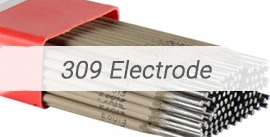
فولاد زنگ نزن آستنیتی ؛ از صفر تا صد!
فولاد زنگ نزن آستنیتی (Austenitic Stainless Steels) مانند دیگر انواع فولاد، آلیاژی از آهن، کربن و دیگر عناصر است که در سری 200 و 300 دسته بندی می شود. به طور کلی 16 تا 30 درصد کروم و 2 تا 20 درصد نیکل برای افزایش کیفیت سطح، شکل پذیری، افزایش مقاومت به خوردگی و مقاومت در برابر سایش به این فولادها اضافه می شود.
فولاد ضد زنگ آستنیتی با عملیات حرارتی قابل سخت شدن نیست. همان طور که گفتیم این فولادها به دلیل قابلیت جوشکاری مطلوب، شکل پذیری عالی و مقاومت در برابر خوردگی، پرطرفدارترین گریدهای ضد زنگ تولید شده در جهان هستند. تمام فولادهای آستنیتی در شرایط آنیل شده، غیر مغناطیسی هستند.
بهترین ورقهای استیل با جوشپذیری بالا – راهنمای کامل انتخاب و خرید
یکی از چالشهای مهم در استفاده از ورقهای استیل، جوشکاری آنهاست که تأثیر مستقیم...لازم به ذکر است که بسته به ترکیب، بعضی از فولادهای آستنیتی هنگام کار در سرما تا حدودی مغناطیسی می شوند. این فولادها به طور گسترده در تجهیزات خودرو، وسایل آشپزی، تجهیزات غذایی و آشامیدنی، ماشین های پردازش و دیگر کاربردهای صنعتی استفاده می شوند.
تاریخچۀ فولادهای زنگ نزن آستنیتی
فولادهای زنگ نزن آستنیتی و سایر فولادهای زنگ نزن بیش از یک قرن سابقه دارند. در اوایل دهۀ 1800، برخی از محققان (Mallet، Faraday ، Stodart و Bunsen) نتیجه گرفتند که آلیاژهای آهن-کروم (مشابه فولادهای کروم دار امروزی) در برابر اکسیداسیون و حملۀ اسیدی مقاوم اند.
در سال 1821 «پیر برتیر» متالورژیست فرانسوی، استفاده از این آلیاژها را برای ساخت کارد و چنگال پیشنهاد داد. زیرا او نیز به مقاومت این مواد در برابر حملۀ اسیدی پی برده بود.
در سال 1913، یک آلیاژ فولادی (اولین فولاد ضد زنگ) حاوی 12.8 درصد کروم توسط «هری برلی» از انگلیس که سعی در تولید فولاد مقاوم در برابر سایش برای لوله های تفنگ داشت، ذوب شد. این متالورژیست به طور تصادفی در پایان گریدی تولید کرد که در برابر حملۀ اسید و زنگ زدگی مقاوم بود.
در واقع هری برلی با افزودن كروم به آهن مذاب، آنچه را كه به آن فولاد زنگ نزن می گفتند، تولید كرد. در سال 1914، چاقوهای از جنس فولاد زنگ نزن به عنوان چاقوهای ضد زنگ به بازار عرضه شدند.
جالب است بدانید سال 1912، مهندسان موسسۀ «کروپ» (Krupp) یعنی «انو اشتراوس» و «ادوارد ماورر» قبلاً این نوع فولاد را با عنوان نیروستا (Nirosta) به صورت یک اختراع ثبت کرده بودند. این اختراع دارای 7 درصد نیکل و 21 درصد کروم بود.
گرید فولاد تولید شده توسط مهندسان Krupp مقاوم در برابر خوردگی اسیدی، داکتیل و شکل پذیر بود. در سال 1919، حق ثبت اختراع فولاد ضد زنگ مارتنزیتی توسط E.Haynes به دست آمد. در همین حال، آلمانی ها گرید آستنیتی محبوب 316 را اختراع کردند. به زودی این گریدهای آستنیتی کاربردهایی در ابزار پزشکی، آشپزخانه، جاروبرقی ها و وسایل نقلیه پیدا کردند.
مجموعه ای از مزایای متالورژیکی …
فولادهای زنگ نزن آستنیتی از نظر متالورژیکی مزایای بسیاری دارند. از یک طرف، می توان آن ها را به اندازۀ کافی -تا استحکام تسلیم حدود 200 مگاپاسکال- نرم و داکتیل ساخت. از طرف دیگر، این قابلیت وجود دارد که آن ها را با کارسرد فوق العاده مستحکم کرد. این استحکام در برخی موارد ممکن است تا 2000 مگاپاسکال (290ksi) نیز برسد.
فولاد زنگ نزن آستنیتی همانطور که از نامش پیداست، یک ساختار آستنیتی FCC دارد که تا دمای صفر مطلق، بسیار چقرمه و قابل انعطاف است. همچنین استحکام خود را در دمای بالا به سرعت آلیاژهای پایه آهن فریتی (با ساختار BCC) از دست نمی دهد.
همانطور که گفتیم، فولاد ضد زنگ آستنیتی حاوی حدود 16 تا 25 درصد کروم است که البته می تواند حاوی نیتروژن محلول نیز باشد. خاصیت ضد زنگ یا Stainless بودن این فولاد، به دلیل حضور این دو عنصر است.
البته هزینه هایی که عنصر نیکل روی دست انسان می گذارد، باعث شده کاربردهای این فولادها کمی محدود شود. (نیکل در فولاد ضد زنگ آستنیتی به تثبیت ساختار آستنیتی کمک می کند.)
✔ مقاومت به خوردگی
حتی گریدهایی از فولاد ضد زنگ آستنیتی با کمترین قابلیت مقاومت به خوردگی، می توانند در برابر حملات خورندۀ طبیعی در محیط های روزمره مقاوم باشند. این در حالی است که مقاوم ترین گریدهای فولاد ضد زنگ آستنیتی، در محیط آب دریای جوشان هم بدون خوردگی به کارشان ادامه می دهند!
البته این آلیاژها برخی ضعف های نسبی دارند که عبارتند از:
- فولادهای زنگ نزن آستنیتی در مقایسه با گریدهای فریتی، مقاومت کمتری در برابر اکسیداسیون چرخه ای دارند. زیرا ضریب انبساط حرارتی بیشتر آن ها باعث می شود تا پوشش اکسید محافظ دچار اضمحلال شود.
- فولاد زنگ نزن آستنیتی در صورت استفاده در محيطی كه در آن مقاومت در برابر خوردگی ناكافی دارد، می تواند دچار ترک خوردگی ناشی از تنش (SCC) شوند. وجود حتی چند قسمت در میلیون ذرات کلرید، می تواند منجر به آسیب ناشی از SCC شود. تنش های پسماند ناشی از ساخت نیز می تواند یکی از عواملی باشد که بر شدت SCC در این فولادها می افزاید.
- حد تحمل خستگی (Fatigue Endurance Limit) در این فولادها فقط حدود 30 درصد استحکام کششی است (که این خاصیت در فولادهای ضد زنگ فریتی 50 تا 60 درصد است). این موضوع، همراه با ضرایب انبساط حرارتی بالا، فولاد ضد زنگ آستنیتی را به خصوص در معرض خستگی گرمایی حساس می کند.
از خستگی در مواد چه می دانید؟
مشاهدات نشان داده اند که فلزات تحت بارگذاری نوسانی، در تنشی کمتر از حد مجاز دچار...با این حال، با اقدامات احتیاطی مناسب می توان از خطرات ناشی این محدودیت ها تا حدود زیادی جلوگیری کرد.
فولاد ضد زنگ آستنیتی یا فریتی؟!
معیار اساسی در انتخاب یک فولاد ضد زنگ، این است که بتواند بدون هیچ گونه خوردگی در محیط عملکردی اش به کار ادامه دهد. گاهی اوقات لازم است که مواد برای عمری مفید اما محدود انتخاب شوند. این امر خصوصاً در مورد سرویس های با درجه حرارت بالا که خزش و اکسیداسیون منجر به عمر محدود برای همۀ مواد می شود، صادق است.
انتخاب در بین فولادهای ضد زنگ قابل استفاده در محیط مشخص، بر اساس آلیاژی است که می توان آن را با کمترین هزینه و با طول عمر مورد نظر تولید کرد. فولادهای زنگ نزن فریتی با همان میزان مقاومت به خوردگی، از قیمت کمتری نیز برخوردار هستند. اما به دلیل ویژگی های زیر، انتخاب مناسبی نخواهند بود:
- این فولادها چقرمگی پایینی دارند. این موضوع به خصوص در دماهای پایین یا ضخامت های بیشتر از 1.5 میلی متر خودش را نشان می دهد.
- عدم شکل پذیری عالی؛ به خصوص اگر بیش از حدود 30 درصد کشیدگی (Elongation) لازم باشد.
- حساسیت به رشد فازهای ترد در دمای بالا، در صورتی که به طور متوسط آلیاژی شده باشد.
وقتی حق انتخاب گسترده تر می شود…
در برخی موارد، گریدهای ارزان قیمت مارتنزیتی به جای آستنیتی استفاده می شوند. این گریدها به جای کارسرد، از طریق عملیات حرارتی به استحکام و سختی بالایی می رسند. البته گریدهای مارتنزیتی وقتی مرجح هستند که خواص مکانیکی، مهم تر از مقاومت در برابر خوردگی باشد.
گریدهای Duplex از نظر مقاومت در برابر خوردگی، با فولاد زنگ نزن آستنیتی مطابقت دارند. همچنین در شرایط آنیل از استحکام بالاتری نیز برخوردار هستند. اما با توجه به فازهای تردی که با قرار گرفتن طولانی مدت در دمای بالا ایجاد می شود، کاربردهای محدودی دارند. البته گریدهای داپلکس مانند آلیاژهای فریتی شکل پذیری متوسطی دارند. در بخش های بعدی با خانوادۀ فولادهای زنگ نزن بیشتر آشنا خواهیم شد.
✔ یک انتخاب هوشمندانه
به دلایل گفته شده در دو بخش قبلی، امروزه در صنایع مختلف معمولا از گریدهای آستنیتی و ضد زنگ استفاده می شود. زیرا در بسیاری از موارد، سطح بسیار خوبی از مقاومت در برابر خوردگی را به همراه خواص مکانیکی عالی ارائه می دهند.
استفادۀ هوشمندانه از فولادهای زنگ نزن آستنیتی می تواند هزینه های قابل توجهی را در مهندسی، طراحی و عملکرد محصول صرفه جویی کند. این فولادها آلیاژهای فلزی کاربرپسند با هزینۀ چرخه عمر کمتر از بسیاری از مواد دیگر هستند.
ترکیبات آلیاژی فولادهای زنگ نزن آستنیتی
آلیاژهای آستنیتی می توانند در هر نقطه از دیاگرام Delong که با برچسب آستنیت مشخص شده است، ترکیباتی داشته باشند. این دیاگرام برای نشان دادن این که کدام فازها در آلیاژهای موجود در حالت جامد وجود دارد، طراحی شده است. از این رو برای محصولات ریخته گری معمولی، ریخته گری مداوم و جوشکاری اعمال می شود.
اگر از دیدگاه قابلیت ریخته گری (Castability) به موضوع نگاه کنیم، ترکیب اکثر آلیاژهای تجاری در امتداد ناحیۀ چندین درصد فریت قرار می گیرد. ویژگی بارز آلیاژهای آستنیتی این است که با افزایش کروم و مولیبدن برای افزایش مقاومت به خوردگی، معمولاً برای حفظ ساختار آستنیتی نیکل یا سایر تثبیت کننده های آستنیت باید به فولاد اضافه شود.
جدول زیر مهم ترین گریدهای فولاد زنگ نزن آستنیتی را به همراه ویژگی های شاخصی که دارند، نمایش می دهد.
بسیاری از گریدهای آلیاژی مانند 308، 309 و 317 نیز وجود دارند که به دلیل پیشرفت در پردازش فولادها، امروزه کمتر استفاده می شوند. حتی امروزه به دلیل پذیرش گستردۀ دکربوریزاسیون آرگون-اکسیژن (Argon Oxygen Decarburization) استفاده از گرید 321 که در جدول فوق ذکر شده، در حال کاهش است.
به همین ترتیب، گرید 302 نیز کم کم جای خود را به گرید 304 با کربن پایین داده است که حتی 304L با کربن پایین تر، می تواند در موارد بسیاری جایگزین آن شود. بسیاری از پژوهش ها نشان داده است که محتوای کربن کم، از حساسیت زایی (Sensitization) در فولاد ضد زنگ آستنیتی جلوگیری می کند.
استیل 304 و 316 چه تفاوتی با هم دارند؟
استیل 304 و 316، دو گرید بسیار پرکاربرد از فولادهای زنگ نزن هستند که به سبب شباه...تفاوت اصلی گریدهای 200 و 300
در فولادهای زنگ نزن آستنیتی، اگر سیستم آلیاژی مبتنی بر نیکل در نظر گرفته شود، حداقل 8 درصد وزنی نیکل (با محتوای 18 درصد کروم) برای تبدیل یک ساختار فریتی (BCC) به یک ساختار آستنیتی (FCC) لازم است. این سیستم های آلیاژی مبتنی بر نیکل، همان سری 300 (به عنوان مثال گرید 304) هستند.
پژوهش ها نشان می دهد که با افزایش میزان نیکل در سری 300، می توان آسیب ناشی از خوردگی SCC را به حداقل رساند. به همین ترتیب، می توان نسبت نیکل به کروم را اصلاح کرد تا شکل پذیری گریدهای آستنیتی بهینه شود.
حال اگر مقدار نیکل کمتر از 8 درصد باشد، در این صورت افزودن نیتروژن می تواند تحول کامل ساختار فریتی به آستنیتی را تضمین کند. گریدهایی که دارای درصد پایین نیکل باشند را سری 200 می نامند که نسبتاً ارزان تر هستند.
البته باید توجه شود که وجود مقادیر زیاد نیتروژن در گریدهای آستنیتی می تواند معایبی را به دلیل تولید رسوبات نیتریدی ایجاد کند. امروزه عناصر دیگری نیز مانند منگنز و مس نیز برای اطمینان از پایداری ساختار FCC به گریدهای آستنیتی اضافه می شوند.
مس : نخستین فلز کشف شده به دست بشر!
اگر تمام سیم های مسی به کار گرفته در یک اتوموبیل معمولی را از آن خارج کنید و به ...نقش عناصر آلیاژی در فولاد ضد زنگ آستنیتی
می دانیم که با افزودن کروم، مقاومت در برابر اکسیداسیون و خوردگی در این فولادها افزایش می یابد. معادل های نیکل (مانند منگنز، نیتروژن، کربن و …) نیز باید به مقدار متناسب اضافه شوند تا پایداری فاز آستنیت بیشتر شود.
اگر مولیبدن -که معادلی برای کروم به شمار می رود- به فولاد اضافه شود، مقاومت در برابر خوردگی حفره ای افزایش می یابد، اما مقاومت در برابر اکسیداسیون تقریبا تغییری نمی کند. معمولا در این مواقع، از نیتروژن هم به عنوان تثبیت کننده آستنیت استفاده می شود، هم برای متعادل ساختن افزایش کروم یا مولیبدن و هم برای افزایش مقاومت در برابر خوردگی.
از عنصر آلیاژی سیلیسیم، می توان به عنوان آلیاژی برای افزایش مقاومت در برابر اکسیداسیون و خوردگی توسط اسیدهای اکسیدکننده استفاده کرد. گریدهایی که حاوی سیلیسیم بالا هستند، در دماهای بالا استحکام مطلوبی دارند. محتوای بالای سیلیسیم و مس، مقاومت فولاد را در برابر حملۀ اسید سولفوریک گرم بهبود می بخشد.
عنصر نیوبیوم مقاومت در برابر خزش را افزایش می دهد. همچنین سبب کاهش استعداد فولاد به خوردگی بین دانه ای می شود. گوگرد و سلنیوم قابلیت ماشینکاری را افزایش می دهند.
ساخت کاهشی (Subtractive Manufacturing) یا ماشین کاری(Machining) چیست؟
ماشین کاری چیست؟ تفاوت آن با ساخت کاهشی چیست؟ زیرتکنولوژیهای این روش ساخت و تول...عملیات حرارتی و سخت کاری
پیش از این گفتیم که گریدهای آستنیتی را نمی توان از طریق عملیات حرارتی سخت کرد. با این حال، سختی و استحکام مکانیکی این مواد می تواند از طریق کارسرد افزایش یابد. از دیگر روش های افزایش سختی، افزودن نیتروژن و فرایند سخت شدن رسوبی (Precipitation Hardening) است. هنگامی که فولادهای ضد زنگ آستنیتی کار سخت می شوند، به سرعت مستحکم می شوند.
امروزه ثابت شده است که با ترکیب فرایند کارسختی با آنیل، می توان قطعات و اجزای فولادی تولید شده را با قابلیت خمش (Bendability) و استحکام مورد نیاز پایان کاری کرد.
اعضای دیگر خانوادۀ فولادهای زنگ نزن
فولادهای زنگ نزن فریتی
این فولادها دارای محتوای استاندارد کروم (11 درصد) و مقدار کمی کربن (زیر 0/1 درصد کربن) هستند. فولاد زنگ نزن فریتی به طور کلی مقاومت کمی در برابر خوردگی دارند. خاصیت مغناطیسی این فولادها را به ساختار BCC با اتم Fe در هر گوشه و اتم Fe در مرکز مکعب نسبت می دهند.
از محدودیت های فولادهای زنگ نزن فریتی می توان به سختی کمتر و استحکام مکانیکی متوسط اشاره کرد. با این وجود، فولادهای فریتی از جمله فولادهای ضد زنگ بسیار مفید و محبوب در صنعت هستند. محتوای کم نیکل در ضدزنگ های فریتی، دلیل ارزان بودن نسبی این فولادها در بازار است.
فولادهای زنگ نزن مارتنزیتی
این فولادها نیز عمدتا حاوی کروم هستند، اما بر خلاف نوع فریتی، حاوی درصد بیشتری کربن (تا 1 درصد) هستند. زنگ نزن های مارتنزیتی قابلیت سخت کاری و تمپر شدن دارند و عموما مغناطیسی هستند.
10 مزیت کلیدی سخت کاری سطحی فولاد (Case Hardening)
عملیات حرارتی یکی از تکنیک های موثری است که پس از تولید فولاد، به جهت دستیابی به...عیب اصلی این فولادها این است که نمی توان آن ها را به راحتی جوش داد و در مقایسه با انواع فریتی و آستنیتی مقاومت کمتری در برابر خوردگی دارند. فولادهای زنگ نزن مارتنزیتی برای کاربردهایی ترجیح داده می شوند که خطر خوردگی بسیار کم بوده و استحکام کششی بالا و ظرفیت تحمل بار ضربه ای (Impact Load Capacity) یک نیاز ضروری باشد.
فولادهای زنگ نزن داپلکس
ریزساختار این فولادها هم آستنیتی (50 درصد) و هم فریتی (50 درصد) است. زنگ نزن های داپلکس به دلیل استحکام بالاتر قادر به تحمل بار در مقیاس هایی بیشتر از انواع آستنیتی یا فریتی هستند و مقاومت ذاتی در برابر ترک خوردگی ناشی از تنش (SCC) و خوردگی اسیدی دارند.
فولاد ضد زنگ داپلکس محدودیت هایی در مشخصات مغناطیسی و قابلیت جوشکاری از خود نشان می دهد. گریدهای داپلکس مواد ترجیحی برای ساخت مخازن بزرگ و ظروف ذخیره و حمل مواد شیمیایی هستند.
فولادهای ضد زنگ سخت شده با رسوب دهی
این فولادها -مانند گریدهای آستنیتی- مقاومت بسیار بالایی در برابر خوردگی دارند. استحکام آن ها نیز می تواند بالاتر از فولاد ضد زنگ مارتنزیتی باشد که به دلیل افزودن نیوبیوم، مس و آلومینیوم تا 0.5 درصد است. ترکیب شیمیایی این فولادها حاوی کروم در حدود 15 تا 17.5 است. این گریدها به دلیل استحکام مکانیکی بالا، مواد ترجیحی برای ساخت شفت های طویل هستند.
از فولاد زنگ نزن آستنیتی برای چه مواردی استفاده می شود؟
ساخت سازه های مغناطیسی
از آنجا که فولادهای زنگ نزن آستنیتی غیر مغناطیسی هستند، می توان از آن ها در ساخت سازه هایی که میدان های مغناطیسی بزرگی تولید می کنند (مانند مراکز پزشکی با اسکنرهای MRI) استفاده کرد.
با این حال، ممکن است چند گرید فولاد ضد زنگ آستنیتی کارسرد شده (به عنوان مثال گرید 302) به دلیل افزایش نفوذ پذیری مغناطیسی (Magnetic Permeability)، خاصیت مغناطیسی ضعیفی پیدا کنند. اما گریدهای آستنیتی با مقدار نیکل زیاد (به عنوان مثال گرید 316) در صورت کارسرد نیز مغناطیسی نمی شوند.
تقویت کنندۀ بتن
گریدهای آستنیتی معمولا به عنوان تقویت کننده برای ساخت بتن های سیمانی در محیط های دریایی بسیار خورنده استفاده می شوند. این فولادها ممکن است به صورت جامد و بالک و یا به عنوان روکش (Cladding) روی هستۀ فولاد کربنی استفاده شوند. البته در چنین کاربردهایی، خطر خوردگی دو فلزی (Bimetallic Corrosion) باید به دقت ارزیابی شود.
سیمان (انواع ، روش های تولید ، نکات خرید)
بدون شک تاکنون با سیمان کار کرده و یا حداقل آن را دیده اید. مادهی چسبنده ای که ...دیگر کاربردهای صنعتی
- فولاد زنگ نزن آستنیتی نیکل دار استاندارد 8/18 (گریدهای 304L و 304) برای تولید اتصالات و چارچوب ها، قطعات ساختاری وسایل نقلیه، تجهیزات معدن، تجهیزات برودتی، اجزای معماری، مخازن ذخیره سازی و سیستم های لوله کشی حاوی مایعات خورنده استفاده می شوند.
- زنگ نزن های آستنیتی کروم-مولیبدن-نیکل با گرید 316 در ماشین آلات درگیر در فرآیندهای شیمیایی، تجهیزات آزمایشگاهی، تجهیزات پردازش منسوجات، تولید دارو، قطعات مبدل حرارتی، وسایل آماده سازی غذا، ابزار جراحی، ایمپلنت های جراحی/پزشکی، تجهیزات آبجوسازی، اتصالات قایق های آب شور و سازه های ساحلی استفاده می شوند.
- گریدهای کم کربن و مقاوم در برابر حرارت 317L در برخی تجهیزات کارخانه های پتروشیمی و شیمیایی و کندانسورهای نیروگاه ها استفاده می شوند.
- گریدهای سیلیکون-کروم-نیکل بالای آستنیتی (309S) در قطعات مبدل کاتالیزوری برای وسایل نقلیه، فرآیندهای شیمیایی و کوره ها استفاده می شوند.
- گریدهای نیکل پایین حاوی منگنز (سری 200) برای ظروف آشپزی، مخازن آب خانگی، اجزای خودرو، تجهیزات تولید مواد غذایی و لوازم خانگی مانند ماشین لباسشویی استفاده می شود.
هر آنچه از ورق استیل 304 باید بدانید
ورق استیل 304 یکی از پرکاربردترین و محبوبترین انواع فولادهای ضدزنگ در صنعت است ...جمع بندی
گریدهای مختلف فولاد فولاد زنگ نزن آستنیتی به طور کلی 18٪ کروم و 8٪ نیکل دارند. با این حال، گریدهای حاوی سطوح بالاتر تا 26٪ کروم و 35٪ نیکل نیز تولید می شوند که از مقاومت در برابر خوردگی و دوام بالاتری برخوردارند.
البته این دوام بالاتر با هزینۀ بالایی حاصل می شود. زیرا نیکل گران است. اما با افزودن منگنز، نیتروژن و مس به آلیاژ، می توان میزان نیکل را کاهش داد. افزودن مولیبدن به این فولادها به عملکرد بهتر در محیط های بسیار خورنده (کلریدی) کمک می کند. اکثر گریدهای آستنیتی را می توان در دامنه های برودتی یا دمای بالا استفاده کرد.
گریدهای آستنیتی زنگ نزن به طور گسترده ای در تجهیزات تولید مواد غذایی، ذخیره سازی مایعات خورنده، ساخت لوله ها و مخازن تحت فشار، ظروف آشپزی، معماری و صنعت حمل و نقل مورد استفاده قرار می گیرند.
منابع
ASM International- Stainless Steels for Design Engineers
Antti Järvenpää, OrcID, Matias Jaskari, Anna Kisko and Pentti Karjalainen. (2020). Processing and Properties of Reversion-Treated Austenitic Stainless Steels. Journal of Metals 2020, 10, 281; doi:10.3390/met10020281
www.corrosionpedia.com
دانلود فقط با IP ایران امکانپذیر است. در صورت عدم مشاهده باکس قرمز رنگ دانلود، VPN خود را خاموش نموده و صفحه را رفرش کنید.
پسورد فایل فشرده : www.iran-mavad.com
دیدگاه کاربران