر خالص، نقطه ذوب پایین تری دارند و به راحتی میتوانند با فولاد مذاب ترکیب شوند.
فروآلیاژها برای دستیابی به یک ترکیب شیمیایی مشخص به فولاد مذاب اضافه می شوند و خواص موردنیاز برای تهیه محصولات خاص را تأمین می کنند. برخی از عناصر موجود در فروآلیاژها، نقش جوانه زایی فازهای معینی از جمله گرافیت کروی و یا بهینه سازی و پالایش ریز ساختار را در آلیاژهای چدن و فولاد به عهده دارند. به این فروآلیاژها مواد تلقیحی یا جوانه زا (Inoculant) گفته می شود.
این مواد جوانه زا را نمی توان به طور مستقیم برای تولید یک قطعه مورد استفاده قرار داد، زیرا شکننده و نامناسب هستند. در حالی که این عناصر برای فولادهای آلیاژی منابع مفیدی هستند و با ترکیب شدن با آن ها ویژگی های مفیدی به آن ها می بخشند.
فروآلیاژهای مصرفی در صنایع فولادسازی کشور ما، به طور عمده برای تولید فولادهای ساده کربنی مورد استفاده قرار می گیرند. بنابراین بیشترین میزان فروآلیاژهای مورد استفاده در فرآیند تولید این محصولات، فروآلیاژهای حاوی منگنز و سیلیسیم است.
فولاد ساده کربنی ؛ پدر فولادهای صنعتی
فولاد مادر آلیاژهای صنعتی و یکی از ارکان علوم مهندسی به ویژه مهندسی متالورژی است...برای انتخاب نوع فروآلیاژ مورد استفاده باید صرفه اقتصادی و میزان بهرهوری آن مورد بررسی قرار گیرد و مشخص شود تا برای تولید فولاد مورد نظر استفاده از کدام از گزینهها مطلوب تر است.
مهم ترین فروآلیاژها
فروسیلیسیم
به جرئت می توان گفت فروسیلیسیم یا فروسیلیس، معروف ترین و پرمصرف ترین فروآلیاژ است. فروسیلیس آمیژانی است از آهن و سیلیسیم که با گرمایش، احیا و ذوب سنگ آهن و سیلیس (کوارتز) توسط کربن و معمولا در کوره های قوس تولید می شود.
ترکیب شیمیایی این آلیاژ عمدتا از 10 تا 90 درصد سیلیسیم و بقیه آهن تشکیل می شود. با این حال عناصر ناخالصی نظیر منگنز، کروم، فسفر، گوگرد، کربن و آلومینیم (در مقادیر کمتر از 5/0 درصد) می توانند در ساختار این فرو آلیاژ حضور داشته باشند.
کاربرد گستردۀ فروسیلیس برای اکسیژن زدایی در فولادها و گرافیت زایی چدن های گرافیتی و البته تولید فولادهای زنگ نزن و نسوز باعث شده که این محصول به یکی از پر مصرف ترین فرو آلیاژها در سطح ایران و جهان تبدیل شود.
فرومنگنز
فرومنگنز آلیاژی فلزی است که از دو عنصر اصلی آهن و منگنز و درصدهای اندکی از عناصری مانند کربن، فسفر و گوگرد تشکیل می شود. فرومنگنز برای افزایش مقاومت، افزایش سختی و کاهش شکنندگی و بهبود رفتار حرارتی در فولادها استفاده می شود.
کاربرد دیگر فروآلیاژهای منگنز، جداسازی گوگرد و اکسیژن زائد در کوره های فولاد سازی است، چرا که غلظت زیاد گوگرد در فولاد، یکنواختی آن را کم می کند و باعث افزایش استعداد شکست در آن می شود. از این رو منگنز با گوگرد ترکیب شده و سولفید منگنز موجود در سرباره را تشکیل می دهد.
گفتنی است منگنز بیشترین کاربرد را در تولید فولاد (فولادهای کربن دار، آلیاژ کم مقاومت، ضد زنگ ابزارآلات) و آلیاژهای غیرفولادی (آلیاژهای غیرآهنی، فروآلیاژها و چدن) دارد. فولادهای کربن دار، بخش اصلی بازار منگنز را به خود اختصاص می دهند.
فروسیلیکومنگنز
همان طور که از نام این فرو آلیاژ پیداست، مهم ترین عناصری که در ساختار آن وجود دارد آهن، سیلیسیم و منگنز است. البته نسبت های کمتری از عناصر فرعی دیگر مانند کربن، فسفر و گوگرد نیز در آن موجود است.
آلیاژ سیلیکو منگنز در مشخصات و سایزهای گوناگونی تولید می شود و به صورت عمده در تولید فولاد به عنوان منبع تامین همزمان منگنز و سیلیس مصرف می شود. امروزه بعضی آلیاژهای سیلیکومنگنز به عنوان عامل آلیاژی در تولید قطعات ریخته گری از جنس چدن نیز استفاده می شوند.
فروکروم
اگر در حوزۀ تولید فولاد های زنگ نزن فعال باشید، حتما نام فروکروم را شنیده اید. این فروآلیاژ متشکل از آهن و کروم است که نسبت ترکیب این دو عنصر، متغیر است. اما معمولا نسبت کروم ترکیب شده در بازۀ 50 تا 70 درصد قرار می گیرد.
استفاده از عنصر کروم منجر به ایجاد خواصی مانند مقاومت به اکسیداسیون و خوردگی، بهبود مقاومت به سایش و جلوگیری از افت استحکام در دماهای بالا در قطعات فولادی می شود. فروکروم نیز یکی از پرطرفدارترین فرو آلیاژهای صنعتی است.
فرومولیبدن
فرومولیبدن آلیاژی با ترکیب شیمیایی شامل آهن و مولیبدن است. فرومولیبدن یکی از مهم ترین عوامل سخت کنندگی فولاد است و به بسیاری از فولادهای آلیاژی که عملیات حرارتی پذیر باشند اضافه می شود.
به علاوه، عنصر مولیبدن باعث ایجاد خاصیت ضد خوردگی در فولادهای زنگ نزن می شود. این عنصر وقتی با آهن ترکیب می شود، باعث تقویت و افزایش سختی فاز آستینت می گردد. اگر چه مانند دیگر فروآلیاژها، تعداد فراوانی از طبقه بندی های ترکیبی برای فرومولیبدن وجود دارد، اما معمولا آن را فقط در دو کلاس که حاوی مولیبدن خالص بین 60 و 75 درصد است، طبقه بندی می کنند.
فروتیتانیوم
فروتیتانیوم نوعی فرو آلیاژ است که در ساختار خود حداقل 30 درصد تیتانیوم داشته باشد. معمولا محصولات فروتیتانیم به صورت کلوخه هایی بزرگ (عمدتا 25 کیلوگرمی) عرضه می شود که بعد از خردایش به ابعاد کوچکتر تبدیل می شوند. کاربرد اصلی فروتیتانیم در ساخت الکترودهای جوشکاری و تولید فولادهای ساختمانی سنگین است. همچنین تیتانیوم سبب کاهش اکسیداسیون می شود و در مواردی برای جداسازی فولادها و آلیاژهای درجه بالا نیز به کار می رود.
فرونیوبیوم
این آلیاژ از ترکیب آهن و عنصر نیوبیوم تولید می شود و حدود 60 الی 70 درصد آن را نیوبیوم تشکیل می دهد. کاربرد اصلی این آلیاژ، در تولید فولاد کم آلیاژ استحکام بالا (فولاد HSLA) است. علاوه بر این کاربرد، از آن برای تولید فولاد ضد زنگ، لوله های نفت و گاز، بدنۀ اتوموبیل ها، انواع ابزارها و لنگر کشتی نیز استفاده می شود.
فروتنگستن
عنصر تنگستن به فریت زایی و کاربیدزایی در فولاد زبانزد است. این عنصر سختی پذيری را افزايش داده و كاربيدهای مقاوم در برابر سايش ايجاد می کند. تنگستن از کاهش سختی در درجه حرارت های بالا كه اتفاقی متداول در نوک ابزار است جلوگيری می كند.
مقادیر کمی از تنگستن سختی پذیری آستنیت را به شدت افزایش می دهد و با تشکیل محلول جامد، فاز فریت را تا حد متوسطی افزایش می دهد. همان طور که حتما تاکنون حدس زده اید، کاربرد اصلی فروتنگستن در توليد فولادهای ابزار و فولادهای پرآلياژی مقاوم در برابر حرارت است.
فرونیکل
این فروآلیاژ در صنعت تولید فولادهای ویژه و ضد زنگ و به عنوان مادۀ اصلی برای مقاومت در برابر گرما در ریخته گری استفاده می شود. سال هاست که فرونیکل به عنوان یک مادۀ خام در فولاد ضد زنگ به کار می رود و برای ایجاد درخشندگی در این فولادها و همچنین ایجاد مقاومت در برابر اسید و حرارت در ظروف خانگی و مصالح ساختمانی و شیمی استفاده می شود.
فروسریم
فروسریم یک آلیاژ ترکیبی است که به تولید جرقه هایی بسیار داغ تا دمای 3000 درجۀ سلسیوس معروف است. قطعات ساخته شده با این آلیاژ سریعا با اعمال ضربه اکسید می شود. در نتیجه تکه هایی از قطعه تجزیه شده و با اکسیژن هوا ترکیب می شود. این ویژگی باعث شده تا فروسریم کاربردهای تجاری زیادی داشته باشد. کاربردهایی مانند منبع اشتعال فندک، سیم جوش های جوشکاری و دی اکسید کننده ها.
فروفسفر
این فروآلیاژ معمولا در قالب محصولاتی با حدود 22 الی 25 درصد فسفر در فولاد و چدن سازی استفاده می شود. هرچند فسفر عنصری مضر در فولادهاست، اما افزودن آن سبب کوچک شدن اندازۀ دانه ها، افزایش حد تسلیم و استحکام کششی نهائی می شود. این تغییر خواص، با افزایش میزان سختی درون دانه ای و تغییرات محدود در میزان ازدیاد طول نسبی حاصل می شود.
از مهم ترین مصارف فروفسفر مصارف نظامی است که برای تولید دود به کار گرفته می شود. همچنین در صنایع ریخته گری برای تولید بوش های ظریف، لوله های چدنی، کفشک ترمز، پودرهای جوشکاری و… استفاده می شود. در مواردی نیز دیده شده است که در تولید برخی فولادهای خاص برای خوش تراش تر شدن، فسفر اضافه می شود.
فروآلیاژ در چه مواردی کاربرد دارد؟
همان طور که گفتیم، این آلیاژها خواص منحصر به فردی را در فولاد و چدن ایجاد می کنند. علاوه بر این، وظایف مهمی را در طول فرآیند تولید به عهده دارند. تا اینجا کاربردهایی که هرکدام از فرو آلیاژها دارند را مختصرا بررسی کردیم. در ادامه نیز مهم ترین استفاده های این مواد را بررسی می کنیم.
اکسیژن گیری یا اکسیژن زدایی
از فرو آلیاژها در تولید فولاد به عنوان زدایندۀ اکسیژن استفاده می شود. می دانیم که عمل فولادسازی چیزی نیست جز اکسیداسیونی که در اثر آن آهن خام به فولاد تبدیل می شود. در این مرحله بعضی از ناخالصی های مزاحم در آهن مانند کربن، گوگرد و فسفر به وسیلۀ اکسیژن و یا اکسیدهای آهن به اکسید مربوطۀ خود (یعنی سرباره) تبدیل می شوند.
بنابراین مقدار معینی از اکسیژنِ دست نخورده در آهن مذاب باقی می ماند. این اکسیژن باقی مانده در فولاد، حین انجماد قطعۀ نهایی، حفره های کوچکی در آن به وجود می آورد که با ایجاد تمرکز تنش، اثرات بدی بر خواص مکانیکی می گذارد.
بنابراین عمل اکسیژن زدایی باید قبل از پایان فرآیند فولادسازی انجام شود. بهترین روش اکسیژن زدایی اضافه کردن عناصری مانند کروم، آلومینیوم، سیلیسیم و منگنز است. این عناصر در مقایسه با آهن، میل ترکیبی بیشتری با اکسیژن دارند. بدین ترتیب باید از فرو آلیاژ هایی نظیر فرومنگنز، فروکروم، فروسیلیس، سیلیسیم-کلسیم و سیلیسیم-آلومینیوم استفاده کرد.
آلیاژسازی
گفتیم که در صورت اضافه شدن فرو آلیاژها به آهن مذاب، ترکیب شیمیایی فولاد تغییر کرده و فولادی با خواصی متفاوت تهیه خواهد شد. به فرو آلیاژی که در چنین فرایندی مصرف می شود آلیاژساز گفته می شود.
فروکروم، فرومنگنز باکربن متوسط یا کم و فرو وانادیم از مهم ترین آلیاژسازهای صنعتی به شمار می روند. اگر این مواد به فولاد مذاب اضافه شوند، عناصر تشکیل دهندۀ آن ها سبب بهبودی خواص فیزیکی، مکانیکی و حرارتی قطعۀ نهایی می شود.
برای مثال عنصر کروم علاوه بر بهبود کیفیت ساختاری، فاز آهن آلفا با شبکۀ کریستالی مکعب مرکز دار (BCC) یا همان فریت را پایدار تر می کند. با این تاثیر، استحکام فولاد و همچنین مقاومت آن را در مقابل خوردگی را افزایش می دهد.
مثال بعدی منگنز است. با اضافه شدن این عنصر به فولاد، فاز گاما (یا آستنیت) که دارای شبکۀ بلوری مکعب با صفحات مرکزدار (FCC) است، از ثبات بیشتری برخوردار می شود. به طور کلی فروآلیاژ های آلیاژساز، با ایجاد تغییر در خطوط تغییرات فازی فولاد، خواص آن را تغییر می دهند.
تلقیح (جوانه زایی) در ریخته گری
می توان از فروآلیاژها برای ایجاد دگرگونی در شرایط انجماد آهن مذاب استفاده کرد. اگر به آهن مذاب قبل از ریخته گری بعضی از عناصر اضافه شوند، مانند هستۀ اولیۀ بلوری عمل می کنند، یعنی سبب می شوند مرکز به آسانی شکل بگیرد و دانه های کریستالی در سرتاسر جرم آهن مذاب به صورت یکنواخت پراکنده شوند.
در نتیجۀ این فرایند، سختی شمش های به دست آمده پس از انجماد به مراتب افزایش یافته و شکنندگی آن نیز کم می شود. برای مثال آلیاژهایی مانند فروسیلیس و فرو منگنز اگر به آهن اضافه شوند، تغییرات مطلوبی را در بافت آن ایجاد می کنند.
یکی از این تغییرات این است که کربنی که در آهن ریخته گری معمولی به شکل لایه لایه پراکنده می شود و نظم مشخصی ندارد، با استفاده از جوانه زا، در سرتاسر ساختار به شکل تقریبا یکنواختی پراکنده می شود. به این دلیل است که آهن تلقیحی از استحکام بالایی برخوردار است.
کاربردهای دیگر
برخی از فرو آلیاژها مانند فروسیلیس، فرو کروم، سیلیکومنگنز به عنوان احیاکننده استفاده می شوند. بعضی از فرو آلیاژها را می توان درصنایع ذوب فلزات غیر آهنی مانند صنایع مکانیکی مورد استفاده قرار داد. برای مثال فرومنگنز با میزان متوسط یا کم کربن، در تولید مفتول های جوشکاری استفاده می شود.
دیدگاه کاربران
سلام خسته نباشید اگه امکانش هست این مقاله راجب به فروآلیاژ هارو واسم ایمیل کنید قابل دانلود نیست