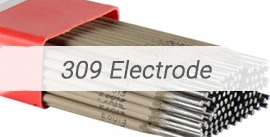
فولادهای زنگ نزن انواع و کاربردها – Stainless steel
فولادهای زنگ نزن انواع و کاربردها – Stainless steel
فولادهای زنگ نزن انواع و کاربردها – Stainless steel
شرح :
فولادهای زنگ نزن انواع و کاربردها – Stainless steel : از آنجایی که صنعت فولاد به عنوان پایه و اساس صنایع جدید و وجود کارخانجات و مجتمع های فولاد در هر کشور نمایانگر اقتدار آن کشور در جهت بخدمت گرفتن تکنولوژی های مدرن می باشد و همچنین با توجه به وجود مجتمع های فولاد در کشور می توان نتیجه گرفت که بیش از ربع قرن از فعالیت صنایع نوین در ایران می گذرد. وجود و بهره برداری از مجتمع های بزرگ فولاد همچون مجتمع فولاد مبارکه و مجتمع فولاد خوزستان حکایت از فعالیت رو به رشد صنعت فولاد کشور دارد.
ولی علی رغم بر خورداری از یک سابقه نسبتا طولانی در تولید فولاد متاسفانه به دلایل مختلف از قبیل مسائل سیاسی که بعد از انقلاب پیش آمد این صنعت از رشد کیفی مطلوبی برخوردار نبود و در دستیابی به فنون و تکنولوژی های پیشرفته موفقیت چندانی بدست نیاورده است و این خود ما را بر آن می دارد برای برخورداری و دستیابی به تکنولوژی های پیشرفته این صنعت از هر تلاش و کوششی دریغ ننماییم که این مستلزم تغییر رویکرد ما نسبت به صنعت فولاد می باشد. با گذشت نزدیک به یک قرن از تولید فولاد زنگ نزن در سال ۱۹۱۰، روش ها و تجهیزات متنوعی در تکنولوژی تجارتی آن بکار گرفته شده است. کارهای اولیه در ژاپن ، آفریقای جنوبی و اروپا با استفاده از تجهیزات معمولی فولاد های کربنی (اما در تناژ کم)انجام گرفته است. اما رقابت بازار جهانی و فولاد با کیفیت خوب تجهیزات مدرن تری را می طلبد برای تولید فولاد زنگ نزن انجام دو اقدام زیر لازم و ضروری می باشد :
۱- سرمایه گذاری مطلوب در جهت تکمیل خطوط تولید و تجهیز مجتمع های فولاد به تجهیزات مدرن
۲- کسب دانش فنی و در اختیار گرفتن تکنولوژی ساخت
دانلود فایل فولادهای زنگ نزن :
قالب بندی : PDF
تعداد صفحات :۷۲
حجم : ۶۳۴KB
دانلود فایل مروری بر طبقه بندی فولادهای زنگ نزن :
قالب بندی : PDF
تعداد صفحات :۱۰
حجم : ۶۱۸KB

دیدگاه کاربران
باعرض سللم و وقت بخیر
لازم دانستم به استحضار برسانم هیچ یک ازتصاویر ونمودارهای موجود در فایل مربوط به فولادهای زنگ نزن چاپ نشده است.
موفق وموید باشید.