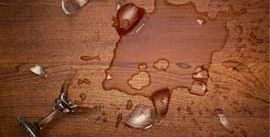
الکترود گرافیتی ؛ هسته مولد کوره قوس الکتریکی
الکترود گرافیتی چیست؟
الکترود گرافیتی از قطعات مهم صنعتی است که جریان برق را با قدرت زیاد و با حداقل مقاومت از خود عبور می دهد. از این رو برای انتقال جریان بالای الکتریسیته در کوره قوس الکتریکی برای ذوب شارژ فلزی استفاده می شود.
الکترود گرافیتی پابه پای هم خانواده های کربنی اش یعنی الماس و ذغال سنگ، توانسته با پیشرفت تکنولوژی و انقلاب صنعتی، توجهات زیادی را به سمت خود جلب کند. این قطعه در تمامی کارخانه هایی که از این نوع کوره ها استفاده می کنند، حضور دارد. این الکترودها مصرفی هستند و پس از استفاده در زمانی مشخصی، نیاز به تعویض دارند.
روش تولید الکترود گرافیتی
بر اساس استاندارد های جهانی، الکترودهای گرافیتی باید از پترولیوم کک کلسینه شده (CPC) تولید شوند. تکنولوژی تولید کک سوزنی (needle coke) به عنوان ماده اولیه اصلی CPC، به شکلی کاملا انحصاری در اختیار کشورهایی مانند چین، آمریکا، ژاپن و آلمان قرار دارد. همین موضوع موجب شده که ساخت الکترودهای گرافیتی به عنوان ماده مصرفی اصلی در کوره های ذوب قوس الکتریکی، در انحصار کشور های توسعه یافته باشد.
برای تولید الکترود گرافیتی ابتدا پودر کک سوزنی، قالب گیری می شود و با ویبراتور فشرده سازی می شود. سپس الکترودی که فرم گرفته، در کوره پخته می شود. پس از پخت یک روکش از قیر به آن اضافه می شود. در آخر نیز دوباره این فرآورده در دمای ۳۰۰۰ درجه سلسیوس قرار گرفته و به گرافیت تبدیل می گردد.
پس از فرایند تولید، عملیات تراشکاری روی الکترودها انجام می شود. این الکترودها بیشتر به شکل استوانه ای تولید می شوند و پس از تولید باید در قطرهای استاندارد برش داده شوند. لازم است حتما یک پین به عنوان سوکت به سر الکترود نصب شود.
مصرف الکترودهای گرافیتی در کوره قوس الکتریکی
متوسط کیلوگرم مصرفی الکترود گرافیتی در واحد هر تن فولاد اندازه گیری می شود. این میزان دارای طیف گسترده ای از کمتر از ۱ تا ۱۰ کیلوگرم به ازای هر تن فولاد است. اگر فرض کنیم برای تولید هر تن فولاد ۱ تا ۲ کیلوگرم الکترود مصرف شود، تقاضای جهانی برای الکترود در مقیاس میلیون تن در سال است!
با توجه به مشکلات اخیری که در تامین الکترود گرافیتی در کشورمان به وجود آمده، تمرکز زیادی روی مکانیزم های مصرف الکترود گرافیتی انجام گرفته و این مسئله، موضوع بسیاری از پژوهش های دانشگاهی بوده است.
مکانیزم های مصرف الکترود گرافیت به دو دسته اصلی پیوسته و ناپیوسته تقسیم می شود. مصارف پیوسته اکثرا به دلیل تصعید ناشی از فرو بردن نوک الکترود و اکسیداسیون دیواره الکترود است. در مصرف ناپیوسته نیز بیشترین میزان مصرف مربوط به شکستگی و افتادن الکترود است. در ادامه هر کدام از این مکانیزم ها را بررسی می کنیم.
تصعید نوک الکترود
این اتفاق معمولا در درجه حرارت های بالای ۳۰۰۰ درجه ساتیگراد رخ می دهد. یعنی وقتی که قوس الکتریکی وجود دارد. چند ثانیه از پایان یافتن قوس، تصعید نیز اتفاق نخواهد افتاد.
در طول فرایند تصعید، گرافیت به شکل مستقیم از حالت جامد به گاز مونوکسیدکربن تبدیل می شود. بدون این که حالت مایع را تجربه کند. پارامترهای مختلفی بر میزان تصعید الکترود گرافیتی تاثیر گذار هستند:
- میزان جریانی که در زمان برقراری قوس از الکترود گرافیتی عبور می کند.
- قطر مقطع نقطه قوس در نوک الکترود
- فاصله زمانی که جریان الکتریکی از الکترود عبور می کند. (Tap To Tap Time)
- مقاومت ویژه الکترود گرافیت
- پایداری قوس
طی گزارشات محققین مختلف، با به کارگیری ولتاژ بالا و جریان پایین (یعنی طولانی کردن عملیات قوس) تلفات تصعیدی الکترود کمتر می شود. همچنین عملیات ذوب نیز بهبود می یابد.
اکسیداسیون الکترود گرافیتی
عوامل زیادی در اکسید شدن دیواره الکترود گرافیتی موثرند. در این میان بیشترین سهم را واکنش اکسیژن موجود در کوره یا اکسیژن تزریق شده به کوره دارد. خوردگی الکترود گرافیتی از بالای سقف کوره با دمای حدود ۵۰۰ درجه سلسیوس آغاز می شود.
هر چه به سمت سقف کوره که دمای ۱۰۰۰ درجه سلسیوس دارد نزدیک شویم، نرخ اکسیداسیون بیشتر می شود. در نقاط نزدیک به زیر سقف کوره، دمای کاری زیاد می شود، بدون این که افزایشی در نرخ خوردگی مشاهده شود.
در ناحیه بالایی سقف کوره (زیر دلتا)، یعنی جایی که در تماس با ذوب نیست، هیچ محافظتی برای جلوگیری از اکسیداسیون الکترود گرافیتی انجام نمی گیرد. در این راستا یک سری محصولات پوششی با نام آلکوپات به بازار ارائه شده اند.
آلکوپات با تشکیل یک لایه محافظ با چسبندگی بالا و ضخامت ۴۰۰ تا ۶۰۰ میکرون روی الکترودهای گرافیتی، از سطح الکترود در برابر اکسیداسیون محافظت می کند. تولید کنندگان این محصول ادعا می کنند وجود نانو ذرات و ترکیبات منحصر به فردی که در آلکوپات است، سبب کاهش 10 تا 15 درصدی ضریب مصرف الکترود در کارخانجات شده است.
مهم ترین عواملی که بر اکسیداسیون الکترود گرافیتی موثرند، عبارتند از:
- چگالی و مقاومت ویژه الکترود گرافیتی
- مدت زمانی که جریان از طریق الکترود عبور می کند. (Tap To Tap Time)
- جریان قوس و دما
- پارامترهای جریان گازهای درون کوره قوس الکتریکی
مصرف ناپیوسته الکترود گرافیتی
این نوع مصارف شامل انواع مختلف شکستگی، افتادن نیپِل (نوک)، شکستن گیره، بدنه و پوسته شدن الکترود است. یکی از متداول ترین دلایل خسارت ناشی از شکستگی یا رها شدن الکترود، شیوه مونتاژ نامناسب الکترود در کوره است. علت مهم بعدی شارژ نامناسب قراضه و آهن اسفنجی است. مشخصا با جلوگیری از دو عامل فوق، می توان تا حدود زیادی از مصرف ناپیوسته الکترودهای گرافیتی جلوگیری کرد.
الکترود گرافیتی، کلیدی و غیر قابل جایگزین!
کالای جایگزینی برای الکترود گرافیتی وجود ندارد. این جمله در عین شفافیت، ممکن است برای صنعتگران کشور ما بسیار غم انگیز باشد. چرا که تولیدکننده الکترود در کشور ما وجود ندارد و مدیران مجبور به واردات آن هستند.
ضریب مصرف الکترودهای گرافیتی به عوامل مختلفی نظیر کیفیت الکترود، فناوری کوره قوس الکتریکی و ظرفیت آن، نوع شارژ (قراضه یا آهن اسفنجی)، دمش اکسیژن و عواملی دیگر بستگی دارد.
امروزه فولادسازان روی روش های کاهش ضریب مصرف الکترود تمرکز کرده اند. همچنین پروژه های دانشگاهی زیادی نیز با موضوع استفاده از راهکارهای کارآمد در مسیر کاهش مصارف الکترود گرافیتی در صنایع متالورژی، تعریف شده است. در ادامه به مهم ترین روش های کاهش مصرف الکترود گرافیتی اشاره می کنیم.
راهکارهایی برای کاهش مصرف الکترود گرافیتی
پوشش دهی الکترود
به طور عمده دو نوع پوشش برای الکترودها در بازار وجود دارد:
- پوشش های فلزی: بهترین مواد برای این نوع پوشش ها آلومینیوم و یا مخلوطی از آلومینیوم و کاربید سیلیسم است.
- پوشش های غیر فلزی: در این موارد سطح خارجی الکترود با موادی مانند نمک های باریم، اسید بوریک، بوراکس و یا ترکیبی از این مواد با مواد دیگر پوشش داده می شود.
در سال های اخیر، الکترودهای پوشش دار زیادی به بازار عرضه شده اند. لازم است بدانید یک پوشش مفید و موفق حتما باید شرایط زیر را دارا باشد:
- حائل پیوسته و کاملی بین گرافیت و اتمسفر کوره ایجاد کند تا مانع اکسیداسیون شود.
- در تماس با سرباره مقاومت خوبی داشته باشد و خورده نشود.
- در برابر الکتریسیته هدایت بالایی داشته باشد تا هدایت الکترود را تضعیف نکند.
- از لحاظ اقتصادی مقرون به صرفه باشد.
خنثی سازی اتمسفر اطراف الکترود
در این روش با به کارگیری گاز خنثی و ایجاد یک لایه محافظ اطراف الکترود، مانع اکسید شدن آن می شویم و مصرف الکترود را کاهش می دهیم. در فرایند خنثی سازی اتمسفر اطراف الکترود، گاز خنثی به صورت جریان مایع به فضای میان الکترودها تزریق می گردد. با ورود به فضای داخل کوره، بلافاصله تبخیر اتفاق می افتد و یک لایه چگال از گاز خنثی اطراف الکترودها به وجود می آید.
گاز خنثی در این روش غالبا نیتروژن یا آرگون است. این گازها با یک نازل به فضای بین سه الکترود گرافیتی انتقال می یابند. نوک نازل معمولا در فاصلۀ 7 تا 24 اینچی از سقف کوره قرار می گیرد. فاصله مناسب نازل از سقف برای یک کوره قوسی با ظرفیت متوسط، 15 اینچ است.
سرمایش الکترود با سیستم آبگرد
در این فرایند با کم کردن دمای بدنه الکترود، واکنش اکسیداسیون جانبی الکترود و مصرف الکترود کاهش می یابد. در سیستم آبگرد، به کمک تراشکاری یک سری کانال در الکترودها تعبیه می شوند. نحوه طراحی این کانال ها به صورتی است که آب اصلا وارد قسمت پایینی الکترود نمی شود و سیستم آبگرد فقط در دو قسمت بالایی جریان پیدا می کند.
سرمایش الکترود با اسپری
در این روش سیستم خنک کنندگی اسپری مایع، به عنوان یک سیستم موثر در کاهش مصرف الکترود ارائه شده است. این سیستم با خنک کردن مستقیم حد فاصل محل اتصال الکترود به سیستم جریان برق تا سقف کوره، سبب سرمایش غیر مستقیم بخش های داخلی الکترود نزدیک به سقف کوره می گردد. از این طریق اکسیداسیون جانبی و مصرف الکترود محدود می شود. در این سیستم، تعدادی لوله انتقال آب، جریان را به نازل های اسپری کننده مایع انتقال می دهند و آب از طریق نازل ها به سطح الکترودها اسپری می شود.
از الکترود گرافیتی در چه مواردی استفاده می شود؟
الکترودهای گرافیتی برای ایجاد قوس الکتریکی در کوره های ذوب فولادسازی استفاده می شوند. این الکترودها ظرفیت مطلوبی برای ایجاد هدایت الکتریکی بالا و توانایی مقاومت در برابر حرارت ایجاد شده را دارا هستند. نوک این الکترودها می تواند تا 3000 درجه سانتیگراد برسد که تقریبا نیمی از دمای سطح خورشید است!
از دیگر کاربردهای الکترودهای گرافیتی می توان به خم کاری، ایجاد شیار یا حذف عیوب در قطعات ریخته گری و جوشکاری شده از طریق قوس الکتریکی اشاره نمود. با ایجاد قوس الکتریکی بین الکترود گرافیتی و سطح قطعه، سطوحی از مذاب روی قطعه ایجاد شده و با هوای فشرده یا نیتروژن، فلز مذاب از روی سطح پاک می شود.
تحلیل بازار جهانی الکترود گرافیتی
تولید الکترود گرافیتی در دنیا حدودا ۱.۲ تن در سال است. سهم کشور چین از این مقدار ۴۰ درصد و سایر کشورها ۶۰ درصد است. قیمت این محصول در سال های اخیر افزایش تقریبا ۱۰ برابری تجربه کرده است!
در همین راستا مدتی پیش یک شرکت آلمانی در اقدامی جالب، طرحی از خودروی گران قیمت مرسدس بنز را منتشر کرده است که در حال فرو رفتن در کوره ذوب است! افزایش قیمت الکترود گرافیت به دو دلیل است:
- اول این که عرضه مواد اولیه تولید الکترود گرافیتی کمتر شده است. برای مثال کک سوزنی که در حدود ۴۰ درصد بهای تمام شده این محصول را تشکیل می دهد، نسبت به سال های قبل کمتر عرضه می شود.
- عامل بعدی که سبب افزایش قیمت الکترود گرافیتی شده است، سیاست های دولت چین است. این کشور به دلایل زیست محیطی و مشکلات آلودگی هوا، در نظر دارد حدود ۲۰ درصد از ظرفیت تولید کل فولاد به روش کوره بلند را کاهش دهد و به سمت استفاده از کوره های قوس گرایش پیدا کند. همین موضوع باعث افزایش میزان مصرف داخلی الکترود گرافیتی در این کشور شده است.
بررسی بازار داخلی الکترود گرافیتی
از بهمن ماه سال ۹۵ که روند افزایشی قیمت الکترود گرافیتی آغاز شد، شرکت های فولادی ایران این موضوع را جدی نگرفتند و اعتنایی به بازارهای جهانی نشد. شاید دلیل وضع نابسامان این محصولات در کشورمان در این برهه زمانی همین موضوع باشد.
در ایران نیاز سالانه کشور به الکترود گرافیتی ۴۰ تا ۵۰ هزار تن است. با استناد به اهداف صنعت فولاد کشور در افق ۱۴۰۴ حدود ۹۰ تا ۱۰۰ هزار تن الکترود گرافیتی موردنیاز است. در حال حاضر اکثر نیاز صنعت فولاد به الکترود گرافیتی از کشورهای روسیه، چین و هند تأمین می گردد.
قیمت الکترود تا پیش از آنکه صعود سریعی داشته باشد، به ازای هر تن حدود ۲۰ تا ۳۰ هزار تومان بود اما بنابر دلایلی که ذکر شد، قیمت آن تغییرات بالایی داشته است و به صورت روزانه تغییر می کند. صنعت فولاد ایران غالبا متکی به کوره های قوس الکتریکی است و این موضوع موجب شده تا کمبود عرضه الکترود های گرافیتی، در ماه های اخیر نگرانی هایی را به وجود بیاورد.
این امر تأثیر بالایی بر قیمت تمام شده محصولات شرکت هایی که از روش قوس الکتریکی استفاده می کنند، داشته است. علاوه بر افزایش نرخ الکترود، با توجه به اینکه این محصول به صورت ارزی خریداری می شود، با افزایش نرخ دلار، بهای تمام شده برای فولاد سازان تحت تأثیر قرارگرفته است.
تا قبل از صعود قیمت الکترود، به علت پایین بودن بهای برق در ایران، روش ذوب با قوس الکتریکی توجیه اقتصادی داشت. اما صعود اخیر بهای الکترود این تصورات را بر هم زد و برگ تازه ای برای این صنعت ورق خورد.
راهنمای خرید الکترود گرافیتی
الکترود های گرافیتی در سه گروه RP، HP و UHP قابل عرضه هستند. نوع RP برای مصارف با مقیاس کم و عادی است. نوع الکترود HP با جریان الکتریکی بالا برای انجام عملیات ریخته گری در کوره پاتیلی و گاهی اوقات برای انجام عملیات در کوره قوس الکتریکی به کار می رود. نوع UHP نیز با جریان بسیار بالا برای کوره های قوس الکتریکی و کوره های پاتیلی تحت بار سنگین به کار می رود.
جداول مشخصات مکانیکی و فیزیکی هر یک از این الکترودها در استاندارد ASTM C1039 – 85 ارائه شده است. در جدول زیر می توانید ظرفیت انتقال جریان الکتریکی را برای هر کدام از دسته ها مشاهده کنید.
مواد اولیه مورد مصرف و روش ساخت، مهم ترین عوامل در تعیین کیفیت الکترون هستند. در هنگام خرید الکترود، خواص و مواردی نظیر وزن مخصوص، تخلل، ضریب انبساط حرارتی، مقاومت الکتریکی، استحکام کششی و خمشی، مدول الاستیسیته و مقاومت در برابر شوک حرارتی با توجه به کاربرد باید در نظر گرفته شود.
الکترودهای گرافیتی با کیفیت از کک سوزنی با کیفیت بالا تولید می شوند. کک سوزنی نوعی کک با پایه نفتی است. هرچه کیفیت کک نفتی در مواد اولیه بالاتر بوده باشد، الکترود کارایی بهتری خواهد داشت.
بخش انتهایی هر الکترود یک پیچ مخروطی شکل است که درون آن یک مغزی (Nipple) پیچ داده می شود. دقت کنید که مغزی باید استحکام مکانیکی خوبی داشته باشد و مقاومت اضافی به وجود نیاورد. دو یا سه تکه از الکترودها توسط مغزی به هم پیچ می شوند و یک ستون الکترود ایجاد می کنند.
انتخاب الکترود گرافیتی منطبق با نوع کاربرد آن و در نظر گرفتن موارد فنی انجام می گیرد. در پایان به برخی از این پارامترهای فنی اشاره می کنیم:
- طراحی کوره
- میزان قراضه تزریق شده در کوره
- ذرات شارژ شده در کوره
- میزان اکسیژن مصرفی
- رینگهای اسپری آب
- سیستم کنترل دود
- زمان عملیاتهای ذوب و پالایش
- توان مصرفی
- سرباره
دیدگاه کاربران
سلام.
الحمدالله در شرکت دانش بنیان پتروفناور بعد از چندسال تحقیق بلاخره کک سوزنی تولید شد البته با حمایتهای معاونت محترم علمی و فن آوری ریاست جمهوری،
از سال ۱۴۰۳ به بعد ایران عزیز پنجمین کشور دارای دانش تولید کک سوزنی می باشد،
با سلام ممنون میشم راهنمایی کنید اسم اون چسبی که پیش از مرحله پخت پودر گرافیت باهاش مخلوط میشه خمیر میشه قالب میزنن رو بگین خیلی برام ضروریه اگه امکانش هست جواب بدین