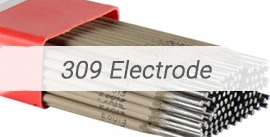
متالورژی پودر Powder Metallurgy
متالورژی پودر چیست؟
متالورژی پودر یکی از روشهای تولید قطعات فلزی و سرامیکی است که بر مبنای فشردن، شکلدهی و تفجوشی ذرات به یکدیگر و ساخت یک قطعه مستحکم و صلب طراحی شده است. تفجوشی در زیر نقطهی ذوب صورت میگیرد. تحت این شرایط، ذرات پودر با تشکیل پیوندهای قوی، در اصطلاح به هم جوش خورده و ساختار همگن و مستحکمی را پدید میآورند.
متالورژی پودر بر بسیاری از محدودیتهای روشهای دیگر مثل ریختهگری، نورد، اکستروژن و آهنگری غلبه کرده است. بسیاری از محصولاتی که قابلیت تولید با روشهای فوق را ندارند، با استفاده از تکنولوژی متالورژی پودر تولید میشوند. اکثر محصولاتی که با این روش تولید میشوند، نیازی به ماشینکاری یا عملیات حرارتی تکمیلی ندارند. این فرایند در شکلدادن فلزاتی با انعطاف پایین و نقطهی ذوب بالا همچون تنگستن توانایی بالایی دارد. همچنین میتوان تمامی ملاحظات مربوط به تغییرات فازی جامد-مایع را نادیده گرفت.
تولید قطعات با پودر به بیش از پنج هزار سال پیش میرسد. هماکنون، ستون آهنی با وزنی حدود شش تن در شهر دهلی هندوستان وجود دارد که هزار و شش صد سال پیش به روش متالورژی پودر تهیه شده است. تاریخچه این فرآیند را میتوان به صورت زیر شرح داد:
- اواخر قرن هجدهم ولاستون کشف کرد که میتوان پودر فلز پلاتین را پس از تراکم و حرارت دادن، در حالت گرم با چکشکاری به بلوک تبدیل کرد.
- قرن نوزدهم: اولین کاربرد متالورژی پودر برای تولید پلاتین با دانسیته کامل بود. با اختراع برق توسط ادیسون، در صنعت الکترونیک از این ماده جهت تولید لامپهای روشنایی و یا مقاومتهای الکتریکی بهره میگرفتند.
- ابتدای قرن بیستم: فناوری متالورژی پودر قطعات تنگستنی را در برگرفت.
تولید قطعات به روش متالورژی پودر مشتمل بر 5 بخش اصلی است:
- تولید پودر
- مخلوط کردن
- فشردن
- سینتر کردن
- عملیات نهایی
روشهای تولید پودر
روش تولید پودر بر اندازه، شکل، ریزساختار، ترکیب شیمیایی و هزینه های تولید تاثیرگذار است. پودرها معمولا به روش های مکانیکی، فیزیکی و شیمیایی تولید می شوند که در این بخش به توضیح هر یک میپردازیم.
روش مکانیکی
در این روش، معمولا تلفیقی از فرایندهای ضربه، سایش، برش و تراکم به کار گرفته میشود. مهمترین روشهای تولید پودر به روش مکانیکی عبارتند از:
ماشینکاری
در این روش، فلزات ماشینکاری شده و برادههای حاصل از آنها برای تولید پودرهای درشتدانه و نامنظم مورد استفاده قرار میگیرند. این روش اغلب برای فلزات فعالی همچون منیزیم، برلیوم و نقره استفاده میشود؛ اما کیفیت پودرهای تولید شده با این روش چندان بالا نیست.
ساخت کاهشی (Subtractive Manufacturing) یا ماشین کاری(Machining) چیست؟
ماشین کاری چیست؟ تفاوت آن با ساخت کاهشی چیست؟ زیرتکنولوژیهای این روش ساخت و تول...خرد کردن
خرد کردن شامل تجزیه فلز جامد به قطعات کوچک به روشهای مکانیکی است و متداولترین روش در تولید پودر فلزات سخت و ترد و پودرهای اکسیدی محسوب میشود. پودرهای تولید شده به این روش غیر یکنواخت و درشت هستند. این کار به روشهای غلتکی، فکی و چکشی انجام میشود.
آسیا کردن (Milling)
آسیاکردن یکی از روشهای کلاسیک برای تولید پودرهای ترد محسوب میشود. در این روش از نیروهای ضربه، سایش، برش و فشار که به پودرها وارد میشود، استفاده میگردد.
مهمترین آسیابها در روش آسیاکاری عبارتند از:
آسیاب گلولهای (Ball Mill): این آسیاب شامل یک محفظه استوانهای شکل است که در امتداد محور افقی میچرخد. با چرخش محفظه، گلولهها نیز به چرخش درآمده و با برخورد به پودرها باعث خرد و ریزتر شدن آنها میشوند.
آسیاب سیارهای (Planetary mill): در آسیاب سیارهای، صفحه دوار در یک جهت چرخیده و محفظه بر اساس مکانیزمی در خلاف جهت حرکت صفحه دوار، حرکت دورانی انجام میدهد. گلوله و پودر به صورت متناوب روی دیواره داخلی غلتیده و ساییده میشوند؛ سپس با سرعت زیادی از جدارهی محفظه جدا و مجددا به جداره روبهرویی برخورد میکنند. در این حالت ذرات پودر تحت انرژی ضربه بالا به صورت مداوم جوش خورده و میشکنند.
آسیاب لرزشی (Vibratory Ball Mill): این آسیاب شامل یک محفظه استوانهای است که با مقداری ماده ساییدنی و گلولههای سخت ساینده پر میشود. در اثر دوران آسیاب، گلولهها بهطور پیوسته با مادهای که باید پودر شود برخورد کرده و آن را به پودر تبدیل میکنند.
آلیاژسازی مکانیکی
موفقترین روش برای تولید آلیاژهای دارای توزیع دقیق دانههای اکسیدی زیر میکرون در فرآیند متالورژی پودر، آلیاژسازی مکانیکی است که از حرکت تلاطمی بین گلولهها برای ایجاد دانههای پودر آلیاژی بهره میگیرد. در این فرآیند مخلوطی از گلولههای ساینده و پودرهای عنصری در محفظه آسیاب ریخته شده و تکرار ضربه، باعث ایجاد جوش سرد بین دانهها و خردشدن مجدد دانههای جوش خورده و در نهایت تولید پودرهای مرکب میشود.
روش فیزیکی
روشهای فیزیکی از دیگر روشهای تولید پودر در فرایند متالورژی پودر است که از جمله روشهای آن عبارتند از:
گرانوله کردن
در این روش، مذاب مورد استفاده از روی صفحات مشبکی عبور کرده و قطرات سقوط میکنند و منجمد میشوند. گرانوله کردن به دو روش تر و خشک قابل انجام است. در روش گرانولهسازی تر، گرانولهها با اضافه کردن مایع گرانول (آب، اتانول و ایزوپروپانول) بر روی یک بستر پودری تشکیل میشوند. در گرانولهسازی خشک، گرانوله بدون استفاده از محلول مایع تشکیل میشود. تحت این فرایند، پودرها نیاز به فشردهسازی و تراکم دارند و تحت فشار زیاد گرانوله میشوند.
اتمیزاسیون (Atomization)
هر فرایند پودری در متالورژی پودر که شامل تولید قطرات مذاب فلز از طریق جداکردن از جریان مذاب یا هر روش دیگر و انجماد قطرهها پیش از رسیدن به یک سطح جامد باشد، جزء این روش است. اصول کار در این روش شامل سرد کردن آهسته (تولید ذرات کروی) و سرد کردن سریع (تولید پودرهای نامنظم با لبههای تیز) است. پودر فلزاتی مانند آهن، مس و آلیاژهای آن، آلومینیوم و آلیاژهای آن، آلیاژهای کبالت، قلع، فولاد زنگنزن و ابزار و سوپرآلیاژها به این روش قابل تولید هستند. تفاوت این روش با دیگر روشها در این است که میتوان پودر آلیاژهای همگن یا به عبارت دیگر مواد پیشآلیاژ شده را تولید کرد.
روشهای فرآیند اتمیزهکردن عبارتند از: اتمیزاسیون گازی، اتمیزاسیون با سیال (آبی یا روغن)، اتمیزاسیون با نیروی گریز از مرکز، اتمیزاسیون در خلا، اتمیزاسیون التراسونیک و اتمیزاسیون نوسانی که به توضیح هریک میپردازیم.
اتمیزاسیون گازی (Gas Atomization)
اتمیزاسیون گازی به خصوص برای تولید پودرهای سوپرآلیاژ استفادههای بسیاری دارد. در این روش، از یک گاز متراکمشونده استفاده میشود که با فشار زیاد، به جریانی از فلز مذاب اعمال شده و باید تولید دانههایی بسیار ریز و همگن میشود. دانهها در حین حرکت سرد و منجمد شده و در محفظهای جمعآوری میشوند. برای این کار، معمولا از گازهایی مثل هلیم، ازت، آرگون و هوا استفاده میشود.
اتمیزاسیون آبی (Water Atomization)
اتمیزاسیون با آب متداولترین روش برای تولید پودر فلزات و آلیاژهایی است که نقطه ذوب زیر 1600 درجه سانتیگراد دارند. این روش مشابه اتمیزاسیون گازی است، با این تفاوت که سرعت انجماد در این روش بالاتر بوده و ویژگیهای عامل متلاشیکننده مذاب نیز با حالت پیشین متفاوت است.
سیستم اتمیزه آبی شامل واحد ذوب، پاتیل واسطه، محفظه اتمیزهکننده و سیستم گردش آب و واحد رطوبتزدا است.
اتمیزاسیون گریز از مرکز (Centrifugal Atomization)
نیاز به کنترل اندازه دانههای پودر و همچنین اشکالات موجود در تولید پودر فلزات فعال منجر به توسعه این روش شده است. در این روش، نیروی گریز از مرکز به صورت ورقهای نازک باعث پرتاب دانههای فلز مذاب و انجماد آنها به صورت پودر میگردد. میزان تولید پودر در این روشها نسبت به روشهای اتمیزاسیون با سیال بسیار کمتر و محدودتر است. هزینه تولید پودر در روش گریز از مرکز بسیار بالا بوده و نسبت به روشهای گازی و سیال بهرهوری انرژی بالایی دارد.
اتمیزاسیون در خلا (Vacuum atomization)
از فلز مذاب که با گاز هیدروژن اشباع شده است و از طریق یک افشانک به محفظه خلا وارد میشود، در این روش استفاده شده که در اثر متلاشی شدن، فلز مذاب به دانههای ریز پودر تبدیل میشود.
اتمیزاسیون التراسونیک (Ultrasonic Atomization)
در این روش فلز مذاب در معرض ارتعاشدهنده التراسونیک قرار میگیرد.
اتمیزاسیون نوسانی (Swinging Atomization)
در روش نوسانی، ضربهها به صورت مکانیکی و نوسانی به مذاب اعمال میشوند.
روش شیمیایی
روشهای شیمیایی برای تولید تمامی فلزات مورد استفاده قرار میگیرند. تولید پودر در این روش، شامل واکنشهای فاز جامد، مایع و گاز است که به بررسی آنها میپردازیم.
الکترولیز
پودر فلزات را ميتوان تحت شرایط مناسب بر سطح کاتد یك ظرف الکترولیز رسوب داد. مزیت این روش خلوص بالای فرآوردههای پودری است. در این روش، ماده اولیه در سطح آند حل شده و در سطح کاتد رسوب ميکند. رسوب متخلخل از سطح کاتد جمعآوری، شسته، خشك و در آخر آسیا شده و برای زدودن هرگونه سختشدگي، تحت عملیات آنیل قرار میگیرد. یك فرایند مشابه دیگر، تهنشینسازی گالوانیکي یونهای محلول از طریق تزریق یك فلز واکنشپذیرتر به محلول است.
احیا در حالت جامد
مواد اولیه در این روش، اکسیدها یا نمکهای فلزی (کربناتها، هالیدها و …) هستند که در طبیعت یافت میشوند. در ابتدا مواد ذکر شده خالص شده و در ادامه، توسط عوامل احیا کننده دز دماهای زیر نقطهی ذوب تحت فرایند قرار میگیرند.
مراحل فرایند عبارتند از:
- آمادهسازی ماده خام (مخلوط کردن، آسیاکردن، خشککردن و چربیزدایی)
- احیای ماده
- تولید پودر (آسیاکردن، طبقهبندی و مخلوط کردن)
این روش بیشتر در مورد تولید پودر آهن، مس، تنگستن و مولیبدن به کار میرود. در این روش، عملیات احیا در سه دما قابل انجام است:
- دمای بالای احیا (Tm 6/0 <)
- دمای احیا پایینتر (Tm 6/0 > T > Tm 3/0)
- دمای احیا خیلی پایین (Tm 3/0 >)
رسوب از فاز گازی
اساس روش رسوب از فاز گازی، رسوب ذرات فاز بخار فلزات یا ترکیب آنها است. دو روش متداول رسوب از فاز گازی، روش رسوبدهی شیمیایی بخار (CVD) و رسوبدهی فیزیکی بخار (PVD) است.
روش رسوبدهی شیمیایی بخار شامل جریان گاز یا گازهای پیشماده در یک محفظه است که در این محفظه، یک یا چند سطح گرم که قرار است پوششدهی شوند، وجود دارد. در این روش، واکنشهای شیمیایی بر روی سطوح گرم رخ داده و در نتیجه رسوب به صورت لایهای نازک بر روی زیرلایه تشکیل میشود.
رسوبدهی فیزیکی بخار یک تکنیک پوشش با استفاده از تبخیر است که در آن، مواد از یک منبع جامد یا مایع به شکل اتم یا مولکول تبخیر میشوند و بخار در محیط خلاء، گاز فشار پایین و یا پلاسما زیرلایه را در برمیگیرد.
از ویژگیهای روش رسوب از فاز گازی میتوان به تولید پودرهایی با خواص مورد نظر، تولید پودرهایی از فلزات فرار (روی، کادمیوم، سرب و منیزیم) و اقتصادی بودن آن اشاره کرد.
تجزیه حرارتی کربنیلهای فلزی
کربنیلهای فلزی ترکیباتی با نقطه ذوب پایین و فرارند که در مولکول آنها، گروههای CO توسط کربن به اتمهای فلز پیوند خوردهاند. اساس این روش سنتز کربنیل به صورت واکنش فلز خالص یا ترکیبات حاوی فلز با مونوکسید کربن در فشارهایی بین 1/0 تا 20 مگاپاسکال و دمای 47 تا 277 درجه سانتیگراد است.
سپس کربنیلهای فلزی تولید شده، در اثر حرارت به کربن مونوکسید و فلز تجزیه میشوند. تجزیه حرارتی کربنیلهای فلزی یک فرایند گرماگیر بوده و با افزایش مقدار محصول پیشرفت میکند؛ به همین دلیل مناسب برای استفاده در فشارهای پایین و دماهای بالا است. واکنش تجزیه حرارتی کربنیلهای فلزی به صورت زیر است:
Mx Bz + y CO → Mx (CO)y → x M + y CO
از مزایای این روش میتوان به مصرف کامل ماده خام، نیاز کم به انرژی و قابلیت اجرا به صورت تمام اتوماتیک اشاره کرد. یکی از معایب این روش این است که برای تعداد محدودی از فلزات قابل انجام است.
خواص پودر فلز تولید شده به چه عواملی بستگی دارد؟
اندازه و توزیع ذرات
شکل ذرات عمدتاً به روش تولید پودر بستگی دارد. ذرات کروی شکل خاصیت سینترینگ عالی دارند و ذرات نامنظم برای قالبگیری مناسب هستند. بیشتر از پودرهای سایز 100میکرون استفاده میشود.
چگالی
چگالی ظاهری به عنوان جرم پودر در واحد حجم واقعی پر شده توسط پودر تعریف میشود که بستگی به شکل ذرات دارد. پودرهای با چگالی ظاهری بالا نیاز به فشردهسازی کمتری دارند تا پودرهای فشردهای با چگالی و اندازه معین ایجاد کنند.
نرخ جریان
به این صورت تعریف میشود که زمان لازم برای خروج مقدار اندازهگیری شده پودر از سرعت جریان استاندارد باید بیشتر باشد تا نرخ تولید بالا به دست آید.
تراکمپذیری و نسبت تراکم
هر دو به اندازه شکل و توزیع اندازه ذرات بستگی دارند. تراکمپذیری را میتوان نسبت حجم اولیه پودر (حجم فشرده نشده) به حجم نهایی استحکام خام پودر تعریف کرد. این معیار به عنوان مقاومت مکانیکی قطعهی فشرده شده نیز شناخته میشود.
مخلوط کردن (Mixing)
این عمل به معنای ترکیب پودرها با اندازههای مختلف و حالت شیمیایی یکسان بوده که برای تهیه ترکیبات جدید آلیاژی انجام میشود. در مخلوطکردن رایج است که یک روانکننده با پودر مورد نظر مخلوط شده تا خوردگی به حداقل مقدار خود برسد و خارج کردن آن پس از فشردهسازی آسان باشد. مخلوط ایدهآل، مخلوطی است که همه ذرات به طور یکنواخت پخش و توزیع شده باشند.
عوامل موثر در مخلوطکردن مواد پودری عبارتند از: جنس و اندازه دانهها، نوع و اندازه مخلوطکن، حجم نسبی پودر در مقایسه با حجم مخلوطکن و سرعت و زمان مخلوطسازی. همچنین عوامل محیطی از قبیل رطوبت نیز بر سهولت مخلوطسازی تاثیرگذار است.
فشردن پودر (Compaction)
هدف از فشردهسازی، تولید قطعات در قالب شکل نهایی است. این قطعات با نام محصولات خام شناخته میشوند.
در مرحله نخست، در اثر تغییر آرایش دانهها و سر خوردن آنها برروی یکدیگر، نقاط تماس افزایش یافته و باعث فشردهسازی بیشتر میشود که این امر چگالی پودر را در اثر تغییر شکل مومسان افزایش داده و باعث ایجاد کارسختی میشود.
فشردن پودر اغلب موارد به کمک دو سنبه که یکی در بالا و دیگری در پایین قالب قرار میگیرند، انجام میشود. فشردن پودر با اعمال فشار از طرف هر دو سنبه انجام میشود و پس از پایان کار، سنبه بالایی از محفظه قالب خارج شده و سنبه پایینی قطعه را بیرون میاندازد. هنگامی که فشار از طریق دو سنبه وارد گردد، فشردن اصطلاحا دوطرفه نامیده شده و اگر فشار از طرف یک سنبه وارد شود، شکلدهی یکطرفه خواهد بود.
در ابتدای کار، پودر همان چگالی خود را دارد و فضاهای خالی بین دانههای پودر آزاد زیاد و عدد همسایگی دانهها کوچک است. نخستین واکنش پودر در برابر فشار خارجی تغییر آرایش دانهها و پر شدن حفرههای بزرگ است که منجر به کاهش فضای خالی و تماسهای جدید بین دانهها میشود. با افزایش تعداد نقاط تماس و همچنین مساحت سطح تماس بین دانهها، تخلخل کاهش مییابد.
علاوه بر روشهای گفته شده، ممکن است فشار از همه جهات به قالب وارد شود که آن را پرس ایزواستاتیک (Isostatic Pressing) مینامند.
پرس ایزواستاتیک (Isostatic Pressing)
پرس ایزواستاتیک روشی است که پودر در قالب با شکل معین توسط فشار هیدواستاتیک فشرده میشود. با توجه به درجه حرارت، این پرس به دو نوع تقسیمبندی میشود:
1) پرس ایزواستاتیک سرد (CIP)
2) پرس ایزواستاتیک گرم (HIP)
در روش سرد، پودر فقط فشرده شده و مجددا باید در درجه حرارت بالا پخت شود؛ اما در روش گرم، فشردهشدن و پخت با هم انجام میشوند.
پرس ایزواستاتیک سرد (CIP)
یکی از روشهای شکلدهی به روش متالورژی پودر است که در آن فشارهای مساوی در دمای محیط و در تمام جهات بر پودر فلز وارد میشود. در این روش، قالبی انعطافپذیر از پودر پر شده و تحت تاثیر فشار ایزواستاتیک قرار میگیرد. این فشار به کمک سیالی مثل آب که قالب را احاطه کرده است، تامین میشود.
اساس کار به این صورت است که قالب مورد نظر در محفظه قرار گرفته و سطح سیال بالا میآید. سپس درب بالایی محفظه بسته شده و آب وارد محفظ میشود تا جایگزین هوا شود. پس از آن، سیستم آب را فشرده کرده و منجر به کاهش حجم پودر و فشرده شدن قطعه میشود. پس از فشردن کامل، فشار حذف شده و آب از محفظه خارج میگردد.
پرس ایزواستاتیک گرم (HIP)
این پرس شامل اتوکلاوی با دیوارهی سردشونده است که در آن گازی مانند آرگون در فشاری حدود 100 مگاپاسکال جهت پرس استفاده میشود. تجهیزات سیستم شامل کوره، مخزن فشار و سیستم گاز و برق است. اساس کار به این صورت است که پودر فشرده شده در داخل قالب قرار داده شده و قالب در محفظهی HIP قرار میگیرد. سپس تحت فشار و حرارت لازم قرار گرفته و نگهداری میشود. سپس فشار وارده حذف شده و دما کاهش پیدا کرده و قطعهی مورد نظر با سرعت سرد کردن متناسب از قالب خارج میشود.
تفجوشی (Sintering)
زینترینگ عبارت است از حرارتدادن پودر در دمایی زیر ذوب فلز، به طوری که در این دما پودرهای فلزی پیوند برقرار میکنند. سینترینگ دانهها از طریق حرکتهای اتمی که به انرژی سطحی دانههای پودر فائق میشوند، انجام میگردد. هر چه دانههای پودر کوچکتر باشند، مساحت ویژه آنها بیشتر شده و انرژی بیشتری خواهند داشت. در نتیجه زودتر زینتر میشوند.
در یک جامد بلوری تقریبا هر تماس بیندانهای یک مرزدانه به وجود میآورد که با نوعی انرژی مرزدانهای همراه است. مرزدانهها در جابهجایی اتمی بسیار حائز اهمیت بوده و دارای نقصهای بسیاری هستند و تحرک اتمی آنها بسیار زیاد است. برای پودرهای فلزی سازوکارهای زینترینگی که مسیرهای حرکت اتمی را توصیف میکنند، معمولا فرآیندهای نفوذی در روی سطح، در امتداد مرزدانهها یا از درون شبکه بلوریاند.
مراحل سینترینگ
مرحله 1: هنگام مجاورت دو ذره، تماس اولیه برقرار شده و نیروهای بین اتمی عمل خواهند کرد. در این هنگام رشد گردنه تابع کاهش انرژی آزاد سطح است. مکانیزمهای نفوذ سطحی، انتقال از مرز، نفوذ شبکهای از روی مرز و نابهجاییها موجب رشد گردنه در این مرحله میشود.
مرحله 2: این مرحله در سینترینگ نقش اساسی دارد. همانطور که با رشد دانه تراکم بیشتر میشود، حفرهها صافتر شده و به صورت کروی و بسته در میآیند. در این مرحله، رشد گردنه ادامه پیدا میکند. در این مرحله، حفرهها به سمت مرزدانه حرکت کرده و در آن متمرکز میشوند و سطوح آنها کاهش مییابد، بهطوری که در نهایت سطح ذرات به 50 درصد نسبت به قبل از مرحله اولیه سینترینگ میرسد.
مرحله 3: در این مرحله، حفرههای کرویشکل از مرز جدا میشوند و با افزایش زمان سینترینگ، ابعاد ذره و خلل و فرج افزایش یافته و درصد تخلخل کم میشود. کاهش تخلخل به چگالی، شعاع تخلخل و نفوذ حجمی وابسته است. افزایش زمان و درجه حرارت موجب تاثیرات منفی از قبیل انقباض بیشتر، رشد دانهها و بالارفتن هزینه میگردد و افزایش فشار نیز سایش ابزار را در پی دارد.
نقاط تماس بین دانههای پودر در اثر رشد به گلویی تبدیل شده و پس از مرحله نخست، وضعیت شکل مرزدانه و حفره، آهنگ سینترینگ را کنترل میکند. در ابتدای مرحله دوم، هندسه حفرهها بسیار پیچیده است و حفرهها در محل تقاطع مرزدانهها قرار دارند. در اثر ادامه سینترینگ، هندسه حفرهها به سمت استوانه میل کرده و کوچکشدن شعاع حفرهها موجب چگالش میشود. در مرحله سوم، هندسه حفرهها میتوانند رشد دانهها را کند کنند و به همراه مرزدانههای در حال حرکت و رشد کشیده شده و حرکت نمایند.
چرا متالورژی پودر؟
- گاهی اوقات به دلیل محدودیتهای ابعادی، هندسهی قطعه یا نوع آلیاژ مورد استفاده، استفاده از روشهای دیگر ممکن نیست. برای مثال جهت تولید رشتههای مقاومت بسیار کوچک لامپ که از تنگستن بسیار سخت تهیه میشوند، روشهای دیگر غیر قابل استفاده بوده و منحصرا باید از تکنولوژی متالورژی پودر استفاده کرد.
- برای تهیه آلیاژهایی از دو فلز که نقطه ذوبشان با یکدیگر تفاوت زیادی دارند (مانند مس و تنگستن)، بهترین راه عملی روش متالورژی پودر است.
- برای تولید قطعاتی که از ترکیب فلزات و غیر فلزات استفاده میشود، این روش ارجحیت دارد.
- به دلیل قابلیت اتوماسیون و سرعت بالا، صرفه اقتصادی بالایی دارد.
- قابلیت دسترسی به رنج وسیعی از ترکیبات وجود داشته و ضایعات ماشینکاری حذف شده یا به حداقل مقدار خود میرسد.
- امکان نرخ تولید بالا از 500 تا 1000 قطعه در ساعت در طول فرایند وجود داشته و تولید قطعههای پیچیده و خاص آسان میشود.
متالورژی پودر چه محدودیتهایی دارد؟
- محدودیت در اندازه و شکل قطعات تولیدی وجود دارد. اندازه و شکل
- قیمت مواد اولیه مورد استفاده در مقایسه با سایر روشهای تولیدی بالاتر است.
- تجهیزات مورد استفاده معمولا گران هستند و برای تولید در مقیاس کم مناسب توجیه اقتصادی ندارند.
- به دلیل اکسیداسیون ذرات در سطح و درون قطعه، میزان تخلخل قطعات تولیدی بالاست.
- معمولا در اثر ایجاد تخلخل در قطعات، سطح آنها زبر میشود.
متالورژی پودر در صنعت امروز چه جایگاهی دارد؟
اهمیت متالورژی پودر در صنعت امروز بر کسی پوشیده نیست. اهمیت این روش، در تولید قطعات پیچیده و ساخت محصولاتی با کیفیت عالی است که با استفاده از روشهای دیگر، این قابلیت وجود ندارد. با توجه به گستردگی کاربرد این تکنولوژی، نمیتوانیم تمامی موارد را در این مطلب کوتاه ذکر کنیم. اما برای درک اهمیت این روش، تعدادی از کاربردهای برجستهی این روش را در صنایع گوناگون ذکر کردهایم.
خودرو: چرخدنده، یاتاقان، بوشها، ذغالهای استارت و دینام، بادامکها، پیستون، کمک فنر و هسته استاتور دینام
ماشینآلات صنعتی: قطعات مورد استفاده در ماشینآلات نساجی و دیگر ماشینهای صنعتی
هوا فضا: موتورهای جت، نازل راکتها و موشکها و حفاظهای گرمایی
جوشکاری: لحیم، الکترود جوشکاری و فیلتر جوشکاری
مغناطیس: رله، مگنت و هسته
پزشکی: آمالگامهای دندانی، پنس و انبرک جراحی
عملیات حرارتی: ترموکوپل، کورهها و سینیهای حمل
متالورژی: بازیابی فلزات، ساخت کامپوزیت و آلیاژسازی
صنایع پلاستیک: قالب پرکننده، ابزارآلات و سطوح سایشی
چاپ: جوهر، پوشش و ورقههای چندلا
بوشهای الکتریکی موتورها از ترکیب مواد فلزی و غیرفلزی، چرخهای سنگزنی با استفاده از فولاد و پودر الماس از دیگر قطعاتی هستند که به روش متالورژی پودر تولید میشوند.
جمعبندی
متالورژی پودر روشی برای ساخت و تولید به روش شکلدهی قطعات فلزی و سرامیکی است که اساس آن بر فشردن پودر مواد به شکل مورد نظر و سینترینگ آن است. در این روش، فلز تلف شده به مراتب کمتر از سایر روشها است. در حال حاضر، مهندسی پودر بیشتر در مواردی مورد استفاده قرار میگیرد که در ساختن محصولاتی با کیفیت عالی از مواد مناسب، کلیه روشهای دیگر غیر ممکن باشند. متالورژی پودر به دلیل قابلیت اتوماسیون و سرعت بالا به ویژه برای قطعات کوچک و متوسط در تولیدهای انبوه صرفه اقتصادی خوبی دارد. همچنین دقت ابعاد و سطح قطعات ساخته شده با این روش، آن قدر عالی و بدون نقص است که هیچگونه کار اضافی دیگر روی قطعات ضرورت پیدا نمیکند و سرمایهگذاری برای صنعت متالورژی پودر به مراتب کمتر از سرمایهگذاری برای روشهای کلاسیک ساخت قطعات است.
در انتهای این مطلب، کتب فارسی و لاتین مختلفی برای علاقه مندان به متالورژی پودر (Powder Metallurgy) قرار داده شده است.
دانلود فقط با IP ایران امکانپذیر است. در صورت عدم مشاهده باکس قرمز رنگ دانلود، VPN خود را خاموش نموده و صفحه را رفرش کنید.
پسورد فایل فشرده : www.iran-mavad.com
دیدگاه کاربران
ممنون بابت سایت عالی و فایل های خوبی که قرار میدین.
سلام.چند تا سوال تخصصی در مورد متالورژی پودر دارم.اگه خودتون کار عملی متالورژی پودر کردین یا کسی رو معرفی کنین تا کمکم کنه ممنون میشم ازتون
با سلام . لینک های دوم و سوم و چهارم مشکل دانلود دارند. ممنون میشم اگه رفع کنید.
حل شد