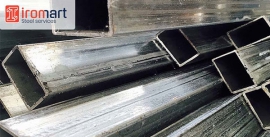
عملیات حرارتی چیست و با چه روش هایی انجام می شود؟
در حین فرآیند تولید و پس از فرآیند ریخته گری دقیق، ممکن است لازم باشد برخی از قطعات با روش هایی اصلاح شوند و ساختار دانه آنها تغییر کند. عملیات حرارتی یک نوع عملیات تکمیلی و یکی از روش هایی است که با استفاده از فرآیندهای کنترل شده گرمایشی و سرمایشی برای تغییر خصوصیات فیزیکی فلز و بهبود آنها در طیف وسیعی از صنایع استفاده می شود.
این فرآیند با توجه به نوع فلز و خصوصیات مکانیکی مورد نیاز قطعات، متفاوت است. برای اطمینان از دستیابی به استحکام مورد نیاز قطعه، ضروری است تمامی مراحل با دقت صورت گیرد.
در شرکت صنعت گستر، بسیاری از خدمات عملیات تکمیلی و سطحی ارائه می شود، از جمله عملیات حرارتی، که برای بالا بردن ارزش نهایی محصولات شما به کار برده می شود.
مزایای عملیات حرارتی
عملیات حرارتی معمولاً برای تغییر یا تقویت ساختار مواد از طریق فرآیند گرمایشی و سرمایشی انجام می شود. از جمله مزایای آن عبارتند از:
- این فرآیند می تواند خصوصیات فیزیکی (مکانیکی) ماده را تغییر دهد و در مراحل دیگر تولید کمک کند.
- تنش ها را از بین برده و باعث آسان تر شدن ماشین کاری یا جوشکاری می شود.
- باعث افزایش استحکام، چکش خواری و انعطاف پذیری قطعه می شود.
- ویژگی هایی مانند مقاومت در برابر سایش (سختی) را در سطح و یا درون قطعه، ایجاد میکند.
- شکنندگی را بهبود می بخشد. بعضی از فلزات پس از قرار گرفتن در یک محیط خاص ممکن است ضعیف یا شکننده شوند، بنابراین برای بهبود آن ها، نیاز به این فرآیند است.
- خصوصیات الکتریکی و مغناطیسی فلز را بهبود می بخشد، که باعث سازگاری آن با سایر مواد می شود.
فولادها به ویژه در فرآیندهای تولید مانند شکلدهی گرم یا پس از عملیات جوشکاری، با عملیات حرارتی اصلاح می شوند و بهبود میابند.
روش های اصلی عملیات حرارتی
نرماله کردن (Normalizing)
این تکنیک فقط برای آلیاژهای آهنی استفاده می شود و برای کاربردهایی که به یک ساختار پرلیتی یکپارچه و در سطح میکروسکوپی نیاز است، مفید می باشد. معمولاً برای آلیاژهای آهنی استفاده می شود که فولاد باید تا حدود 40 درجه سانتیگراد بالاتر از دمای بحرانی خود گرمتر شود، برای مدتی در آن دما نگه داشته شود و سپس در هوای آزاد سرد شود.
هدف نهایی این فرآیند افزایش استحکام فولاد، از بین بردن عیوب ساختاری، رفع تنش های داخلی و بهبود اندازه دانه است. موادی که نرماله شده اند سخت تر از مواد آنیل شده هستند. نرمال سازی، معمولاً آخرین مرحله آماده سازی قطعه فولادی برای استفاده های آتی می باشد. نرماله کردن در ریخته گری دقیق فولاد کربنی (کربن استیل) و ریخته گری دقیق فولادهای آلیاژی ضخیم، بزرگ و پیچیده مناسب تر است.
فرآیند آنیلینگ و آنیل انحلالی (Annealing & Solution Annealing)
آنیلینگ (بازپخت) به نوعی از عملیات حرارتی گفته می شود، که مواد تا دمای مورد نظر گرم شده و برای مدت مشخصی پیش از آنکه به آرامی یا به سرعت سرد شوند، در آن دما باقی می مانند. این فرآیند ریزساختار دانه قطعات را بهبود می بخشد. علاوه بر آن باعث یکنواخت سازی اندازه دانه ها نیز می شود. این مهم موجب می شود تا کارکردن با آنها نیز آسان تر شود. آنیلینگ همچنین باعث بهبود شکل پذیری مواد برای عملیات ماشینکاری و کاهش تنش های احتمالی ریخته گری می شود.
فرآیند آنیلینگ اغلب برای کاهش سختی ماده نیز استفاده می شود که به بهبود قابلیت ماشینکاری آن کمک می کند. این فرآیند برای آلیاژهای آهنی و غیر آهنی مناسب است. وقتی نوبت به آنیلینگ انحلالی می رسد، این فرآیند اگرچه از نظر دمایی به روش آنیلینگ شباهت دارد، اما معمولاً برای بهبود مقاومت فولادهای ضد زنگ سری 300 در برابر خوردگی و شکل پذیری مورد استفاده قرار می گیرد.
هر دو روش عملیات حرارتی آنیلینگ و آنیلینگ انحلالی اغلب در صنایع متالورژی، از جمله در فرآیند ریخته گری دقیق، استفاده می شود.
تمپر کردن (Tempering)
تمپر کردن عبارت است از حرارت دادن مجدد قطعات فولادی ریخته گری شده در دمایی مشخص و سپس آهسته سرد کردن در دمای محیط، این فرآیند معمولا پس از کوئنچ کردن (سردایش) یا نرماله کردن استفاده می شود. علت استفاده از عملیات حرارتی تمپرینگ این است که معمولا پس از کوئنچ کردن تنش های داخلی در قطعات ایجاد می شود. این تنش ها موجب تردی و شکنندگی شده، به همین علت باید قبل از آنکه فولاد مورد استفاده قرار گیرد تمپر شود؛ مگر در مواردی که سختی بالایی مورد نیاز باشد، در این صورت از فولاد کوئنچ شده استفاده می شود.
کوئنچ کردن، سردایش یا آبدهی (Quenching)
کوئنچ فرآیندی برای سرد سازی قطعات ریخته گری دقیق با سرعت بالا است. این کار اغلب برای تغییر به ساختار مارتنزیتی انجام می شود. در آلیاژهای آهنی، این فرآیند اغلب باعث تولید فلز سخت تری می شود، در حالی که آلیاژهای غیر آهنی معمولاً نرم تر از حد نرمال می شوند. برای ایجاد استحکام از طریق این فرآیند، باید قطعات ریخته گری دقیق (معمولاً فولاد یا چدن) را بالاتر از دمای بحرانی گرم کرده و سپس سریع خنک کرد. روشهای متداول آن عبارتند از خنک کننده آب، روغن و هوا و غیره.
توجه: بیشتر ریخته گری های فلزات غیر آهنی، مانند آلیاژهای مس، آلومینیوم، نیکل و برخی از ریخته گری های فولاد پرآلیاژ مانند ریخته گری دقیق فولاد ضد زنگ آستنیتی (304، 316)، هنگام کوئنچ، نتیجه عکس می دهند و نرم می شوند. استنلس استیل آستنیتی در ریخته گری دقیق باید کوئنچ شده تا کاملاً در برابر خوردگی مقاوم شود، به علت محیط کاری آنها که نیازمند سختی بالاست.
کربونیزه کردن یا کربن دهی سطحی (Carburizing)
کربونیزه کردن فرآیند هدایت عنصر کربن به سطح ریخته گری دقیق است. با تغییر در ترکیب کربن محصولات، سختی سطح و مقاومت در برابر سایش را تا حد زیادی بهبود می بخشند، اما هنوز کمی سختی در داخل قطعه باقی می ماند.
تمپر کردن و سخت کردن (Tempering & Hardening)
تمپرینگ و سخت کردن شامل دو مرحله می شود:
عملیات سخت کردن را می توان روی فولادهای خاصی که حاوی محدوده کربنی مشخص هستند، قبل از خنک کردن سریع یا کوئنچ کردن آن، انجام داد. نتیجه دستیابی به قطعاتی سبک تر و مستحکم تر می باشد که حتی در ساخت قالب های فلزی می توان با این عملیات مقاومت لازم در برابر سایش را بدست آورد. اگر یک قطعه از فولاد ضد زنگ مارتنزیتی ساخته شده باشد، تنها با این روش در برابر خوردگی می تواند مقاومت پیدا کند.
با استفاده از چرخه گرمایش و خنک سازی بعدی که با عنوان تمپر کردن نامیده می شود می توان میزان شکل پذیری قطعه را بهبود بخشید، در نتیجه باعث سخت شدن و ترک خوردگی کمتر در شرایط تحت فشار می شود. تمپرینگ باعث می شود تا قطعات سخت تر شوند.
این مراحل مهم در صنعت لوله ها و اتصالات استیل انجام می شود، زیرا ویژگی های مکانیکی فلزات را بهبود می بخشد و استفاده ایمن از آنها در خطوط لوله انتقال نفت، آب یا گاز را تضمین می کند. این روش عملیات حرارتی به طور معمول برای بهبود سختی داخلی و خارجی قطعات ریخته گری دقیق استفاده می شود.
سخت کاری پوسته (Case Hardening)
در روش سخت کاری پوسته، عناصر سخت کننده به سطح ریخته گری دقیق تزریق شده و باعث ایجاد یک لایه محافظ اضافی می شود. سخت کاری پوسته یک فرآیند ترموشیمیایی است که در آن عناصر آلیاژی، که عمدتا شامل کربن یا نیتروژن است، تا عمق خاصی به سطح فلز اضافه می شوند که فقط لایه بیرونی تحت تاثیر فرآیند سخت شود. این روش برای برخی از کاربردها مفید است زیرا به یک قطعه اجازه می دهد تا یک هسته شکل پذیر “نرم” با یک قسمت بیرونی بسیار سخت و مقاوم در برابر سایش داشته باشد.
نتیجه این فرآیند بهبود مقاومت در برابر سایش است اما شما خاصیت چقرمگی را نیز از دست نخواهید داد. این فرآیند ایده آل در انواع پروژه ها که در آن فشار و ساییدگی موجب نگرانی است، به کر گرفته می شود.
اثر فشار هیدرواستاتیک گرم (HIP= Hot Isostatic Pressing)
در این نوع عملیات حرارتی از گازهای بی اثر، معمولاً آرگون، در دمای بالا و فشار بسیار زیاد استفاده می کنند. این شرایط اجازه می دهد تا تغییر شکل پلاستیک، خزش و نفوذ رخ دهد. عملیات حرارتی HIP برای حذف ریز تخلخل های داخلی استفاده می شود که با فشرده سازی هرگونه مک گازی و تخلخل که در قطعه وجود دارد، خواص مکانیکی را بهبود می بخشد.
خواص عملیات حرارتی HIP آن را برای حذف ریز تخلخل در هر نوع فلز برای کاربردهایی با یکپارچگی بالا مانند موتورها و اجزای هواپیما ایده آل می کند. همچنین این ماده در صنعت پزشکی، جهت بهبود ایمپلنت های پایه کروم، تیتانیوم و فولاد ضد زنگ استفاده می شود.
سخت کاری القایی (Induction Harden)
سخت کاری القایی که اغلب برای فولاد و چدن استفاده می شود، از طریق حرارت القایی و کوئنچ کردن، باعث سخت شدن سطح یک قطعه فلزی می شود. سختی و شکنندگی مواد از طریق این فرآیند افزایش می یابد، که به شما این امکان را می دهد که بخش خاصی از یک قطعه را بدون تحت تاثیر قرار دادن بخش های دیگر، سخت کنید. این عملیات حرارتی از طریق عبور یک جریان متناوب با فرکانس بالا از یک سیم پیچ انجام می شود.
سخت کاری القایی باعث می شود سطح یک قطعه در برابر سایش مقاومت بیشتری داشته باشد و برخی بخش های خاص بدون آنکه نیاز به دخالت در فرآیند باشد سخت کاری شوند. سخت کاری القایی برای قطعات بزرگ نیز انتخاب مناسبی است.
عملیات حرارتی در خلا (Vacuum Heat Treatment)
این فرآیند بستری را فراهم می کند تا بتوان به اکثر عملیات های حرارتی مانند فرآیند کوئنچ کردن و آنیلینگ دست یافت. این نوع عملیات حرارتی کم فشار برای آلیاژهای مقاوم در برابر حرارت، از جمله آلیاژهای بر پایه نیکل مناسب است و به قطعات کمک می کند تا در محیط های با گرمای زیاد و سایر تنش ها بهتر مقاومت کنند. به همین دلیل، معمولاً در تولید قطعات بخش هایی مانند هوا فضا، عمدتا در موتورها و اگزوزها، مورد استفاده قرار میگیرد.
رسوب سختی (Precipitation Hardening)
رسوب سختی (که به آن پیرسختی نیز گفته می شود) روشی است که برای سخت کردن آلیاژهایی خاص استفاده می شود. معمولاً در این روش از آلیاژهایی چون فولاد ضد زنگ، آلومینیوم و مس استفاده می کنند. رسوب سختی یک روش آنیلینگ انحلالی است که در دمای بالا و به دنبال آن یک یا چند پیر سختی برای رسیدن به سختی مورد نظر، انجام می شود.
آیا در ریخته گری همیشه به عملیات حرارتی نیاز داریم؟
جواب کوتاه، خیر است. بعضی از قطعات آماده استفاده به عنوان “as cast” هستند، اما، بعضی اوقات، شما برای پروژه ای به یک قطعه نیاز دارید که نیاز به مشخصات خاصی دارد که با ریخته گری به خواص مورد نظر نمی رسید. این بدان معناست که اگر آلیاژی به هر طریقی همه ی ویژگی ها را به جزء مقاومت در برابر سایش داشته باشد، می تواند تحت عملیات حرارتی قرار گیرد تا این ویژگی را بدست آورد.
بنابراین، اگرچه هر ریخته گری یا قطعه ای به عملیات حرارتی نیاز ندارد، اما بسیاری از مواد می توانند از طریق آنها بهبود پیدا کنند، زیرا خواص فیزیکی و مکانیکی آن ها بهتر می شود.
در بالا روش های اصلی عملیات حرارتی برای ریخته گری دقیق ذکر شده است. عملیات حرارتی عمدتا با توجه به کاربرد قطعه ریخته گری دقیق انجام می شود. اگر با عملیات حرارتی آشنایی ندارید و یا در این خصوص به سوالی بر خورده اید، نگران نباشید. اگر محصولات شما به این فرآیند نیاز دارند، مهندسین و متخصصان صنعت گستر شما در این راه یاری می رسانند. برای تماس با ریخته گری دقیق صنعت گستر، تمامی راه های ارتباطی در صفحه “تماس با ما“ وبسایت وجود دارد.
دیدگاه کاربران
سپاسگزارم
ممنون از توجه شما
موضوع مقاله با متن فایل همخوانی ندارد.