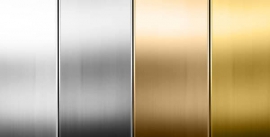
خوردگی دما بالا یا داغ چیست؟
خوردگی داغ چیست؟
به زبان ساده، خوردگی داغ را می توان نوعی از خوردگی دانست که بر اثر رسوب نمک ها و ترکیبات خورنده مذاب بر سطح آلیاژهای فلزی اتفاق می افتند. این نوع خوردگی، یکی از شایع ترین انواع خوردگی در توربین های گازی، موتورهای دیزلی، کوره ها و سایر تجهیزاتی است که به صورت مداوم در معرض محصولات احتراق سوخت های فسیلی یا مواد مذاب اسیدی قرار دارند. امروزه تحقیقات زیادی در جهت کاهش این نوع خوردگی انجام گرفته و معادلات متعددی در این زمینه ارائه شده اند، اما با این وجود خوردگی دما بالا سالانه هزینه های هنگفتی را بر روی دست صنایع و کارخانجات می گذارد.
خوردگی داغ به چه صورتی اتفاق می افتد؟
به طور کلی محصولات آلیاژی که در معرض سوخت ها و محصولات احتراقی ناشی از آن ها، مذاب های اسیدی و گازهای داغ مانند گازهای ترش قرار دارند، مستعد وقوع این نوع خوردگی هستند. اما اجازه دهید تا با ذکر مثالی ساده، نحوه وقوع این نوع خوردگی را توضیح دهیم:
در نیروگاه ها که توربین های گازی بر اساس انرژی ناشی از احتراق سوخت های فسیلی تولید انرژی می کنند، به صورت مداوم در معرض گازهای داغی قرار دارند که سطح آلیاژ فلزی را احاطه می کنند. سوخت های فسیلی اغلب دارای ناخالصی هایی مانند عناصر وانادیم، سدیم، پتاسیم و سولفات هستند که در حین احتراق، واکنش داده و به صورت ترکیباتی زود ذوب بر سطح آلیاژ رسوب می کنند.
بر روی سطح آلیاژهای فلزی معمولا یک لایه محافظ و چسبنده اکسیدی قرار دارد که این ترکیبات زود ذوب و نمک های ایجاد شده به آن ها حمله می کنند و با تخریب آن ها به سطح فلز نفوذ می کنند. نفوذ این ترکیبات ناخالصی به سطح فلز با تخریب شدید آن ها همراه خواهد شد.
خوردگی دما بالا معمولا زمانی تشدید می شود که رسوبات نمکی تشکیل شده بر سطح آلیاژ ذوب شوند تا شرایط برای نفوذ و تخریب مهیاتر باشد، گرچه مواردی هم وجود دارند که تشکیل رسوبات متراکم و جامد می توانند سبب خوردگی داغ در آلیاژ شوند.
در خصوص وقوع این نوع از خوردگی به واسطه رسوب نمک ها و ترکیبات ناخالصی، لازم است تا به چند سوال مهم پاسخ داده شود:
- نمک راسب شده چه سطحی از آلیاژ را پوشش می دهد؟
- ضخامت لایه تشکیل شده بر سطح آلیاژ چقدر است؟
- رسوب تا اندازه بر روی سطح چسبندگی دارد؟
- نقطه ذوب رسوب چقدر است و تا چه اندازه می تواند ذوب شود؟
- میزان ترشوندگی سطح آلیاژ با رسوب ایجاد شده چقدر است؟
معمولا نمک های اکسیدی، سولفاتی و کلریدی مانند K2SO4 ،Na2SO4 ،NaCl ،KCl و V2O5 از جمله متداول ترین نمک های مخربی هستند که در بحث خوردگی داغ مطرح می شوند. نمکهای مذاب سولفات سدیم Na2SO4 و کربنات سدیم Na2CO3 در توربین ها و راکتورها و نمک کلرید سدیم NaCl به علت فراوانی در آب دریا در کشتی ها غالبا باعث ایجاد این نوع از خوردگی می شوند.
خوردگی دما بالا عموما در دو مرحله اتفاق می افتد:
مرحله اول: شروع و جوانه زنی که کند و آهسته است.
مرحله دوم: گسترش خوردگی که به سرعت اتفاق میافتد.
1) مرحله شروع و جوانه زنی: تلاش برای در هم شکستن پوسته اکسیدی محافظ
در این مرحله گازهای داغی که در اثر احتراق ایجاد شده اند و حاوی ناخالصی هایی مانند ترکیبات سدیم، گوگرد، اکسیژن و … هستند، به صورت نمک هایی مانند سولفات سدیم بر سطح آلیاژ رسوب می کنند.
در طول مراحل نخستین، یک واکنش الکتروشیمیایی برقرار می شود که در طی آن عناصر فلزی موجود در آلیاژ الکترون از دست می دهند (اکسید می شوند) و این الکترون را عناصر احیا شونده ای مانند اکسیژن در رسوب دریافت می کنند. در اثر این تبادلات، یک لایه اکسیدی بین بستر آلیاژ و لایه نمکی رسوب می کند که خصوصیاتی مشابه لایه های اکسیدی معمولی دارد.
اما در ادامه عناصری مانند گوگرد با نفوذ به آلیاژ و واکنش با عناصری مثل نیکل، کروم، آلومینیوم و … آلیاژ را تهی می کنند. بدین ترتیب عناصری که مسئول حفاظت از سطح آلیاژ بودند، از ساختار آن خارج می شوند و لایه اکسیدی محافظی که چسبنده و متراکم بود، به یک ساختار متخلخل تبدیل می شود:
Na2SO4 + Ni (metal) → NiO (porous)
لازم به ذکر است که زمان اجرای این مراحل متغیر بوده و شروع خوردگی داغ می تواند از چند ثانیه تا هزاران ساعت به طول بینجامد. سرعت انجام این مراحل به عوامل زیر بستگی دارد:
- ضخامت لایه راسب شده
- ترکیب آلیاژ
- ترکیب و سرعت جریان گاز
پایان مرحله اول با نفوذ موضعی رسوب مذاب و پخش شدن آن در فصل مشترک پوسته اکسیدی – آلیاژ همراه است.
2) مرحله گسترش سریع خوردگی
با تشدید نفوذ عوامل خورنده به داخل پوسته اکسیدی محافظ، سرعت انحلال پوسته افزایش می یابد و با انحلال ترکیبات جدید در نمک های خورنده، قدرت خورندگی آن ها بیشتر می شود. نتیجه این است که عوامل خورنده با عبور از سد لایه محافظ اکسیدی، خود را به آلیاژ می رسانند و با شدت آن را تخریب می کند. به صورتی که آلیاژ بخش مهمی از عناصر ارزشمند خود مانند آلومینیوم و نیکل را در ترکیب با این عناصر از دست می دهد و مقاومت آن در دمای بالا از بین می رود.
معمولا نمک هایی که باعث خوردگی داغ می شوند، از دو جزء اسیدی و بازی تشکیل شده اند. برای مثال نمک نمک Na2SO4 از یک جز بازی Na2O (با یونهای O2-) و یک جزء اسیدی SO3 تشکیل شده است.
SO4-2 = ½ O2 + SO2 + O-2
در صورتی که پوسته محافظ با جزء بازی نمک یعنی Na2O واکنش دهد، به صورت عوامل آنیونی در نمک حل میشود. در این حالت گفته می شود که پوسته محافظ به صورت بازی در نمک حل شده است.
NiO + Na2O = 2Na+ + NiO22-
MO + O2- = MO22-
در صورتی که پوسته با جزء اسیدی نمک یعنی SO3 وارد واکنش شود، به صورت عوامل کاتیونی در نمک حل میشود. در این حالت گفته می شود که پوسته محافظ به صورت اسیدی در نمک حل شده است.
–NiO + SO3 + Ni2+ + SO42-
–MO = M2+ + O2-
این که لایه اکسیدی به صورت اسیدی یا بازی در نمک خورنده مذاب حل شود، بستگی به میزان یون اکسیژن موجود در نمک دارد. اگر غلظت یون اکسیژن در نمک زیاد باشد، اکسید به صورت بازی و در صورتی که غلظت یون اکسیژن کم باشد، به صورت اسیدی در نمک حل میشود. در تصویر زیر حل شدن بازی و اسیدی اکسید نیکل در نمک مذاب خورنده را مشاهده می کنید:
خوردگی داغ توسط نمکهای مذاب در درجه حرارتهای بالاتر از نقطه جوش یا پایینتر از درجه حرارت لیکوئیدوس
دانشــنـامه
لیکوئیدوس
چیست ؟
در نمودارهای فازی، خطی است که آغاز انجماد و یا پایان ذوب را برای یک آلیاژ نشان می دهد. بالای این خط، محلول به صورت مذاب، تک فاز و همگن است.
نمک اتفاق نمیافتد. بلکه معمولا در حد فاصل بین این دو دما به حداکثر می رسد. وقوع این نوع خوردگی تا حد زیادی به ترکیب شیمیایی نمک، اجزای تشکیل دهنده گازهای داغ و همچنین ترکیب شیمیایی آلیاژ وابسته است.
خوردگی داغ به دو صورت اتفاق می افتد …
به صورت کلی، خوردگی دما بالا را می توان به دو نوع تقسیم کرد:
- خوردگی داغ دمای بالا یا نوع اول (HTHC)
- خوردگی داغ دما پایین یا نوع دوم (LTHC)
تفاوت این دو نوع خوردگی داغ در محدوده دمایی است که اتفاق میافتند. اما وجه تشابه آن ها در این است که هر دو جریان نمکهای مذاب پوسته اکسیدی محافظی را که بر روی سوپر آلیاژ ایجاد شده بود، میشکنند و از این طریق موجب خوردگی در آلیاژ میَشوند. در تصویر زیر محدوده دمایی خوردگی داغ نوع اول و دوم را مشاهده می کنید.
خوردگی نوع اول یا دما بالا (HTHC)
این نوع خوردگی در محدوده دمایی 800 تا 900 درجه سانتیگراد به وقوع می پیوندد. اصلی ترین عامل این نوع از خوردگی را می توان به نمک های مذاب Na2SO4 نسبت داد که با تشکیل بر روی سطح آلیاژ، سبب تخریب آن می شوند. واکنش زیر نحوه تشکیل این نمک را نشان می دهد:
NaCl (aq) → Na + Cl
Na + S (fuel) → Na2SO4
حضور سدیم کلرید می تواند به وجود مقادیر بسیار کمی آب شور در سوخت مایع یا نمک آب دریا نسبت داده شود.
همان طور که ملاحظه می کنید، در نتیجه جدا شدن سدیم، کلر در سیستم باقی می ماند که با نفوذ به مرزدانه های آلیاژ فلزی، سبب خوردگی مرزدانه ای آن می شود. گوگرد نیز علاوه بر واکنش با سدیم و تشکیل نمک، به داخل پوشش آلیاژ نفوذ کرده و در ترکیب با عناصری مانند کروم، نیکل، تیتانیوم، آلومینیوم و … ترکیبات سولفیدی تشکیل می دهد و باعث تهی شدن پوشش از این عناصر می شود. این عمل ادامه پیدا می کند تا با تخریب لایه اکسیدی، ترکیبات خورنده به داخل آلیاژ نفوذ کنند. از آن پس اکسیداسیون و خوردگی داغ با شدت زیادی ادامه پیدا می کند.
به عنوان یک نتیجهگیری، خوردگی داغ نوع اول با تشکیل ذرات سولفیدی و همچنین نشانه هایی از خوردگی مرز دانهای همراه است.
خوردگی نوع دوم یا دمای پایین (LTHC)
خوردگی نوع دوم معمولا در محدوده دمایی 650 تا 800 درجه سانتیگراد اتفاق می افتد. در این روش، معمولا نمک مذاب لایه های اکسیدی محافظ را در هم می شکند و در ساختار نهایی مناطق تهی از عناصر آلیاژی به چشم می خورد. اما بر خلاف حالت قبل معمولا نشانه ای از حضور ذرات سولفیدی یا خوردگی مرزدانه ای مشاهده نمی شود، بلکه این نوع از خوردگی خود را به صورت حفرات ریز نمایان می کند.
برای اینکه این که خوردگی داغ نوع دوم اتفاق بیفتد باید فشار جزئی گاز داغ SO3 در محیط بالا باشد. نمونهای از خوردگی داغ نوع دوم در تجهیزات با دمای بالا در یک کشتی که در اثر رسوب نمکهای دریایی رخ داده، در تصویر زیر به نمایش درآمده است:
چگونه می توانیم با خوردگی داغ مقابله کنیم؟
روشهای زیادی وجود دارند که با اجرای مجموعه آن ها می توان مقاومت آلیاژ فلزی را در برابر خوردگی دما بالا افزایش داده و خسارت های ناشی از آن را به حداقل رساند. از جمله مهم ترین این روش ها می توان به کاهش ناخالصیهای موجود در سوخت، ساخت آلیاژهای مقاوم در برابر این نوع از خوردگی و پوشش دهی سطح قطعه اشاره کرد.
پوشش های سد حرارتی (Thermal Barrier Coatingas (TBC)) از متداول ترین پوشش هایی هستند که برای بالابردن مقاومت به خوردگی داغ قطعات آلیاژی و به ویژه پره های توربین گازی مورد استفاده قرار می گیرند. این پوشش ها سرامیکی هستند و به عنوان یک سد حرارتی برای جلوگیری از افزایش دمای زیرلایه عمل می کنند. زیرکونیا پایدار شده با ایتریا (YSZ) یکی از پرکاربردترین سرامیک ها در ساخت این پوشش ها است.
منابع
N. Birks, G. H. Meier, F. S. Pettit, Introduction to the high temperature oxidation of metals, Cambridge University Press, 2006.
M. G. Fontana, N. D. Greene, Corrosion engineering, McGraw-hill, 2018.
دانلود فقط با IP ایران امکانپذیر است. در صورت عدم مشاهده باکس قرمز رنگ دانلود، VPN خود را خاموش نموده و صفحه را رفرش کنید.
پسورد فایل فشرده : www.iran-mavad.com
دیدگاه کاربران
لطفا در کاربرد روشهای انتشار صوتی در خوردگی دما بالا نیاز به اطلاعات دارم