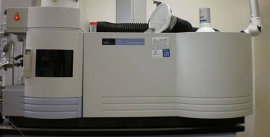
افزایش ایمنی در بازرسی با فناوری درون خطی التراسونیک (ILI)
سیستم های مدیریت یکپارچگی خط لوله برای اطمینان از عملکرد ایمن و مطمئن شبکه های لوله کشی بسیار حائز اهمیت هستند. در صنعت نفت و گاز، مقررات متعددی وجود دارد که مسئولین خطوط را ملزم می کند به صورت دوره ای، یکپارچگی خطوط لوله را ارزیابی کنند. یکی از متداول ترین و پذیرفته شده ترین روش ها برای انجام این نوع ارزیابی، آزمون فشار هیدرواستاتیک (Hydrostatic Pressure Testing) است.
آزمون فشار هیدرواستاتیک چیست؟
آزمون فشار هیدرواستاتیک یا به طور خاص تر آزمون هیدروتستینگ پس از ساخت (Post-Construction Hydrotesting)، فرایندی است که با استفاده از آب، فشاری بیشتر از فشار عملیاتی بر روی یک خط لوله اعمال می شود.
نشت های محتمل، ممکن است به عنوان افت فشار هیدرواستاتیک در امتداد لوله یا به صورت بصری و با استفاده از رنگ شناسایی شوند. برای خطوط لولۀ در حین کار، آزمایشات فشار پس از ساخت می تواند نقایص موجود را برجسته و همچنین تناسب و کفایت نصب لوله را تأیید کند.
در حالی که آزمایش هیدروتست پس از ساخت می تواند نتایج فوری را به همراه داشته باشد، این روش دارای اشکالات قابل توجهی است:
در وهلۀ اول، از کار انداختن بخشی از خط لوله برای آزمایش هزینه بر است. عمل برداشتن مقاطع لوله، نصب تجهیزات تست، تحت فشار قرار دادن لوله، آبگیری (Dewatering) و سرانجام بازگرداندن بخش های لوله به توقف گسترده ای در خط لوله نیاز دارد. به ویژه در صنعت پتروشیمی، دوره های طولانی توقف کار خط لوله می توانند بسیار گران تمام شوند.
آزمون هیدرواستاتیک پس از ساخت چه مشکلاتی به همراه دارد؟
گفتیم که پیامدها و هزینه های آزمایش هیدرواستاتیک نگران کننده است. اما این روش، خطرات ایمنی و زیست محیطی نیز به همراه دارد. آزمون فشار، ذاتاً ماهیتی مخرب دارد. چرا که لوله تحت فشارهای بالاتر از حد طبیعی قرار گرفته و نقص های موجود را مجبور به خرابی می کند. این عملیات پیامدهای مختلفی را به دنبال خواهد داشت.
آزمون فشار (Compression Test)
مروری بر آزمون فشار در مواد مقدمه آزمون فشار، یکی از آزمون های مخرب مورد استفاد...- تحت فشار قرار دادن خط لوله تا حداکثر حد تحمل خود، می تواند نقایص موجود را تقویت کند یا حتی نقصی ایجاد کند که در هنگام کار عادی خطوط لوله ظاهر نشده باشد.
- موضوع مسئله سازتر این است که این نقص های جدیدتر، ممکن است بلافاصله در تست هیدرواستاتیک شکست نخورند. بنابراین با دوباره کارکردن لوله، شناسایی نشده باقی بمانند و سبب خرابی های جبران ناپذیری در آینده شوند.
- علاوه بر این، تست هیدرو پس از ساخت، در مکان نقص خط لوله را می شکند و باعث نشت مایع به خاک اطراف می شود. این نشت می تواند عواقب ویرانگری بر روی سازه ها و زیرساخت های اطراف مانند بزرگراه ها، پل ها و پایه های ساختمان ایجاد کند.
- شاید یکی از خطرناک ترین جنبه های آزمون هیدرواستاتیک پس از ساخت، خطری باشد که برای ایمنی کارگران در محل ایجاد می کند. تجمع فشار شدید در خط، می تواند منجر به آزاد شدن ناگهانی و ناخواسته انرژی ذخیره شده شود.
- وجود ترک، خرابی و شل بودن اتصالات، شیرهای معیوب و خرابی هایی از این دست، به طور تصاعدی این خطر را افزایش می دهند. برخی از خطرات احتمالی ایمنی مرتبط با آزمایش فشار هیدرواستاتیک عبارتند از:
- پرتاب شدن اجزای لوله؛ مانند شیرآلات، سوپاپ ها، فلنج ها و اتصالات
- پرتاب ترکش های ناشی از پارگی قطعات لوله
- خطر ایجاد سیل در مناطقی که صنایع برق تحت انرژی وجود دارد.
اما چگونه بازرسی درون خطی التراسونیک بر این مشکلات فائق آمده است؟
بازرسی درون خطی اولتراسونیک (Ultrasonic Inline Inspection) که با حروف مخفف ILI شناخته می شود، شامل استفاده از امواج فراصوت برای ارزیابی یکپارچگی خط لوله است. این امواج صوتی که توسط مبدل ها ساطع می شوند، از طریق مواد تشکیل دهندۀ خط لوله، منتشر می شوند. وقتی امواج صوتی با مرزی روبرو می شوند (برای مثال ترک)، بخش هایی از آن به مبدل بازتاب می شوند و به سیگنال الکتریکی تبدیل می شوند.
آزمون اولتراسونیک به عنوان یک آزمایش غیر مخرب طبقه بندی می شود. به عبارت دیگر، با این آزمون می توان خط لوله را با خیالی راحت و بدون به خطر انداختن یکپارچگی فعلی آن ارزیابی کرد. از آنجا که بازرسی های التراسونیک درون خطی تحت فشار نیستند، خطر پارگی ناشی از فشار بالا از بین می رود. همچنین می توان از امنیت کارگران مجاور و عموم مردم منطقه اطمینان حاصل کرد.
از آنجا که در هنگام بازرسی درون خطی التراسونیک لوله از مایعات استفاده نمی شود، احتمال نشت مایع به خاک اطراف وجود ندارد. بنابراین، عوارض جانبی مانند آلودگی محیط زیست و فرو ریختن سازه های مجاور، دیگر نگران کننده نیست.
استفاده از فناوری های پیشرفته در تست بازرسی اولتراسونیک
در حالی که روش های بازرسی اولتراسونیک سنتی بسیاری از نقایص ایمنی آزمایش هیدرواستاتیک پس از ساخت را برطرف می کند، محدودیت هایی نیز برای این فناوری وجود دارد. با استفاده از ابزارهای فراصوت معمولی، تشخیص عیوب ریز و پیچیده مانند ترک های هوک (Hook Cracks) دشوار است.
منظور از ترک هوک، نوعی ترک بسیار کوچک است که در راستای خط جوشکاری در خطوط لوله به وجود می آید. و اگر به اندازۀ کافی بزرگ و قدرتمند شود، به سطح لوله راه پیدا می کند. این ترک ها معمولا با آخال هایی از جنس اکسیدهای غیرفلزی همراه هستند.
این مشکل بازرسی التراسونیک، به دلیل اصول عملکرد تجهیزات بازرسی قدیمی به وجود می آید. در نسل های قبلی فناوری اولتراسونیک، سیگنال های موج فراصوت با یک زاویۀ خاص ساطع می شدند. این امر باعث می شود ترک هایی که در جهت گیری های مختلف رشد کرده اند، قابل ردیابی نباشند.
بازرسی فراصوتی (تست التراسونیک UT)
در تست التراسونیک UT، امواج فراصوتی با دامنه بین ۵ تا ۲۵ مگاهرتز، توسط یک مولد ص...با این حال، برخی از ارائه دهندگان فناوری التراسونیک (مانند NDT Global) فناوری های مناسبی تولید کرده اند که قادر به رفع کمبود تکنیک های مرسوم بازرسی التراسونیک است.
به عنوان مثال، دستگاه NDT Eclipse UCx، از آرایش سنسوری استفاده می کند که بینش عمیق تری در مورد نقص های خاص و کوچک ارائه می دهد. برخلاف ابزارهای بازرسی درون خطی معمولی التراسونیک که فقط از یک سیگنال استفاده می کنند، Eclipse UCx دو سیگنال منتشر می کند که به طور هماهنگ برای ثبت اطلاعات عیوب کار می کنند.
وقتی ربات این دستگاه در طول خط لوله حرکت می کند، سیگنال دوگانه با مواد تشکیل دهندۀ لوله ارتباط برقرار می کند. با برخورد به یک عیب، یک سیگنال به سنسور «A» برمی گردد. در حالی که قسمتی از سیگنال که به مانع برخورد نکرده است، همچنان از طریق ماده حرکت می کند و در سنسور «B» رهگیری می شود.
این ترتیب خاص، امکان جمع آوری اطلاعات دقیق بدون توجه به جهت ترک را فراهم می کند. واضح است که فناوری های ILI (مانند Eclipse UCx) می توانند به عنوان جایگزینی ایمن و اقتصادی برای آزمون هیدرواستاتیک پس از ساخت استفاده شوند.
جمع بندی
هر عملیاتی که سازه ای را تحت فشار قرار دهد ذاتاً خطرناک است. تخلیۀ ناگهانی و ناخواستۀ انرژی ذخیره شده، می تواند پارگی های شدیدی ایجاد کند که ترکش های پر سرعتی را آزاد می کند. علاوه بر این، تحت فشار قرار دادن لوله می تواند منجر به تشکیل نقص های جدیدی شود. فناوری های ILI راه حلی را در اختیار مدیران خط لوله قرار می دهد که می تواند جایگزین روش های آزمون فشار مخرب شود. با حذف دو مولفۀ اصلی تخریب یعنی آب و فشار، اپراتورها می توانند طول عمر خطوط لولۀ خود را افزایش داده و به اهداف خود در راستای مدیریت یکپارچگی لوله نیز برسند.
منابع
دیدگاه کاربران
سلام، اگر مقاله با عکس و فیلم و توضیحات بیشتر همراه بود خیلی بهتر می شد.
با سپاس فراوان