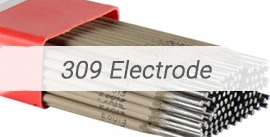
ریخته گری گریز از مرکز (بخش اول)
نیروی گریز از مرکز چیست؟
به نیرویی که به سمت بیرون، بر یک جسم در حال دوران وارد می شود، نیروی گریز از مرکز یا مرکز گریزی (Centrifugal Force) گفته می شود. منشاء این نیرو همین حرکت دورانی است. همۀ ما این کمیت را وقتی که شیئی در مسیری منحنی یا پیچ دار حرکت می کند، دیده ایم.
جالب است بدانید دلیل چرخش سیارات به دور خورشید، بدون آن که روی خورشید سقوط کنند، برابر بودن نیروی گریز از مرکز با نیروی گرانش خورشید است. البته فیزیک دانان معتقدند نیرویی حقیقی به نام نیروی گریز از مرکز، وجود حقیقی ندارد!
بلکه علت گریز جسم از مرکز در حرکت دورانی، اینرسی (Inertia) خود جسم است. مانند زمانی که در لحظۀ حرکت ناگهانی خودرو به جلو، ابتدا به عقب پرتاب می شویم. این به عقب پرتاب شدن به دلیل اینرسی بدن ماست (اینرسی را می توان تمایل جسم برای حفظ حالت قبلی تعریف کرد).
ریخته گری گریز از مرکز چیست؟
فرایند ریخته گری گریز از مرکز به روشی گفته می شود که در آن قالب تحت تاثیر نیروی گریز از مرکز پر می شود. به دلیل وجود چرخش در این روش، به آن ریخته گری سانتریفیوژ (Centrifugal Casting) هم می گویند.
در اکثر روش های ریخته گری، قطعۀ در حال شکل گیری در قالبی ثابت منجمد می شود. اما در ریخته گری سانتریفیوژ از یک قالب چرخنده برای شکل دهی قطعۀ نهایی استفاده می شود.
اکثر پروفیل های لوله ای شکل که به این روش تولید می شوند، دارای مقاطعی دایروی هستند. اما در مواردی دیده شده که از این روش برای تولید پروفیل های ششگوش و متقارن نیز استفاده شده است.
در دهۀ اخیر، استفاده ریخته گری گریز از مرکز با اعمال خلاء بهبود زیادی یافته است. اعمال خلاء برای جلوگيری از اكسيداسيون (Oxidation) و آلودگی مذاب و برای كمک به پر شدن سريع تر قالب انجام می گیرد.
تاریخچۀ ریخته گری گریز از مرکز
طرح استفاده از نیروی گریز از مرکز برای ریخته گری در سال 1809 میلادی، توسط فردی انگلیسی به نام «آنتونی ایچارد» ارائه شد. اما اولین استفادۀ صنعتی از آن در سال 1848 میلادی در بالتیمور به منظور تولید لوله چدنی انجام گرفت.
همگام با پیشرفت چشمگیر علم و صنعت از سال 1890 میلادی، پیشرفت هایی در روش ریختهگری گریز از مرکز هم شکل گرفت که در سال های 1912 تا 1918 میلادی، منجر به ساخت ماشین «د لاوود» برزیلی گردید. این ماشین در ادامه به شکل دستگاه ریخته گری امروزی در آمد
ماشین ریخته گری سانترفیوژ در یک نگاه
اصول روش ریخته گری گریز از مرکز
در آغاز فرایند، فلز مذاب به درون قالب چرخنده (دوار) ریخته می شود. از آنجایی که قالب در حال چرخش است، نیروی گریز از مرکز به فلز مذاب وارد می شود. بنابراین مذاب به سمت بیرونی قالب متمایل می شود و به دیواره ها هجوم می برد.
از این لحظه فرایند انجماد و جوانه زنی کریستال های جامد از دیوارهٔ قالب شروع می شود. در واقع نیروی گریز از مرکز با راندن مذاب به سمت دیوارۀ قالب، سبب شکل دهی فلز به صورت حلقوی می شود. لازم به ذکر است که در ریخته گری گریز از مرکز، از هیچ گونه ماهیچۀ داخلی برای شکل دهی به مذاب استفاده نمی شود.
همچنین برای این روش ریخته گری هیچ نیازی به سیستم راهگاهی هم نیست. ضخامت نهایی دیواره تولیدی، تابعی از حجم مذاب اولیهٔ ورودی است. در این روش ریخته گری به دلیل عمل چرخش و اختلاف چگالی بین ناخالصی ها و مذاب فلز اصلی مورد نظر، ناخالصی ها معمولا روی سطح لوله جمع می شوند و به سادگی با عملیات ماشین کاری (Machining) قابل حذف هستند.
ریخته گری لوله های ضخامت بالا
در فرایند ریخته گری گریز از مرکز برای تولید لوله هایی با ضخامت بالا، لازم است فرایند انجماد از هر دو سو انجام گیرد. یعنی هم از سمت درون لوله به بیرون آن و هم از سمت بیرون به سمت درون. در این حالت احتمال به وجود آمدن مُک افزایش می یابد. بنابراین لازم است سطح قالب پیش گرم شود، تا انجماد از سمت درونی به بیرونی قطعه نیز انجام گیرد.
ابعاد قطعات تولیدی و تلورانس
محدودهٔ ضخامت برای ریخته گری گریز از مرکز به طور معمول، بین ۲٫۵ میلی متر تا 12.5 سانتی متر است که معادل است با محدودهٔ ۰٫۱ تا ۵ اینچ. قطر لوله های تولیدی با این روش نیز معمولاً بین ۳ تا ۱۵ متر است (معادل با ۱۰ تا ۵۰ فوت).
میزان تلورانس برای قطر داخلی و خارجی قطعات تولیدی با این روش متفاوت است. تلورانس برای قطر خارجی در حدود ۲٫۵ میلیمتر (معادل ۰٫۱اینچ) و برای قطر داخلی در حدود ۴ میلی متر (معادل ۰٫۱۵ اینچ) است. البته با توجه به ریزه کاری های طراحی، این ابعاد و تلورانس مذکور ممکن است دستخوش تغییر قرار گیرند.
مواد معمول برای ریخته گری
تمام فلزاتی که قابلیت ریختگی داشته باشند را با این روش می توان ریخته گری کرد. اما معمولا برای فلزاتی مانند انواع چدن، انواع فولاد (مخصوصا فولاد ضد زنگ)، انواع آلیاژهای آلومینیوم، مس، منیزیوم و نیکل کاربرد دارد.
البته به غیر از فلزات، این روش برای انواع شیشه و بتن نیز قابل اجراست. به طور کلی هر ماده مهندسی که قابلیت ذوب داشته باشد، با این روش ریخته گری می شود.
عوامل موثر در ریخته گری سانتریفیوژ
سرعت بارریزی
سرعت بارریزی مذاب در ریخته گری گریز از مرکز باید بهینه باشد. یعنی لازم است اپراتور میزان حداقل سرعتی که منجر به تولید قطعات سالم می شود را با تجربه به دست آورد. اگر سرعت بارریزی از حالت بهینه کمتر باشد، باعث عیوبی مانند پر نشدن و سرد جوشی می شود و اگر بیشتر باشد زمان انجماد بیشتر می شود. زمان طولانی انجماد سبب ایجاد ترک های طولی (Longitudinal cracks) می شود.
دمای بارریزی
میزان دمای فوق ذوبی که برای ریخته گری گریز از مرکز انتخاب می شود، بستگی به شکل، ابعاد و جنس محصول دارد. افزایش حساب نشده فوق ذوب باعث کم شدن قدرت تبریدی قالب و افزایش زمان انجماد می شود.
البته به دنبال آن پدیدۀ جدایش (Segregation) و درشت دانه گی نیز ایجاد می شود. همچنین می تواند باعث ریزش مذاب در اثر سرد نشدن آن در سطح قالب و لغزش مذاب به دلیل منجمد نشدن مذاب در هنگام رسیدن به هم نیز بشود.
دمای قالب
بدیهی است که افزایش دمای قالب باعث انبساط حرارتی قالب می شود. این اثر انبساطی باعث افزایش فاصله هوایی و نیز بیشتر شدن زمان انجماد می شود. کاهش دمای قالب نیز باعث کاهش میزان انبساط شده و سبب اعمال نیروهای انقباضی به قطعه می شود. نیروهای انقباضی نیز عامل اصلی ایجاد ترک هستند. دمای بهینۀ قالب بین 150 تا 200 درجۀ سلسیوس است.
مزایای ریخته گری سانتریفیوژ
- امکان تولید تعداد قابل توجهی از اجزای استوانهای شکل با سرعت مطلوب
- دقت ابعادی مناسب
- کاهش استفاده از ماهیچه گذاری و ایجاد راهگاه برای ریختهگری
- خواص مکانیکی مناسب قطعۀ نهایی
- تولید قطعاتی با مقاومت به خوردگی بسیار بالا به دلیل شکل گیری خوب دانه بندی در سطح خارجی قطعه
- امکان ریخته گری فلزات با وزن مخصوص بالا
- اپراتوری بسیار ساده به دلیل وجود بخش کنترل کامل الکترونیک
- سرعت بالای انجماد در مقایسه با سایر روش ها
- عدم ایجاد آلودگی در محیط زیست
معایب ریخته گری سانتریفیوژ
- عدم قابلیت تولید اشکال هندسی پیچیده
- استعداد ایجاد تفکیک و جدایش در مناطق مختلف قطعه
- لزوم روغن کاری روزانۀ اجزای دستگاه
- مصرف انرژی نسبتا بالا برای تولید قطعات حجیم و سنگین
در پایان این مطلب، توجه شما را به فیلم آموزشی کوتاهی که در خصوص ریخته گری سانتریفیوژ آماده شده، جلب می کنیم.
برای مطالعه انواع روش های ریخته گری گریز از مرکز، کاربردهای این روش و انواع عیوب ریخته گری، بخش دوم این مقاله را مطالعه کنید.
منبع
حجازی، جلال ؛ دولمی، پرویز ؛ نظم دار شهری، سیاوش ؛ عسگر زاده، علی اکبر ؛ درس فنی سال های سوم و چهارم ؛ (1369) ؛ شرکت چاپ و نشر ایران ؛ کرج
جامعه ریخته گران ایران ؛ تحلیل علمی و آماری ؛ جامعه ریخته گران ؛ تهران
دوامی، پرویز ؛ حجازی، جلال ؛ اطلس عیوب ریخته گری ؛ جامعه ریخته گران ایران.
دیدگاه کاربران
سلام . خیلی بده سایت مهندسی مواد فولاد زنگ نزن بنویسه فولاد ضد زنگ. انتظار ما از شما خیلی بالاتره!
سلام . عبارت صحیح تر، فولاد زنگ نزن هست اما با توجه به این که در صنعت و عموم، استفاده از فولاد ضد زنگ هم بسیار رایج هست، گاهی استفاده شده.
آیا شما میتوانید فسبور برنز را به آهن به چسبانید ؟
سلام دوست عزیز
منظورتان رو دقیق متوجه نشدم
لطف کنین دقیق تر سوالتون رو مطرح کنین