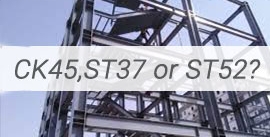
فولاد تریپ (TRIP)
اثر تریپ (TRIP effect) چیست؟
اثر تریپ به معنی تشکیل مارتنزیت بر اثر شکل دهی است. در اینجا، لازم است میان شکل گیری مارتنزیت ناشی از از اعمال تنش (stress-induced)، و شکل گیری آن بر اثر تغییر شکل (deformation-induced)، تمایز قائل شویم. چراکه واژۀ تریپ، تنها بر حالت دوم یعنی تغییر شکل دلالت دارد.
زمانی که آستنیت در دمایی بالاتر از Ms و پایینتر از دمای بحرانیِ MD دفرمه شود، تبدیل به مارتنزیت می شود. اما این تبدیل زمانی اتفاق می افتد که یک میزان تنش یا کرنش بحرانی به ساختار اعمال شود. یعنی به محض اینکه به این میزان بحرانی برسیم، آستنیت سرشار از کربن و نیمه پایدار شروع به تبدیل شدن به مارتنزیت می کند.
در نتیجه می توان گفت فولاد تریپ، توسط تغییر شکل پلاستیک سخت شده است. بنابراین اثر تریپ به این معنی است که تبدیل آستنیت باقیمانده به مارتنزیت، به طور موضعی سبب سخت شدن فولاد شود. حال اگر این اثر در تمام فولاد اتفاق بیفتد، یک فولاد با نرخ بالای کرنش سختی خواهیم داشت که داکتیلیتۀ مطلوبی را همزمان با افزایش سختی رقم خواهد زد.
میزان رخ دادن این اثر در فولاد تریپ تا حدود زیادی به عناصر آلیاژی ارزان قیمتی مانند کربن، منگنز، سیلیکون و آلومینیوم بستگی دارد. به خصوص افزودن سیلیکون باعث سخت شدن فولاد بر اثر تشکیل محلول جامد میشود.
ریزساختار فولاد تریپ
ابتدا تکلیف مان را با عبارت Transformation Induced Plasticity مشخص کنیم. شاید بهترین ترجمۀ فارسی برای این عبارت، “تغییر شکل مومسان در اثر تغییر حالت” باشد. بنابراین در این جا، منظور از TRIP ، بهبود رفتار تغییر شکل مومسان فولاد، در اثر تغییر حالت آستنیت به مارتنزیت در نتیجۀ اعمال نیروهای مکانیکی است.
ریزساختار فولاد TRIP شامل حداقل پنج درصد حجمی آستنیت باقی مانده است، که در فاز فریت اولیه جاسازی شده است. البته این ریزساختار شامل فازهای سختی مانند بینیت و مارتنزیت در مقادیر متنوع نیز هست.
اعمال شرایط ایزوترمال به طور ثابت (در دماهای متوسط) برای ایجاد ساختار بینیت در فولاد تریپ مورد نیاز است. حضور آستنیت باقی مانده در ریزساختار نهایی، آن هم در نسبت های حجمی بزرگ، نتیجۀ مقادیر بالای کربن و سیلیسیم در فولادهای تریپ است.
یک شماتیک کلی از ریز ساختار فولاد TRIP در شکل زیر نشان داده شده است و یک تصویر میکروسکوپی نیز از فولاد تریپ ۶۹۰ نیز در آن دیده می شود.
عملیات حرارتی تولید فولاد تریپ
فولادهای تریپ را می توان از طریق نورد سرد، نورد گرم یا گالوانیزۀ عمیق گرم با استحکام ۵۰۰ تا ۸۰۰ مگاپاسکال تولید کرد. اما آن چه اهمیت ویژه ای در تولید این فولاد دارد، عملیات حرارتی آن است.
برای تولید یک فولاد مستحکم و داکتیل، فرآیند آنیل Intercritical برای به دست آوردن توزیع فاز مطلوب ضروری است. در طی این عملیات حرارتی، فولاد به دمای بالای یوتکتوئید منتقل می شود که در آن منطقه، متریال شامل فازهای آستنیت و فریت است.
آستنیت یک فاز جامدِ دما بالا است که فقط در شرایط تعادلی در دماهای بالاتر از ۷۲۷ درجه سلسیوس وجود دارد. پس از گرمایش تا بالای یوتکتوئید، فولاد تا دمایی حدود ۴۰۰ درجه سلسیوس خنک می شود تا به آستنیت اجازه دهد که بینیتِ فریتی را تشکیل دهد. سپس دو مسیر برای حصول حالت نهایی وجود دارد که در شکل زیر مشخص است.
این موضوع بسیار مهم است که تحول ایزوترمال یوتکتوئیدی، در دمایی کامل شود که تشکیل فریت بینیتی، به حد کافی آهسته باشد. این آهستگی سبب نفوذ کربن به فاز آستنیت می شود. در ادامه این موضوع را دقیق تر بررسی می کنیم.
غنی سازی آستنیت باقیمانده از کربن
حضور آستنیت باقی مانده در ریزساختار پایانی، نکتهای بسیار کلیدی در مفهوم فولاد TRIP است. بنابراین، دستیابی به حداکثر مقدار کربن ممکن در بخش های آستنیتی نهایی، برای کاهش دمای MS به زیر دمای محیط ضروری است. البته این موضوع در فولادهایی که شامل ۰.۲ درصد کربن باشند، صدق می کند. از این رو عملیات حرارتی فولاد تریپ، به منظور غنی سازی فاز گاما با کربن در طول تبدیلات فازی اجرا می شود.
سه فرآیند مهم در طول گرمایش تا دمای intercritical اتفاق می افتد:
- تبلور مجدد فریت
- انحلال سمانتیت
- شکل گیری آستنیت
تمام ملاحظات مربوط به اثرات ساختار اولیه یا نرخ گرمایش در فولادهای دوفازی، در عملیات حرارتی فولاد TRIP نیز صدق می کند. (برای مطالعۀ بیشتر در این مورد، می توانید به فصل دوم کتاب Advanced High Strength Sheet Steels (pp 185-239) مراجعه کنید.)
نکته ای که برای دستیابی به خواص مورد نظر در فولاد تریپ ضروری است، اطمینان حاصل کردن از درصد کربن ابتدایی در ساختار (۰.۲ درصد) و درصد فریت حدودا 50 درصد است. البته همین مقادیر هم برای غنی سازی فاز آستنیت با کربن در آنیل intercritical کافی نیست.
برای رسیدن به ماکزیمم محتوای کربن در آستنیت و جلوگیری از تحول مارتنزیتی در سرمایش نهایی تا دمای اتاق، مقادیر بیشتری از کربن لازم است. مشخص است که در حین تحول بینیتی، کربن توزیع مجدد می شود و ترکیب فریت/سمنتیت (کاربید) پدید می آید. یعنی کربن مصرف می شود!
بنابراین تنها راهی که برای جلوگیری از مصرف کربن داریم، اضافه کردن عناصر فریت زا است. این عناصر از رسوب کاربیدها جلوگیری می کنند و فازهایی عاری از کربن یعنی فریتِ بینیتی به وجود می آورند. از این رو شرایط مطلوب برای افزوده شدن کربن به آستنیت باقی مانده مهیا می شود.
با توجه به نقش حیاتی عناصر آلیاژی در تاخیر تشکیل کاربید، بخش اعظمی از جزئیات تبدیل فاز و اثر پارامترهای آنیل در ریز ساختار فولاد تریپ، وابسته به ملاحظات ترکیب شیمیایی است.
ترکیب شیمیایی فولاد TRIP
فولادهای تریپ نوعی فولاد هیپویوتکتوئیدی به شمار می روند که به طور معمول حاوی 0.1 تا 0.4 درصد وزنی کربن است. همان طور که گفتیم، فولاد تریپ شامل عناصر آلیاژی است که از رسوب فاز سمنتیت که در فولادهای معمولی در دمای اتاق وجود دارد، جلوگیری می کنند.
سیلیکون و آلومینیوم متداول ترین عناصری هستند که برای تثبیت فاز آستنیت در دمای اتاق به کار می روند. دیگر عناصر آلیاژی مانند تیتانیوم، نیوبیوم و وانادیوم نیز می توانند به بهبود استحکام فولاد TRIP کمک کنند.
وانادیم ؛ الهه زیبایی در فلزات!
وانادیم الهۀ زیبایی در فلزات است. اگرچه این فلز شهرت کمی دارد؛ اما به دلیل مقاوم...نرخ های کار سختی در فولاد تریپ
در هنگام تغییر شکل فولادهای دوفازی (DP) فازهای ثانویۀ سخت، در زمینۀ نرم فریتی توزیع شده اند. این فازهای سخت سبب افزایش نرخ کارسختی در فولاد می شوند. با این حال، در مورد فولادهای تریپ، کرنش فزاینده، باعث تبدیل شدن آستنیت باقی مانده به مارتنزیت می شود. بدیهی است که این اتفاق، همانطور که در شکل زیر دیده می شود، سبب افزایش نرخ کارسختی در سطوح کرنش بالاتر می شود.
در شکل بالا، می بینیم که فولاد تریپ 350 و 360 الانگیشن کلی بیشتری نسبت به فولادهای DP و HSLA دارد. همچنین مشخص است که نرخ اولیۀ کارسختی فولاد TRIP، کمتر از فولاد DP است. اما نرخ کارسختی فولاد TRIP در سطوح کرنش بالاتر، بیشتر می شود.
قابلیت حفظ نرخ بالای کارسختی در سطوح بالاتر کرنش، موجب می شود که فولاد TRIP انتخاب بهتری نسبت به فولادهای DP در کاربردهایی شامل شکل دهی شدید باشد.
آیا در فولادهای تریپ اثر سایز وجود دارد؟
شاید بدون بررسی دقیق اثر سایز در فازهای فولاد تریپ هم می توانستیم به این سوال پاسخ “بله” بدهیم. چرا که همیشه در فولادها اثر سایز وجود دارد! برخی فولادهای مدرن که حاوی جزایر آستنیتی در مقیاس نانو و یا فیلمهای پراکنده شده در ماتریس مارتنزیتی باشند، علاوه بر استحکام بسیار بالا، شکل پذیری و چقرمگی مناسبی نیز از خود نشان می دهند.
هنوز مکانیسم ریزساختاری مربوط به این خواص، به طور دقیق درک نشده است. اما پژوهشگران نتیجه گرفته اند که این موضوع به شدت به این جزیره های نانومقیاس یا اندازۀ فیلم های پراکنده، مربوط است. دو اثر میکرومکانیکی اصلی را در این زمینه می توان در نظر گرفت:
- برهمکنش فاز گاما با میکرو ترک های موجود در ماتریس
- تحول فازی گاما به مارتنزیت، ناشی از تغییر شکل (همان اثر تریپ)
که این جا تمرکز بر روی پدیدۀ دوم است. برای بررسی تاثیر اندازه در تحول گاما (بدون در نظر گرفتن عوامل دیگر) یک مدل سازی بر اساس نرم افزار DICTRA انجام شده است. تحقیقات نشان داده است که در این نوع تحول، ذرات کوچکتر پایداری کمتری دارند. همچنین آثاری از دخالت دوقلویی های مکانیکی نیز در تحول فازی ناشی از تغییر شکل مشاهده شده است که بررسی آن در این مطلب نمی گنجد. علاقمندان برای مطالعۀ بیشتر در این باره، می توانند به مقالۀ زیر مراجعه کنند:
Wang et al, “Smaller is less stable: Size effects on twinning vs. transformation of reverted austenite in TRIP-maraging steels”, Acta Materialia 79 (2014) 268-281
کاربردهای فولاد TRIP
از دهۀ 1980، فولاد تریپ به عنوان موادی بالقوه برای بدنه خودرو ظاهر شد. بخش اعظمی از این اتفاق، در نتیجۀ تحقیقات گستردۀ شرکت Nippon Steel بود. با این حال، تقریبا دو دهه طول کشید تا ذهنیت تولید کنندگان فولاد تعدیل شود و کاربرد بین المللی فولاد تریپ در صنایع اتوموبیل توسعه یابد.
صنعت خودرو نیاز بالایی به برآورده کردن تقاضای صرفه جویی در سوخت دارد. علاوه بر موضوع سوخت، جلوگیری از سوانح مختلف نیز در دستور کار است. از این رو امروزه تمام شرکت های اتوموبیل سازی، قصد گسترش تعداد قطعات تولید شده از فولادهای استحکام بالا با کیفیت شکلپذیری بهتر را دارند.
چرا که پارامترهای بهتر در رفتار مکانیکی بخش های مختلف اتوموبیل، سبب حفظ ایمنی مسافر میشود. فولاد TRIP به دلیل مزایایی که دارد، موضوع بسیار جالبی برای تحقیقات آزمایشگاهی، بحثهای علمی، و در نهایت برای آزمایشها صنعتی و تجاری سازی شده است.
در یک کلام، این فولادها برای کاربردهای خودروسازی عالی هستند؛ جایی که نیاز به کارسختی بالا طی تغییر شکل ناشی از تصادفات است. و البته فولاد باید مقدار زیادی انرژی جذب کند. این فولادها همچنین برای ایجاد هرنوع قطعۀ پیچیده، سخت و شکل پذیر مناسب هستند.
متداول ترین گریدهای فولاد TRIP شامل 2 نوع تولیدی از نورد سرد در هر دو حالت بدون پوشش و با پوشش (TRIP 690 و TRIP 780) و یک گرید تولید شده با نورد گرم (TRIP 780) است. جدول زیر کاربردهای فولاد تریپ را بر حسب گرید آن خلاصه کرده است.
فولاد تریپ از منظر اقتصادی
به طور کلی از فولاد معمولاً به دلیل استحکام، شکل پذیری و کم هزینه بودن نسبت به سایر فلزات استفاده می شود. اگر چه فلزاتی مانند تیتانیوم، منیزیم و آلومینیوم نسبت استحکام به وزن بالاتری دارند و می توانند صرفه جویی قابل توجهی در وزن قطعات خودرو ایجاد کنند.
با این وجود، به دلیل فراوانی کمتر، هزینه های تولید بیشتر و هزینه های ماشینکاری، بسیار گران تر تمام می شوند. بنابراین عرضۀ این فلزات در سراسر جهان نسبتاً محدود است. این عوامل باعث می شود که این فلزات به طور معمول در اتومبیل هایی که اکثر مردم رانندگی می کنند، استفاده نشوند.
فولاد تریپ با هیچ یک از این مشکلات روبرو نیست! چرا که یک فولاد کم آلیاژ است. اجرای مرحله آنیل intercritical در پردازش این نوع فولاد، خیلی دشوار به نظر نمی رسد. این بدان معنی است که فولاد TRIP می تواند با همان قیمت سایر فولادهای استحکام بالا تولید شود. مهمترین مانعی که فولادهای تریپ در بازار با آن رو به رو شده اند، ضعف در گالوانیزه کردن سطحی در پایان فرایند تولید آن است.
فرآیند گالوانیزه کردن در تعداد زیادی از اجزای خودرو اعمال می شود. زیرا آسان، ارزان و بسیار موثر است. با کشف آلومینیوم به عنوان جایگزینی برای سیلیکون، فولادهای TRIP دیگر با مشکلات گالوانیزۀ گذشته روبرو نیستند. فولادهای TRIP اکنون می توانند به طرز موثری از نظر اقتصادی در برابر خوردگی محافظت شوند. این بدان معناست که ممکن است در آینده شاهد تولید فزایندۀ فولاد تریپ باشیم.
دیدگاه کاربران
سلام. من خودم مهندس مواد هستم. خیلی از فولادها و استحاله ها را میشناسم
مطالب که نوشته اید گنگ است، منسجم نیست، اصطلاحات غیر علمی دارد و خلاصه من که رشته تحصیلی و شغلی م مرتبط با فولادهاست چیزی ازش نفهمیدم.
به ویژه نامگذاری این فولادها. نه نامگذ اری انگلیسی و نه ترجمه فارسی، هیچ کدام گویا نیست.