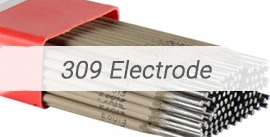
تکنولوژی آهنگری (Forging) – قسمت اول
این مقاله در 2 بخش تهیه شده است. در قسمت اول به معرفی روش آهنگری، جذابیت های این روش و نکات مربوط با قالب های فورج می پردازیم و در بخش دوم، انواع روش های فورج را از جنبه های مختلف معرفی خواهیم کرد.
“تکنولوژی” آهنگری چیست؟
به تکنولوژی ساخت یک قطعه فلزی با شکل دادن آن از طریق نیروهای فشاری موضعی، آهنگری یا فورج می گویند. این نیروهای فشاری معمولا از طریق چکش یا قالب به قطعه وارد می شوند. به طور کلی می توان گفت در آهنگری، هندسه يک قطعه ساده با استفاده از تغییر شکل مومسان، به یک هندسه پيچيده تبديل می شود.
فرآیند آهنگری می تواند قطعاتی با خواص مکانیکی عالی با ضایعات پایین تولید کند. چرا که با تغییر شکل فلز اولیه به شکل هندسی دیگر، مقاومت خستگی و استحکام قطعه تا حدود زیادی افزایش می یابد. این فرآیند به لحاظ اقتصادی نیز حرف های زیادی برای گفتن دارد. چرا که با توانایی تولید انبوه قطعات و دستیابی به خواص مکانیکی منحصر به فرد در محصول تمام شده، روشی مقرون به صرفه به نظر می رسد.
تنوع وزن و جنس قطعات آهنگری شده بالا است. به گونه ای که قطعات فورج شده می توانند وزنی کمتر از 1 کیلوگرم تا صدها تن داشته باشند! همچنین فلزات و آلیاژهای آهنی و غیرآهنی مختلفی مانند آلومینیوم، مس، برنج، فولادهای کربنی و آلیاژی مانند فولادهای زنگ نزن، ابزار و … می توانند تحت این عملیات قرار بگیرند.
جذابیت آهنگری در چیست؟!
به طور کلی قابلیت فورج در تولید قطعاتی مستحکم و با کیفیت بالا است. قطعاتی که در بسیاری از مواردی استحکام بیشتری نسبت به سایر روش های تولید مانند ریخته گری یا متالورژی پودر دارند. هنگامی که فلز در طول فرایند فورج شکل می گیرد، دانه بندی داخلی آن تغییر شکل می دهد تا به بافت مد نظر برسد. در نتیجه تغییر دانه بندی در سراسر قطعه، خواص مکانیکی آن تا حدود زیادی بهبود می یابد.
علاوه بر این، با استفاده از این روش می توان در بسیاری از هزینه ها نسبت به فرایند ریخته گری صرفه جویی کرد. بخشی از صنعتگران بر این باورند که شاید ریخته گری از لحاظ صرفه های اقتصادی کوتاه مدت، جذاب تر به نظر برسد؛ اما روش آهنگری در بلند مدت صرفه بیشتری خواهد داشت. این ادعا با در نظر گرفتن چرخه عمر محصول و کیفیت نهایی محصولات آهنگری شده ارائه شده است.
ریخته گری چیست؟ انواع و روش های ریخته گری
ریخته گری (casting) یکی از فرآیند های تولید است که طی آن یک ماده مذاب درون یک قا...با این حال آهنگری به تجهيزات نسبتاً گران قیمتی نياز دارد. در نتيجه، بخش دیگری از صنعتگران عقیده دارند اين فرآيند زمانی از نظر اقتصادی جذاب است كه هدف، تولید تعداد زيادی از قطعات باشد يا این که خواص مكانيكی مورد نياز در محصول نهايی را بتوان با یک یا دو کورس فورج به دست آورد. بنابراین اقتصادی بودن را باید با در نظر گرفتن جزئیات هر مورد خاص، بررسی کرد.
روش های آهنگری معمولاً ضايعات كمی دارند يا بدون ضايعات هستند و می توانند هندسه قطعه نهایی را در مدت زمانی کوتاه در یک یا چند کورس پرس یا چکش ایجاد کنند. از آن جا این قطعات به ابعاد مورد نظر سازندگان بسیار نزدیک هستند، بنابراین نياز به براده برداری و ماشین کاری به شدت کاهش می یابد كه این صرفه جویی زیادی را در مصرف ماده و انرژی به دنبال خواهد داشت.
قدمت آهنگری به چه دورانی باز می گردد؟
فورج یا آهنگری چند هزار سال است که توسط آهنگران اجرا می شود. در ابتدا، برنز و مس مشهورترین فلزات آهنگری شده در عصر برنز بودند. با پی بردن به قدرت آب و نقش آن در اعمال نیرو، در قرن 12 میلادی از چکش های هیدرولیکی بزرگتری برای اعمال فشار به فلزات استفاده شد. این موضوع سبب شد تا بتوان قطعات بزرگتری را با این روش تولید کرد.
بعدها که متالورژها قابلیت کنترل دما و پارامترهای فرایند ذوبِ آهن را کشف کردند، آهن به فلز اصلی آهنگری تبدیل شد. در آن دوران، محصولات مختلفی از لوازم آشپزخانه، سخت افزارها و ابزارهای دستی و انواع سلاح ها با این روش تولید می شدند.
با گذشت زمان، انقلاب صنعتی سبب شد آهنگری به فرایندی پربازده تر با قابلیت تولید انبوه تبدیل شود. امروزه برای برآورده کردن نیازهای متغیر صنعت مدرن، آهنگری نیز پیشرفت چشمگیری داشته است.
این روش شکل دهی هم در تجهیزات و طراحی، هم در روند اتوماتیک شدن و ایجاد قابلیت کنترل الکترونیکی تکامل زیادی داشته است. در عصر حاضر، فورجینگ صنعتی با فشار حاصل از چکش های مدرن و ابزار پرس پیشرفته ای انجام می شود که نیروی آن ها توسط هوای فشرده، الکتریسیته، هیدرولیک یا بخار تامین می شود.
یک استراتژی کلی برای فورج فلزات!
آهنگری روش های زیادی دارد که با توجه به نیاز به نوع محصول مورد و نیازی که باید برآورده کند، متفاوت است. با این حال شکل دهی به روش فورج، از یک سری طرح و اصول کلی پیروی می کند:
طراحی و انتخاب ابزار
فورجینگ به استفاده از قالب برای فشرده سازی و شکل دهی فلزات متکی است. پس مهم است که مشخص شود کدام مجموعه ابزار برای رسیدن به شکل مورد نظر بیشترین کارایی را خواهند داشت. در بسیاری از موارد، برای اطمینان از این که محصول نهایی دقیقا مطابق با انتظارات تولید شود، قالب باید سفارشی طراحی شود. به طوری که برای تولید در مقیاس بزرگتر، این مرحله ممکن است شامل طراحی و تولید چندین ابزار برای مسطح سازی، شکل دهی و یا برشکاری باشد.
شکل دهی به روش های مختلف
در این نقطه، روش های مختلف آهنگری از هم تجزیه می شوند. بسته به فرآیند انتخاب شده، بیلت یا شمش ممکن است گرم شده و بین دو قالب پرس شود یا این که وارد یک حفره قالب بسته شده و فشرده شود. در برخی موارد، اپراتور شمش را در دمای اتاق به صورت دستی و با چکش شکل می دهد که همان آهنگری کلاسیک است.
عملیات ثانویه
در برخی مواقع، پس از شکل دهی نیاز به انجام یک سری عملیات نهایی بر روی محصول است. از عملیات حرارتی های مختلف گرفته تا دیگر تمهیداتی که برای کاهش عیوب قطعات آهنگری و قالب ها اندیشیده می شوند.
عملیات حرارتی فلزات و کاربردهای آن
فرآیند عملیات حرارتی روی فلزات در مقیاس صنعتی به منظور بهبود خواص کلی فلزات برای...از جمله عیوبی که در قالب ها به وجود می آیند و نیاز به تعمیر و نگه داری آن ها است می توان به سایش، فرسایش، خستگی حرارتی و مکانیکی و تغییر شکل های ناخواسته اشاره کرد.
از جمله مهم ترین عیوبی که در قطعات اتفاق می افتند نیز می توان به ترک های سطحی، گوشه های تیز و خمیده، روی هم افتادگی (Overlap) و عیوب ساختاری مانند عیب در دانه بندی قطعات اشاره کرد.
نکاتی مهم جهت طراحی قالب های فورج
طراحی قالب های فورج به دانش گسترده ای از خواص مواد مهندسی نیاز دارد. خواصی مانند استحکام، چکش خواری، حساسیت به نرخ تغییر شکل و دما، خواص اصطکاکی، شکل قطعه و … علاوه بر این، باید توجه کرد که اعوجاج قالب تحت نیروهای بالا خصوصا در تولید قطعات با تلرانس ابعادی کم قابل توجه خواهد بود.
تلرانس چیست؟ (Tolerance) همه چیز درباره تلورانس
رسیدن به اندازه های دقیق در صنعت ممکن نیست! این واقعیت تلخ اما عادی، با توجه به ...بنابراین مهمترین قانون در طراحی قالب این است که قطعه در هنگام عملیات فورج در جهتی جریان یابد که هم برای قالب و هم برای خواص قطعه بهترین اثرگذاری را داشته باشد.
قالب باید به گونه ای طراحی شود که لغزش های شدید بین قطعه و قالب برطرف شوند تا فرسایش به حداقل برسد. علاوه بر این …
- بدیهی است انتخاب و طراحی شکل قالب نیازمند تجربه زیادی است. محاسبات سطوح مقطع در هر موقعیتی از قالب فورج باید با بالاترین دقت انجام بگیرد. چرا که فلز در این فرایند ممکن است تحت تغییر شکل های مختلفی در مناطق مختلف حفره های قالب قرار بگیرد. در این راستا باید به این نکته توجه داشت که خواص مکانیکی قطعه نهایی وابستگی زیادی به موقعیت فورج دارد.
- در اغلب قطعات فورج شده، خط جدایش یا Parting line درست در موقعیت بزرگترین سطح مقطع قطعه قرار می گیرد. در قطعاتی که متقارن هستند، این خط جدایش عمدتا یک خط مستقیم در مرکز قطعه است. اما در قطعات پیچیده این خط در یک صفحه قرار ندارد. این قالب ها باید به صورتی طراحی شوند که هنگام کار با ثبات باشند و قفل شوند. یعنی قالب در جهت محورهای عرضی حرکتی نداشته باشد. در این حالت تعادل نیروها و هم محوری قطعات قالب حفظ می شود.
- وجود یک سیمراهه (Gutter) در قالب فورج ضروری است. چرا که پس از پر شدن قالب، باید به مواد اضافی اجازه داده شود که به داخل سیمراهه راه پیدا کنند. این موضوع باعث می شود که این مواد اضافی سبب افزایش فشار قالب نشوند.
- توجه به پارامترهای قالب مانند زاویه شیب (Draft angle)، زوایای داخلی و خارجی، اندازه شعاع ها، گوشه ها و… بسیار مهم است. پژوهش ها نشان می دهند که معمولا شعاع های کوچک برای قالب مطلوب نیستند. چرا که سبب دشواری جریان فلز می شوند. به علاوه سبب تمرکز تنش و حرارت شده و فرسایش قالب را به دنبال خواهند داشت.
- قوس های کوچک قالب باعث ایجاد ترک های خستگی می شود. از این رو مقدار این قوس ها تا جایی که طراحی قطعه فورج اجازه می دهد، باید بزرگ باشد.
- در فرایند آهنگری، خصوصا برای قطعات پیچیده می توان از قالب های چندتکه به جای قالب های یک تکه استفاده کرد. این استراتژی سبب کاهش هزینه های ساخت در مقایسه با ساخت قالب های یک تکه پیچیده می شود.
چه مولفه هایی بر طراحی قالب های فورج تاثیرگذار هستند؟
عملیات آهنگری معمولا در دماهای بالایی اجرا می شود. به خصوص برای قطعاتی که دارای ابعاد بزرگی باشند. از این رو مواد قالب بایستی دارای استحکام و چقرمگی مورد نیاز را در این دماها داشته باشند. ضمن این که این قطعات بایستی سختی پذیری بالایی داشته و قابلیت سخت کاری به صورت یکنواخت را داشته باشند.
مواد قالب (مخصوصا فورج داغ) باید در برابر شوک های حرارتی و مکانیکی مقاوم باشند و مقاومت به خستگی بالایی داشته باشند. نکته مهم دیگر مقاومت در برابر سایش است. چرا که باید از پدیده پوسته شدن در فورج داغ جلوگیری کرد.
بدیهی است که روانکارها نیز شدیدا بر میزان اصطکاک و سایش میان قطعه و قالب تاثیرگذار هستند. این مواد نقش مهمی در میزان نیروهای اعمالی و جریان یافتن فلز به داخل حفره ها ایفا می کنند. از طرف دیگر، این مواد به عنوان عامل جدایش، از چسبیدن قطعه به قالب جلوگیری می کنند. در فورج داغ معمولا از روانکار گرافیتی و دی سولفید مولیبدن (MoS2) استفاده می شود.
مشخصا انتخاب جنس قالب به فاکتورهایی مانند نرخ انتقال حرارت از قطعه به قالب، ابعاد قالب، ترکیب و خواص قطعه، پیچیده بودن قطعه، دمای فورج، نوع فرایند، هزینه مواد قالب و تیراژ قطعه بستگی دارد.
برای ساخت قالب های فورج داغ از فولاد ابزارهای کارگرم (سری H AISI)، فولادهای آلیاژی مانند AISI سری 4300 یا 4100 و برخی فولادهای کم آلیاژ استفاده می شود. برای اطلاعات تکمیلی در این باره می توانید به هندبوک ASM جلد ۱۴ شکل دهی و فورج کاری که در همین سایت جهت استفاده قرار داده شده است، مراجعه نمایید.
جهت دانلود کتاب بر روی تصویر کلیک کنید.
در قسمت دوم این مقاله، شما را با تقسیم بندی روش های آهنگری از منظرهای مختلف و موارد استفاده از آن ها آشنا خواهیم کرد.
منابع
ASM Handbook-Volume 14- Forming and forging
www.en.wikipedia.org
www.reliance-foundry.com
www.cornellforge.com
دانلود فقط با IP ایران امکانپذیر است. در صورت عدم مشاهده باکس قرمز رنگ دانلود، VPN خود را خاموش نموده و صفحه را رفرش کنید.
پسورد فایل فشرده : www.iran-mavad.com
دیدگاه کاربران
یک سوال کسی بخواهد اهنگری را یاد بگیرد باید چه رشته ای را بخوند و یا کجا دوره ببیند؟
سلام
برای دیدن و آشنایی با شرکت های فورج سازی یا کارآموزی میتونید با شرکت های ، فورج آهنگری تراکتورسازی ( شهر تبریز در مجموعه تراکتور سازی ) شرکت پارت سازن و فورج مشهد ( هر دو در شهر مشهد ) شرکت رافکو ( شهر خمین ) شرکت فورج البرز ( نرسیده به نیروگاه شهید رجایی قزوین ) و …. هماهنگ و از نزدیک با پروسه ها آشنا شید .
سازمان فنی و حرفه ای باید داشته باشد.