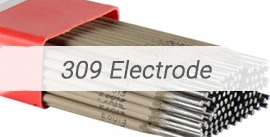
انواع روش های ریختهگری چدن نشکن (داکتیل)
در این مقاله، ابتدا به معرفی چدن داکتیل و دلایل نامگذاری آن پرداخته میشود. سپس روشهای مختلف ریختهگری، مزایا و معایب هر روش، تأثیر فرآیندها بر خواص مکانیکی و شیمیایی، و در نهایت، کاربردهای صنعتی و پیشرفتهای تکنولوژیک در این زمینه بررسی خواهد شد. با ما همراه باشید تا با یکی از مواد کلیدی در صنعت مدرن آشنا شوید.
چدن داکتیل چیست و چرا به آن چدن نشکن میگویند؟
چدن داکتیل، که به نام چدن نشکن نیز شناخته میشود، یکی از گریدهای پیشرفته چدن است که به دلیل خواص مکانیکی بهینه و استحکام بالا، در صنایع مختلف کاربرد دارد. وجه تمایز اصلی این نوع ، ساختار گرافیتی آن است که به جای صفحات یا فلسهای گرافیتی (مشابه چدن خاکستری)، به صورت کروی یا گلولهای شکل میگیرد. این آلیاژ آهنی شامل ترکیبات اصلی آهن، کربن (حدود 3-4%) و سیلیسیم (حدود 1.8-3%) است. علاوه بر این، افزودن عناصر آلیاژی مانند منیزیم (Mg) یا سریم (Ce)در فرآیند تولید، باعث تغییر ساختار گرافیتی از حالت صفحهای به کروی میشود. گرافیت کروی در ساختار چدن داکتیل، انعطافپذیری و مقاومت در برابر شکست را افزایش میدهد. این تغییر ساختار گرافیتی باعث توزیع یکنواختتر تنشها در ماده شده و مانع از تمرکز تنش و ایجاد ترک میشود. به همین دلیل، این نوع چدن برخلاف چدن خاکستری که شکننده است، خاصیت نشکن بودن دارد.
ترکیب شیمیایی چدن داکتیل
چدن داکتیل از عناصر مختلفی تشکیل شده است که هر کدام نقش خاصی در خواص مکانیکی و متالورژیکی آن ایفا میکنند.
عنصر | درصد وزنی (%) | نقش |
کربن (C) | 3.6 – 3.2 | تشکیل گرافیت و ماتریس؛ افزایش سیالیت مذاب. |
سیلیسیم (Si) | 2.8 – 2.2 | کمک به کرویسازی گرافیت؛ افزایش مقاومت به اکسیداسیون. |
منیزیم (Mg) | 0.06 – 0.03 | کرویسازی گرافیت؛ بهبود خواص مکانیکی. |
منگنز (Mn) | 0.3 – 0.1 | بهبود استحکام و سختی؛ جلوگیری از رشد دانهها. |
گوگرد (S) | حداکثر 0.02 | کاهش اثر منفی بر کرویسازی. |
فسفر (P) | حداکثر 0.05 | بهبود سیالیت؛ اما در مقادیر بالا تردی را افزایش میدهد. |
خواص مکانیکی چدن داکتیل
خواص | مقدار | توضیحات |
استحکام کششی (Tensile Strength) | 400 تا 800 مگاپاسکال | در صنایع خودروسازی برای قطعاتی مانند میللنگ و شاتون که نیاز به مقاومت به کشش دارند. |
مقاومت به ضربه ((Impact Resistance) | 7 تا 12 ژول بر میلیمتر مربع | برای قطعاتی که تحت بارهای ضربهای قرار دارند، مانند اتصالات خطوط لوله و قطعات ماشینآلات سنگین. |
چقرمگی (Toughness) | چدن داکتیل به دلیل انعطافپذیری بالا، چقرمگی خوبی ارائه میدهد. | گرافیت کروی اجازه تغییر شکل بدون شکست را فراهم میکند. |
سختی (Hardness) | گرافیت کروی اجازه تغییر شکل بدون شکست را فراهم میکند. 150تا 300 برینل (HB) | ساختار میکروسکوپی شامل ماتریس (پرلیت یا فریتی) و درصد کاربیدها سختی را تعیین میکند. |
مدول الاستیسیته (Elastic Modulus) | حدود169 گیگاپاسکال | این ویژگی نشاندهنده توانایی ماده در بازگشت به شکل اولیه پس از اعمال نیرو است. |
مقاومت به خستگی (Fatigue Resistance) | خوب | مناسب برای قطعاتی که تحت بارهای متناوب و دینامیکی قرار دارند، مانند قطعات موتور |
روشهای ریختهگری چدن داکتیل: از سنتی تا مدرن
ریختهگری چدن داکتیل به دلیل نیاز به کنترل دقیق ساختار گرافیتی و توزیع عناصر آلیاژی، فرآیندهای متنوعی دارد. در این فرآیندها، تبدیل گرافیت فلسمانند (مانند چدن خاکستری) به گرافیت کروی با افزودن عناصر کرویکننده مانند منیزیم یا سریم انجام میشود. در ادامه، روشهای اصلی ریختهگری این نوع چدن از سنتی تا پیشرفته معرفی شدهاند:
الف– روشهای سنتی و رایج ریختهگری چدن داکتیل: روشی است که فاقد فناوریهای مدرن کنترل فرآیند است تجهیزات ساده دارد و عمدتاً وابسته به مهارت اپراتور و مناسب برای تولید قطعات عمومی یا تولیدات کمحجم است.
1- ریختهگری ماسهای (Sand Casting)
2- روش پاتیل روباز (روریزی) (Open Ladle Method (Pour-Over Method))
3- روش ساندویچی (Sandwich Method)
4- روش افزودن مواد کرویکننده در قالب (In-Mold Treatment Method)
5- روش فروبری (Plunging Method)
6- روش فن سقوط مستقیم (Direct Drop Method)
ب- روشهای پیشرفته و خاص ریختهگری چدن داکتیل : روشی است که در آن از تجهیزات مدرن، فناوریهای دیجیتال یا فرآیندهای بهینه برای کنترل دقیقتر و بهبود کیفیت استفاده میکنند و مناسب برای تولید قطعات پیچیده، حساس، یا تولید انبوه با دقت بالا است.
1- ریختهگری دقیق (سرامیکی) (Investment Casting (Ceramic Mold Casting))
2- ریختهگری گریز از مرکز (Centrifugal Casting)
3- روش تزریق سیم حاوی آلیاژهای منیزیم (Wire Inoculation Method (Magnesium Alloy Wire Injection))
4- روش پاتیل درپوشدار (Covered Ladle Method)
5- روش کنورتور جورج فیشر (George Fischer Converter Method)
6- روش توپی متخلخل (Porous Plug Method)
7- روش پاتیل فشاری و محفظه فشاری (Pressurized Ladle Method and Pressure Chamber Method)
در ادامه هر کدام از روشها به اجمال توضیح داده میشود.
ریختهگری ماسهای (Sand Casting)
ریختهگری ماسهای یکی از رایجترین روشها برای تولید قطعات چدن داکتیل است. این روش به دلیل انعطافپذیری در طراحی، هزینه نسبتاً پایین قالبسازی و امکان تولید قطعات بزرگ یا پیچیده بسیار پرکاربرد است. در این روش، مذاب چدن به درون قالب ماسهای ریخته میشود. ماسه قالب معمولاً از سیلیس و چسب ساخته میشود و ماسه استفادهشده میتواند بازیافت و دوباره مصرف شود. این روش برای قطعات بزرگ یا پیچیده که نیاز به تولید در تیراژ کم دارند، کاربرد دارد و از مزایای آن میتوان به هزینه پایین قالبسازی و انعطافپذیری در تولید قطعات متنوع اشاره کرد. نکته ای که حائز اهمیت است، امکان ترکهای حرارتی و کیفیت سطح پایینتر در چدنهای ریخته شده با این روش وجود دارد.
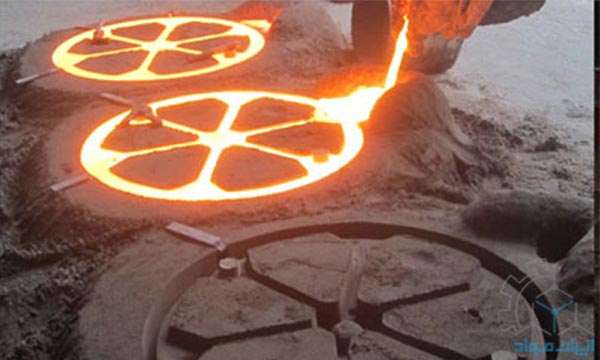
روش پاتیل روباز-روریزی (Open Ladle Method; Pour-Over Method)
روش پاتیل روباز یا روریزی یکی از سادهترین و رایجترین روشها برای تولید چدن داکتیل است. این روش عمدتاً در کارگاههای کوچک و برای تولیدات با حجم پایین استفاده میشود. در این روش، مواد کرویکننده مانند فروسیلیس منیزیم مستقیماً به مذاب اضافه شده و در یک پاتیل روباز واکنش انجام میشود. روش پاتیل روباز (روریزی)، به دلیل سادگی و هزینه پایین، انتخابی مناسب برای تولید قطعات عمومی و سبک در مقیاس کوچک است. اگرچه این روش کنترل کمتری بر واکنشها دارد و ممکن است کیفیت سطحی پایینتری ارائه دهد، همچنان در بسیاری از صنایع جایگاه خود را حفظ کرده است.
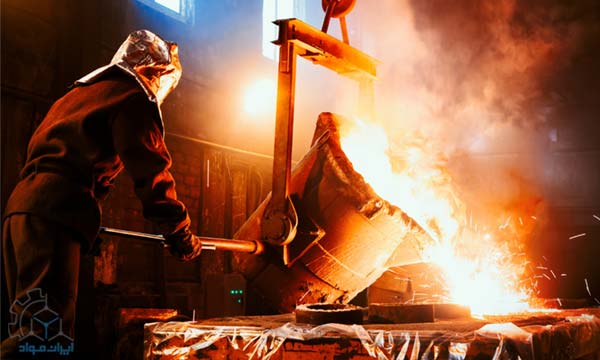
روش ساندویچی (Sandwich Method)
روش ریختهگری ساندویچی یکی از روشهای رایج و کارآمد و اقتصادی برای تولید چدن داکتیل است که به دلیل کنترل بهتر واکنش کرویسازی و کاهش هدررفت مواد کرویکننده، در صنایع مختلف کاربرد دارد. این روش به نام ساندویچی شناخته میشود زیرا مواد کرویکننده در کف پاتیل قرار میگیرند و مذاب به آرامی روی آنها ریخته میشود، شبیه به لایههای یک ساندویچ. در این روش، سرعت و نحوه ریختن مذاب بسیار مهم است و کوچکترین اشتباه میتواند باعث نقص در کرویسازی شود. همچنین نسبت به روشهایی مانند تزریق سیم، زمان بیشتری برای کرویسازی نیاز دارد.
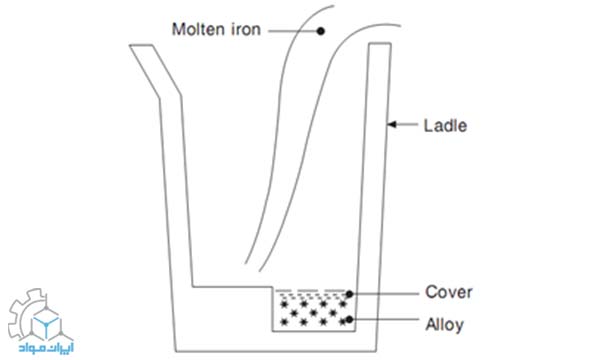
ریخته گری چدن داکتیل به روش ساندویچی
ریخته گری چدن داکتیل به روش ساندویچی ریخته گری چدن داکتیل به روش ساندویچی...روش افزودن مواد کرویکننده در قالب (In-Mold Treatment Method)
روش افزودن مواد کرویکننده در قالب یکی از روشهای کارآمد و اقتصادی برای تولید چدن داکتیل است که بهویژه در تولید قطعات کوچک و متوسط استفاده میشود. در این روش، مواد کرویکننده مستقیماً در داخل قالب قرار داده میشوند و قالب باید دارای حفرههایی برای قرار دادن مواد کرویکننده در نقاط مشخص باشد و واکنش کرویسازی هنگام روریزی مذاب انجام میگیرد. ممکن است مواد کرویکننده با یک لایه نازک از مواد گدازآور یا ماسه نسوز پوشانده شوند تا واکنش بهصورت کنترلشده انجام شود. از مزایای این روش، کاهش هزینه و هدررفت مواد کروی کننده و سادگی فرایند و تجهیزات کمتر است ولی کنترل محدود واکنش و کیفیت نامناسب برای قطعات بزرگ و ایجاد حبابهای گازی در قطعه نهایی از معایب این روش است.
روش فروبری (Plunging Method)
روش فروبری یکی از روشهای موثر و رایج برای تولید چدن داکتیل است که در آن مواد کرویکننده به مذاب اضافه میشود و با هم زدن یا غوطهوری در مذاب، واکنش کرویسازی انجام میشود. این روش به دلیل کنترل ساده و امکان استفاده در تولیدات مختلف، در بسیاری از کارگاهها و کارخانههای ریختهگری کاربرد دارد. در این روش، ابتدا مواد در کوره ذوب میشوند و سپس به داخل پاتیلی که پیشگرم شده و مواد کروی کننده در کف آن ریخته شده است، ریخته میشوند. علیرغم هدررفت منیزیم و خروج گازها، این روش، همچنان بهعنوان یکی از سادهترین و اقتصادیترین روشها برای تولید چدن داکتیل است و یک گزینه مطلوب برای تولید قطعات چدن داکتیل با کیفیت مناسب در حجم بالا شناخته میشود.
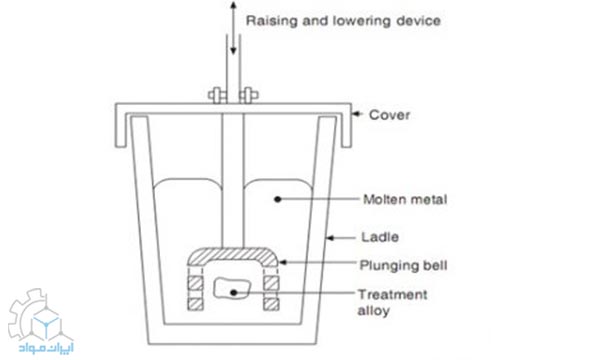
روش فن سقوط مستقیم (Direct Drop Method)
روش فن سقوط مستقیم یکی از روشهای اقتصادی و سریع برای تولید چدن داکتیل است که در آن مواد کرویکننده مستقیماً از ارتفاع مشخصی (معمولاً چند متر بالاتر از سطح مذاب) به داخل پاتیل از پیش گرم شده حاوی مذاب ریخته میشوند. این روش با استفاده از نیروی گرانش و تماس مستقیم مواد کرویکننده با مذاب، واکنش کرویسازی را بهسرعت انجام میدهد. با این حال، به دلیل هدررفت بالای منیزیم و کنترل دشوار واکنش، این روش عمدتاً برای تولید قطعات عمومی و کمدقت استفاده میشود. اگرچه این روش ساده و کمهزینه است، اما نیاز به دقت بالایی دارد تا کیفیت مطلوب حاصل شود.
ریختهگری دقیق (سرامیکی) (Investment Casting (Ceramic Mold Casting))
ریختهگری دقیق یا سرامیکی (Investment Casting) یکی از پیشرفتهترین روشهای ریختهگری است که برای تولید قطعات پیچیده، کوچک یا با دقت بالا استفاده میشود. این روش به دلیل استفاده از قالبهای سرامیکی و امکان دستیابی به ابعاد دقیق و کیفیت سطح بالا، برای تولید قطعات خاص بسیار کاربردی است. در این روش، مدل اولیه معمولاً از موم یا پلاستیک ساخته میشود و شکل قطعه نهایی را تقلید میکند. راهگاهها و تغذیهها نیز از جنس موم یا پلاستیک به مدل اضافه میشوند و چندین مدل ممکن است روی یک شاخه مرکزی (مانند درخت) مونتاژ شوند تا چند قطعه بهطور همزمان ریختهگری شوند. از معایب این روش میتوان به زمانبر و گران بودن مراحل آمادهسازی و قالبسازی سرامیکی، پایین بودن سرعت تولید و به صرفه نبودن تولید قطعات بسیار بزرگ اشاره کرد.
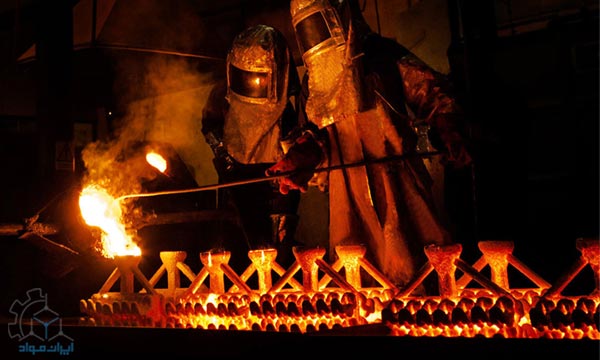
روش ریختهگری گریز از مرکز چدن داکتیل (Centrifugal Casting)
ریختهگری گریز از مرکز یکی از روشهای پیشرفته برای تولید قطعات تقارنمحور مانند لولهها، سیلندرها، و بوشها است. در این روش، مذاب چدن داکتیل به یک قالب چرخان ریخته میشود و نیروی گریز از مرکز، مذاب را به سمت دیواره قالب هدایت میکند. این فرآیند باعث تولید قطعات با کیفیت بالا، توزیع یکنواخت مواد و کاهش عیوب داخلی میشود.
انواع چدن با قابلیت ماشینکاری بالا
چدنها از جمله آلیاژهای صنعتی کاربردی هستند که به دلیل ویژگیهای فیزیکی و مکانیک...از مزایای این روش، توزیع یکنواخت مواد و حذف ناخالصیها و در نتیجه کیفیت سطح عالی و کاهش هزینههای ماشینکاری به دلیل نیروی گریز از مرکز است. از محدودیتهای این روش میتوان به این مورد اشاره کرد که این روش تنها برای قطعات تقارنمحور مناسب است و تجهیزات آن هزینه بالایی دارند.
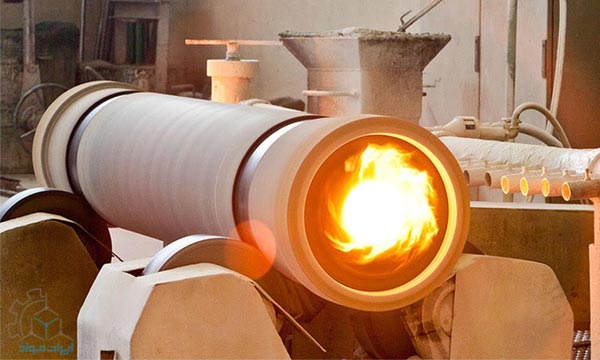
روش تزریق سیم حاوی آلیاژهای منیزیم (Wire Inoculation Method)
روش تزریق سیم حاوی آلیاژهای منیزیم (Magnesium Alloy Wire injection) یکی از دقیقترین و پیشرفتهترین روشهای تولید چدن داکتیل است. در این روش، دستگاه مخصوصی برای تزریق سیمهایی که حاوی آلیاژهای کرویکننده مانند منیزیم هستند، در پاتیل نصب میشود. این دستگاه سیم را با سرعت مناسب به داخل مذاب هدایت میکند و مستقیماً به داخل مذاب تزریق میشوند. این روش به دلیل کنترل بهتر واکنش کرویسازی، کاهش هدررفت مواد و امکان اتوماسیون، در تولید قطعات چدن داکتیل با کیفیت بالا بسیار کاربرد دارد. به دلیل هزینه بالای تجهیزات تزریق سیم و نیاز به تخصص این روش برای تولیدات کوچک و کمحجم اقتصادی نیست.
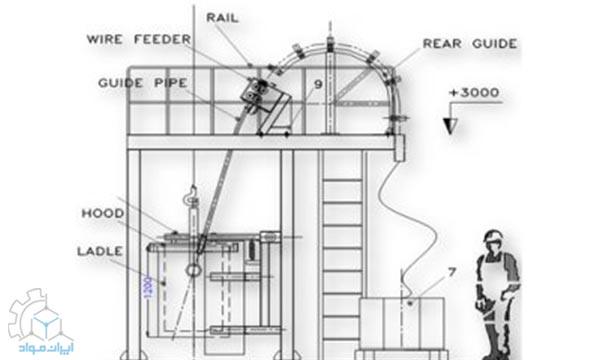
روش پاتیل درپوشدار (Covered Ladle Method)
روش پاتیل درپوشدار یکی از پیشرفتهترین روشهای ریختهگری چدن داکتیل است که برای کنترل واکنش کرویسازی و بهبود بازده مواد کرویکننده طراحی شده است. در این روش، یک پاتیل با درپوش مخصوص استفاده میشود که از هدررفت منیزیم ناشی از اکسیداسیون جلوگیری میکند. این روش بهویژه در تولید انبوه قطعات چدن داکتیل مورد استفاده قرار میگیرد. از آنجاییکه واکنش کرویسازی در یک محیط بسته انجام میشود، کیفیت و یکنواختی مذاب تضمین میشود و احتمال خطرات ناشی از گازها کاهش مییابد. از محدودیتهای این روش میتوان به موارد زیر اشاره کرد: 1- طراحی و استفاده از پاتیلهای درپوشدار هزینهبر است. 2- نصب و استفاده از درپوش و تجهیزات مرتبط نیازمند آموزش و تجربه است. 3- به دلیل زمان بیشتری که برای کنترل واکنش و جابجایی نیاز است سرعت پایینتری نسبت به روشهای باز دارد.
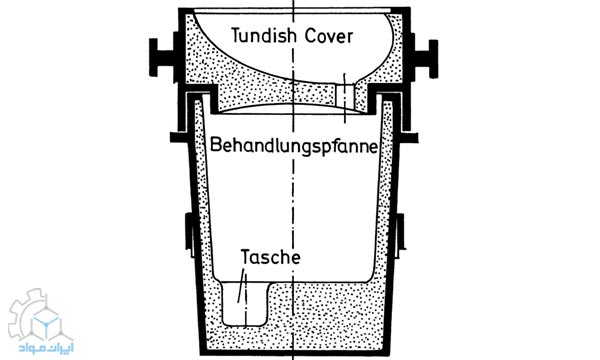
روش توپی متخلخل (Porous Plug Method)
روش توپی متخلخل یکی از روشهای پیشرفته برای تولید چدن داکتیل است که در آن از یک توپ متخلخل حاوی مواد کرویکننده استفاده میشود. این توپ به گونهای طراحی شده است که مواد کرویکننده را بهتدریج و بهصورت کنترلشده در تماس با مذاب آزاد میکند. توپ در کف پاتیل یا در یک محفظه مخصوص داخل پاتیل قرار میگیرد و ممکن است با لایهای از مواد گدازآور پوشیده شود تا واکنش بهصورت تدریجی انجام شود. این روش برای کاهش هدررفت منیزیم و کنترل بهتر واکنش کرویسازی طراحی شده است و توزیع مواد کرویکننده در مذاب یکنواختتر است. هرچند این روش برای قطعات بزرگ یا تولید انبوه ممکن است محدودیت داشته باشد، اما برای تولید قطعات کوچک و متوسط با کیفیت بالا گزینهای ایدهآل است. همچنین، ممکن است واکنش تدریجی زمان بیشتری نسبت به روشهای دیگر نیاز داشته باشد و هزینه تولید و استفاده از توپ متخلخل نیز نسبت به روشهای ساده تر بیشتر باشد.
روش کنورتور جورج فیشر (Georg Fischer Converter Method)
روش کنورتور جورج فیشر یکی از پیشرفتهترین و دقیقترین روشهای تولید چدن داکتیل است که در آن فرآیند کرویسازی و ریختهگری به صورت کاملاً کنترلشده و خودکار درون دستگاه کنورتور انجام میشود. فرآیند کاملاً کنترلشده در کنورتور باعث یکنواختی و کیفیت بالای قطعات تولیدی میشود و به دلیل طراحی سیستم بسته و مدیریت دقیق واکنشها، هدررفت منیزیم به حداقل میرسد. به دلیل هزینه بالای تجهیزات پیچیده و خودکار کنورتور و نیاز به تخصص این روش برای تولید انبوه و یکنواخت قطعات با کیفیت بالا بسیار مناسب است و عمدتاً در صنایع بزرگ و پیشرفته مورد استفاده قرار میگیرد.

روش پاتیل فشاری و محفظه فشاری (Pressurized Ladle Method and Pressure Chamber Method)
روش پاتیل فشاری یا محفظه فشاری یکی دیگر از پیشرفتهترین و دقیقترین روشها برای تولید چدن داکتیل است که در آن از یک محفظه یا پاتیل تحت فشار استفاده میشود. این روش به دلیل کنترل دقیق واکنش کرویسازی و کاهش هدررفت مواد کرویکننده مانند منیزیم، در تولید قطعات با کیفیت بالا کاربرد فراوان دارد. در این فرآیند، مواد کرویکننده در کف محفظه یا پاتیل قرار میگیرند و درپوش محفظه بسته میشود تا از خروج گازها و هدررفت مواد جلوگیری شود و سپس مذاب از کوره به آرامی وارد محفظه فشاری میشود و واکنشها تحت فشار انجام میشود. به دلیل هزینه بالای تجهیزات و سیستم کنترل و نیاز به تخصص، این روش برای تولیدات کوچک و کمحجم اقتصادی نیست.
انتخاب بهترین روش ریخته گری چدن داکتیل
روش ریختهگری باید بر اساس ویژگیهای موردنیاز قطعه و هزینههای تولید انتخاب شود. برای قطعات حساس با استحکام و چقرمگی بالا، روشهای پیشرفته مانند محفظه فشاری یا ریختهگری دقیق مناسبتر هستند، در حالی که برای قطعات عمومی با هزینه پایین، روشهایی مانند ریختهگری ماسهای کفایت میکنند. در جذول زیر به طور خلاصه روشهای مناسب ذکر شده است:
ویژگی مکانیکی | روش پیشنهادی |
استحکام کششی بالا | محفظه فشاری، ریختهگری گریز از مرکز |
سختی بالا | ریختهگری دقیق، گریز از مرکز |
مقاومت به ضربه بالا | محفظه فشاری، تزریق سیم |
چقرمگی بالا | پاتیل درپوشدار، محفظه فشاری |
کیفیت سطح عالی | ریختهگری دقیق (سرامیکی)، ریختهگری گریز از مرکز |
قطعات بزرگ و ارزان | ریختهگری ماسهای، افزودن مواد کرویکننده در قالب |
چالشهای ریختهگری چدن داکتیل: مشکلات و راهکارها
ریختهگری چدن داکتیل به دلیل خواص مکانیکی عالی و مزایای اقتصادی، در صنایع مختلف بسیار مورد توجه است. با این حال، چالشها و محدودیتهای خاصی در تولید، کنترل کیفیت و بهرهبرداری از آن وجود دارد که بسیاری از آنها در روشهای ریختهگری بیان شد اعم از دشواری در کنترل واکنش کرویسازی، ایجاد حفرات گازی، انجماد ناهمگن، پیچیدگی تجهیزات پیشرفته، محدودیت در تولید قطعات بزرگ و پیچیده، عیوب سطحی و مصرف بالای انرژی. با وجود چالشهای عملیاتی، محدودیتهای فناورانه و مسائل زیستمحیطی، ریختهگری چدن داکتیل همچنان یکی از فرآیندهای کلیدی در تولید قطعات صنعتی است و با استفاده از فناوریهای پیشرفته، طراحی بهینه فرآیندها و آموزش نیروی کار، میتوان بر این چالشها غلبه کرد و کیفیت، کارایی و پایداری فرآیند تولید را افزایش داد. برای این منظور، راهکارهای کلی برای بهبود این چالش ها در ادامه آمده است:
- استفاده از فناوریهای پیشرفته: سرمایهگذاری در روشهایی مانند تزریق سیم، ریختهگری دقیق و گریز از مرکز برای بهبود کیفیت و کاهش هزینهها.
- بهبود طراحی قالب و سیستم راهگاهی: طراحی مهندسیشده قالبها برای کاهش تنشهای حرارتی و افزایش یکنواختی انجماد.
- آموزش نیروی انسانی: آموزش مداوم کارکنان برای بهرهبرداری بهتر از تجهیزات و کاهش خطاهای عملیاتی.
- پایش مداوم کیفیت: استفاده از ابزارهای پیشرفته برای کنترل لحظهای دما، ترکیب شیمیایی و ساختار میکروسکوپی مذاب.
- مدیریت زنجیره تأمین: تأمین مواد اولیه باکیفیت و استفاده از مواد کرویکننده با بازده بالا.
کاربردهای صنعتی چدن داکتیل: ارتباط مستقیم با روشهای تولید
چدن داکتیل به دلیل ویژگیهای مکانیکی و شیمیایی منحصر به فرد، مانند استحکام کششی بالا، مقاومت به ضربه، و انعطافپذیری، در صنایع مختلف کاربرد گستردهای دارد. هر یک از این کاربردها ارتباط مستقیمی با روشهای تولید و فرآیندهای ریختهگری دارند. انتخاب روش تولید مناسب، نقش مهمی در بهینهسازی ویژگیهای قطعات چدن داکتیل برای کاربردهای صنعتی ایفا میکند.
صنعت | کاربردها | روش تولید پیشنهادی |
خودروسازی | میللنگ، دیسک ترمز | گریز از مرکز، محفظه فشاری |
ماشینآلات سنگین | چرخدندهها، بدنهها | ماسهای، گریز از مرکز |
لولهسازی | لولهها و اتصالات | گریز از مرکز، افزودن کرویکننده در قالب |
نفت و گاز | شیرآلات، تجهیزات حفاری | دقیق، محفظه فشاری |
ساختمان | اتصالات سازهای، دریچههای فاضلاب | ماسهای، افزودن کرویکننده در قالب |
هوافضا | قطعات موتور، حلقههای تقویتی | دقیق (سرامیکی)، گریز از مرکز |
آینده ریختهگری چدن داکتیل: فناوریهای نوین و پیشرفتها
آینده ریختهگری چدن داکتیل به طور چشمگیری تحت تأثیر فناوریهای نوین قرار خواهد گرفت و این پیشرفتها به بهینهسازی فرآیند تولید، ارتقاء کیفیت قطعات و کاهش هزینهها متمرکز است. یکی از مهمترین تغییرات در این صنعت، اتوماسیون و هوش مصنوعی (AI) است که از سیستمهای هوشمند برای کنترل فرآیندها، پیشبینی عیوب و بهینهسازی تولید استفاده میشود. این فناوریها موجب کاهش خطاهای انسانی، افزایش دقت در کنترل دما، ترکیب شیمیایی و زمان واکنشها و در نهایت بهبود بهرهوری و کاهش زمان تولید میشوند. همچنین، چاپ سهبعدی (Additive Manufacturing) به عنوان یک نوآوری جدید در تولید قالبها و مدلهای دقیق برای ریختهگری در حال گسترش است. این روش دقت بالاتری در طراحی قطعات پیچیده به ارمغان میآورد و هزینهها و زمان تولید قالبها را کاهش میدهد. روشهای هیبریدی ریختهگری نیز که ترکیبی از فرآیندهای سنتی و فناوریهای نوین است، به بهبود کیفیت و دقت قطعات کمک میکند. علاوه بر این، سیستمهای پایش لحظهای (Real-Time Monitoring) که با استفاده از حسگرها و ابزارهای پیشرفته دما، ترکیب شیمیایی و جریان مذاب را به طور لحظهای کنترل میکنند، امکان نظارت دقیقتر بر فرآیند تولید را فراهم میکنند.
در کنار این نوآوریها، مواد پیشرفته و بهینهسازی ترکیبات شیمیایی نقش مهمی در توسعه آلیاژهای جدید دارند. این آلیاژها مانند ترکیبات نیکل-منیزیم و آلیاژهای سریم، بازده بالاتری برای کرویسازی گرافیت به ارمغان میآورند و کیفیت قطعات را بهبود میبخشند. همچنین، فناوریهای دوستدار محیط زیست مانند سیستمهای تصفیه گازهای خروجی و طراحی فرآیندهایی با آلایندگی کمتر در حال توسعه هستند که موجب کاهش اثرات منفی بر محیط زیست میشود. از دیگر پیشرفتها میتوان به بازیافت و بهینهسازی مواد خام اشاره کرد که در آن ضایعات چدن و قالبهای مصرفشده بازیافت میشوند تا هزینهها کاهش یابد و اثرات زیستمحیطی به حداقل برسد. استفاده از شبیهسازیهای پیشرفته نیز به کمک نرمافزارهای مدلسازی برای تحلیل جریان مذاب، انجماد و توزیع گرافیت، به بهینهسازی فرآیند ریختهگری کمک میکند. در نهایت، مدیریت دادهها و اینترنت اشیا (IoT) با اتصال تجهیزات ریختهگری به شبکه، امکان پایش و مدیریت دادههای تولید را فراهم میآورد که این امر میتواند به افزایش کارایی و کاهش خطاها در تولید کمک کند.
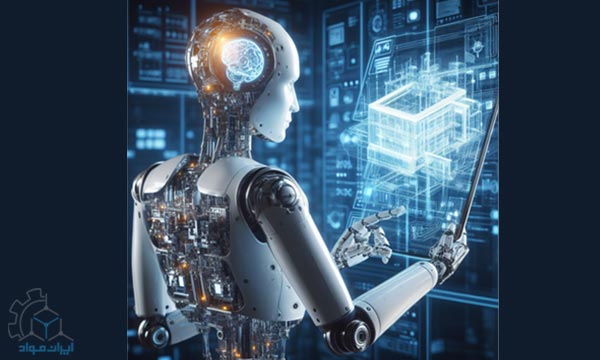
جمعبندی
چدن داکتیل به عنوان یکی از مواد کلیدی در صنایع مختلف، به دلیل خواص مکانیکی و شیمیایی برجسته، مانند استحکام کششی بالا، مقاومت به ضربه، انعطافپذیری، و چقرمگی، جایگاه ویژهای در تولید قطعات حساس و پرکاربرد دارد. با وجود این ویژگیها، ریختهگری چدن داکتیل با چالشهایی مانند کنترل واکنش کرویسازی، مدیریت گازها، تنشهای حرارتی، و بهینهسازی ترکیب شیمیایی روبهروست.
انتخاب روش ریختهگری مناسب، تأثیر مستقیمی بر کیفیت و عملکرد قطعات چدن داکتیل در صنایع دارد. برای مثال: در صنایع خودروسازی، روشهایی مانند ریختهگری گریز از مرکز برای تولید میللنگ و شاتون به دلیل یکنواختی ساختار و استحکام بالا ایدهآل هستند. در صنایع لولهسازی، ریختهگری گریز از مرکز قطعاتی با مقاومت به فشار و خوردگی تولید میکند. در صنایع نفت و گاز، روشهای پیشرفته مانند ریختهگری دقیق یا محفظه فشاری، قطعاتی مقاوم به حرارت و فشار بالا را ارائه میدهند.
دیدگاه کاربران