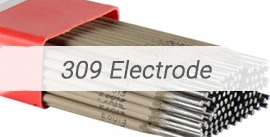
روش های آهنگری (فورج) – قسمت دوم
این مقاله در دو قسمت تهیه شده است. پیشنهاد می کنیم که پیش از مطالعه این مقاله، بخش اول مقاله را که در خصوص معرفی تکنیک فورج نوشته شده، مطالعه نمایید.
تکنیک فورج با توجه به دامنه کاربرد وسیعی که دارد، به چندین روش تقسیم می شود. برای سادگی بیشتر، ما در این مقاله این روش ها را در سه دسته مورد بررسی قرار داده ایم:
تقسیم بندی روش های فورج بر اساس دمای کار
آهنگری سرد (Cold Working)
اين نوع آهنگری در دمای محيط و غالبا در چندين مرحله اجرا می شود. دمای این فرایندها تا اندازه ای پایين است كه فلز اكسيد نشود و در آن كار سختی ايجاد شود. از این رو دقت ابعادی در مقایسه با آهنگری داغ بالاتر است. آهنگری سرد برای فلزات نرم مانند قلع، سرب و آلومينيم قابل اجرا است، اما برای فولادها تقريباً غيرممكن است.
آهنگری گرم (Warm Working)
این روش يک فرایند تعديل يافته از آهنگری سرد و داغ است كه قطعه کار تا دمایی زیر دمای تبلور مجدد حرارت می بیند. در طی فورج گرم، انتقال گرما از قطعه داغ به قالب و به محيط اطراف (از طریق جابجايی و تشعشع) سبب کاهش دمای قطعه می شود. بنابراين خواص ماده در طول فرآيند متغير است.
آهنگری داغ (Hot Working)
در فورج داغ دمای قطعه بيشتر از دمای تبلور مجدد آن است. این دما برای فولادها بالاتر از 600 تا 700 درجه سلسیوس است. يعنی دمای بيلت در حدی بالا است كه از ايجاد كرنش سختی در طی فرآيند فورج جلوگيری شود. در اين حالت، به دليل بالا بودن دمای قطعه، تمايل به اكسيد شدن بسيار زياد است. بنابراین دست يابی به ابعاد دقيق بسيار مشكل خواهد بود.
آهنگری ایزوترمال (Isothermal Forging)
این فرایند نوع خاصی از آهنگری داغ است که معمولا در منابع به عنوان تکنیکی جداگانه طبقه بندی می شود. در آهنگری ایزوترمال، فلز و قالب تا یک دمای یکسان گرم می شوند. دمای قالب در این فرایند بسیار بالاتر از روش های معمول فورجینگ است. استفاده از این نوع آهنگری، نرخ کرنش بسیار پایین تری را در مقایسه با روش های دیگر رقم می زند.
قطعات تولیدی با این روش بسیار نزدیک به خواص نهایی مورد نظر هستند و معمولا نیازی به ماشین کاری ندارند. امروزه از این روش برای تولید اجزای موتور جت با جنس آلیاژهای تیتانیوم و نیکل استفاده می شود. البته مقاطع فولادی مختلف نیز با این روش قابلیت تولید دارند.
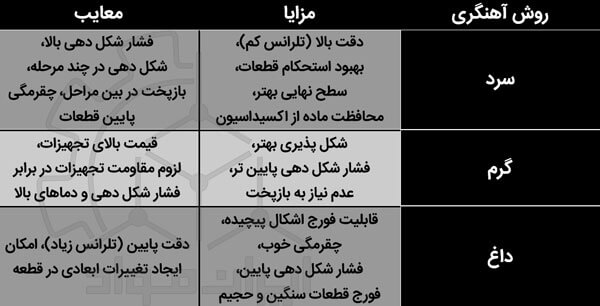
تقسیم بندی روش های فورج از نظر دقت ابعادی
آهنگری دقیق
هدف نهایی این روش تولید قطعه ای است که شکل آن بسیار نزدیک به شکل نهایی مورد نظر باشد و یا این که قطعه خروجی دقیقا شکل نهایی را داشته باشد. به همین دلیل، پس از شکل دهی به این روش قطعه نیازی به ماشین کاری ندارد یا ماشین کاری آن بسیار کم است.
در آهنگری دقيق، ابعاد قطعه بايد به دقت تعيين شود تا فلز كاملا محفظه قالب را بدون هيچ ماده اضافه ای پر كند. یعنی قطعه باید در دقيق ترین و مناسب ترین موقعیت قرار بگیرد. نکته بعدی این است که طراحی قالب و روان كاری آن به صورتی باشد كه جريان فلز در حین عملیات كنترل شود.
اصولا فرایندهای آهنگری سرد و در برخی موارد آهنگری گرم روش های دقیقی هستند یا این که با تمهیداتی می توان آن ها را دقیق کرد. در شکل زیر یک قطعه آلومینیومی را مشاهده می کنید که به این روش تهیه شده است.
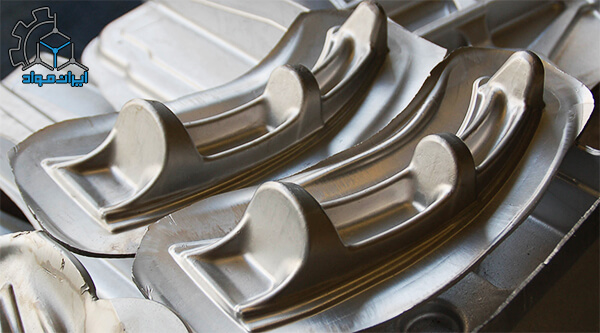
آهنگری معمولی
در اين نوع فرآيندها، متریال آهنگری بين قالب ها شكل می گیرد تا قطعه مورد نظر به دست آید. در این حالت یک سری مواد اضافی (فلاش یا پلیسه) به صورت زائده های نازكی بين دو نيمه قالب قرار می گیرد که در انتهای آهنگری توسط قالب ديگری برش داده شده و جدا می شود.
در آهنگری به روش معمولی معمولا تنش های کمتری به قالب وارد می شود که هزینه نگهداری و تعمیرات آن را کاهش می دهد، اما قطعات تولید شده دقت و تلرانس ابعادی متوسطی دارند و پس تولید نیاز به ماشین کاری خواهند داشت.
تلرانس چیست؟ (Tolerance) همه چیز درباره تلورانس
رسیدن به اندازه های دقیق در صنعت ممکن نیست! این واقعیت تلخ اما عادی، با توجه به ...تقسیم بندی روش های آهنگری از نظر نوع قالب
فورج قالب باز (Open Die Forging)
این فرایندها با نام های فورج آهنگری (smith)، چکشی (hammer)، دستی (hand) و قالب تخت (flat-die) نیز شناخته می شوند. در فورج قالب باز، یک چکش با ضربه ای که به قطعه وارد می کند، سبب تغییر شکل آن می شود. منظور از چکش، هر عاملی است که بتواند نیروی زیادی را به قطعه وارد کند.
در آهنگری قالب باز، قطعه بین دیواره های قالب محصور نمی شود و می تواند آزادانه در دو راستای طولی و عرضی جریان پیدا کند.
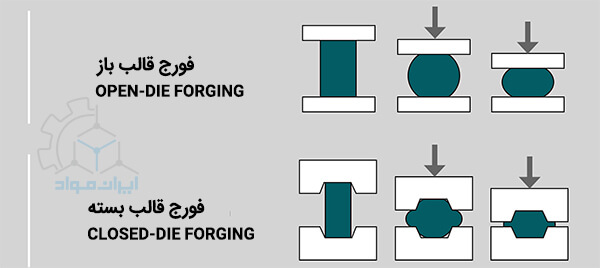
معمولا زمانی که ابعاد قطعات بزرگتر از آن باشند که بتوان آن ها را در قالب های بسته تولید کرد، از روش قالب باز استفاده می شود. اپراتور این روش ها باید جهت گیری و موقعیت قطعه را برای رسیدن به شکل و ابعاد مورد نظر تنظیم کند.
قالب ها در این فرایند معمولا مسطح هستند، اما می توان آن ها را با سطوحی خاص جهت اجرای عملیات مشخصی طراحی کرد. برای مثال، یک قالب ممکن است سطحی گرد، مقعر یا محدب داشته باشد و یا حتی ابزاری برای ایجاد سوراخ یا برش داشته باشد.
در این روش، ممکن است از قالب هایی با چند کیلوگرم وزن تا قالب های 600 تنی استفاده شود. امروزه شفت های پروانه ای مورد استفاده در کاربردهای دریایی که 23 متر طول و چندین متر قطر دارند، با فورج قالب باز تولید می شوند. بنابراین محدودیت سایز و وزن قطعات تولیدی با این روش، تنها به محدودیت ابزار ایجاد حرارت و خصوصا قالب بستگی دارد.
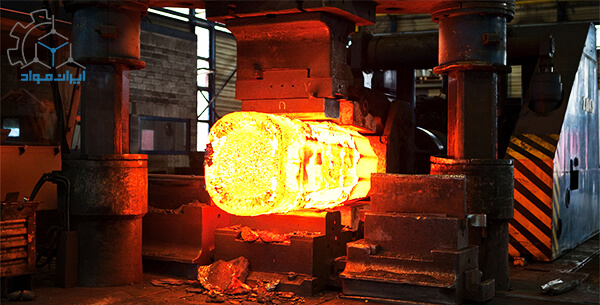
کاهش احتمال تشکیل حفرات، مقاومت بالا در برابر خستگی، جریان دانه پیوسته (Continuous grain flow) و ریزدانگی از ویژگی قطعات تولید شده به روش فورج قالب باز هستند.
فورج آپست داغ (Hot Upset Forging)
فورج آپست داغ که آهنگری ماشینی نیز نامیده می شود، فرایندی است که برای بزرگتر شدن و تغییر سطح مقطع میله، لوله یا دیگر محصولاتی که مقطع یکنواخت دارند، اجرا می شود.
ساده ترین شکل آهنگری آپست داغ، با نگه داشتن قطعه داغ بین قالب های شیاردار و اعمال فشار از طریق قالب های هدینگ (Heading) به انتهای قطعه انجام می گیرد. البته می توان از قالب های شیاردار نیز برای اعمال نیرو به قطعه استفاده کرد.
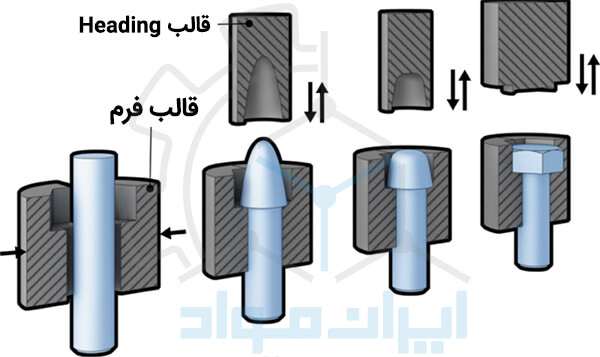
در فورج آپست، به دلیل همزمان شدن حرکت عرضی قالب و اعمال نیروی طولی، قابلیت فورجینگ در دو جهت وجود دارد.
فورج آپست داغ بیشترین تنوع را در بین محصولات تولیدی به روش آهنگری دارد. از این روش می توان برای تولید دریچههای موتور، کوپلینگ ها، پیچ ها و برخی اتصالات فلزی دیگر استفاده کرد.
فورج نوردی (Roll Forging)
در این فرایند، سطح مقطع میله یا بیلت حرارت دیده کاهش می یابد. این کاهش سطح مقطع، با گذشتن قطعه از میان دو غلتک متحرک که در مخالف جهت یکدیگر می چرخند، انجام می گیرد.
هدف اصلی از اجرای فورج نوردی، کاهش ضخامت و افزایش طول قطعه است. این کار تا زمانی ادامه پیدا می کند که شکل و اندازه مورد نظر به دست آید.
با توجه به کاربرد، غلتک های مورد استفاده می توانند شیارهایی داشته باشند یا نداشته باشند. تمام فلزاتی که با دیگر روش های آهنگری شکل داده می شوند، می توانند با این روش نیز شکل دهی شوند.
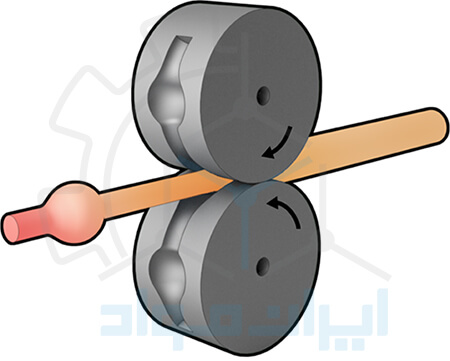
نورد حلقه (Ring Rolling)
در این فرایند از دو غلتک برای شکل دهی یک حلقه استفاده می شود. يک غلتک از درون سوراخ حلقه می گذرد و غلتک دوم آن را از بيرون فشار می دهد. با چرخش غلتک ها و فشرده شدن حلقه با ضخامت بالا در بين آن ها، ضخامت حلقه به تدريج كاهش یافته و قطر آن بیشتر می شود.
با استفاده از غلتک های شكل دار می توان انواع سطح مقطع را توليد كرد. اجزای موشک، توربين، هواپيما، مخازن تحت فشار و رینگ های آلومینیومی از جمله محصولاتی هستند که با این روش تولید می شوند.
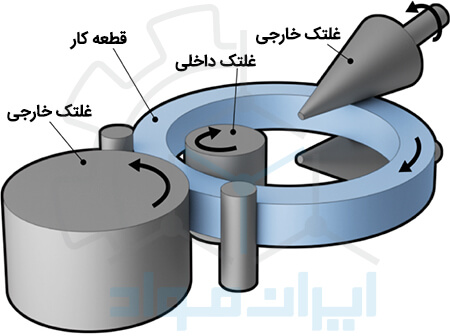
فورج دوار (Rotary Forging)
فورجینگ دوار نوعی فرایند شکل دهی دو قالبه است که فقط یک قسمت کوچک از قطعه کار در هر لحظه و به صورت پیوسته تغییر شکل می یابد. در این روش محور قالب بالایی نسبت به محور قالب پایینی انحراف دارد. همین انحراف است که باعث می شود نیروی فورج فقط به سطح کوچکی از قطعه کار وارد شود.
بدیهی است هر چه این زاویه انحراف بیشتر باشد، طراحی، نگهداری و تعمیرات قالب مشکل تر است. این روش نیز مانند روش های دیگر با ایجاد تنوع در دستگاه، زاویه، نوع و شکل قالب و دمای کاری می تواند انواع و اقسام مختلفی پیدا کند. قطعاتی مانند چرخ دنده ، فلانج ، توپی، بادامک و یاتاقان های غلتکی و مخروطی را می توان با این روش تولید کرد.
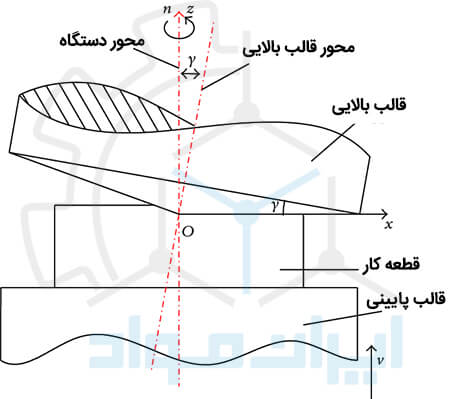
فورج شعاعی (Radial Forging)
فورج رادیال یا شعاعی نوعی فرایند آهنگری قالب باز است که در آن قالب ها روی فک های یک ماشین فورج که حرکت نوسانی رفت و برگشتی دارند، سوار می شوند. حرکت این فک ها همزمان و هماهنگ بوده و وقتی در انتهای کورس خود قرار گیرند، سبب ایجاد یک مقطع بسته می شوند.
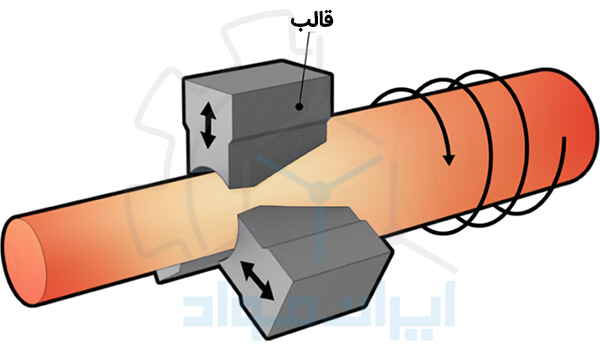
قطعه کاری که می تواند پیشروی دورانی یا محوری داشته باشد، از این مقطع گذرانده می شود. در اثر ضربات فک ها این قطعه تغییر شکل یافته و سطح مقطع متفاوتی پیدا می کند. در این فرایند معمولا یک ماندرل در درون لوله قرار می گیرد تا به کمک آن بتوان پروفیل مورد نظر را داخل لوله ایجاد کرد.
فورج شعاعی به طور گسترده در کاهش قطر محورها، لوله ها، اکسل ها، محورهای پله ای و تولید پروفیل های داخلی در لوله ها مثل لوله تفنگ مورد استفاده قرار می گیرد.
فورج قالب بسته (Closed Die Forging)
به فرایند شکل دهی که یک قطعه به طور کامل درون دیواره ها یا حفرات دو قالب محبوس شود و به شکل مورد نظر درآید، آهنگری قالب بسته گفته می شود. این فرایند در منابع لاتین با نام Impression-die forging نیز شناخته می شود.
در این روش، یک قالب نقش سندان را دارد و قالب دیگر نقش چکش. قالب چکشی به روی فلز ضربه وارد می کند و سبب پر شدن حفرات قالب زیرین می شود. در اکثر موارد، قالب چکشی نیز شکل خاصی دارد.
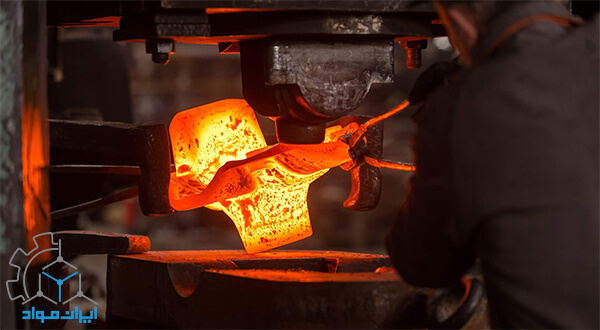
تماس چکش با فلز در مقیاس میلی ثانیه اتفاق می افتد و فلزات اضافی (فلاش یا پلیسه) از حفره های قالب خارج می شوند. فلاش سریع تر از بقیه مواد سرد می شود و همین موضوع باعث می شود که مستحکم تر از فلز درون قالب باشد. پس از تکمیل فرایند فورج، فلاش حذف می شود.
با استفاده از قالب های بسته، علاوه بر ایجاد تغییر شکل زیاد در قطعه، می توان اشکال پیچیده با ابعادی دقیق و با تیراژ بالا تولید کرد. در این قالب ها جهت جریان دانه کنترل می شود و قطعاتی با خواص مکانیکی عالی در جهت طولی به دست می آید.
از قالب های باز معمولا برای شکل دهی اشکال ساده یا بیش از حد بزرگ استفاده می شود، در حالی که قالب های بسته برای تولید اشکالی دقیق و نزدیک به شکل نهایی کاربرد دارند.
روش های آهنگری با نرخ انرژی بالا (HERF)
این فرایند که بعضا آهنگری با سرعت بالا نیز نامیده می شود، نوعی آهنگری قالب بسته است که می تواند به صورت گرم یا سرد انجام گیرد. در تکنیک HERF از انرژی ذخیره شده در یک گاز با فشار بالا برای افزایش چشمگیر سرعت تغییر شکل در قطعه استفاده می شود. از این رو خواص نهایی قطعه معمولا در یک یا دو کورس آهنگری به دست می آید. سرعت ضربه در ماشین های HERF از 5 تا 22 متر بر ثانیه متغیر است. سرعت پیستون نیز می تواند بین 4.5 تا 9.1 متر بر ثانیه متغیر باشد.
فورج پودری (Powder Forging)
آهنگری پودری از روش های تکمیلی و نوین برای بهبود خواص مهندسی قطعات متالورژی پودر است. آهنگری پودری بسیاری از مراحل تولید سابق در متالورژی پودر را حذف می کند. اولین مرحله برای اجرای فورج پودری، شکل دادن پودر به صورت قطعه خام اولیه است. این مرحله توسط پرس های کامپکت انجام می شود.
قطعه اولیه باید به نحوی طراحی و ساخته شود که انتقال پودر و در نتیجه توزیع وزنی قطعه را تضمین نماید. پس از کامپکت کردن نوبت به زینترینگ (Sintering) قطعات در کوره می رسد. پس از زینترینگ، قطعات توسط ربات یا به صورت دستی در قالب بسته قرار می گیرند. البته بسته به کاربرد و دمای کاری می توان از پودرهای فلزی زینتر نشده نیز استفاده کرد.
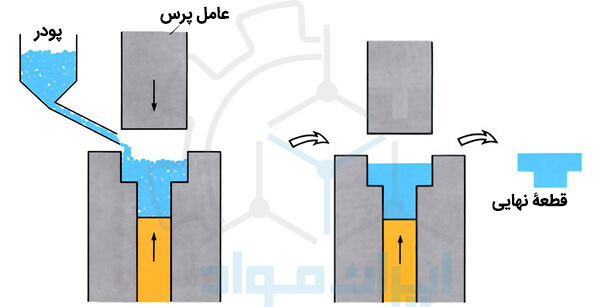
پرس فورج پودری معمولا به صورت هیدرولیک، ضربه ای و اتوماتیک عمل می کند. استفاده از روش آهنگری پودر باعث بهبود خواص مکانیکی مخصوصاً خواص خستگی می شود. آن چه مشخص است، این است که چگالی پودرهای زینتر شده تاثیر زیادی بر خواص مکانیکی قطعات آهنی و فولادهای کم آلیاژ تولیدی با این روش خواهند گذاشت.
سکه زنی (Coining)
سکه زنی نوعی آهنگری قالب بسته است که معمولا به صورت سرد انجام می شود. امروزه از این روش برای شکل دادن سکه ها، مدال ها و جواهرات استفاده می شود. در سکه زنی، برای رسیدن به ابعاد دقیق به فشارهایی تا پنج یا شش برابر استحکام ماده نیاز است.
در این فرایند نمی توان از مواد روانکار استفاده کرد؛ چرا که فلز تحت فشار بالا رفتار غیر قابل تراکم از خود نشان می دهد و از شکل دهی دقیق قطعه جلوگیری می شود.
با توجه به نوع کاربرد و طراحی قالب، فلز به دلخواه نازک يا ضخیم شده و يا پستی و بلندی های مناسب در مقطع فلز ایجاد می شود. از اين روش به طور گسترده برای حروف زنی روی ورق های فلزی یا قطعاتی نظیر سکه ها استفاده می شود.
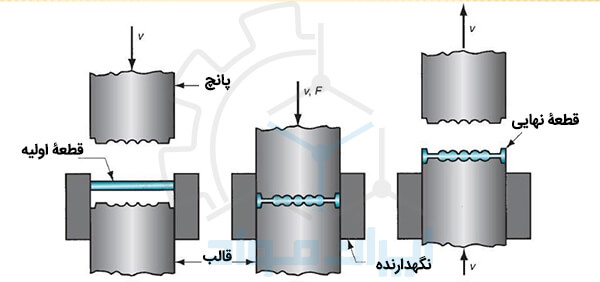
منابع
ASM Handbook-Volume 14- Forming and forging
www.en.wikipedia.org
www.reliance-foundry.com
دیدگاه کاربران
بسیار ممنون از مقاله جالب و علمی شما