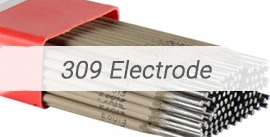
جوشکاری با پرتو الکترونی EBW
برای اولین بار در حدود سال ۱۹۶۸ میلادی آقای استیگر والد به کار بر روی پرتو الکترونی به عنوان یک منبع حرارتی در ماشین کاری دقیق پرداخت. در سال ۱۹۵۷دکتر استور از موسسه انرژی اتمی فرانسه نتایج جوشکاری با پرتو الکترونی را که از سال ۱۹۹۶ آغاز کرده بود، منتشر ساخت. تجهیزات استفاده شده توسط وی کاملا با وسایلی که بعدأ استفاده شد، متفاوت بود. او از یک منبع با ولتاژ بین ۱۰- ۱۶KV استفاده کرد. در سال ۱۹۹۸، یک ماشین مته کاری ، با پرتو الکترونی در ایالت متحده ابداع شد که در جوشکاری نیز مورد استفاده قرار گرفت. در همان سال برتون و فرانک هوسر مطالعات و آزمایشات خود را در مورد جوشکاری زیرکونیوم به منظور استفاده در مصارف هسته ای آغاز کردند. در کنار این تلاشها، بهینه سازی و اقتصادی کردن فرایند در آمریکا مورد توجه قرار گرفت. در حال حاضر این فرایند در بسیاری از صنایع به ویژه صنایع هسته ای و هوافضا مورد استفاده قرار میگیرد.
اصول فرایند جوشکاری با پرتو الکترونی
فرایند جوشکاری با پرتو الکترونی یک فرایند اتصال ذوبی است که در طی آن قطعه کار توسط جریانی متراکم از الکترونهای دارای سرعت بالا بمباران شده و کل انرژی جنبشی الکترونها، در اثر برخورد با قطعه کار به حرارت تبدیل می شود. این حرارت موجب ذوب لبه های قطعات و اتصال دو قطعه پس از انجماد می شود.
جوشکاری با پرتو الکترونی معمولا در یک محفظه خلأ با استفاده از یک سیستم تولید و تمرکز پرتو الکترونی انجام می شود. جوشکاری در یک محفظه بسته محدودیت های زیادی را به دنبال دارد ولی نقطه قوت بسیار مهم آن، انجام فرایند در یک محیط تمیز و عاری از هر گونه آلودگی است که موجب می شود یک جوش با کیفیت بسیار عالی ایجاد شود. شکل زیر یک نمای کلی از دستگاه جوشکاری با پرتو الکترونی را نشان می دهد.
بارزترین مشخصه جوشکاری با پرتو الکترونی توانایی آن در ایجاد جوش های بسیار باریک و کاملاً عمیق است. به عنوان مثال به کمک این فرآیند می توان تسمه های فولادی با ضخامت ۱۲ میلیمتر را به شکل سر به سر به گونه ای به هم جوش داد که پهنای جوش از ۱٫۶ میلیمتر بیشتر نشود. این مشخصه در مقایسه با الگوی جوش ذوبی قوسی و روش های حفاظت با گاز بسیار بالاتر است. این امر ناشی از مکانیزم و نحوه عملکرد خاص پرتوالکترونی در هنگام جوشکاری است.
در روش های جوشکاری قوسی منابع حرارتی تنها اندکی از سطح را ذوب می کنند و عمق نفوذ جوش ناشی از حرارتی بوده که عمدتاً از طریق هدایت از سطح ذوب شده در تمام جهات است. با توجه به این که هدایت حرارت در تمام جهات انجام می گیرد با عمیق تر شدن جوش، عرض آن نیز افزایش می یابد.
پرتو الکترونی می تواند دارای چنان شدت حرارتی باشد که به طور همزمان در کنار توپ گردن فلز، عمل تبخیر و ایجاد سوراخ کلید در فلز مذاب را در ولتاژهای بالا انجام دهد، دیواره این سوراخ به صورت مناب است و با پیشرفت سوراخ در محل اتصال، فلز بیشتری از دیواره ذوب می شود با حرکت پرتو، عمل ذوب شدن حول دهانه سوراخ ادامه می یابد و همزمان با آن انجماد در قسمت پشت سوراخ انجام می گیرد.
تفنگ الکترونی قلب این فرایند جوشکاری است در تفنگ الکترونی الکترونهای نشر داده شده از کاند که به شکل پرتو در آورده شده اند، به سمت قطعه کار شتاب داده می شوند. در اینجا از قانون ساده الکتریسیته دفع بارهای همنام از یکدیگر و جذب بارهای غیر همنام توسط یکدیگر استفاده می شود. یک الکترود با | شکل کاملا مشخص فنجانی با بارهای منفی پرتو را شکل می دهد. شتاب دهی به الکترونها توسط میدان الکتریکی ناشی از ولتاژ اعمال شده و به کمک پست الکترود با بار مثبت انجام می شود، پرتو حاصل شده با تمرکز بالا با سرعت ۳۰ تا ۷۰ درصد سرعت نور از سوراخ کوچک میان آند عبور کرده و به قطعه کار می رسد، دفع متقابل الکترونها باعث واگرایی پرتو در طی مسیر خود می شود. بنابراین باید این مسأله تحت کنترل باشد تا پرتو در محل از پیش تنظیم شده با قطعه کار برخورد کند و قطر پرتو به هنگام برخورد با قطعه مناسب باشد.در تجهیزات قدیمی تر از خود قطعه کار به عنوان آند شتاب دهنده استفاده می شد که چندین عیب داشت جوشکاری در عمق های از پیش طراحی شده امکان پذیر نبود چرا که لبه های آماده سازی شده قطعه کار، پرتو را به خود جذب می کرد و کنترل روی فرایند کاهش می یافت. همچنین استفاده از قید و بند در کنار قطعه کار به راحتی امکان پذیر نیست چرا که قید و بندها نیز مانند قطعه کار در معرض اتصال قرار می گرفتند، بنابراین تصمیم گرفته شد که آند شتاب دهنده در تفنگ الکترونی قرار گیرد و سیستم تولید پرتو کاملا از قطعه کار مستقل باشد.
حرارت ورودی در جوشکاری با چهار پارامتر کنترل می شود:
- تعداد الکترون در ثانیه (جریان پرتو) که با قطعه کار برخورد می کند
- سرعت الکترونها در لحظه برخورد (پتانسیل شتاب دهی)
- قطر پرتو الکترونی روی صفحه برخورد با قطعه کار (اندازه قطعه پرتو
- سرعت انتقال دستگاه یا حرکت قطعه کار ( سرعت جوشکاری)
دو مورد اول تقریباً ثابت هستند و با کنترل ولتاژ و امپر دستگاه کنترل می شوند. قابلیت کنترل قطر پرتو یک مزیت نسبت به جوش های قوسی محسوب می شود.
تجهیزات مورد نیاز
یک ماشین جوشکاری پرتو الکترونی سه جزء اصلی دارد:
- یک تلفنگ الکترونی که پرتو کنترل شده الکترونی تولید می کند.
- یک محفظه خلاء با تجهیزات و پمپ های مربوطه
- یک دستگاه که پرتو را در امتداد خط اتصال حرکت می دهد یا قطعه کار را زیر تفنگ الکترونی جابجا می نماید.
تجهیزات مربوط به پروسه جوشکاری پرتو الکترونی از نظر ولتاژ مصرفی به دو دسته تقسیم می شوند:
- ولتاژ پایین
- ولتاژ بالا
مزایا و محدودیت ها
مهم ترین مزایای فرآیند جوشکاری با پرتوالکترونی EBW عبارتند از:
- ایجاد جوش های عمیق تر و باریکتر نسبت به روش های قوسی
- حرارت ورودی کمتر به جوش در مقایسه با روشهای ذوبی دیگر (برای ایجاد حجم جوش ثابت)
- نسبت عمق به عرض بالای جوش و عدم نیاز به جوش های چند پاسه
- ناحیه متأثر از حرارت جوش باریک به علت تمرکز حرارتی بالای فرایند
- تمیزی فلز جوش به دست آمده به علت استفاده از خلاء در فرایند
- امکان دست یابی به سرعت جوشکاری بالا و در نتیجه سرعت تولید بالاتر
- بازدهی انرژی بالا (تا حدود ۹۵٪)
- پیچیدگی کم قطعه جوشکاری شده به علت تمرکز حرارتی بالای فرایند
- عدم نیاز به عملیات حرارتی جدی قبل و بعد از فرایند
- امکان اتصال قطعات و آلیاژهای حساس به حرارت
- امکان جوشکاری فلزات دیرگداز و فعال که خواص آنها به شدت تابع آلودگی های گازی نظیر اکسیژن ، نیتروژن و هیدروژن در محدوده تا چند صد ppm است( نظیر تنگستن ، مولبیدن ، نیوبیم ، تانتال ، زیرکونیوم ، تیتانیون و هافتیم)
- امکان آب بندی با کیفیت بسیار بالا در اتصالات
- امکان اتصال بهتر عناصر و فلزات فعال
- سهولت کنترل فرایند به صورت رایانه ای
- امکان انجام فرایند در طرح اتصال های گوناگون
- عدم نیاز به سیم جوش (در اغلب موارد) و عدم نیاز به برطرف کردن سرباره و اضافه های جوش
- امکان جوشکاری قطعات بسیار ظریف مورد استفاده در صنایع الکترونیک و تجهیزات پزشکی و آزمایشگاهی
مهمترین محدودیت های این فرایند نیز عبارتند از:
- در این روش، قطعه کار می بایست طوری در خلأ قرار داده شود که کمترین انحراف و پراکندگی پرتو را از مسیر اولیه خود به همراه داشته باشد.
- در اثر برخورد پرتو الکترونی با سطح فلز ، پرتو X تولید می شود و لذا نیاز به حفاظت در برابر این پرتو وجود دارد.
- به علت آنکه پرتو الکترونی شامل اجزای با بار منفی است، وجود میدان های الکتریکی و مغناطیسی سرگردان باعث انحراف پرتو از مسیر اصلی طراحی شده می شود.
- عدم پایداری طولانی مدت پرتو: استفاده از این فرایند در سازه های بزرگ نیاز به پایداری چند ساعته پرتو دارد. تفنگ الکترونی ممکن است چند بار در یک دوره معین متحمل تخلیه بار الکتریکی شود که به نوبه خود می تواند باعث اختلال در توزیع توان و بر جای ماندن عیوب در جوش شود.
- تعمیر عیوب ایجاد شده در عمق قطعه در اتصال قطعات ضخیم مشکل است و در صورت تلاش برای تعمیر موضعی عیوب، به احتمال زیاد، عیوب جدیدتری شکل می گیرد.
- قیمت بالای تجهیزات و کاربرد محدودتر نسبت به روش های قوسی
- نیاز به تمیز کاری قطعات به شکلی بسیار خوب برای آنکه از شکل گیری عیوبی مثل تخلخل در جوش جلوگیری شود. در مورد فولاد، مقدار اکسیژن بایستی کمتر از ppm 60 و مقدار نیتروژن کمتر ppm ۱۰۰ باشد. مشکل دیگر آن است که فولادهای جوشان به هر صورتی با این روش قابل استفاده نیستند چرا که با تولید گاز ، علاوه بر هم زدن خلأ محیط، به تجهیزات تولید خلا نیز آسیب مسی رسانند.
- ترکیدگی فلز جوش: به علت محدودیت در استفاده از سیم جوش در این روش و نیز نیروی شدید روی مذاب، امکان شکل گیری ترک به خصوص در ابتدا و انتهای مسیر قابل توجه است. نکته دیگر آن که به علت سرعت انجماد بالا در این فرایند، اگر فلز استحکام کافی را در حالت گرم نداشته باشد، امکان ترک خوردن آن در اثر تنش های حرارتی وجود دارد.
- درز جوش و گرده جوش بسیار نازک در این فرایند موجب حساسیت زیاد در برابر عیب ذوب ناقص می شود که ناشی از خطا در دنبال کردن صحیح درز اتصال توسط پرتو است.
- چقرمگی کم در اغلب فولادها: در صورتی که نسبت عمق به پهنای جوش بزرگتر از ده باشد، حفره جوش ناپایدار شده و به جای آنکه ناحیه HAZ کوچکتری نسبت به سایر روشها حاصل شود، ناحیه مذکور بر عکس، بزرگتر هم می شود.
- نبود آزمون های غیر مخرب تدوین شده
- حفره انتهای محل جوشکاری: در اثر تغییر ناگهانی توان پرتو در انتهای جوش، احتمال شکل گیری تخلخل بسیار بالا می رود.
- حساسیت شدید فرایند به تغییرات جزیی متغیرهای فرایند
نکات تکنیکی
الکترون دارای بار منفی است و بر اثر برخورد به قطعه، بار منفی به نمونه انتقال می یابد. این بار منفی در قسمت های مختلف دستگاه و نمونه می تواند باعث اثر دافعه بر پرتو شود. برای جلوگیری از این مشکل، نمونه و دستگاه ها به اتصال زمین وصل می شوند. مسأله دیگر اثرات مغناطیسی است که باید کنترل شوند و قطعه از مغناطیس خالی شود تا موجب انحراف پرتو نگردد.
مونتاژ کردن قطعات در کنار هم اگر به شکل ضعیفی انجام شود می تواند موجب کشیدگی زیاد مذاب و بروز عیوبی نظیر بریدگی کناره جوش و حفره شود. فاصله شیار نباید از یک حدی نیز بیشتر شود. جوشکاری با پرتو زاویه دار هم ممکن است در کاهش عیوب ناشی از مونتاژ ضعیف موثر باشد اما موجب افزایش پهنای جوش و کاهش سرعت جوشکاری (برای حفظ عمق نفوذ) می شود. در EBW معمولا نیاز به فلز پرکننده نیست مگر در مواردی که جنس قطعات متفاوت باشد، خطر ترکیدگی وجود داشته باشد، نیاز به آلیاژ سازی باشد و یا پخ کاری صورت گرفته است و باید شیار پر شود.
در اتصال فلزات غیر همجنس باید به خواص فیزیکی قطعات از جمله دمای ذوب، ضریب انتقال حرارت و گرمای ویژه توجه کرد. جوش پذیری فلزات غیر همجنس را می توان از روی دیاگرام فازی تعیین کرد. اگر فاز شکننده بین فلزی تشکیل گردد، فلز جوش ترد شده و جوش پذیری خوب نخواهد بود.
آماده سازی و ترتیب انجام فرایند روش های آماده سازی در فرایند جوشکاری با پرتو الکترونی بسته به تجهیزات و کاربرد مورد نظر متفاوت بوده ولی روش کلی زیر قابل اجراست:
- آماده سازی و سرهم کردن قطعه کار و قید و بندهای جوشکاری که شامل تمیزکاری و احتمالا مغناطیس زدایی، پیشگرم کردن و خال جوش زدن می باشد.
- قرار دادن قطعه به همراه قید و بند درون محفظه خلأ
- شروع تخلیه محفظه و سپس متمرکز شدن روی قطعه و تنظیم پارامترهای فرایند
- هم خط کردن راستای اتصال با راستای حرکت پرتو و انجام فرایند
- دادن فرصت کافی جهت سرد شدن قطعه و سپس وارد کردن هوا به محفظه و خارج کردن مجموعه
سطح قطعه کار می بایست کاملا برای عملیات جوشکاری در خلأ آماده سازی شود. تمیز کاری غلط قطعات باعث ایجاد عیوب در جوش و افت خواص مکانیکی می شود. تمیز کاری غلط همچنین باعث افزایش زمان تخلیه هوای محفظه و ناپایداری عملکرد تفنگ الکترونی می شود. علاوه بر این روغن و چربی باقیمانده باعث آسیب دیدگی تجهیزات سیستم خلا می شود. عموما استفاده از برس سیمی به منظوره تمیز کاری توصیه نمی شود چرا که باعث نفوذ آلودگی به لایه های زیر سطحی می شود. عموما به منظور تمیز کردن اجزای تفنگ و قطعه کار از استن استفاده می شود. مغناطیس زدایی عمدتا با قرار دادن قطعه در یک میدان متناوب القایی با فرکانس ۶۰ هرتز و بیرون کشیدن تدریجی آن از میدان انجام می شود. برای سنجش میزان مغناطیس باقی مانده از دستگاه گاوس متر استفاده می شود.
محدوده تغییرات ضخامتی که به روش پرتو الکترونی قابل اتصال است وسیع می باشد و حتی در اتصالات ضخیم نیز، ضرورت پیشگرم چندان شدید نیست، چرا که ناحیه HAZ آن بسیار باریک است. فلزات سختی پذیر و فلزاتی که جوش پذیری ضعیفی دارند، عموما نیاز به پیشگرم کردن دارند که با تغییر حرارتی و افزایش احتمال تاب برداشتن قطعه، این ضرورت بیشتر احساس می شود. فولادهای HSLA و فولادهای ابزار با ضخامت بالاتر از ۹٫۵ میلیمتر به منظور جلوگیری از ترک خوردگی معمولا پیشگرم می شوند. جوش عمیق فولادهای کربنی با درصد کربن بالاتر از ۰٫۳۵% نیز به پیشگرم کردن نیاز دارد. عملیات پیشگرم کردن بایستی قبل از قرار دادن قطعه در محفظه انجام شود. بسته به نوع آلیاژ مصرفی و ابعاد آن ، روش های گرم کردن با مشعل و گرم کردن در کوره استفاده می شوند. پسگرم کردن این قطعات نیز تفاوت چندانی با سایر روش های جوشکاری ندارد.
در این فرایند به جای استفاده از قید و بند از خال جوش زدن با پرتو الکترونی استفاده می شود که هزینه تمام شده و زمان انجام فرایند را کاهش می دهد.
خال جوش مناسب در این روش برای جلوگیری از تغییر ابعاد و شکل قطعه ضروری است. خال جوش زدن عمدتا با انرژی پایین انجام می شود و معمول ترین روش آن، | انجام این کار در فواصل مختلف و معین است.
کابردهای جوشکاری با پرتو الکترونی
مهمترین فلزات و آلیاژهایی که با این روش جوشکاری می شوند عبارتند از:
برلیم
مسأله مهم در جوشکاری این فلز واکنش های اتمسفری و توزیع تنش در اتصال است چرا که سیستم های لغزشی چندانی در شبکه بریلیم فعال نمی باشند و لذا انعطاف پذیری چندانی نخواهد داشت. مشکل جوشکاری بریلیم با این روش تبخیر بریلیم در فشارهای کم (خلا) می باشد. ضخامت های تا ۱٫۵ میلیمتر را می توان به صورت تک پاس جوشکاری نمود و نیازی به آماده سازی نمی باشد، ولی ترک خوردگی و تبخیر شدید در اتصالات از مشخصات فرایند است.
تیتانیم
جوشکاری قوسی روی تیتانیم باعث کاهش مقاومت ضربه و انعطاف پذیری فلز جوش نسبت به فلز پایه می شود که عمدتا ناشی از آلودگی توسط اکسیژن و نیتروژن می باشد. یکی از بهترین آلیاژهای جوش پذیر تیتانیم ، آلیاژ Ti6Al4V می باشد.
زیرکونیم
در آلیاژهای مصرفی در صنایع هسته ای و برای تولید جوش های باریک استفاده می شود. بهترین آلیاژ جوش پذیر زیرکونیوم، ۲-Zircally است و حداکثر ضخامت قطعات اتصال داده شده in ۲ می باشد. نسبت ارتفاع به پهنای جوش بالاتر از ۲ قابل دسترسی است. استحکام کششی بالاتر نسبت به فلز پایه و انعطاف پذیری حداقل برابر فلز پایه قابل دست یابی است.
مولیبدن
مهم ترین مشکل جوشکاری مولیبدن، تردی، انعطاف پذیری کم و استحکام ضربه پایین است. بهتر است آلیاژهای مصرفی تا حد امکان خالص باشند. EBW با انرژ کم و جوش سریع در خلاء مناسب نیز به حصول اتصال با خواص بهتر کمک می نماید.
مهم ترین صنایعی که از این فرآیند استفاده می کنند عبارتند از:
صنایع هوافضا
روش جوشکاری با پرتو الکترونی در صنعت ساخت موتورهای فضاپیماها کاربرد وسیعی دارد. اصلی ترین کاربرد آن، جوشکاری اجزای استاتورهای ضخیم آلیاژهای تیتانیم، دیسک کمپرسورها و محور روتور کمپرسورها است. در این موارد عمدتاً به انسجام خوب جوش و حداقل پیچش و ناحیه HAZ کوچک احتیاج است.
صنایع هسته ای
روش جوشکاری با پرتو الکترونی در صنایع هسته ای بیشتر برای جوشکاری قطعات تیتانیمی و زیرکونیومی استفاده می شود.
صنایع الکترونیک و پزشکی
جوشکاری سنسورها روی اجزای الکترونیکی و وسائل پزشکی که در دماهای پایین کاربرد دارند با این روش تسهیل می شود. جنس های مصرفی در این بخش عمدتاً فولاد زنگ نزن آستنیتی و کبالت و کرم است.
صنایع خودروسازی
جوش باریک با عمق نفوذ بالا، کرابرد وسیعی در اتصال شعاعی چرخ دنده ها دارد و در مواردی که حداقل عملیات ماشین کاری و پرداخت ضروری باشد، استفاده می شود.
دیدگاه کاربران
سلام.
خیلی ممنون از قرار دادن این فایل. امیدوارم موفق باشین.