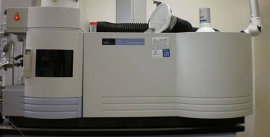
از خستگی در مواد چه می دانید؟
معرفی تست خستگی
آشنایی با پدیده خستگی و آنالیز آن از اهمیت خاصی برخوردار است چرا که قطعات زیادی در ماشین آلات و سازه های مختلف تحت بارگذاری متغیر قرار دارند. برای مثال در قطعاتی مانند مته های ابزار، محور چرخ اتومبیل و پل ها، اعمال تنش های سیکلی امری طبیعی محسوب می شود. با این که این بارهای متناوب از حد تحمل قطعات کمترند و در ظاهر نباید آسیبی به قطعه وارد شود؛ اما با گذشت زمان بسیاری از آنها می شکنند. با توجه به مطالب فوق می توان لزوم درک مکانیزم خستگی و بررسی و انجام تست خستگی در مواد را به عنوان یکی از مهم ترین تست های مخرب دریافت.
مکانیزم رخ دادن خستگی در فلزات
دلیل اصلی خطرناک بودن شکست خستگی، وقوع آن بدون آگاهی قبلی و بدون قابلیت مشاهده است. بنابراین همواره باید قابلیت اطمینان خستگی قطعات را مد نظر قرار داد. بررسی ها نشان داده اند که معمولا این نوع شکست، در اثر وجود تمرکز تنش مکانیکی (مانند یک گوشه تیز، فاق یا شیار) یا در اثر عوامل متالورژیکی (مانند ناخالصی یا خوردگی) رخ می دهد.
خستگی شباهت هایی با سیالیت مومسان و تخریب تحت تغییر شکل تک جهتی یا ایستا دارد. متالورژیست ها بر این عقیده اند که فلز تحت کرنش چرخه ای، توسط لغزش صفحات اتمی مشابه و در همان جهات بلوری کرنش تک جهتی تغییر شکل می دهد. در حالی که لغزش در تغییر شکل تک جهتی معمولا در تمام دانه ها منتشر می شود. در خستگی فقط در بعضی دانه ها خطوط لغزش مشاهده می شود و در دانه های دیگر هیچ اثری از لغزش وجود ندارد.
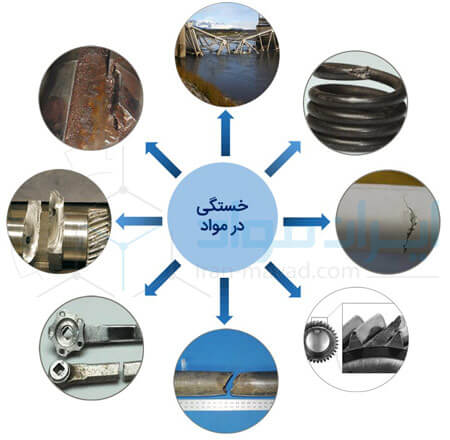
تحقیقات نشان داده اند که به طور کلی خطوط لغزش هنگام چند هزار چرخه اول تنش تشکیل می شوند. با وقوع چرخه های پیاپی، نواحی پیچیده ای از لغزش به وجود می آیند که باعث ایجاد ترک خستگی می شوند. در نهایت با گسترش ترک های خستگی، شکست خستگی اتفاق می افتد.
به طور کلی در مطالعات ساختاری، فرایند خستگی برای سهولت درک به مراحل زیر تقسیم شده است:
- شروع ترک: ناشی از عیوب خستگی که اکثرا با عملیات حرارتی مناسب قابلیت برطرف شدن دارند.
- رشد نوار لغزش ترک: عبارت است از شیوع و عمیق شدن ترک ابتدایی روی صفحاتی با تنش برشی زیاد. این مرحله اغلب “مرحله ی اول رشد ترک” نامیده می شود.
- شکست ترک روی صفحاتی با تنش کششی زیاد: رشد یک ترک معین در جهت عمود بر تنش کششی حداکثر. این مرحله معمولا “مرحله دوم رشد ترک” نامیده می شود.
- شکست نرم نهایی: هنگامی رخ می دهد که طول ترک به اندازه کافی رسیده باشد، طوری که سطح مقطع باقیمانده نتواند بار وارده را تحمل کند.
در این بحث نرخ رشد ترک (da/dN) از اصول تجزیه و تحلیل خستگی مواد بوده و برای قطعات اهمیت قابل توجهی دارد. نمودارهایی برای بررسی این مشخصه وجود دارد. این نمودارها رابطه نرخ رشد ترک را با ضریب تمرکز تنش (ΔK) بیان میکنند. مشهورترین رابطه بر این اساس، رابطهٔ پاریس است که در تصویر زیر به همراه نمودار آن شرح داده شده است. در این نمودار سه مرحلهٔ جوانه زنی ترک، رشد ترک و شکست به خوبی نمایان است. قابل ذکر است که m عددی بین ۱ تا ۶ است و بسته به نوع ماده متغیر است.
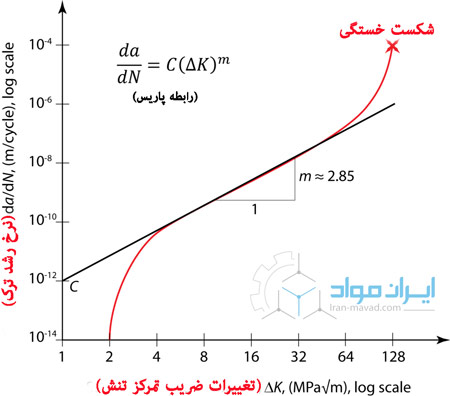
عوامل متالورژیکی موثر بر خستگی
پژوهش های بسیار دقیق بر روی سطح نمونه های تست خستگی نشان داده است که معمولا ترک های خستگی از مکان های فرورفتگی و برآمدگی در قطعات شروع می شوند. عملا تمام شکست های خستگی از سطح آغاز می شوند و این موضوع اهمیت سطح در خستگی فلزات را نشان می دهد. در بسیاری از روش های متداول بارگذاری، (مانند خمش و پیچش) تنش حداکثر در سطح رخ می دهد. در بارگذاری محوری نیز، شکست خستگی تقریبا همیشه از سطح شروع می شود.
عواملی که در سطح یک نمونه خستگی تاثیر می گذارند عمدتا به سه دسته تقسیم می شوند:
- منابع تنش سطحی (ناهمواری و زبری سطح)
- تغییرات استحکام سطحی فلز
- تنش های باقی مانده در سطح
کنترل هر یک از عوامل مذکور نقش به سزایی در فرایند خستگی دارد. علاوه بر این موارد، عوامل دیگری نیز در وقوع شکست خستگی در قطعه تاثیرگذارند که در این بخش به آن ها اشاره می کنیم:
خوردگی: رخ دادن همزمان تنش چرخه ای و حمله شیمیایی به قطعه، به خستگی خوردگی موسوم است. حمله خورنده بدون حضور تنش غالبا در سطوح فلزی حفراتی ایجاد می کند که مانند شیار عمل کرده و استحکام خستگی را کاهش می دهند. هنگامی که خوردگی و خستگی همزمان واقع شوند، حمله شیمیایی سرعت اشاعه ترک خستگی را به شدت تسریع می کند. به طور کلی، انتخاب هر ماده ای برای این نوع عملکردهای صنعتی، باید بر خواص مقاومت به خوردگی متکی باشد. بنابراین فولاد زنگ نزن، برنز یا آلیاژ مس-بریلیم، احتمالا بهتر از فولاد عملیات حرارتی شده عمل خواهند کرد.
حفاظت از فلز در برابر تماس با محیط خورنده توسط روکش های فلزی و غیرفلزی موثر است؛ به این شرط که روکش در اثر کرنش چرخه ای تخریب نشود. روکش های روی و کادمیم بر فولاد و روکش های آلومینیوم آلکلاد در بسیاری کاربردهای خستگی موثر هستند، حتی اگر این پوشش ها باعث شوند هنگام تست خستگی در هوا استحکام خستگی کم شود .
تشکیل تنش های باقیمانده فشاری روی سطح نیز از باز شدن شیارهای سطحی و وارد شدن ماده خورنده جلوگیری می کنند. برای مثال ساچمه زنی و نیتریده کردن در مبارزه با خستگی بسیار موثر است.
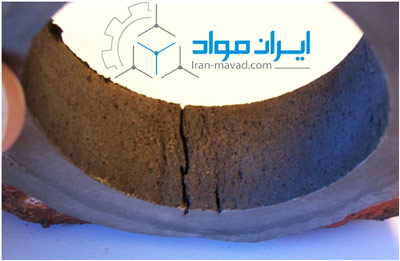
زبری سطح: زبری سطح یکی از عوامل مهمی است که باعث تسریع فرایند شکست می شود. بررسی ها نشان می دهند که نمونه هایی که صافی سطح آنها بالاست و خراش های ظریف آنها موازی جهت تنش کششی اصلی قرار دارد بهترین نتایج را در تست خستگی نشان می دهند چرا که تمرکز تنش و وجود تنش های پسماند در آن ها به حداقل می رسد. در نمونه های آزمایشگاهی نیز برای تست خستگی معمولا از نمونه هایی استفاده می شود که به دقت پرداخت شده اند و به میله های پار معروف هستند.
دما: تست خستگی فلزات در دماهای کمتر از دمای اتاق نشان می دهد که استحکام خستگی با کاهش دما افزایش می یابد. برای مثال با اینکه فولادها در حالت خستگی در دمای کم به شیار حساس تر می شوند، هیچ گونه تغییر ناگهانی در خواص خستگی در دماهای کمتر از دمای انتقال تردی به نرمی وجود ندارد. این واقعیت که با کاهش دما استحکام خستگی نسبتا بیشتر از استحکام کششی افزایش می یابد، با نشان دادن شکست خستگی در دمای اتاق که با تشکیل و تمرکز جای خالی همراه است، توجیه می شود. به طور کلی می توان گفت استحکام خستگی فلزات با افزایش دما نسبت به دمای محیط کم می شود. در این میان فقط فولاد های نرم استثنا هستند که در دمای ۲۱۱ تا ۸۱۱ درجه سلسیوس استحکام خستگی آن ها حداکثر است.
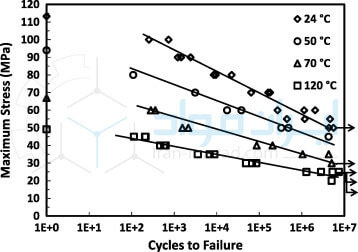
اندازه دانه: رابطه عمر خستگی با اندازه دانه به چرخه های فرایند تغییر شکل بستگی دارد. بیشترین تاثیر اندازه دانه بر عمر خستگی در شرایط تعداد چرخه زیاد و تنش کم اتفاق می افتد. در موادی با انرژی نقص انباشتگی زیاد (مانند آلومینیوم و مس) ساختارهای سلولی به سادگی به وجود آمده و مرحله ۱ اشاعه ترک را کنترل می کند. بنابراین اثر اندازه دانه از بین می رود و عمر خستگی در تنش ثابت به اندازه دانه حساس نیست. اما در ماده ای با انرژی نقص انباشتگی کم (مانند برنج آلفا)، لغزش مسطح و عدم وجود ساختار سلولی باعث می شود مرزهای دانه آهنگ ایجاد ترک را کنترل کنند. در این حالت، عمر خستگی با نصف قطر دانه متناسب است.
تنش های حرارتی: گاهی اوقات شکست خستگی بدون دخالت نیروهای مکانیکی و توسط تنش های حرارتی اتفاق می افتد. اگر شکست در اثر اعمال تنش حرارتی رخ دهد، شرایط به “شوک حرارتی” موسوم است؛ اما اگر شکست پس از اعمال مکرر تنش های حرارتی رخ دهد، این حالت “خستگی حرارتی” نامیده می شود. غالبا در قطعاتی که در دمای بالا کار می کنند، شرایط ایجاد شکست در اثر خستگی گرمایی وجود دارد. برای مثال فولاد زنگ نزن آستنیتی از فلزاتی است که به دلیل هدایت حرارتی کم و ضریب انبساط حرارتی زیاد خود نسبت به این پدیده بسیار حساس است.
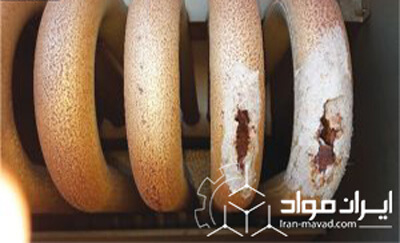
طراحی: همان طور که گفته شد تمرکز تنش نقش اساسی ای در رخ دادن خستگی دارد. در طراحی قطعات صنعتی، تغییرات طراحی به نحوی که تمرکز تنش کم شود و استفاده صحیح از تنش باقیمانده فشاری مفید انجام گیرد، بسیار رایج است. بنابراین معمولا به جای تغییر جنس قطعه، می توان با کنترل فرایند طراحی، در خواص خستگی بهبود ایجاد کرد.
استحکام خزشی: به طور کلی می توان گفت هرچه استحکام خزشی ماده ای بیشتر باشد، استحکام خستگی آن ماده “در دماهای زیاد” بیشتر است. باید توجه داشت که عملیات متالورژیکی که باعث ایجاد بهترین خواص خستگی در دمای بالا می شود، لزوما به ایجاد بهترین مشخصات مکانیکی در خزش منجر نخواهد شد. در دماهای زیاد که خزش مکانیزم غالب است، مواد درشت دانه استحکام خستگی بیشتری دارند.
فرایند ساخت نیز در این مورد موثر است. اغلب قطعات ریختگی به خزش مقاوم ترند، ولی آلیاژهایی که بر آنها کار مکانیکی انجام شده باشد مقاومت به خستگی بهتری نشان می دهند.
چگونگی انجام تست خستگی
سه عامل مهم بر وقوع شکست خستگی موثرند. این عوامل عبارتند از:
- تنش کششی حداکثر
- تغیرات نوسانی زیاد در تنش اعمالی
- زیاد بودن چرخه های اعمالی
علاوه بر این، پارامتر های دیگری مانند تمرکز تنش، خوردگی، دما، بار اضافی، ساختار متالوژیکی، تنشهای باقی مانده و تنش های مرکب هم وجود دارند که شرایط را برای وقوع شکست خستگی فراهم می کنند.
در تست خستگی تعداد زیادی متغیر دخالت دارند. حتی اگر تمام نمونه های یکسان آزمایش با دقت زیادی تهیه و به طور یکنواخت صیقل داده شوند، نتایج آزمون خستگی ممکن است دارای پراکندگی قابل ملاحظه ای باشند. انجام آزمایش خستگی در آزمایشگاه، معمولا بر اساس شرایط بارگذاری یکنواخت استاندارد است و بنابراین برقراری ارتباط میان نتایج به دست آمده در تست خستگی در آزمایشگاه با آنچه که مستقیما در هنگام کار اتفاق می افتد، دشوار است. لذا بهکار گیری مستقیم نتایج تست خستگی در طراحی مشکل است؛ بنابراین در بعضی موارد لازم است با ابداع و انجام آزمایش خستگی روی تمامی یک سازه مهندسی، آزمون تا شکست کامل ادامه یابد. در شرایط آزمایشگاهی، آزمایش خستگی مواد معمولا به دو صورت محوری و خمشی انجام می گیرد.
تست خستگی خمشی
با وارد کردن نیرو به صورت خمشی به نمونه ها در دستگاه تست خستگی بلافاصله در سطح بالایی نمونه تنش کششی و در سطح زیری تنش فشاری ایجاد میشود. بعد از اینکه نمونه نیم دور یعنی ۱۸۰ درجه چرخید، مکانی که ابتدا تحت تأثیر تنش کششی قرار گرفته بود، تحت تنش فشاری قرار می گیرد. به این ترتیب تنش در هر نقطه ای از نمونه به صورت تناوبی تغییر میکند. در تست خستگی خمشی تنش متناوب میتواند بین دو مقدار حداکثر و حداقل در گونه های مختلف تنشی، از کشش تا فشار تغییر کند. اینجا سه حالت پیش می آید:
- حالت اول: تغییرات بارگذاری میتواند به گونهای باشد که تنش اعمالی بین دو مقدار تنش کششی و تنش فشاری تغییر کند و تنش متوسط میانگین آن دو باشد .
- حالت دوم: تغییرات تنش میتواند به صورتی باشد که حداکثر تنش در موقعیت فشاری، کمتر از حداکثر تنش کششی باشد.
- حالت سوم: بارگذاری به گونهای باشد که مقدار تنش بین حداکثر و حداقل در موقعیت کششی یا فشاری تغییر کند.
با توجه به هدف آزمایش هر یک از حالت های فوق می تواند تعریف گردد. نکته قابل توجه این است که تنش های اعمال شده نباید هر دو به صورت فشاری باشند؛ زیرا تنشهای فشاری باعث بسته شدن ترکها میشود. بنابراین شکست رخ نمیدهد و نتیجه ای به دست نمی آید.
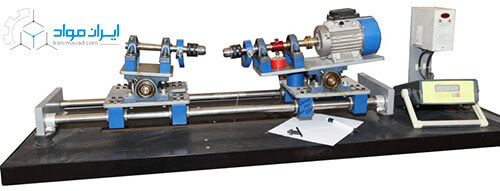
دستگاه تست خستگی خمشی
تست خستگی محوری
در آزمایش خستگی با بارگذاری محوری یا مستقیم، به نمونه در یک محور هم کشش و هم فشار وارد می شود. به این نکته باید توجه شود که لازم است که بارگذاری روی قطعه، کاملا تک محوری باشد. در آزمون خستگی محوری، نگه دارنده های نمونه به صورت بسیار دقیق درون راهنماهای ثابتی جای می گیرند تا بارگذاری هم در کشش و هم در فشار کاملا محوری باشد. یک مزیت روش آزمون تنش مستقیم در برابر آزمایش خمشی این است که چرخه بارگذاری را می توان طوری تنظیم نمود که تنش متوسط صفر نشود.
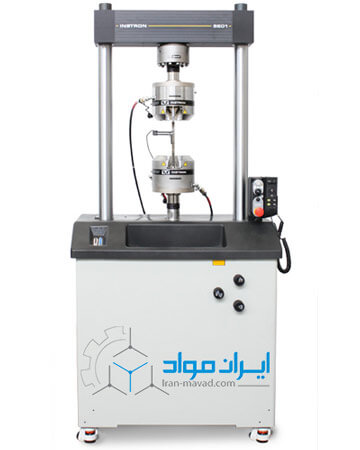
دستگاه تست خستگی محوری
در این بخش توجه شما را به فیلمی که در خصوص آزمون خستگی مواد تهیه شده، جلب می کنیم.
نتایج آزمون خستگی
حین انجام آزمایش خستگی بعد از تعداد دور معینی شکست در نمونه ظاهر میشود. نتایج تست خستگی معمولا به صورت منحنی های S-logN نمایش داده می شوند و مهم است که ضمن گزارش نتایج، روش اعمال تنش، نوع ماشینی که به کار گرفته شده، اندازه های نمونه آزمایش و بسامد چرخه، گزارش شوند. باید توجه کرد که نقاط به دست آمده ممکن است همگی بر روی یک منحنی قرار نگیرند، بلکه اکثرا در محدوده ای کم و زیاد میشوند. برای حل این موضوع، می توان منحنی را با استفاده از مقداری متوسط از مقادیر مشخص شده به وسیله آزمایش رسم کرد. این بدین معنی است که احتمال این که نمونه حد معینی از تنش و تعداد دور تناوب مربوط به آن را بدون شکست بتواند تحمل کند، ۵۰ درصد است.
حد خستگی
حد خستگی یا استحکام خستگی بالاترین تنشی است که یک ماده میتواند برای یک تعداد سیکل بدون شکستن تحمل کند. پس از تست خستگی دیده می شود که اغلب فولادهای نرم، آلیاژهای منیزیم و تیتانیم و بعضی از آلیاژهای آلومینیم در نمودار خود به حد خستگی می رسند. در مقابل تعدادی از فلزات غیرآهنی از قبیل آلیاژهای مس، بعضی از آلیاژهای منیزیم و آلومینیم چنین حدی کاملاً مشخصی ظاهر نمیشود، بلکه کاهش پیوسته تنش به ازای افزایش دوره تناوب دیده میشود، در این حالت تعیین حد خستگی چندان ساده نخواهد بود. اما از آنجایی که دادن کمیتی که بتواند حد خستگی یک ماده را مشخص کند از نظر صنعتی اهمیت دارد، لذا در این گونه موارد تنشی را که به ازای آن حدود ۱۰۰ میلیون دور تناوب هنوز قابل تحمل باشد به عنوان حد تحمل انتخاب میشود.
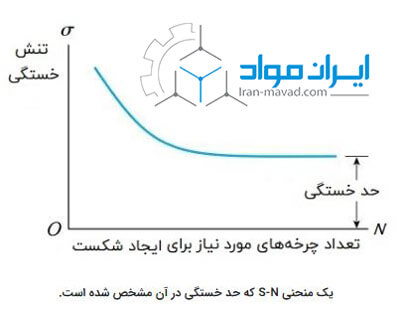
جمع بندی
با پیشرفت صنعت و افزایش تعداد وسایلی از قبیل خودرو، هواپیما، کمپرسور، پمپ، توربین و غیره که تحت بارگذاری تکراری و ارتعاشی هستند، خستگی بیشتر متداول شده و اکنون چنین برداشت میشود که عامل حداقل ۹۰ درصد شکست های ناشی از دلایل مکانیکی حین کار، خستگی باشد. با توجه به این موضوع ضرورت انجام تست خستگی با اصولی که در این مقاله بررسی گردید همچنان زیادتر می گردد.
در پایان توصیه می کنیم برای مطالعه در خصوص سایر تست های مخرب که در همین وب سایت تهیه شده، به پست های زیر مراجعه کنید:
- آزمون کشش (Tensile Test)
- آزمون فشار (Compression Test)
- آشنایی با تست ضربه (Impact Test)
- مروری بر روش های سختی سنجی مواد (Haedness Test)
- تست خمش مواد (Bending Test)
- خزش و مکانیزم های آن (Creep and Mechanisms)
- متالوگرافی و کاربردهای آن (Metallography)
منابع
- خستگی در فلزات – مهرزاد رییسی
- متالورژی مکانیکی – جورج دیتر (ترجمه شهره شهیدی)
دانلود فقط با IP ایران امکانپذیر است. در صورت عدم مشاهده باکس قرمز رنگ دانلود، VPN خود را خاموش نموده و صفحه را رفرش کنید.
پسورد فایل فشرده : www.iran-mavad.com
دیدگاه کاربران
خیلی خوب بود