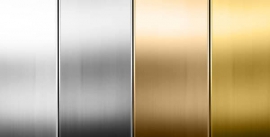
هندبوک تکنولوژی پوشش دهی فلزات (Arthur A. Tracton)
هندبوک پوشش دهی فلزات
Coatings Technology Handbook
(third Edition)
Arthur A. Tracton
شرح :
به طور کلی «پوشش» لایه ای است با ضخامت کمتر از ماده پایه، که پوشش روی آن نشانده می شود. با تغییر ضخامت و نحوه نشاندن پوشش روی ماده پایه، انواع پوشش های مورد نیاز برای کاربردهای خاص را به وجود می آید. تمام مواد نیاز به پوشش دارند، چون نباید در طی مراحل تولید، بسته بندی، ورود به بازار و مهم تر از همه در موقع مصرف، خواص و ویژگیهای خود را از دست بدهند. البته گاهی برای بهبود خواص فیزیکی، شیمیایی و مکانیکی از فناوری پوشش دهی استفاده می شود.
پوشش دهی فلزات برای ایجاد خواص بهتر و یا متفاوت، از قدمت زیادی برخوردار است. روش های معمول پوشش دهی شامل آبکاری الکتریکی و یا الکترولس، پوشش کاری به روش غوطه وری، روکش کردن، پوشش کاری نفوذی، پوشش کاری تبدیلی، پوشش کاری پاششی و غیره است. این پوشش ها معمولا علاوه بر تغییر خواص سطحی مانند سختی، مقاومت به خستگی، مقاومت به سایش، خواص الکتریکی و غیره، به عنوان محافظی برای فلز زیرلایه در برابر اکسید شدن و خوردگی نیز عمل می کنند. فرآیند های پاشش حرارتی خانواده بزرگی از روش های پوشش دهی را در بر می گیرند که در آن ها برای تشکیل پوشش، ذرات فلز بر روی سطح قطعه مورد نظر پاشیده می شوند.
در این دسته فرآیند ها، ذرات ماده پوشش، توسط روش های الکتریکی ( قوس یا پلاسما) و یا شیمیایی گرم شده، همزمان با ذوب شدن توسط جریان گاز سرعت گرفته و به سطح زیرلایه (قطعه تحت پوشش) برخورد می نمایند. سپس به سرعت منجمد شده و تشکیل پوشش می دهند. روش های پاشش حرارتی به دلیل گستره وسیع موادی که می توان با آن ها پوشش داد، نرخ رسوب دهی بالا، انعطاف پذیری فرآیند (در کاربردهای ترمیمی و…)، به سرعت جای خود را در صنایع مختلف باز کردند.
با این حال در روش های پاشش حرارتی به دلیل ماهیت ذوب و انجماد، معایبی همچون تنش پسماند کششی، تخلخل نسبتا زیاد پوشش (۰ الی ۲۰ درصد)، اکسیداسیون ماده پوشش، استحاله های ناخواسته، از بین رفتن عناصر آلیاژی و حرارت دهی بیش از اندازه به زیرلایه وجود دارد. در دو دهه اخیر فرآیند پاششی جدیدی به نام “پاشش کینتیکی” یا اصطلاحا “پاشش سرد” ابداع شده و توسعه یافته که در آن اتصال ذرات بر سطح زیرلایه در حالت جامد (بر خلاف فرآیندهای پاشش حرارتی) صورت می گیرد. در این فرآیند، گاز کاری (هلیم، نیتروژن یا هوا) با عبور از یک نازل خاص (نازل همگرا-واگرا) ضمن اختلاط با ماده پودریِ پوشش، به سرعت های مافوق صوت می رسد. ذرات توسط جریان مافوق صوت گاز سرعت گرفته و به شدت به سطح زیرلایه برخورد می کنند. شدت برخورد بر سطح زیرلایه به حدی است که ذره به همراه بخشی از زیرلایه که به آن برخورد نموده دچار تغییر شکل شدید پلاستیک می شود.
این تغییر شکل پلاستیک شدید سبب اتصال ذره به زیرلایه در حالت جامد می شود. نتیجه چنین اتصالی، ایجاد پوشش یکنواخت با تخلخل بسیار کم و استحکام پیوند بالا است. واژه پاشش سرد به علت دمای نسبتا پایین ( ۰ تا ۱۰۰+ درجه سانتیگراد ) جریان گاز منبسط شده که از نازل خارج می شود، برای نامیدن این فرآیند استفاده شد. در این فرآیند دمای گاز همواره زیر نقطه ی ذوب ذرات مواد پوشش دهی است؛ در نتیجه هیچ گونه ذوب و انجمادی در ذرات صورت نمی گیرد و به همین دلیل، معایبی که در فرآیندهای پاشش حرارتی وجود دارد در اینجا یا حدف شده (مانند تنش پسماند کششی، اکسید شدن ماده پوشش، استحاله های ناخواسته و از بین رفتن عناصر آلیاژی) و یا کمینه می شود (مانند تخلخل در پوشش و حرارت دهی به قطعه تحت پوشش).
علاوه بر حذف معایب فرآیندهای پاشش حرارتی، فرآیند پاشش سرد ویژگی های منحصر به فردی همچون ایجاد پوشش های بسیار ضخیم، امکان پوشش دهی مواد با نقطه ذوب بالا بر روی مواد با نقطه ذوب پایین (مانند تانتالوم بر روی مس) و بازده پوشش دهی بسیار مناسب (تا حدود ۹۸ درصد) را دارد. علی رغم کاربردهای گسترده و وسیع، فرآیند پوشش دهی فلزات سرد هنوز فرآیند نسبتا جوانی محسوب می شود؛ پس طبیعی است که هم اکنون بیشتر در مرحله تحقیقاتی بوده و از تمام ظرفیت های بالقوه صنعتی آن استفاده نشده است.
دانلود فقط با IP ایران امکانپذیر است. در صورت عدم مشاهده باکس قرمز رنگ دانلود، VPN خود را خاموش نموده و صفحه را رفرش کنید.
پسورد فایل فشرده : www.iran-mavad.com
دیدگاه کاربران