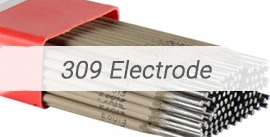
ریخته گری پیوسته ؛ صنعتی ترین روش ریخته گری جهان!
در سال های گذشته، ریختهگری تک باری مهم ترین روش ساخت قطعات فلزی بوده است. مطمئنا این روش خالی از اشکال نبود و برای قطعات بزرگ و حجیم عملکرد خوبی نداشت. چرا که قطعات تولید شده انواع مشکلات ساختاری و متالورژیکی را به همراه داشتند.
به هرحال برای سال های متمادی این روش حرف اول را می زد تا اینکه در سال 1857 ایده و طرح اولیه ریخته گری پیوسته در ذهن هنری بسمر «Henry Bessemer» جرقه زد. اما از آن زمان تا توسعه صنعتی این روش بیش از صد سال طول کشید طوری که کاربردهای صنعتی این روش بیشتر از 50 سال نیست!
در حال حاضر بهترین روشی که برای ریخته گری قطعات بزرگ و حجیم در حال حاضر به کار برده میشود، ریختهگری پیوسته یا مداوم است. امروزه این روش بهترین شیوه برای ساخت شمش های فلزی از جمله آلومینیوم، برنج، مس، چدن و انواع فولاد است.
ریخته گری پیوسته چیست؟
ریخته گری پیوسته (Continuous Casting) یعنی شکل دهی پیوسته و مستقیم فلز مذاب به مقاطع فلزی نیمه نهایی مانند شمش، بیلت و اسلب. در این فرایند تمام مسیر ریخته گری در یک خط تولید خلاصه شده است. یعنی در یک دستگاه مخصوص، فرآیند ریختهگری تا سرد شدن نهایی قطعات به صورت پیوسته انجام می گیرد. و هیچ نیازی به توقف دستگاه یا خارج کردن قطعات و انتقال آن ها به مرحله بعدی نیست.
مراحل ریخته گری پیوسته
1) جمع آوری مذاب در مخزن دستگاه
در ابتدا فلز مذاب به درون کوره ای ریخته می شود. همین ابتدا لازم است عملیاتی نظیر کنترل ترکیب آلیاژی، گاز زدایی و رساندن مذاب به دمای مطلوب انجام گیرد. سپس فلز مذاب به مخزن (منابع تغذیه) که اولین بخش ریختهگری پیوسته هستند، انتقال می یابد. دقت داشته باشید که همواره یک منبع تغذیه آماده برای جایگزین کردن با منبع تغذیۀ ابتدایی لازم است.
2) انتقال مذاب به تاندیش
در مرحله بعد این مذاب با یک لولۀ دیرگداز، به مخزن ثابتی به نام «تاندیش» ریخته می شود. وظیفۀ مهم تاندیش، تامین مذاب لازم برای عملکرد پیوستۀ دستگاه ریخته گری مداوم همزمان با تعویض منبع تغذیه است. البته تنظیم مقدار مذاب، پایین آوردن دمای فلز مذاب و در نتیجه کاهش سیالیت آن نیز به عهدۀ تاندیش است.
نازل تاندیش چیست؟ نکات مهم هنگام خرید و استفاده
نازل تاندیش قطعه ای دیرگداز است که به منظور هدایت مذاب از تاندیش به قالب ریخته گ...3) سرمایش اولیه
در ادامه فلز مذابی که در تاندیش است، با لوله هایی به قالب های مسی انتقال می یابد. این قالب وظیفه شکل دهی و سرمایش اولیۀ فلز را در ریخته گری به عهده دارد. برای سرمایش، انواع روش های خنک کنندگی را می توان اجرا کرد. ساده ترین استراتژی، استفاده از آب سرد است. نوسان هایی که این قالب در این مرحله انجام می دهد، باعث می شود فلزی بر روی سطح درونی قالب باقی نماند. این قالب باید مقاومت به خوردگی بالا و قابلیت انتقال حرارت خوبی داشته باشد.
4) شکل گیری لایۀ استرند
در طول سرمایش قالب، یک لایۀ نازک فلزی در مجاورت قالب منجمد می شود. این لایه را استرند (Strand) می نامند. درون لایه های استرند، هنوز فلز مذاب وجود دارد. از این رو استرندها به وسیلۀ فضای بستۀ ریل های خنک کننده حمایت می شوند تا به واسطۀ فشار مذاب، تغییر شکل ندهند یا دچار شکست نشوند. در این مرحله از ریخته گری مداوم ، لایۀ استرند با حجم زیاد آب خنک می شود تا انجماد مذاب درون آن با سرعت بیشتری اتفاق بیفتد.
5) سرمایش ثانویه
در این مرحله، شمش گداخته وارد ناحیه خنک کننده ثانویه که در زیر قالب قرار دارد، می شود. در این ناحیه شمش توسط آب به صورتی خنک می شود که فرایند انجماد تا هسته شمش پیش روی کند و پس از خارج شدن از این ناحیه به طور کامل جامد شده باشد.
در بخش سرمایش ثانویه آب به وسیلۀ نازل هایی با فشار نزدیک به 0.2 تا 0.3 مگاپاسکال به صورت پودر به همه سطوح شمش پاشیده می شود و آن را به صورت یکنواخت خنک می کند. مصرف آب در این ناحیه، معمولا نزدیک به 0.5 تا 0.8 متر مکعب به ازای هر تن فولاد است.
6) شکل گیری نهایی
مذاب با عبور از یک قالب مسی آبگرد، برای اولین بار شکل مقطع مورد نظر را به خود می گیرد. در ادامه خط ریخته گری مداوم ، غلتک هایی تعبیه شده اند که ابعاد مقطع را کنترل می کنند و سبب افقی شدن حرکت مقطع می شوند. همزمان با کاهش دما در خط تولید و انجماد مذاب، مقطع نهایی تولید می شود.
فرایندهای پس از تولید
با توجه به کاربرد کارفرما، فرایند های دیگری نیز می توان روی مقاطع تولیدی ایجاد کرد. برای مثال، لایه های اکسیدی ایجاد شده در سطح مقطع، به کمک فشار آب جدا می شوند. همچنین مقاطع اسلب (تختال)، بیلت و بلوم در طول های مشخصی به کمک هوا برش، بریده می شوند.
از آن جا که شمش ها معمولا محصول نیمه تمام هستند، همواره پس از ریخته گری تحت فرایندهای مختلف مکانیکی نورد، پتک کاری، مفتول کشی و … قرار می گیرند. در بسیاری از واحدهای تولیدی دیده می شود که شمش قبل از سرد شدن کامل، به بخش نورد که در ادامۀ واحد ریخته گری پیوسته قرار دارد منتقل شده و تمام و یا قسمتی از تغییر شکل بر روی آن انجام می شود.
انواع روش های ریخته گری مداوم
- ریخته گری پیوسته عمودی با ناحیه انجماد ثانویه عمودی و برش شمش در وضعیت عمودی
- ریخته گری پیوسته عمودی با ناحیه انجماد ثانویه عمودی، خمش شمش به جایگاه افقی و برش آن در وضعیت افقی
- ریخته گری پیوسته خمیده با ناحیه انجماد ثانویه خمیده با شعاع خمیدگی ثابت و یا متغیر و برش شمش در وضعیت افقی
اما این روش چه وجه تمایزی با دیگر روش های ریخته گری دارد؟
مکانیزم سرمایش
مهم ترین وجه تمایز روش های مداوم ریزی با روش های تکبار، سرمایش سریع و گاه بدون واسطه شمش یا محصول است. عمدۀ مختصات متالوژیکی قطعۀ نهایی از این مکانیزم ناشی می شود. همین مکانیزم سرمایش منحصر به فرد، سبب تولید قطعات ریز دانه تر و همگن تر می شود. استفاده مستقیم از آب جاری، آبفشان آب اتمیزه (پودر شده)، مخلوط آب و روغن بهترین روش های سرمایش را در ریخته گری پیوسته هستند.
برای خنک کردن شمش، معمولا 5 تا 20 متر مکعب آب، با فشار 0.6 مگاپاسکال، به ازای هر تن فولاد لازم است تا انجماد با شرایط مناسب درون قالب انجام پذیرد.
مکانیزم حرکت
بیرون کشی مداوم مقاطع تولیدی از قالب، طرح ها و روش های گوناگونی را پدید می آورد. در انواع طرح های موجود و ماشین های مورد استفاده می توان به دو روش اساسی اشاره کرد که بر مبنای قالب ثابت و قالب متحرک طراحی شده اند.
- در قالب ثابت خارج کردن شمشال یا تختال، با استفاده از سیستم های هیدرولیکی، غلتکی و چرخ دنده انجام می گیرد.
- در قالب متحرک قالب و شمش حرکت نسبی دارند. این حرکت سبب می شود که مقطع تولیدی در مراحل اولیه همراه با قالب و پس از زمان معین که به چرخه (سیکل) مربوط است، به وسیله مکانیزم های دیگری بیرون کشیده شود .
مکانیزم جدا کردن و انتقال
در ریخته گری پیوسته با توجه به ابعاد قطعه و یا زمان انجماد کامل آن، به یک فضای اضافی برای حرکت محصول نیاز است. اگر حرکت مستقیم عمودی یا افقی باعث گسترش فضای طولی یا عمقی شود، ممکن است تغییراتی نیز در جهت حرکت ایجاد شود.
بعد از آن که طول شمش تعیین شد، برش و جدا کردن شمش با ابزار مختلف برشی انجام گرفته و محصول به قسمت های دیگر انتقال می یابد. در تسمه ریزی و ورق ریزی، برش قطعه با طولی معین لزومی ندارد. معمولا صفحات را «قرقره» می کنند و برش و تعیین اندازه های مناسب در فرایند نورد انجام می گیرد.
انواع قالب های ریخته گری پیوسته
قالب در ماشین ریخته گری پیوسته برای شکل دهی به مذاب فلز استفاده می شود. مواد مذاب بعد از عبور از درون قالب، با شکل های مختلف از آن خارج می شوند. امروزه معمولاً برای همگن شدن مواد درون قالب و همچنین خروج بهتر قطعات، از دستگاه لرزاننده (Oscillator) استفاده می شود.
قالب ریخته گری مداوم باید به اندازۀ کافی در برابر سایش مقاوم باشد. همچنین باید خاصیت انتقال حرارت مطلوبی نیز داشته باشد. با توجه به این دو ویژگی، جنس قالب ریخته گری مداوم را از مس یا گرافیت انتخاب می کنند.
قالب های مسی
سطح مس مورد استفاده در قالب ریخته گری پیوسته را با استفاده از کروم آبکاری و سخت می کنند. ضخامت تقریبی این پوشش ۰٫۱۵ میلیمتر است. این قالب ها متشکل از صفحات مسی و بدنۀ فلزی (نگه دارندۀ صفحات) هستند که در بین این صفحات مسی و بدنه فلزی، آب جریان دارد.
قالب های گرافیتی
گرافیت به علت خواص منحصر به فرد خود مانند عدم چسبندگی به فلز مذاب، دمای ذوب بالا و عدم اختلاط شیمیایی با ترکیبات مذاب به گزینۀ مناسبی برای ساخت قالب های ریخته گری مداوم تبدیل شده است. امروزه فلزاتی مانند چدن خاکستری، چدن سفید، آلیاژهای آلومینیم و آلیاژهای طلا و نقره، اغلب در قالب های گرافیتی تولید می شوند.
کنترل فرایند ریخته گری مداوم به چه صورتی انجام می شود؟
در بسیاری از مراکز تولیدی، عملیات ریخته گری پیوسته به صورت کامپیوتری کنترل می شود. برای این منظور، چندین سنسور الکترومغناطیسی، حرارتی یا تشعشعاتی در دهانۀ لوله، تاندیش و قالب تعبیه می شوند تا میزان فلز، دمای مذاب یا میزان سیالیت آن را اندازه گیری و گزارش کنند.
کنترل انتقال فلز به قالب
حرکت فلز به درون قالب می تواند از سه روش زیر کنترل شود:
- با استفاده از میله های نگه دارنده که به داخل تاندیش میروند.
- توسط دیواره های کناری در ابتدای لولهٔ منتهی به قالب
- اگر فلز به صورت باز ریخته شود، میزان آن به وسیلۀ نازل های قابل سنجش تنظیم می شود.
کاربردهای سیستم PLC
سیستم PLC یا کنترل قابل برنامه نویسی، قابلیت تنظیم نوسان قالب، مقدار پودر وارده شده به قالب و همچنین میزان آب اسپری های خنک کننده را دارد. در انتهای فرایند نیز این سیستم با تغییر دلخواه سرعت ریل های بارگیری، میزان استاندارد بارگیری را تنظیم می کند.
محاسبات دینامیک سیالات
امروزه محاسبات تکنیکی دینامیک سیالات به طور گسترده ای در طراحی عملیات ریختهگری پیوسته کاربرد دارند. این محاسبات به خصوص در تاندیش برای حصول اطمینان از عدم رخ دادن تلاطم در فلز مذاب به کار می روند. همچنین برای اطمینان از این که تمام فلز قبل از خنک شدن بیش از حد وارد قالب شوند، از محاسبات طراحی دینامیک سیالات می توان استفاده کرد. مشخص است که تغییراتی هر چند اندک در حالات حرکت فلز مذاب به داخل تاندیش و قالب می تواند باعث ایجاد تفاوت در تلرانس محصولات تولیدی شود.
در روش پیوسته چه مشکلاتی ممکن است به وجود بیاید؟
در روش ریخته گری پیوسته چالش هایی وجود دارد که اگر به درستی کنترل و مهندسی نشوند؛ ممکن است فرایند ریخته گری را با مشکل مواجه کنند و یا قطعه نهایی خواص مناسبی نداشته باشد. حضور انواع آخال ها و اکسیدها در قطعه حداقل مشکلاتی است که در صورت عدم رعایت ایمنی و مهندسی، ممکن است ایجاد شوند. از این رو حضور یک مهندس و کارشناس کنترل کیفیت در تمامی مراحل ریخته گری ضروری است. در این قسمت به مهم ترین مشکلاتی که ممکن است در این فرایند به وجود بیایند، اشاره می کنیم.
آلودگی اکسیژنی
همان طور که می دانید، فرایند اکسیداسیون در دمای ذوب فلز به سرعت اتفاق می افتد. همچنین در این دما امکان ورود گازها، ذرات خاکستر یا آخال های نامحلول وجود دارند. برای جلوگیری از اکسید شدن فلز در این روش، تا حد امکان از اتمسفر ایزوله استفاده می شود. هوشمندانه ترین راه رسیدن به این شرایط، محافظت سطح فلز مذاب با تشکیل سرباره یا پوشاندن اجزای دستگاه است. این اجزا را می توان به وسیلهٔ لولهها یا سرپوش های مختلف محافظت کرد.
لازم به ذکر است هنگامی که تاندیش و قالب برای اولین بار در دور ریختهگری پر می شوند، به طور نامطلوبی با اکسیژن ترکیب می شوند و آلودگی بسیاری توسط اکسیژن روی قطعه ایجاد می شود. معمولاً قطعات تولید شده اولیه به مشتریانی که خواستار کیفیت بالا نیستند، عرضه می شود.
گریز مذاب
از بزرگترین مشکلات موجود در ریختهگری پیوسته، خروج فلز مذاب از دستگاه است که می تواند بسیار هزینه بر باشد. این مشکل معمولاً به دلیل نازک بودن دیوارۀ دستگاه و عدم توانایی تحمل مذاب اتفاق می افتد. وجود ایراد در سیستم خنک کننده دستگاه نیز می تواند علتی دیگر بر ایجاد این فاجعه باشد.
زمانی که مذاب با سرعت معقولی ریزش کند، زمان برای انجماد لایه ای از مذاب بر روی دیواره وجود خواهد داشت که با ادامه فرایند این لایه ضخیم تر شده و از دیواره دستگاه محافظت می کند. اما در صورتی که سرعت بارریزی بالا باشد، فرصتی برای تشکیل این دیواره وجود نخواهد داشت و امکان شکسته شدن دیواره لوله های بار ریزی و بیرون ریختن مذاب وجود دارد. در این شرایط دستگاه باید سریعا خاموش شود و باقی مانده مذاب از درون لوله ها خارج شود. در برخی موارد حتی ممکن است نیاز به تعویض دستگاه باشد.
تلرانس ابعادی نامناسب در قطعه نهایی
تلاطم بیش از حد مذاب درون قالب ریخته گری پیوسته ، سبب شکل گرفتن قطعه به صورت بی قاعده و غیر نرمال می شود. همچنین ممکن است ذرات خاکستر و ناخالصی در دیواره ها به دام افتاده و در نهایت مقاومت قسمتی از دیواره را کاهش دهند.
یک مشکل معمول دیگر نیز چسبیدن دیواره به قالب و کنده شدن قسمتی از آن است. در قالب های مدرن و با سیستم های کنترل کامپیوتری این مشکل تا حدود زیادی رفع شده و فرایند جداسازی از قالب به آهستگی انجام می شود تا تغییرات دمایی در دیواره ها بهطور تنظیم شده رخ دهد.
ترک خوردگی قطعه نهایی
یکی دیگر از مشکلات گزارش شده برای ریختهگری مداوم ، مشاهدۀ ترک هایی در قطعۀ نهایی است. علت این ترک ها نیز عدم به کار بردن نسبت های مناسب از ترکیبات مختلف است. کارشناسان متالورژی معتقدند با به کار بردن نسبت های دقیق و استاندارد از فلزات مختلف در ایجاد آلیاژها می توان از بروز ترک در قطعات جلوگیری کرد.
جوشش کربن
طبق پژوهش های مختلف، اکسیژن حل نشده در فولاد با کربن درون آن واکنش می دهد و حباب های کربن مونوکسید (CO) را تشکیل می دهد. به این واکنش، جوشش کربن گفته می شود. همانطور که از کلمۀ جوشش پیداست، این واکنش بسیار سریع و با شدت زیاد ریو می دهد و حجم زیادی گاز داغ تولید می کند.
اگر فرایند ریخته گری پیوسته در فضای محدود و بسته در حال انجام باشد، جوشش کربن بسیار خطرناک است. برای جلوگیری از این اتفاق، سیلیکون یا آلومینیوم به فولاد اضافه می شود که اکسیژن موجود در آن را از بین می برد.
چرا که اکسیژن با سیلیکون و آلومینیوم واکنش می دهد و سیلیکا و آلومینیا را تشکیل می دهد. البته، استفادۀ بیش از حد از آلومینیوم، باعث خفگی در نازل های ریخته گری مداوم شده و عملیات را متوقف می کند.
جمع بندی
ریخته گری پیوسته روشی بهینه و سریع برای ریخته گری انواع فلزات است. انعطاف پذیری و قابلیت کنترل و مکانیزه شدنی که این روش دارد، آن را به قابل اعتمادترین روش تولید فولاد خام در جهان تبدیل کرده است. شناخت عیوب و مشکلاتی که ممکن است برای قطعات تولیدی از این روش اتفاق بیفتد، به تولید قطعاتی با کیفیت تر منجر خواهد شد.
دانلود فقط با IP ایران امکانپذیر است. در صورت عدم مشاهده باکس قرمز رنگ دانلود، VPN خود را خاموش نموده و صفحه را رفرش کنید.
پسورد فایل فشرده : www.iran-mavad.com
دیدگاه کاربران
سلام مهندس دارابی..شما کارخانه فولاد مشیز بردسیر هم کار کرده اید؟؟؟
برای خرید ماشین الات ریخته گری پیوسته آلومینیم داخل کشور تولید کننده این ماشین الات وجود دارد ؟
بله. در ایران هم تولید کنندگان و فروشندگان این دسته از ماشین آلات وجود دارند.
کافی است تا در اینترنت و شبکه های اجتماعی جست و جو کنید.
سلام . ذکر کردید که مخلوط آب و روغن بهترین روش های سرمایش را در ریخته گری پیوسته هستند.چگونه و در کدام مرحله از سرمایش این مخلوط استفاده شود؟
با سلام در بخش نورد
با عرض سلام و وقت بخیر من ذوب و نورد به صورت قدیمی دارم
اگه بخواهم به روز کنم چکار باید بکنم ممنون
سلام
بنده خودم ذوب آهن کار میکنم و از نزدیک با ریخته گری پیوسته آشنایی دارم
مقاله بسیار مفیدی بود متشکرم
درود بر شما
بسیار خرسندیم که این مقاله برای شما مفید واقع شده است.
ممنون بابت مطالب خوب شما امید واریم بتوانیم از نزدیک تمام مراحل تولید شمش ببینیم ….
با تشکر از شما
ویدئوهای زیادی از تولید شمش های فلزات مختلف و شمش ریزی در وبسایت و کانال ایران مواد قرار داده شده است که می توانید آن ها را دریافت کنید.
کانال: https://t.me/iranmavad
سلام و ممنون اما مقاله شما کلی هست امیدوارم با معرفی تجهیزات و شرح وظایف تخصصی به سطح دانش ایرانیان بیفزایید.
با عرض سلام
ممنون از نظرات ارزنده شما
در صورتی که مراجعی در ارتباط با ریخته گری و ریخته گری پیوسته می شناسید برای ما ارسال نمایید و در تکمیل مقالات ما را یاری کنید.