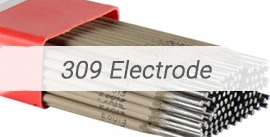
آلیاژ اینکونل، بی رقیب در مقاومت به حرارت و خوردگی
در این مقاله علاوه بر معرفی این آلیاژ و انواع آن، به محدودیتهای این آلیاژها، نظیر هزینه بالا و فرایندهای تولید پیچیده، مورد تحلیل قرار گرفته و به چشماندازهای آینده برای بهبود این ویژگیها پرداخته شده است.
تاریخچه توسعه و استفاده از اینکونل
توسعه آلیاژهای اینکونل از دهه 1930 آغاز شد، زمانی که صنایع نیازمند مواد مقاوم به حرارت و خوردگی شدند. اولین آلیاژهای نیکل-کروم توسط شرکت Special Metals Corporation معرفی شدند و به سرعت به دلیل ویژگیهای منحصربهفرد خود در صنایع مختلف محبوبیت یافتند. این آلیاژها در ابتدا برای حل مشکلات مرتبط با اکسیداسیون و خوردگی در تجهیزات گرمایشی و محیطهای شیمیایی طراحی شدند.
در طول جنگ جهانی دوم، نیاز به موادی که توانایی تحمل دماهای بسیار بالا و فشارهای شدید را داشته باشند، منجر به توسعه گسترده آلیاژهای اینکونل شد. در این دوران، اینکونلها نقش حیاتی در ساخت موتورهای جت و تجهیزات هوافضایی ایفا کردند. آلیاژ Inconel 600 به دلیل مقاومت بالای خود در برابر اکسیداسیون و خوردگی در تجهیزات موتورهای جت و توربینهای گازی مورد استفاده قرار گرفت.
پس از جنگ، تحقیقات بیشتر بر روی این آلیاژها ادامه یافت و منجر به توسعه انواع جدیدی از اینکونل با ویژگیهای خاص شد. برای مثال:
- Inconel 718 که در دهه 1950 معرفی شد، به دلیل مقاومت بالا به خزش و خواص مکانیکی عالی در دماهای متوسط، در صنایع هوافضا و توربینهای گازی جایگاه ویژهای یافت.
- Inconel 625 نیز در دهه 1960 بهعنوان آلیاژی مقاوم به خوردگی شدید و سازگار با محیطهای شیمیایی و دریایی عرضه شد.
امروزه این آلیاژها به دلیل کاربردهای گسترده در صنایع نوظهور، همچنان مورد توجه هستند. تلاشها برای کاهش هزینه تولید و بهبود خواص مکانیکی و شیمیایی این آلیاژها ادامه دارد و امکان استفاده گستردهتر از آنها را فراهم کرده است.
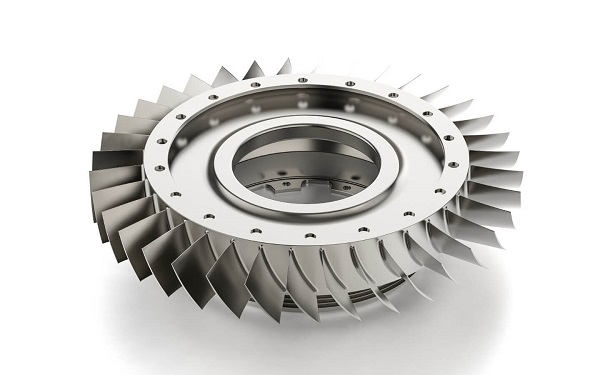
ترکیب شیمیایی آلیاژهای اینکونل
آلیاژهای اینکونل ترکیباتی پیچیده از عناصر آلیاژی هستند که ترکیب دقیق آنها متناسب با کاربرد و خواص موردنیاز تنظیم میشود.
- نیکل (Ni): عنصر اصلی اینکونلها، که باعث مقاومت بالا به اکسیداسیون و خوردگی میشود و نقش مهمی در پایداری در دماهای بالا دارد. نیکل معمولاً بین 50 تا 75 درصد از ترکیب شیمیایی این آلیاژها را تشکیل میدهد.
- کروم (Cr): افزودن کروم (15 تا 25 درصد) مقاومت به اکسیداسیون و تشکیل لایه محافظ بر روی سطح آلیاژ در دمای بالا را فراهم میکند.
- مولیبدن (Mo): بین 3 تا 10 درصد، که مقاومت به خوردگی در محیطهای اسیدی و کلریدی را افزایش میدهد.
- آهن (Fe): معمولاً بین 5 تا 20 درصد، که خواص مکانیکی را بهبود میبخشد و هزینه تولید را کاهش میدهد.
- عناصر دیگر: عناصر جزئی مانند کبالت، تیتانیوم، نیوبیوم، و آلومینیوم نیز بهمنظور تقویت استحکام و پایداری در محیطهای خاص اضافه میشوند. رسوبات تقویتکننده مانند Nb، Ti و Al در برخی گریدها موجب افزایش مقاومت مکانیکی و خزش میشوند.
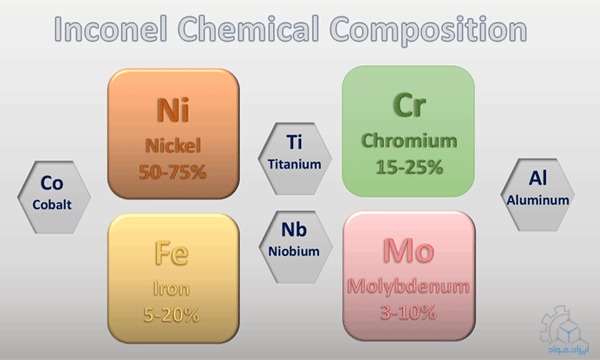
تأثیر عملیات حرارتی و فرآوری بر ریزساختار و عملکرد آلیاژهای اینکونل
عملیات حرارتی و فرآوری نقش بسیار مهمی در بهینهسازی ریزساختار و در نتیجه عملکرد آلیاژهای اینکونل دارند. این فرایندها با کنترل رسوبدهی فازهای تقویتکننده، کاهش تنشهای داخلی، و تغییر ریزساختار پایه، خواص مکانیکی، حرارتی و مقاومت به خوردگی را بهبود میبخشند.
- عملیات انحلالی (Solution Treatment): در این مرحله، آلیاژ در دمای بالایی (معمولاً 1150-980درجه سانتیگراد) حرارت داده میشود تا رسوبات موجود در در زمینه آستنیتی آن حل شوند. این عمل باعث یکنواختی ساختار و کاهش احتمال تشکیل ترکهای ناشی از تنشهای داخلی میشود. هدف اصلی از عملیات انحلالی، آمادهسازی آلیاژ برای مراحل بعدی عملیات حرارتی است.
- پیرسازی: پس از عملیات انحلالی، آلیاژ در دمای متوسطی (900-650درجه سانتیگراد) نگهداری میشود. در این دما، رسوبات تقویتکنندهای مانند γ′(Ni3Al) و (Ni3Nb) ″γ در ساختار تشکیل میشوند. این رسوبات مانع از حرکت نابجاییها شده و باعث افزایش قابل توجه استحکام، سختی و مقاومت به خزش آلیاژ میشوند. به عبارت دیگر، پیرسازی باعث افزایش مقاومت آلیاژ در برابر تغییر شکل در دماهای بالا میشود.
عملیات حرارتی سوپر آلیاژهای پایه نیکل
عملیات حرارتی سوپرآلیاژ های پایه نیکل مقدمه: عملیات حرارتی سوپرآلیاژ های پایه نی...- آنیلینگ: این مرحله معمولاً برای بهبود شکلپذیری و کاهش تنشهای داخلی انجام میشود. در این فرایند، آلیاژ در دمای بالایی (دمای 1050-900درجه سانتیگراد) حرارت داده شده و سپس به آرامی سرد میشود. آنیلینگ باعث میشود آلیاژ در هنگام عملیات مکانیکی مثل خمکاری یا کشش، رفتار انعطافپذیرتری داشته باشد و در دماهای کاری بالا به دلیل ساختار متالورژیکی ایجاد شده، پایدارتر باشد و به راحتی دچار تغییر شکل دائمی نشود. همچنین، عملیات آنیلینگ با ایجاد یک ساختار همگنتر، باعث افزایش پایداری ساختار و بهبود مقاومت به خوردگی آلیاژ میشود.
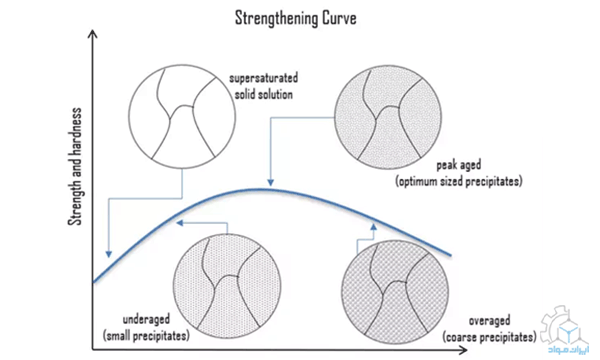
انواع آلیاژهای رایج اینکونل و کاربرد آنها
آلیاژهای اینکونل به دلیل ویژگیهای منحصربهفرد، به شکل گستردهای در صنایع مختلف استفاده میشوند. در ادامه لیستی از آلیاژهای رایج اینکونل همراه با ترکیب شیمیایی و ویژگیهای کلیدی آنها بر اساس استانداردهای ASTM ارائه میشود:
آلیاژ 600 Inconel
آلیاژ اینکونل 600 با پایه نیکل-کروم، به دلیل مقاومت بالای خود در برابر خوردگی، اکسیداسیون و اثرات دماهای بالا شناخته میشود. وجود نیکل بالا در این آلیاژ باعث میشود که در محیطهای خورنده حاوی کلریدها یا اسیدهای اکسیدکننده عملکرد عالی داشته باشد.
نوع اینکونل | نیکل+کبالت (Ni+Co) | کروم (Cr) | آهن (Fe) | کربن (C) | منگنز (Mn) | گوگرد (S) | سیلیسیم (Si) | مس (Cu) |
Inconel 600 | 72 | 14-17 | 6-10 | 0.15 max | 1.0 max | 0.015 max | 0.50 max | 0.50 max |
نوع اینکونل | محدوده دمای ذوب | چگالی | استحکام کششی | حد تسلیم | ازدیاد طول |
Inconel 600 | 1354-1413 ºC | 8.47g/cm3 | 172-354MPa 1517MPa | 172MPa 1034MPa | 35-55% در شرایط آنیل شده |
نکته قابل توجه در جدول بالا مقادیر استحکام کششی و حد تسلیم است. در شرایط حرارتی متلف مقادیر استحکام با یکدیگر متفاوت است. معمولا در شرایط سردکار
دانشــنـامه
سردکار
چیست ؟
فلزی که تحت کارمکانیکی در زیر دمای کریستاله شدن خود قرار گرفته است.
ی شدید مقدار استحکام کششی و حد تسلیم بیشتر است.
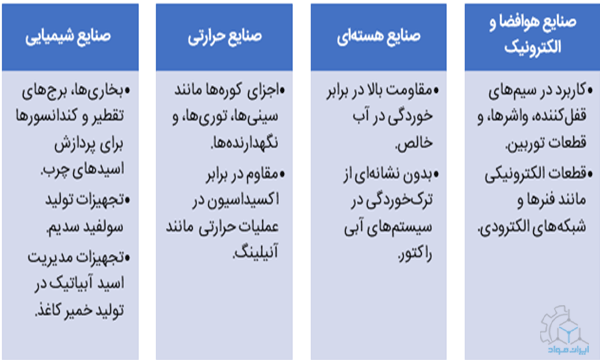
آلیاژ 601 Inconel
این آلیاژ بهواسطه حضور آلومینیوم علاوه بر نیکل و کروم، از مقاومت بسیار بالایی در برابر اکسیداسیون و کربوریزاسیون در دماهای بالا برخوردار است. آلیاژ اینکونل 601 لایه اکسیدی پایداری تشکیل میدهد که از سطح در برابر تخریب محافظت میکند، حتی در محیطهایی با حرارت متناوب.
نوع اینکونل | نیکل (Ni) | کروم (Cr) | آهن (Fe) | آلومینیوم (Al) | مس (Cu) |
Inconel 601 | 58-63 | 21-25 | remained | 1.0-1.7 | max 0.5-1.0 |
در ترکیب شیمیایی این آلیاژ مقادیری جزئی از کربن، منگنز، گوگرد و سیلیسیم به ترتیب حداکثر 0.1، 1، 0.015 و 0.5 درصد وجود دارد.
نوع اینکونل | محدوده دمای ذوب | چگالی | استحکام کششی | حد تسلیم | ازدیاد طول |
Inconel 601 | 1360-1411ºC | 8.11g/cm3 | 550-790MPa درشرایط آنیل شده | 205-415 MPa در شرایط آنیل شده | 30-50% بسته به شرایط حرارتی و مکانیکی |
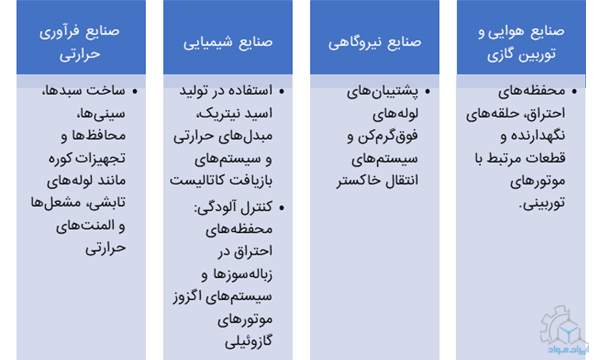
آلیاژ 617 Inconel
آلیاژ اینکونل 617 به دلیل ترکیب پایه نیکل-کروم-کبالت با مقدار قابل توجهی مولیبدن، مقاومت بسیار بالایی در برابر اکسیداسیون، خوردگی گازهای داغ و کربوریزاسیون دارد. این آلیاژ به طور ویژه در دمای بالاتر از 1000°C استحکام خود را حفظ میکند و در صنایع مرتبط با توربینهای گازی، مبدلهای حرارتی و سیستمهای پتروشیمی به کار میرود.
نوع اینکونل | نیکل (Ni) | کروم (Cr) | کبالت (Co) | مولیبدن (Mo) | آلومینیوم (Al) | مس (Cu) | برون (B) |
Inconel 617 | 44.5 | 20-24 | 10-15 | 8-10 | 0.8-1.5 | max 0.5 | max 00.6 |
در جدول بالا دیگر عناصر به مقدار جزئی وجود دارند. به عنوان مثال حداکثر مقادیر کربن 0.15-0.5، آهن 3، سیلیسیم 1، منگنز 1، تیتانیوم 0.6 و گوگرد 0.015 درصد در ترکیب آلیاژ اینکونل 617 موجود است.
نوع اینکونل | محدوده دمای ذوب | چگالی | استحکام کششی | حد تسلیم | ازدیاد طول |
Inconel 617 | 1332-1380ºC | 8.36g/cm3 | 534-770MPa بسته به دما | 144-319 MPa بسته به دما | 30-50% بسته به دما و فرایند |
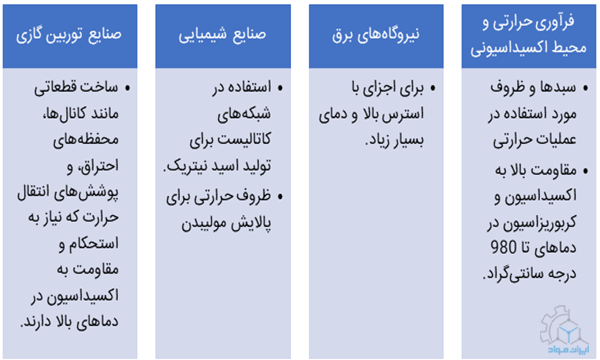
آلیاژ 625 Inconel
آلیاژ اینکونل 625 با محتوای بالای مولیبدن و نیوبیوم، به مقاومت فوقالعاده در برابر خوردگی ناشی از کلریدها، اسیدها و محیطهای آبی خورنده شناخته میشود. انعطافپذیری بالا و قابلیت جوشکاری خوب، آن را به یکی از محبوبترین آلیاژها برای کاربرد در صنایع دریایی، شیمیایی، نفت و گاز و هستهای تبدیل کرده است.
نوع اینکونل | نیکل (Ni) | کروم (Cr) | آهن (Fe) | مولیبدن (Mo) | نیوبیوم+تانتالیوم (Nb+Ta) | آلومینیوم (Al) | تیتانیوم (Ti) | کبالت (Co) |
Inconel 625 | 58 | 20-23 | max 5 | 8-10 | 3.5+4.15 | max 0.4 | max 0.4 | max 1 |
در جدول بالا عناصر دیگری به مقدار جزئی وجود دارد. به عنوان مثال حداکثر مقادیر کربن 0.1، منگنز 0.5، سیلیسیم 0.5، فسفر و گوگرد 0.015 درصد در ترکیب آلیاژ اینکونل 625 موجود است.
نوع اینکونل | محدوده دمای ذوب | چگالی | استحکام کششی | حد تسلیم | ازدیاد طول |
Inconel 625 | 1290-1350ºC | 8.44g/cm3 | 827-1103MPa برای شرایط آلیاژکاری مختلف | 414-758MPa بسته به دما | 30-60% بسته به دما و فرایند |

آلیاژ 718 Inconel
این آلیاژ که به دلیل استفاده از نیوبیوم و مولیبدن تقویت شده است، دارای استحکام تسلیم بالا، مقاومت به خزش و قابلیت تحمل بارهای سنگین در دماهای پایین و بالا است. به همین دلیل، آلیاژ 718 بهویژه در صنایع هوافضا، توربینهای گازی و سیستمهای فشار بالا به کار میرود.
نوع اینکونل | نیکل+کبالت (Ni+Co) | کروم (Cr) | آهن (Fe) | مولیبدن (Mo) | نیوبیوم+تانتالیوم (Nb+Ta) | برون (B) | کبالت (Co) |
Inconel 718 | 50-55 | 17-21 | balance | 2.8-3.3 | 4.75-5.50 | max 0.006 | max 1 |
در ترکیب شیمیایی این آلیاژ مقادیری جزئی از کربن، منگنز، گوگرد و سیلیسیم، فسفر، آلومینیوم، تیتانیوم و مس نیز وجود دارد.
نوع اینکونل | محدوده دمای ذوب | چگالی | استحکام کششی | حد تسلیم | ازدیاد طول |
Inconel 178 | 1260-1336ºC | 8.19g/cm3 | 965-1275MPa برای شرایط آلیاژکاری مختلف | 790-1035 MPa بسته به دما | 10-25% بسته به دما و فرایند |
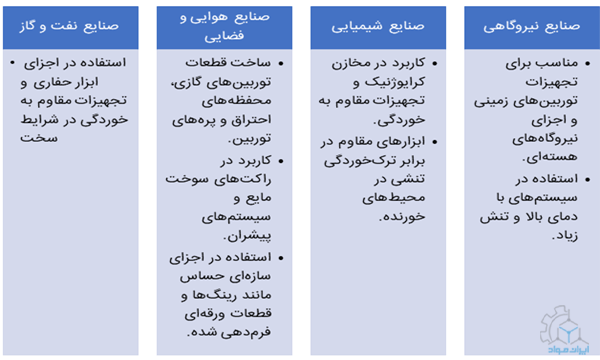
آلیاژ X-750 Inconel
آلیاژ X-750، بر اساس آلیاژ پایه نیکل-کروم توسعه یافته و با افزودن تیتانیوم و آلومینیوم بهبود یافته است. این آلیاژ به دلیل مقاومت بالا در برابر خزش و خستگی در محیطهای دما بالا، برای کاربردهایی نظیر فنرهای دما بالا، اجزای موتورهای هواپیما و قطعات هستهای مناسب است.
نوع اینکونل | نیکل+کبالت (Ni+Co) | کروم (Cr) | آهن (Fe) | نیوبیوم+تانتالیوم (Nb+Ta) | تیتانیوم (Ti) | مس (Cu) | کبالت (Co) |
Inconel X-750 | 70 | 14-17 | 5-9 | 0.7-1.2 | 2.25-2.75 | max 0.5 | max 1 |
در این آلیاژ مقادیری جزئی از کربن، منگنز، سیلیسیم، گوگرد و آلومینیوم موجود است.
نوع اینکونل | محدوده دمای ذوب | چگالی | استحکام کششی | حد تسلیم | ازدیاد طول |
Inconel X-750 | 1393-1427ºC | 8.28g/cm3 | 790-1170MPa بسته به نوع عملیات حرارتی | 515-860 MPa بسته به دما | 15-25% در دمای اتاق 5-10% در دماهای بالاتر |
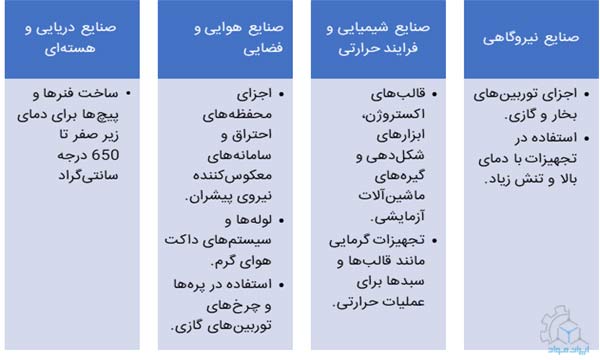
در ادامه جدولی برای مقایسه آلیاژهای رایج اینکونل بر اساس ASTM B443, ASM Metals Handbook در یک نگاه آماده شده است تا درک بهتری از آلیاژهای رایج اینکونل به دست آید. لازم به ذکر است مقادیر ذکر شده ممکن است بسته به شرایط خاص عملیاتی و فرایندهای حرارتی یا مکانیکی متفاوت باشند.
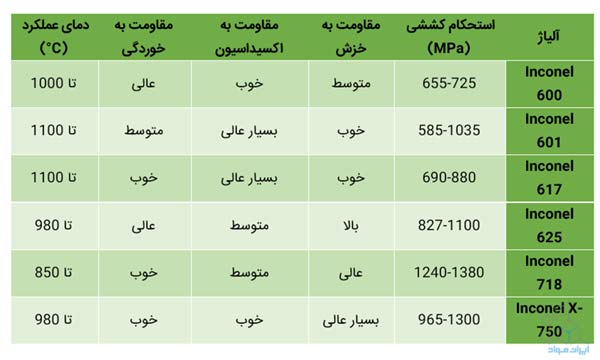
فرایندهای تولید آلیاژهای اینکونل
آلیاژهای اینکونل (Inconel) به دلیل خواص استثنایی مانند مقاومت به حرارت، خوردگی، و استحکام مکانیکی بالا، نیازمند فرایندهای تولید خاصی هستند که برای حفظ یکنواختی ترکیب و کیفیت بالا طراحی شدهاند. مراحل کلیدی تولید این آلیاژها عبارتند از:
- ذوب و ریختهگری: تولید آلیاژهای اینکونل با فرایند ذوب آغاز میشود، که در آن مواد اولیه شامل نیکل، کروم، آهن، و سایر عناصر آلیاژی در کورههای پیشرفته ذوب میشوند. برای کنترل دقیق ترکیب شیمیایی و حذف ناخالصیها، معمولاً از روشهای ذوب در خلا (VIM) و ذوب قوس الکتریکی در خلا (VAR) استفاده میشود. این روشها تضمین میکنند که آلیاژ تولید شده دارای خواص مکانیکی و شیمیایی یکنواخت باشد. پس از ذوب، فلز مذاب در قالبهای خاص ریخته میشود تا شمشهای اولیهای ایجاد شود که پایهای برای فرایندهای بعدی هستند.
- عملیات حرارتی اولیه: شمشهای ریختهگری شده تحت عملیات حرارتی اولیه قرار میگیرند تا تنشهای داخلی ناشی از فرایند ریختهگری کاهش یابد و ساختار میکروسکوپی فلز یکنواختتر شود. در این مرحله، فرایندهایی مانند آنیلینگ برای نرم کردن ساختار و افزایش چقرمگی به کار میرود. همچنین، پیشسرد کردن شمشها باعث جلوگیری از ایجاد ترکخوردگی در مراحل بعدی تغییر شکل میشود. این عملیات حرارتی اولیه بهطور قابل توجهی در کیفیت نهایی آلیاژ تأثیرگذار است.
- تغییر شکل مکانیکی: در این مرحله، شمشهای تولید شده به کمک روشهای شکلدهی مکانیکی به فرمهای دلخواه تبدیل میشوند. فرایندهایی مانند نورد گرم و سرد برای تولید ورقها و نوارهای نازک و فورجینگ برای تولید قطعات مستحکمتر مانند پرههای توربین مورد استفاده قرار میگیرند. همچنین، اکستروژن یکی دیگر از فرایندهای مهم است که برای تولید لولهها و پروفیلهای خاص بهکار میرود. این مراحل به دلیل سختی و استحکام بالای آلیاژهای اینکونل، نیازمند تجهیزات پیشرفته و نیروی قابل توجه هستند.
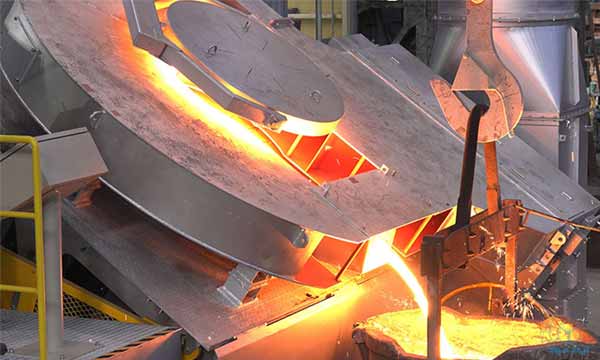
- عملیات حرارتی پیشرفته: پس از شکلدهی مکانیکی، آلیاژ تحت عملیات حرارتی پیشرفته قرار میگیرد تا خواص مکانیکی و فیزیکی آن بهینه شود. یکی از فرایندهای مهم، حلالسازی (Solution Heat Treatment) است که با حل کردن کاربیدها در دماهای بالا به یکنواخت کردن ساختار کمک میکند. در ادامه، عملیات پیری (Aging) انجام میشود تا رسوبات تقویتکنندهای مانند γ′′\gamma” و γ′\gamma’ تشکیل شوند. این رسوبات باعث افزایش استحکام و مقاومت به خزش آلیاژ میشوند. رسوبسختی (Precipitation Hardening) نیز برای بهبود استحکام نهایی قطعه مورد استفاده قرار میگیرد.
- ماشینکاری و جوشکاری: به دلیل سختی و مقاومت به حرارت بالای اینکونل، فرایند ماشینکاری آن چالشبرانگیز است و نیازمند استفاده از ابزارهای خاص مانند کاربید تنگستن یا ابزارهای پوششدار است. در جوشکاری، روشهایی مانند TIG و MIG استفاده میشوند که به دمای دقیق و سرعت خنکسازی مناسب نیاز دارند تا از ترکخوردگی در محل جوش جلوگیری شود. این مرحله نیازمند دقت و مهارت بالا است، زیرا کیفیت نهایی قطعات به شدت به فرایند ماشینکاری و جوشکاری بستگی دارد.
- تست و کنترل کیفیت: پس از تولید، آلیاژهای اینکونل تحت تستهای مکانیکی و فیزیکی گستردهای قرار میگیرند تا کیفیت آنها تضمین شود. آزمونهایی مانند کشش و خستگی برای بررسی استحکام، سختی و خزش برای ارزیابی دوام در شرایط دمای بالا، و آزمونهای غیرمخرب (NDT) مانند اولتراسونیک و رادیوگرافی برای شناسایی ترکها انجام میشوند. همچنین، آنالیز شیمیایی با روشهایی مانند XRF یا ICP برای اطمینان از یکنواختی ترکیب شیمیایی انجام میشود.
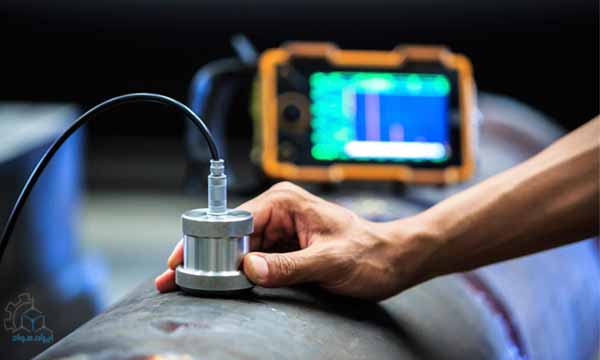
معادلهای آلیاژهای اینکونل در استانداردهای مختلف
آلیاژهای اینکونل در صنایع مختلف با استفاده از استانداردهای گوناگون شناسایی و استفاده میشوند. استانداردهای معروف شامل UNS (Unified Numbering System)، ASTM، AMS (Aerospace Material Specifications)، DIN/EN و ISO است. در ادامه، معادلهای رایج آلیاژهای اینکونل در این استانداردها ارائه شده است تا مهندسین و متخصصین بتوانند آلیاژ مناسب را با توجه به استانداردهای مرتبط شناسایی کنند.
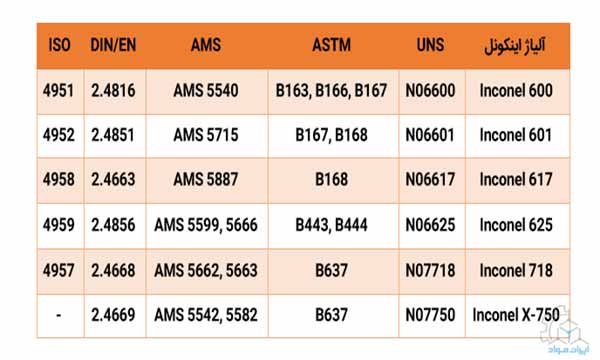
کاربرد آلیاژهای اینکونل در صنایع مختلف
آلیاژهای اینکونل به دلیل خواص استثنایی مانند مقاومت بالا در برابر خوردگی، اکسیداسیون و دماهای بالا، در صنایع پیشرفته کاربردهای گستردهای دارند. در صنایع هوافضا، این آلیاژها برای ساخت قطعات موتورهای جت مانند پرههای توربین و محفظههای احتراق استفاده میشوند. صنایع نفت و گاز از آنها در لولهها و تجهیزات مقاوم به محیطهای خورنده بهره میبرند، در حالی که در نیروگاهها برای اجزای توربینهای گازی و بخار و سیستمهای گرمایش کاربرد دارند.
در صنایع شیمیایی و پتروشیمی، اینکونل به دلیل مقاومت به اسیدها و بازها در مبدلهای حرارتی و رآکتورها استفاده میشود. صنایع دریایی از این آلیاژها برای ساخت قطعات زیرآبی مانند پروانهها و لولهها بهره میگیرند و در صنایع هستهای نیز برای سیستمهای خنککننده و مخازن مقاوم به تشعشعات استفاده میشوند. همچنین، اینکونل در صنایع پزشکی برای ساخت ابزارهای مقاوم به خوردگی و ایمپلنتها و در صنعت خودروسازی برای اجزای مقاوم به حرارت در سیستمهای اگزوز کاربرد دارد.
کاربردهای مذکور پیشتر در بخش معرفی آلیاژهای رایج اینکونل با جزئیات کاملتری بررسی شدهاند و ویژگیها و توانمندیهای منحصربهفرد هر آلیاژ در صنایع گوناگون بهطور دقیق تشریح شده است.
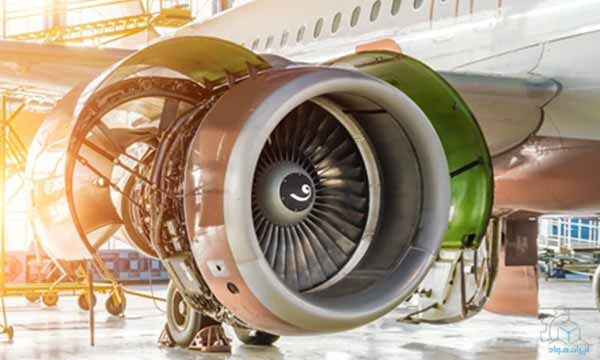
مقایسه آلیاژهای اینکونل با آلیاژهای مشابه
مقایسه آلیاژهای اینکونل با آلیاژهای مشابه، مانند آلیاژهای هستلوی (Hastelloy)و مونل (Monel)میتواند دیدگاهی جامع درباره تفاوتها و شباهتهای آنها ارائه دهد. این آلیاژها هرکدام ویژگیهای منحصر به فردی دارند. اینکونل که پایه آن نیکل-کروم است، مقاومت عالی در برابر خوردگی ناشی از اکسیداسیون و کربوریزاسیون در دماهای بالا ارائه میدهد و عملکرد آن تا دماهای 1000-1100°C بسیار مطلوب است و برای کاربردهای هوافضا مانند توربینها و موتورهای جت ایدهآل است، اما در محیطهای اسیدی قویتر، عملکردی به اندازه هستلوی ندارد. هستلوی، که پایه آن نیکل-مولیبدن است که اگرچه استحکام مکانیکی آن متوسط است، مقاومت بالایی در برابر اسیدهای قوی دارد و در صنایع شیمیایی و نیروگاهی بسیار موثر است و بهترین عملکرد آن در دماهای زیر 600°C مشاهده میشود. مونل که پایه آن نیکل-مس است، به محیطهای حاوی کلرید به خوبی مقاوم است و بهترین عملکردش در شرایط دریایی و آب شور دیده میشود، اما در دماهای بالا عملکرد ضعیفتری دارد و استحکام آن در دماهای بالا کمتر است، با این حال چقرمگی خوبی در دماهای پایین ارائه میدهد.
مزایا و محدودیتهای آلیاژهای اینکونل
همانطور که پیشتر اشاره شد، آلیاژهای اینکونل به دلیل خواص برجستهای مانند مقاومت شیمیایی عالی در محیطهای خورنده، استحکام مکانیکی در دماهای بالا، و مقاومت به اکسیداسیون و خوردگی داغ، در صنایع هوافضا، انرژی و پتروشیمی بهکار گرفته میشوند. همچنین، داکتیلیته و چقرمگی بالای این مواد باعث شده است که در کاربردهایی با شرایط کاری سخت و دماهای بسیار بالا عملکرد مطلوبی داشته باشند.
با این حال، این آلیاژها محدودیتهایی نیز دارند که باید مدنظر قرار گیرند. هزینه بالای مواد اولیه و فرآوری یکی از چالشهای اصلی است. علاوه بر این، ماشینکاری و شکلدهی این آلیاژها به دلیل استحکام و سختی بالا دشوار است. حساسیت به ترکخوردگی در حین جوشکاری و وزن بالاتر نسبت به آلیاژهای سبکتر نیز از دیگر محدودیتهای این مواد هستند. این عوامل میتوانند بر انتخاب و استفاده از آلیاژهای اینکونل در برخی کاربردها تأثیرگذار باشند.
آینده آلیاژهای اینکونل
آلیاژهای اینکونل با توجه به کاربردهای گسترده در صنایع پیشرفته و نیاز روزافزون به مواد مقاوم در شرایط دشوار، همچنان به عنوان یکی از انتخابهای کلیدی در مهندسی مواد باقی خواهند ماند. با این حال، تحقیقات در راستای کاهش هزینهها، بهبود خواص و بهینهسازی فرایندهای تولید ادامه دارد. در این بخش، دو محور اصلی توسعه آلیاژهای اینکونل بررسی میشود: نوآوری در ترکیبهای آلیاژی و پیشرفت در روشهای تولید.
- نوآوری در ترکیبهای آلیاژی برای کاهش هزینه: نوآوری در ترکیبهای آلیاژی اینکونل با هدف کاهش هزینه مواد اولیه، بدون افت در خواص عملکردی آلیاژ، یکی از موضوعات مهم در صنعت متالورژی است. بهدلیل قیمت بالای نیکل بهعنوان عنصر اصلی این آلیاژها، راهبردهایی برای کاهش مقدار نیکل و جایگزینی آن با عناصر کمهزینهتر مانند منگنز و آهن پیشنهاد شدهاند. همچنین، استفاده از ترکیبات نانوذرات تقویتکننده مانند نانوذرات اکسید آلومینیوم (ODS) یا کاربیدها میتواند خواص مکانیکی و حرارتی آلیاژها را بهبود بخشد.
- پیشرفت در روشهای تولید: پیشرفت در روشهای تولید آلیاژهای اینکونل با هدف کاهش هزینه، زمان تولید و بهبود کیفیت قطعات، از اهمیت بالایی برخوردار است. استفاده از فناوری چاپ سهبعدی با روشهایی مانند SLM و EBM امکان تولید قطعات پیچیده با پرت مواد کمتر و کنترل دقیق ساختار لایهبهلایه را فراهم میکند. همچنین، تکنولوژیهای مدرن ذوب القایی و ریختهگری پیشرفته به کاهش نواقص ساختاری و بهبود یکنواختی کمک میکنند. روشهای پیشرفته فورجینگ و نورد، با کنترل دقیق ریزساختار، باعث افزایش استحکام و کاهش هزینه تولید قطعات بزرگ میشوند. علاوه بر این، استفاده از هوش مصنوعی و شبیهسازی در پیشبینی خواص مکانیکی و بهینهسازی فرآیندها، موجب بهبود بهرهوری و کاهش زمان تولید میشود. این فناوریهای نوین دقت در ساخت قطعات با کیفیت بالا را افزایش داده و بهرهوری مواد اولیه را بهینه میکنند.
مواد فنر - Spring materials
مواد فنر – Spring materials مواد بهینه برای ساخت فنرها، همان گونه که از نا...جمعبندی
در مقاله مورد نظر، به بررسی سوپرآلیاژ اینکونل (Inconel) پرداخته شد. این آلیاژ به دلیل ترکیب شیمیایی خاص خود، مقاومت بالایی در برابر حرارت، اکسیداسیون و خوردگی دارد. همچنین، استحکام کششی و خزشی بالای آن در دماهای بالا، اینکونل را برای استفاده در صنایع مختلفی مانند هوافضا، نیروگاههای هستهای و صنایع شیمیایی مناسب میسازد. جایگاه آلیاژهای اینکونل در صنایع پیشرفته به دلیل توانایی آنها در مواجهه با چالشهای صنعتی و ارائه عملکرد قابل اعتماد، بیبدیل است. با پیشرفت در ترکیبهای آلیاژی و روشهای تولید، این آلیاژها نه تنها به گسترش کاربردهای خود ادامه خواهند داد، بلکه نقش مهمتری در توسعه فناوریهای نوظهور ایفا خواهند کرد. بنابراین، اینکونلها همچنان یکی از انتخابهای اصلی در طراحی و ساخت قطعات حیاتی برای صنایع پیشرفته باقی خواهند ماند.
دیدگاه کاربران