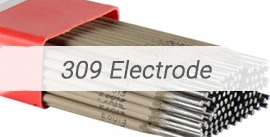
ریخته گری ثقلی (Gravity casting)
ریختهگری فرآیندی است که از دیرباز جایگاه ویژهای در بین روشهای تولید داشته است. ریختهگری را میتوان فن شکل دادن فلزات و آلیاژها از طریق ذوب، ریختن مواد مذاب در محفظهای به نام قالب و سرد کردن و انجماد آن مطابق شکل محفظه دانست. روشهای متعددی در زیرمجموعه فرآیند ریختهگری وجود دارند.
ریخته گری ثقلی (ریژه) (به انگلیسی Gravity casting) که عنوان آن کاملا نشاندهندهی حضور نیرو جاذبه در این فرآیند است جزو زیردسته ریختهگری دایکست است. بهطور کلی در این فرآیند فلز در حالت مذاب به داخل قالب ریخته شده و پس از انجماد از آن خارج میشود. ریختهگری دایکست در دو حالت ریختهگری تحت فشار و ریختهگری ثقلی انجام میشود. در ریخته گری دایکست تحت فشار pressure die casting، فلز مذاب، تحت فشار خارجی به داخل قالب تزریق میشود. این در حالی است که در ریخته گری ثقلی Gravity die casting، مواد مذاب توسط نیرو گرانشی به درون قالب جریان پیدا میکند. در ادامه به توضیح و بررسی فرآیند ریختهگری ریژه پرداخته خواهد شد.
ریخته گری ثقلی چیست؟
ریخته گری ثقلی یا Gravity casting یکی از رایج ترین فرآیندهای ریخته گری است. در این فرآیند فلز در حالت مذاب به کمک پاتیل و یا مخزن بهداخل حفرهی قالب ریخته میشود. سوراخ حفره در سطح بالایی قالب قرار گرفته است، به این علت که هیچ نیرویی جز نیرو جاذبه در پر کردن حفره قالب دخیل نباشد. میتوان از ریختهگری ریژه برای تولید قطعات مختلف مانند چرخدنده و قرقرههای ساده و اجزاء پیچیده همانند موتورهای خودرو استفاده کرد.
ریخته گری ثقلی به چه صورت انجام میشود؟
ریخته گری ثقلی شامل چندین مرحله اصلی میشود که اصول اجرای این فرآیند به شرح زیر است:
- در ابتدا دو نیمهی قالب حرارت داده شده و قبل اینکه دو نیمه بههم متصل شوند پوشش بر روی سطح آنها اسپری میشود.
روغنکاری و پاشش پوشش بر روی سطح قالب بهمنظور جلوگیری از انجماد زودرس و کمک به جدایش آسان قطعه ریختگی پس از انجماد از قالب است.
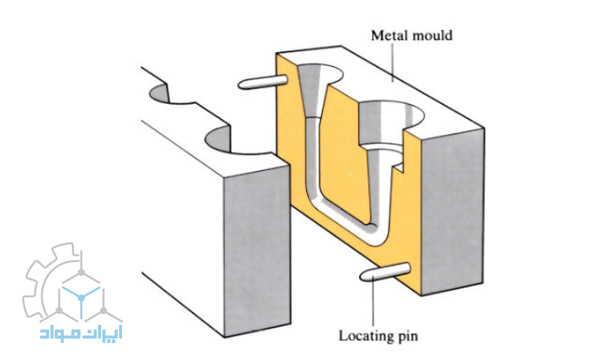
- سپس فلز موردنظر را در کوره ذوب کرده و بهکمک پاتیل بهدرون حفرهی قالب ریخته میشود که تحت نیرو جاذبه، حفره از مواد مذاب پر میگردد.
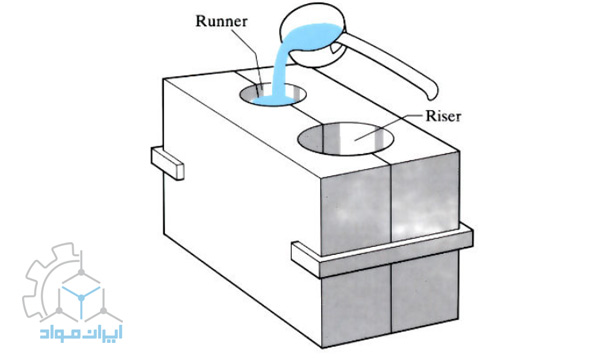
- انجماد سریع فلز در قالب رخ میدهد.
- دو نیمهی قالب بعد از انجماد فلز باز شده و قطعه از آن خارج میگردد و تمیزکاری قالب برای استفادهی بعدی آن انجام میشود.
- در نهایت در صورت لزوم ماشینکاری بر روی قطعه، ریختگی انجام میشود.
- لازم به ذکر است که در طول ریختهگری ثقلی، سرعت جریان مواد به داخل حفره قالب و سرعت انتقال حرارتی در طول انجماد باید کنترل شود.
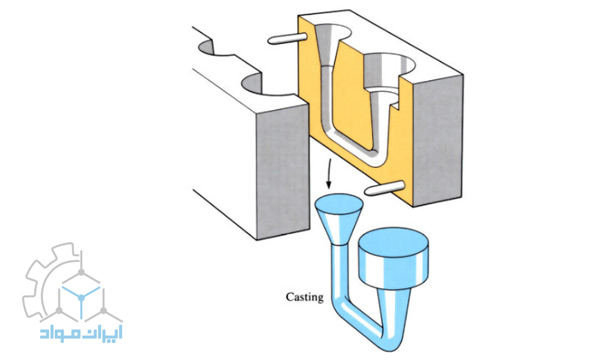
قالب مورداستفاده در این فرآیند میتواند هم قالب ماسهای باشد و هم قالب دائمی که به فرآیند ریخته گری در قالب ریژه (فلزی) نیز شناخته میشود.
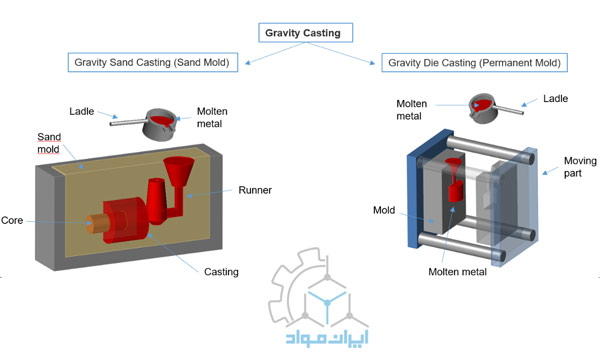
انواع مواد قالب ریخته گری ثقلی
مواد قالب ریختهگری ریژه دائمی از آلیاژهای مختلفی مانند آلومینیم، روی، منیزیم و مس تشکیل شده است. هر نوع فلزی مزایا و معایب خاص خود را دارد و با توجه به کاربرد انتخاب میشوند. بهعنوان مثال، آلومینیم دارای نقطه ذوب بالایی است که استفاده از آن را برای کاربرد دمای بالا مطلوب میکند. از طرف دیگر، «روی» فلزی انعطاف پذیر است و بهراحتی میتوان آن را به اشکال پیچیده تبدیل کرد.
همانطورکه در قسمت بالا ذکر شد هر یک از مواد با توجه به کاربرد انتخاب میشوند که در ادامه به توضیح مختصری از ویژگی های هر کدام از آنها اشاره شده است.
آلیاژهای آلومینیم نقطهذوب بالایی دارند و در برابر خوردگی از مقاومت مطلوبی برخوردار هستند. همچنین دارای رسانایی حرارتی و الکتریکی خوبی بوده و آنها را برای طیف وسیعی از کاربردها مناسب می کند.
آلیاژهای روی شکل پذیری بسیار خوبی دارند و بهآسانی میتوان آنها را به اشکال پیچیده درآورد. همچنین از مقاومت خوبی در برابر خوردگی برخوردار هستند و در مقایسه با سایر فلزات، نسبتا کمهزینه هستند.
آلیاژهای منیزیم دارای نسبت استحکام به وزن خوبیاند، در نتیجه سبکوزن بوده و میتوانند در کاربردهایی استفاده شوند که به اجزاء با وزن سبک موردنیاز است.
در نهایت، آلیاژهای مس رسانایی حرارتی و الکتریکی خوبی دارند و در برابر خوردگی مقاوم هستند.
انواع ریخته گری ثقلی
قطعات تولیدی با استفاده از فرآیند ریختهگری ثقلی با توجه به تجهیزات بهکاررفته میتواند به سه روش زیر تفکیک یابند:
- دستی
- نیمه اتوماتیک
- اتوماتیک
دستی
در این روش تمامی مراحل از ذوب ریزی تا مرحله ی خروج قطعه از قالب بهصورت دستی و بدون استفاده از دستگاه انجام میشود. از آنجاییکه تمامی مراحل بهصورت دستی بوده، لذا سرعت تولید پایین است و برای تولید انبوه مناسب نیست.
نیمه اتوماتیک
در این روش جهت بالابردن سرعت تولید، برای باز و بسته کردن قالب از سیستم هیدرولیکی استفاده میشود و تنها خروج قطعه از قالب توسط نیروی انسانی انجام میشود.
اتوماتیک
در این روش تمامی مراحل بهصورت خودکار و توسط دستگاه انجام می شود.
پیشنهاد میکنیم:
ریخته گری آلیاژهای آهنی
ریخته گری آلیاژهای آهنی شرح یکی از رایج ترین تقسیم بندی ها در رابطه با فل...نکات تکمیلی فرآیند ریخته گری ثقلی
- بازده فرآیند بستگی به طراحی سیستم راهگاهی دارد، اما معمولا 40% تا 60% است.
- قالبهای بزرگ که عمدتا برای آلیاژهای آلومینیم و منیزیم استفاده میگردند، معمولا با دست، مونتاژ و جدا میشوند. قالبهای کوچک، بهویژه برای ریخته گری آهنی بهطورخودکار جدا میشوند. طراحی قالب و فشار گیره بهگونه ای است که اعوجاج حرارتی کمی وجود دارد یا اصلا وجود ندارد.
- ریختهگری آهنی کوچک بهطور خودکار انجام میشود تا پاتیل و قالب در طول ریختن مذاب، کنترل شوند و تلاطم به حداقل برسد.
- نرخ تولید بهطور قابلتوجهی بسته به اندازه، طراحی و مواد مورداستفاده متفاوت است. نرخ معمول برای سرسیلندرهای آلومینیمی یک در هر پنج دقیقه است. اکثر ریختهگریهای آهنی در مقیاس کوچک و با طراحی ساده در صورت بهکارگیری، به روش اتوماتیک نرخ تولید بالایی دارند.
- در ریخته گری ثقلی ، فلز آهسته تر از ریخته گری تحت فشار وارد قالب میشود از این رو تلاطم کمتری وجود دارد و درنتیجه قطعهی ریخته گری متراکم تر خواهد بود.
- در این روش انرژی موردنیاز در حدود نصف ریختهگری ماسهای معمولی است. نشان داده شده که ریختهگری فولادی 15 تا 20 درصد ارزانتر از ریختهگری ماسهای است.
- طراحی سیستم راهگاهی (که میتواند در بالا، کنار و یا پایین باشد) مهم است، به این دلیل که بر تلاطم و عملکرد فلز تاثیر میگذارد.
- اندازهی قالب باید به اندازه کافی بزرگ باشد تا راهگاه و رایزر بهخوبی در آن جای بگیرد و فاصلهای در حدود 75-200 میلیمتر از بالای قالب داشته باشد. وزن مواد بسته به مواد و طراحی متفاوت است، اما برای ریخته گری آهنی معمولا 4-6 کیلوگرم تا 200 کیلوگرم است.
فاکتورهای تعیینکننده در انتخاب مواد قالب ریخته گری ثقلی
هنگام انتخاب مواد قالب ریخته گری ریژه برای کاربردهای مختلف، توجه به عوامل زیر حائز اهمیت است.
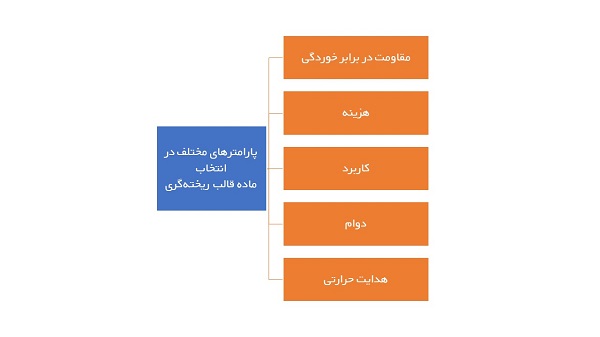
اشتباهات رایج در استفاده از مواد قالب ریخته گری ثقلی
هنگام کار با مواد قالب ریختهگری ریژه ، مهم است که از اشتباهات رایجی که میتواند منجر به تولید محصولات بیکیفیت شود اجتناب گردد. از مهمترین این موارد میتوان به موارد زیر اشاره کرد:
- عدم حفظ دمای قالب: اگر قالب در دمای مناسب نگهداری نشود، میتواند منجر به تولید محصولی بیکیفیت گردد.
- تمیز نکردن قالب: اگر قالب بهطورمرتب تمیز نشود، میتواند منجر به نقص در محصول نهایی و عمر پایین قالب گردد.
- عدم بازرسی قالب: اگر بررسی قالب بهطورمنظم انجام نشود و عیوب آن شناسایی نگردد در کیفیت محصول نهایی و دوام آن اثرگذار خواهد بود.
- تست نکردن محصول: اگر محصول نهایی موردآزمایش قرار نگیرد، هنگام سرویسدهی مشکلات زیادی را بههمراه خواهد داشت.
مزایای ریخته گری ریژه
- نیرویی بهجز نیروی گرانشی برای پر کردن داخل حفره با مواد مذاب دخیل نیست.
- قطعات ریختهگری ثقلی چگالی بهتری نسبت به قطعات ریختهگری ماسه ای دارند.
- این فرآیند نسبت به سایر فرآیندها مانند ریختهگری تحتخلاء و ریختهگری فشاری هزینه کمتری دارد.
- قطعات تخلخل کمتر و ساختار دانه بهتری نسبت به ریختهگری ماسهای دارد.
- قطعات دارای خواص مکانیکی خوبی هستند که برای عملیات حرارتی عالی است.
- سطح قطعات تحت این فرآیند پرداخت سطحی بهتری نسبت به سایر قطعات ریختهگری دارند.
- دقت ابعادی قطعات تولیدی بالا است و از ثبات ابعادی مطلوبی برخوردار هستند.
- این روش ریختهگری نسبت به روشهای دیگر، نیاز به هزینهی کمی دارد.
- قطعات ریختهگری با ابعاد کوچک و نازک بهآسانی قابل تولید هستند.
- قطعات تولید شده با این روش دارای کیفیت متالورژیکی بالا هستند.
معایب ریخته گری ثقلی
برخی از معایب این روش ریختهگری در تصویر پایین آمده است:
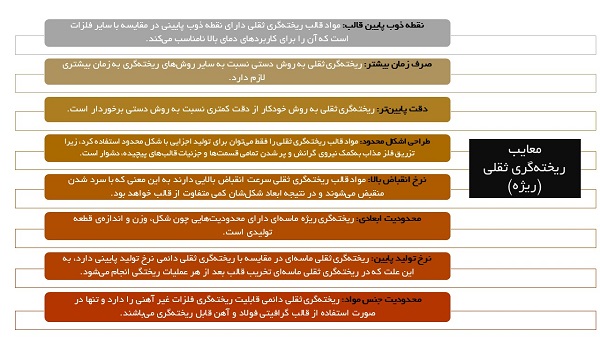
آیا ریخته گری ثقلی برای تولید انبوه مناسب است؟
زمانی که ریختهگری ثقلی برای اولینبار ابداع شد، از این روش برای تولید قطعات ساده به جای قطعات پیچیده استفاده میشد. اما با گذشت زمان و پیشرفت فناوری، اکنون تولیدکنندگان میتوانند قطعات پیچیده را با روش ریختهگری ثقلی تولید کنند. با این حال، اکنون روشهای پیشرفتهتری نسبت به روش ریخته گری ریژه برای تولید قطعات خاص وجود دارد. اما از آنجاییکه این روش کم هزینه بوده و ابزار و روش سادهتری نسبت به سایر روشهاست بنابراین، انتخاب ریختهگری ثقلی برای تولید انبوه قطعات ساده بهتر است. پُرواضح است که تولیدکنندگان درصورتیکه از این روش برای تولید حجم زیادی از قطعات پیچیده استفاده کنند بهصرفه نخواهد بود. لذا، در صورت ساخت قطعات با حجم تولید کم و یا متوسط، روش ریختهگری ثقلی انتخاب بهتری نسبت به سایر روشهای ریختهگری است.
کاربرد ریخته گری ریژه
تولید قطعات پیچیده با استفاده از روش ریخته گری ثقلی بهدلیل پیشرفت فناوری غیرممکن نیست. امروزه صنایع متعدد مانند خودروسازی، قطعات آشپزخانه و روشنایی از این فرآیند برای ساخت لوازم و قطعات مختلف استفاده میکنند. برخی از کاربردهای رایج ریخته گری ثقلی عبارتنداز:
قطعات خودرو مانند: پیستون، سرسیلندر و کالیپر ترمز
قطعات روشنایی مانند: محفظه نور LED
وسایل آشپزخانه مانند: قاشق و قابلمه.
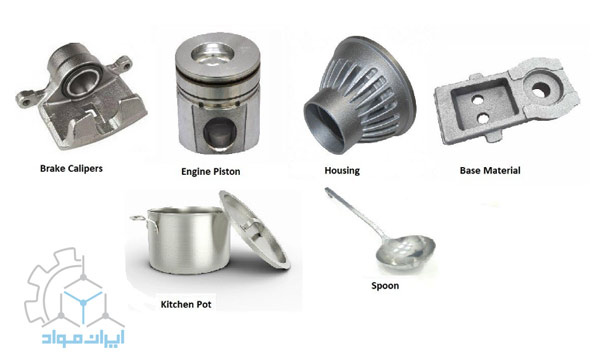
جمعبندی
ریخته گری ثقلی یکی از فرآیندهای ریخته گری است که مذاب تحت نیروی جاذبه و بدون حضور هیچ نیرو خارجی، محفظه قالب را پر میکند. قالب مورداستفاده در این فرآیند میتواند از نوع قالب ماسهای و یا دائمی باشد. کاملا واضح است که استفاده از قالب دائمی بهدلیل عدم تخریب آن منجر به افزایش سرعت و کاهش زمان تولید میشود. با اینکه این فرآیند با معایبی همراه است اما دارای مزایایی چون خواص مکانیکی بالا، دقت ابعادی و پرداخت سطحی بالا و هزینهی کم منجر به استفاده از این روش در صنایع مختلف شده است. بهطورکلی با رعایت نکاتی چون حفظ دمای قالب، تمیز کردن و بازرسی قالب میتوان قطعات با کیفیت بالا را تحت این فرآیند تولید کرد.
دیدگاه کاربران
مقاله جالب و مفیدی بود. تقریبا هر چیزی که درباره کلیت ریخته گری ثقلی باید میدونستیم رو گفته بود. ممنون از ایران مواد