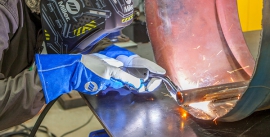
جوشکاری زیر پودری (SAW)
منظور از جوشکاری زیر پودری چیست؟
فرایند جوشکاری زیر پودری فرایندی است که در آن قوس الکتریکی زیر پوششی از پودر روانساز مخفی است. بنابراین برخلاف جوشکاری SMAW که سیم جوش به مواد سرباره ساز متصل بود، در SAW الکترود از مواد سرباره ساز یا روان ساز (پودر جوش) جدا است. این فرایند از روش های جوشکاری قوسی است؛ یعنی گرمای لازم برای جوشکاری توسط قوس بین الکترود مصرفی و قطعه کار تامین می شود.
محافظت در این فرایند به عهدۀ پودری است که به وسیلۀ یک مجرا از داخل مخزن نگهدارنده به سطح قطعه كار هدايت می شود. از آنجا که در این فرایند قوس الکتریکی مخفی است، می توان از شدت جریان های بالا (حتی تا 2500 آمپر) نیز استفاده کرد. این فرایند جوشکاری، یکی از موفق ترین راه حل های اتوماتیک کردن جوشکاری محسوب می شود. جوشکاری زیر پودری میتواند به ۳ روش نیمه خودکار، خودکار و ماشینی انجام گیرد.
جوشکاری زیرپودری به چه صورتی انجام میشود؟
برای اعمال جوش SAW ابتدا جریان الکتریکی از یک ژنراتور (ترانسفورماتور یا رکتی فایر) تامین می شود. این جریان قوسی را بین الکترود و فلز پایه بر قرار می کند تا حوضچۀ مذاب را برای پرکردن اتصال تشکیل دهد. در جوشکاری SAW ، حوضچۀ مذاب جوش، ترکیبی از فلاکس (پودر) مذاب و فلز جوش مذاب است.
جریان الکتریکی پس از اعمال قوس از این منطقه می گذرد. فلاکس مذاب معمولا هادی خوب جریان الکتریسته است، در حالی که فلاکس سرد رسانا نیست. برای ادامه یافتن جوشکاری، غلتک های هدایت با نیروی مکانیکی، به طور پیوسته سیم الکترود مصرفی فلزی را از میان لوله تماس (نازل) و توده فلاکس به اتصالی که باید جوش داده شود، می راند.
سیم جوش (الکترود) در منطقه جوش ذوب شده و در طول اتصال رسوب می کند. فلاکس پودری در جلوی قوس ریخته شده و پس از انجماد فلز جوش، فلاکس ذوب نشده توسط سیستم مکش جمع کننده برای استفاده مجدد جمع آوری می گردد.
در برخی کاربردهای خاص دو یا چند الکترود به صورت متوالی در یک اتصال تغذیه می شوند. این الکترودها ممکن است کنار یکدیگر بوده و به یک حوضچه تغذیه شوند یا اینکه به اندازۀ کافی فاصله داشته باشند تا پس از انجماد یکی، حوضچۀ دیگری شروع به تشکیل کند و در واقع به شکل مستقل منجمد شوند.
متغیرهای اصلی جوشکاری SAW
جریان الکتریکی (شدت، نوع و قطبیت)
شدت جریان جوشکاری زیر پودری بر روی جوش دو اثر کمی و کیفی دارد. منظور از اثر کمی عمق جوش است و اثر کیفی نیز همان میزان حرارت داده شده به جوش است. برای جوشکاری SAW عمدتا از جریان با قطبیت معکوس (DCEP) استفاده می گردد؛ چون در این حالت بازیابی عناصر الکترود بیشتر است و اکسیداسیون کمتری اتفاق می افتد. در صورتی که به عمق جوش بیشتری نیاز باشد، از جریان با قطبیت مستقیم (DCEN) استفاده می شود.
ولتاژ
معمولا تأثیرات ولتاژ روی پهنای جوش و حجم ذوب شدن است. همچنین ولتاژ تأثیر کمی در حرارت داده شده به جوش دارد. هرچه ولتاژ بیشتر شود، پهنای جوش نیز بیشتر خواهد شد. در ولتاژهای بالا، جرقه و ترشح جوش زیاد بوده و تمایل به جذب نیتروژن از هوا در جوش افزایش می یابد که نتیجۀ آن ایجاد حباب یا خلل و فرج در جوش است. همچنین سبب می شود گردۀ جوش شکل مناسبی نداشته باشد.
در مقابل، ولتاژ کم باعث افزایش اندازۀ قطرات مذاب در نوک الکترود می شود. همچنین احتمال ایجاد مدار بستۀ متناوب با کاهش ولتاژ؛ بالا میرود. در مواردی نیز گزارش شده است که ولتاژ کم، گردۀ جوش نامنظم و بدون نفوذ کافی تولید می کند و تمایل به حبس سرباره در جوش را افزایش می دهد.
همان طور که ذکر شد، ولتاژ روی حرارت ورودی نیز تأثیرگذار است و از این جهت شرایط گرم و سرد شدن جوش را می تواند تغییر دهد. در نتیجه ساختار و خواص مهندسی جوش نیز دستخوش تغییر قرار خواهد گرفت. هرچه ولتاژ بیشتر شود، به دلیل افزایش طول قوس، قسمت عمدۀ قوس بالای سطح نمونه خواهد بود. در نتیجه پودر جوش بیشتری ذوب می شود و سطح جوش بیشتر شده و صاف تر می شود.
سرعت جوشکاری
هرچه سرعت جوشکاری بیشتر باشد، زمان جوشکاری کوتاه تر خواهد شد. بنابراین حرارت ورودی نیز کمتر می شود و حجم جوش (هم پهنا، هم عمق جوش) کمتر خواهد بود. به عبارت دیگر، سرعت زیاد باعث ایجاد گردۀ جوش لاغر می گردد. همچنین حوضچۀ جوش، حاصل از ذوب الکترود همراه با ذوب سطحی قطعه کار خواهد بود.
در این حالت موضوع برجسته شدن گرده جوش نیز مطرح است. البته پارامتر سرعت، بیشتر روی پهنای جوش اثر دارد تا روی عمق آن. با افزایش سرعت، حرارت کمتری در قطعه توسط مکانیزم هدایت به هدر می رود. از این جهت در سرعت بیشتر، بازدهی حرارت نیز بیشتر است.
سیم جوش
می دانیم ترکیب شیمیایی جوش، آمیزه ای از ترکیب قطعه کار و سیم جوش است. با تغییر نوع سیم جوش، ترکیب فلز جوش و در نهایت خواص مهندسی آن نیز تغییر می کند. شکل مقطع سیم جوش نیز مهم است. چرا که جوش حاصل از سیم جوش با مقطع گرد، پهنای جوش کمتر و عمق نفوذ بیشتری نسبت به نوع تسمه ای دارد.
اگر سطح مقطع الکترود گرد باشد، با کاهش قطر آن ، چگالی جریان و عمق نفوذ جوش بیشتر خواهد شد. زاویه و میزان راندن سیم جوش نیز دیگر پارامترهای مربوط به سیم جوش است که باید در مراحل طراحی جوشکاری SAW مد نظر قرار گیرد.
طول مؤثر الکترود
فاصلۀ مکانی که جریان برق به سیم وصل می شود تا مکانی که سیم به سطح کار می رسد، طول مؤثر الکترود نام دارد. با افزایش این طول، مقاومت الکتریکی سیم زیاد شده و به دنبال آن حرارت تولیدی نیز افزایش می یابد. در نتیجه نرخ رسوب و ذوب نیز افزایش می یابد.
افزایش طول مؤثر سیم جوش، موجب کاهش نفوذ جوش نیز می شود. اگر طول مؤثر الکترود کم باشد، یعنی نازل بیش از اندازه پایین می آید و با حرکت نازل و جارو کردن پودر اطراف آن، در محافظت قوس توسط پودر خلل وارد می شود. همچنین نازل ممکن است به علت حرارت ذوب شود.
پودر فلاکس
یکی از پارامترهای مهم در مورد پودر جوش، عدد بازیسیتۀ آن است. هرچه عدد بازیسیته بیشتر باشد، یعنی ترکیبات قلیایی مثل CaO در آن بیشتر است و تصفیه مذاب بهتر انجام می شود. مهم ترین پودرهای مورد استفاده در جوشکاری زیر پودری عبارتند از:
- پودر سیلسکات منگنز(MS )
- پودر سیلیکات کلسیم ( CS)
- پودر سیلیکات زیرکونیوم (ZS)
- پودر سیلیکات روتیلی (RS)
- پودر آلومینات روتیلی (AR)
- پودر آلومینات قلیایی (AB )
- پودر آلومینات سیلیکات (AS )
- پودر قلیایی آلومینات فلوراید (AF)
- پودر فلورید قلیایی (FB)
- پودر آهن (IP)
سیستم طبقهبندی الکترودها و پودرها
احتمالا با مقاله مقاله تا بدین جا متوجه شدهاید که در جوشکاری SAW دو نوع مصالح برای پرکردن درز جوش وجود دارد: پودر و الکترود. مصالح پرکننده در جوشکاری قوسی زیر پودری تحت استاندارد ASW A5.17 برای فولاد کربنی و AWS A5.23 برای فلزات پرکننده کم آلیاژی قرار می گیرند. یعنی هم پودرها و هم الکترودها تحت این استاندارد قرار دارند. در شکل زیر به خوبی این نحوه نام گذاری را مشاهده میکنید.
نامگذاری پودر فلاکس
طبق تصویر بالا، حرف F نشان دهندۀ پودر (Flux) است. عدد ۷ نشانگر مقاومت کششی جوش با واحد Ksi است. حرف A نشان می دهد که جوش در حالت ساخته شده (As Built یا As Weld) تست شده است. عدد ۲ نشانگر زبری دندانهای ۲۰ ft-lb پودر در دمای ۲۰ درجه فارنهایت است.
نامگذاری الکترود
حرف اول یعنی E نشان دهندۀ الکترود است. حرف دوم ممکن است L، M و H باشد که به مقدار پایین، متوسط و زیاد منگنز در الکترود اشاره دارد. یک یا دو عدد بعدی به درصد کربن اسمی اشاره دارد. برای مثال عدد 13 نشان دهندۀ محتوای کربن اسمی در 0.13 درصد است. تاکید می کنیم که این مقدار اسمی است و ممکن است که با مقادیری مشخص در الکترود بالا یا پایین شود.
در برخی موارد، الکترود از فولاد کشته شده (Killed Steel) ساخته می شود. در این موارد، سیلیکون به فولاد اضافه شده است و الکترود دارای حرف K در پایان طبقهبندی است. امروزه برای ساخت الکترودهای جوشکاری SAW از مواد کامپوزیتی نیز استفاده می شود که در این حالت، حرف C بعد از E آورده می شود.
الکترود جوشکاری (سیم جوش) و انواع آن
در بسیاری از روش های جوشکاری، نمی توان با حرارت مستقیم، دو قطعه را به هم متصل کر...
انواع فلاکس در جوش SAW
فلاکس های به هم چسبانده شده (Bonded Flux)
برای تولید این نوع پودرها، ابتدا مواد اولیه کاملا خشک می شوند. سپس عملیات چسباندن اجزای پودری با کمک یک ترکیب با نقطه ذوب پایین مانند سیلیکات سدیم انجام می شود. اغلب فلاکس های باند شده دارای اکسید زداهای فلزی هستند. اکسید زداهای فلزی به جلوگیری از تخلخل جوش کمک می کنند.
فلاکس های زینتر شده (Agglomerated Flux)
تفاوت این پودر با نوع چسبانده شده، استفاده از مواد سرامیکی با درجه حرارت بالاتر است. به بیان دیگر موادی به ترکیبات پودر افزوده می شود که نقطۀ خمیری شدن پایین تری نسبت به مواد اصلی پودر دارند و ضمن حرارت دادن موجب چسباندن مواد اصلی می شوند.
فلاکس های پیش ذوب شده (Prefused Flux)
برای تولید این نوع پودرها ابتدا اجزا به صورت کامل مخلوط می شوند. سپس این مخلوط در یک کوره الکتریکی برای تشکیل یک محصول شیمیایی همگن ذوب می شوند. در نهایت با عملیات سرمایش خنک شده و خرد می شوند. عملیات خردایش تا رسیدن به اندازۀ ذرات مورد نیاز ادامه می یابد. از جذابیت های اصلی این نوع فلاکس ها ایجاد قوس نرم و پایدار در آمپراژ بالا و همچنین ایجاد خواص ثابت فلز جوش را می توان نام برد.
عیوب ایجاد شده در جوشکاری زیر پودری
گاهی در هنگام جوشکاری زیر پودری و یا پس از آن، مشکلاتی برای برای جوش به وجود میآید. این مشکلات عمدتاً به دلیل وجود آلودگی در منظقهی جوش یا خطا در انتخاب ناحیهی مناسب برای جوشکاری به وجود میآیند. در این بخش با برخی از مهمترین این مشکلات آشنا خواهیم شد.
ذوب ناقص و سربارۀ محبوس
این عیوب معمولا به دلیل اتصال نامناسب قطعات رخ میدهند. نامناسب بودن ناحیۀ جوش در قطعه ممکن است باعث شود فلز جوش بالاتر از سرباره غوطه ور شود. یعنی سرباره در زیر فلز جوش محبوس شود. اگر مهرۀ جوش دور از لبۀ اتصال قرار داشته باشد، فلز مذاب ممکن است فلز پایه را ذوب کند.
یکی از عوامل مهمی که سبب این عیب میشود، محدب بودن شکل مهره جوش است. این حالت باعث می شود که ولتاژ جوشکاری SAW کاهش یابد. در پی آن حتما سربارۀ محبوس به وجود می آید و ذوب ناقص اجازه نمی دهد که فلز مذاب به خوبی در ناحیۀ جوش پخش شود.
ترک انجمادی
ترک انجمادی معمولا در طول مرکز مهرۀ جوش به وجود می آید. علت آن شکل نامناسب مهره جوش، نادرست بودن طرح اتصال یا انتخاب نادرست روش جوشکاری است. مهرۀ جوش محدب با نسبت عمق به عرض بیشتر، از احتمال ترک انجمادی میکاهد.
در روش SAW اگر عمق نفوذ جوش خیلی زیاد باشد، تنش های انقباضی ممکن است ترک خط مرکزی را به وجود آورند. علت اصلی افزایش تنش های انقباضی، طرح اتصال است که خطر ترک انجمادی را افزایش می دهد.
ترک هیدروژنی
این ترک ها نیز مانند ترک های انجمادی، تقریبا بعد از انجام جوشکاری SAW ظاهر می شوند. ترک هیدروژنی زمانی به حداقل خواهد رسید که منبع هیدروژن (برای مثال آب، روغن، گازها و ناخالصی) در پودر الکترود یا محل اتصال وجود نداشته باشند.
لازم است پودر الکترود و قطعه کار حتما تمیز و خشک باشند. همچنین برای جلوگیری از ورود نم و رطوبت، پودرها و الکترودها باید در جعبه های مقاوم به رطوبت و در مکان های خشک انبار شوند. در اکثر موارد برای کاهش ترک هیدروژنی، پیشگرم کردن محل اتصال پیشنهاد می شود.
مُک
عیب مک به دلیل حبس شدن گازها در مذاب جوش به وجود می آید. حباب های گازی که سبب به وجود آمدن مک می شوند، در اثر عدم وجود محافظت کامل پودری در برابر اتمسفر حاصل می شوند. این عیوب همچنین میتوانند در اثر آلودگی به وسیلۀ آب، روغن یا گریس و دیگر ناخالصی ها ایجاد شوند.
برای کاهش مک در جوشکاری زیر پودری محل جوش باید به طور کامل به وسیله پودر فلاکس پوشش داده شود. همچنین آب، گریس و ناخالصی های سطحی کاملا باید از قطعه کار، الکترود و فلاکس پاک شوند. البته به وجود آمدن مک در جوش SAW علت دیگری نیز دارد.
سرعت بیش از اندازه جوشکاری نیز ممکن است باعث مک شود. افزایش سرعت حرکت اجازه نخواهد داد که حباب های گازی از جوش خارج شوند. به این ترتیب حباب ها ممکن است در فلز جوش در میان فلز و سرباره محبوس شوند.
مزایای جوشکاری SAW
- نرخ يا بازدهی رسوب بالا (سرعت توليد بالا)
- پيوسته بودن فرایند
- ایجاد حفاظت مناسب به کمک فلاکس و عدم حساسیت به باد
- قابلیت اتوماسیون فرایند (تاثير کم اپراتور روی کيفيت جوش)
- راندمان حرارتی بالای قوس (اتلاف کم)
- حرارت ورودی بالا و عمق نفوذ زياد (مناسب برای جوشکاری قطعات با ضخامت بالا)
معایب جوشکاری SAW
- تجهیزات پیچیده و گران
- عدم رویت جوش در هنگام جوشکاری
- وجود محدودیت در حالت جوشکاری (تخت و افقی)
- استعداد ایجاد خلل و فرج در جوش به دلیل حضور مواد ناخالصی در پودر
- مناسب نبودن برای جوشکاری قطعاتی با ضخامت کمتر از 5/4 میلی متر
- لزوم جمع آوری سرباره قبل از پاس بعدی
کاربردهای تکنیک SAW
با توجه به قابلیت اتوماسیون، سرعت بالا و عمق نفوذ بالای جوش SAW، از این روش میتوان برای ساخت سازههای بزرگ فلزی که نیاز به دقت بالایی دارند، استفاده کرد. در این بخش به سه مورد از کاربردهای این روش اشاره میکنیم.
ساخت مخازن تحت فشار به وسیله جوشکاری زیر پودری
در ساخت مخازن تحت فشار به روش جوشکاری، از روش های متعددی می توان استفاده کرد که جوش SAW از مهم ترین روش هاست. در این روش پس از رول کردن بدنهی مخزن و ساختن و نصب کلاهک آن، لازم است این بخش ها با جوشکاری زیر پودری به هم متصل شوند. در ابتدا نوع پودر و الکترود باید به طور دقیق با توجه به پارامترهای مختلف تعیین شوند. مهم ترین این پارامترها عبارتند از: متریال فلز پایه، نوع کاربری، میزان حساسیت در ساخت مخزن و وجود تجهیزات کارگاهی. اصول ساخت مخازن تحت فشار با جوشکاری SAW در استاندارد ASME sec VIII – Division1 تدوین شده است.
تولید لوله های درز دار با استفاده از جوشکاری زیر پودری
یکی از روش های قدیمی تولید لوله، روش U&O است. در این روش، به وسیلۀ قالب هایی ابتدا ورق را به شکل U و سپس O درمی آورند. شکل دهی ورق در حالت سرد انجام می شود. قبل از شکل دهی، لبه های ورق پخ زده می شوند و بعد از شکل دهی، به صورت درز مستقیم جوشکاری می شود.
لبه های درز لوله به هم فشرده شده و در ایستگاه پاس ریشه، ابتدا ریشۀ جوش با روش GMAW جوش داده می شود. سرعت جوشکاری در این مرحله بسته به ضخامت ورق، بین 5 تا 12 متر بر دقیقه است. بعد از ایستگاه GMAW ، لوله به ایستگاه جوش زیرپودری منتقل می شود.
در ایستگاه جوش زیر پودری ابتدا پاس داخل و سپس پاس خارج جوشکاری می شود. در پاس داخلی و خارجی، لوله متحرک بوده و دستگاه جوش ثابت است. در پاس داخلی دستگاه جوش توسط بازوهای متحرکی به داخل لوله رفته و جوشکاری را انجام می دهد. پر واضح است که پاس خارجی بعد از سرد شدن کامل پاس داخلی انجام می شود.
سخت کردن سطحی توسط جوشکاری زیر پودری
همان طور که ذکر شد، جوش SAW را می توان با سرعت حرکت و نرخ رسوب بالا روی سطوح صاف يا استوانه ای انجام داد. همچنین دیدیم که برای نوع پودر فلاکس و الکترود گسترۀ وسیعی از ترکیب وجود دارد. بنابراین می توان نتیجه گرفت اين روش برای سخت کردن سطحی نيز مناسب است. برای مثال می توان با استفاده از پودر و الکترود غنی از کربن روی سطح، سختی سطوح مورد نظر را تا حدود زیادی بالا برد.
در پایان توجه شما را به فیلم کوتاهی که در خصوص آموزش روش جوشکاری زیر پودری (SAW) تهیه شده، جلب می کنیم.
منابع
-Duane K. Miller, Sc.D., P.E. Steel design guide, welded connections, a primer for engineers. ASCE guide 21.
علیرضا شمس – پارامترهای موثر بر کیفیت جوش با روش زیرپودری
محمدحسین حلاج – جوشکاری زیرپودری
دانلود فقط با IP ایران امکانپذیر است. در صورت عدم مشاهده باکس قرمز رنگ دانلود، VPN خود را خاموش نموده و صفحه را رفرش کنید.
پسورد فایل فشرده : www.iran-mavad.com
دیدگاه کاربران
مطالب خوب و آموزنده بود
عالی بود