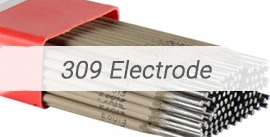
عملیات حرارتی آلومینیوم (Aluminium Heat Treatment)
چرا آلیاژهای آلومینیوم نیاز به عملیات حرارتی دارند؟
آلیاژسازی آلومینیوم تا حد زیادی باعث افزایش استحکام این فلز می شود. با این حال، آلیاژسازی به تنهایی برای دستیابی به خواص مکانیکی مناسب کافی نیست. بسیاری از قطعات به منظور استفاده در دماها و تنش های بالا نیاز به استحکام بالایی دارند که این استحکام به تنهایی با آلیاژسازی حاصل نمی شود.
گرچه عملیات حرارتی آلومینیوم منحصر به افزایش استحکام آلیاژ نمی شود و در بسیاری از مواقع برای کاهش و یا حذف تنش های باقی مانده در قطعه ریخته گری یا شکل داده شده، افزایش مقاومت به سایش و بالا بردن مقاومت به ضربه آلومینیوم و حتی افزایش مقاومت به خوردگی و جوشکاری آلومینیوم نیاز به عملیات حرارتی داریم. بنابراین هدف از عملیات حرارتی آلومینیوم و آلیاژهای آن را می توان بهبود خواص فیزیکی، مکانیکی و شیمیایی آلیاژ عنوان کرد.
روش های استحکام بخشی آلیاژهای آلومینیوم
به طور کلی استحکام آلیاژهای آلومینیوم را از طریق دو روش کارسختی و پیرسختی می توان افزایش داد. توجه داشته باشید که در این دسته بندی، هدف افزایش استحکام آلیاژهای آلومینیومی است. بنابراین از صحبت در خصوص استحکام بخشی با تشکیل محلول های جامد صرف نظر می کنیم.
کار سختی (Work Hardening)
کار سختی یعنی افزایش استحکام مکانیکی فلز یا آلیاژ در اثر انجام کار مکانیکی بر روی آن. ممکن است این فرایند را با نام کرنش سختی نیز بشناسید. این عملیات می تواند از طریق فرایندهای کارسرد مثل نورد، اکستروژن، کشش یا پرس انجام گیرد.
در طول فرایند تغییر شکل، نرخ تکثیر نابهجاییها بسیار سریع تر از نرخ کاهش آن ها در اثر بازیابی دینامیکی خواهد بود. عناصر آلیاژی با روش های مختلف می توانند این نرخ تکثیر را افزایش بدهند. اما دقت داشته باشید که افزایش آن ها باید به میزانی باشد که ترکیبات بین فلزی نامحلول ایجاد کنند. چرا که این خود این ترکیبات ترد هستند. مس و منیزیوم موثرترین عناصری هستند که برای این منظور استفاده می شوند.
این روش موثرترین روشی است که برای افزایش استحکام آلیاژهای عملیات حرارتی ناپذیر آلومینیوم (گروه 3000 و 5000) استفاده می شود.
پیرسختی (Age Hardening)
پیرسختی مکانیزم اصلی افزایش استحکام در آلیاژهای عملیات حرارتی پذیر (سری 2000، 6000 و 7000) است. این روش، تاثیر زیادی بر افزایش استحکام آلیاژهای آلومینیوم دارد. به طوری که در برخی مواقع می توانند جایگزین فولادهای کربنی شوند!
شرط اصلی برای پیرسختی یک آلیاژ، کاهش حد حلالیت آن با کاهش دما است. این عملیات شامل سه مرحله اصلی می شود:
- مرحله اول شامل حرارت دادن آلیاژ در ناحیه تک فاز تا دمایی بالاتر از یوتکتیک و نگه داشتن در این دما است. به طوری که عناصر آلیاژی در این فاز به طور کامل حل شوند.
- مرحله دوم سرد کردن سریع است که به عملیات کوئنچ معروف است. در این حالت اتم هایی که در ساختار حل شده اند، فرصت خروج از فاز اولیه َα را نمی کنند و محلول جامد فوق اشباع (Super Saturated) تشکیل می شود.
- مرحله سوم به پیرسازی (Aging) معروف است. در این مرحله قطعه در دمایی مشخص (زیر دمای استحاله یوتکتیک) طی مدت زمان مشخصی قرار می گیرد تا عناصر آلیاژی اضافی از فاز اولیه خارج شده و به صورت رسوب در ساختار باقی بمانند. چنان جه این عملیات در دمای اناق انجام شود، به آن پیرسازی طبیعی و چنان چه در دمای بالا انجام شود، به پیرسازی مصنوعی معروف است.
دقت داشته باشید که اگر در دمای بالا آلیاژ بیش از زمان مجاز نگه داشته شود، پدیده ای به نام Over Aging اتفاق می افتد که سختی آلیاژ را کاهش می دهد.
با آلیاژهای کارپذیر آلومینیوم بیشتر آشنا شوید
آلیاژهای کارشده آلومینیوم به هشت گروه تقسیم می شوند. این تقسیم بر اساس نوع عنصر آلیاژی هر دسته انجام می شود. در جدول زیر می توانید تفکیک این هشت گروه را مشاهده کنید.
سری 1XXX
منظور از سری 1000، آلومینیوم تجاری با خلوص بالای 99% است که به دلیل خلوص بالا در صنایع الکترونیک کاربرد دارد. این گروه با مشخصه مقاومت عالی در برابر خوردگی، رسانایی حرارتی و الکتریکی بالا شناخته شده است. ناخالصی های این گروه، عناصر آهن و سیلیسوم هستند. به دلیل استحکام پایین، کاربرد این گروه به خازن ها، هادی ها، فویل های بسته بندی و تزئینات محدود می شود.
سری 2XXX
سری 2000 با عنصر آلیاژی مس شناخته شده است. همان طوری که در بخش های قبل گفتیم، مس عنصری است که عملیات حرارتی آلومینیوم را تسهیل می کند. این آلیاژها مقاومت به خوردگی خوبی ندارند. به همین دلیل معمولا ورقه های آن ها با لایه ای از آلیاژ سری 6000 پوشانده می شوند. اما استحکام آن ها پس از عملیات حرارتی گاهی بیش از فولادهای کم کربن می شود. آلیاژهای سری 2000 معمولا جوش پذیری مناسبی ندارند اما برخی از آن ها قابلیت ماشین کاری فوق العاده ای دارند. از این سری در ساخت چرخ های قطار و کامیون و بخش هایی از بدنه هواپیماها استفاده می شود.
"فولاد" چیست؟ چه انواعی دارد؟
فولاد از چه چیزی درست شده؟ فولاد را در گذشته به صورت آلیاژی از آهن و کربن توصیف ...سری 3XXX
منگنز، اصلی ترین عنصر آلیاژی سری 3000 است. سری 3000 جزو دسته عملیات حرارتی ناپذیر محسوب می شود. این آلیاژها استحکامی متوسط، انعطاف پذیری بالا و مقاومت خوردگی خوبی دارند. از این آلیاژها در ساخت قوطی های نوشابه، مبدل های حرارتی، مخازن ذخیره و لوازم پخت و پز استفاده می شود.
سری 4XXX
سیلیسیوم عنصری است که می تواند دمای ذوب آلیاژ را تا نزدیک 12% کاهش دهد. به همین دلیل آلیاژهای سری 4000 در ساخت سیم جوش ها و آلیاژهای لحیم استفاده زیادی دارند. این آلیاژها معمولا عملیات حرارتی ناپذیر هستند. اما زمانی که به منظور اتصال آلیاژهای عملیات حرارتی پذیر استفاده می شوند، تا حدودی فلز پایه در فلز جوش نفوذ کرده و تا حدودی به عملیات حرارتی پاسخ می دهند.
سری 5XXX
منیزیوم عنصر اصلی آلیاژی در سری 5000 است. زمانی که این عنصر به همراه منگنز برای تولید آلیازهای این سری استفاده می شود، آلیاژی عملیات حرارتی ناپذیر با قابلیت جوش پذیری مناسب، مقاومت به خوردگی خوب و مقاومت نسبتا بالا را به وجود می آورد. نقش منیزیوم در افزایش استحکام این آلیاژها پر رنگ تر است و می تواند به مقدار بیشتری به آلیاژ اضافه شود. از این آلیاژها در ساخت بدنه قایق ها و کشتی ها، مخازن تحت فشار، قوطی ها و وسایل خانگی استفاده می شود.
سری 6XXX
آلیاژهای سری 6000، به میزان لازم سیلیسیوم و منیزیوم برای تشکیل فاز Mg2Si دارند. به همین دلیل جزو دسته عملیات حرارتی پذیر به حساب می آیند. این دسته، استحکام خوبی در حد آلیاژهای سری 2000 یا 7000 ندارد، اما شکل پذیری، جوش پذیری، ماشین کاری و مقاومت به خوردگی بالا از ویژگی های این دسته محسوب می شود. از این سری برای تولید آلیاژهای سازه ای با استحکام متوسط مانند مقاطع اکستروژن استفاده می شود. 6030 معروف ترین آلیاژ این دسته است.
سری 7xxx
روی عنصر آلیاژی اصلی این دسته است که به مقدار 1 تا 8 درصد استفاده می شود و با همراه شدن با منیزیوم، آلیاژی عملیات حرارتی پذیر با استحکام بالا به دست می دهد. در بین آلیاژهای آلومینیومی، سری 7000 بیشترین پتانسیل پیرسختی را از خود نشان می دهد. برای کنترل خواص ترکیب این دسته، از عناصری مثل منگنز، کروم و زیرکونیوم نیز استفاده می شود. این سری به دلیل استحکام بسیار بالا و مقاومت خوردگی خوب، کاربرد زیادی در صنایع هوایی به خصوص ساخت هواپیماهای نظامی دارد. 7050 , 7075 از مهم ترین آلیاژهای این سری به حساب می آیند.
سری 8xxx
سری 8000 با نام آلیاژهای متفرقه شناخته می شود. این دسته شامل آلیاژهای مختلف با درصد عناصر آلیاژی کم می شود. 8001 آلیاژی آلیاژی مشکل از 1.1% نیکل و 0/6% آهن است مقاومت خوبی در برابر فشار و خوردگی در برابر آب در دماهای بالا دارد و در تاسیسات هسته ای استفاده می شود. 8011 آلیاژی است که به دلیل قابلیت خوب در کشش عمیق در ساخت سر بطری ها استفاده می شود. 8280 و 8081 نیز آلیاژهایی بر پایه قلع هستند که در ساخت یاتاقان ها، موتورهای اتومبیل ها و کامیون ها استفاده می شود.
با آلیاژهای ریختگی آلومینیوم آشنا شوید
آلیاژهای ریختگی آلومینیوم نیز همانند نوع کارشده در هشت گروه طبقه بندی می شوند. در جدول زیر نام گذاری هر کدام از این دسته ها را بر حسب عنصر آلیاژی آن مشاهده می کنید.
سری 4xx.x
این دسته از آلیاژها، جوش پذیری، ماشین کاری و مقاومت خوردگی بالایی دارند. حضور سیلیسیم باعث افزایش سیالیت مذاب می شود. اما مشکل این دسته از آلیاژها سرد شدن آهسته آن هاست که باعث تشکیل ساختاری درشت دانه و تضعیف خواص مکانیکی آلیاژ می شود. برای رفع این مشکل باید از ریخته گری پیوسته استفاده کرد تا سرعت سرد شدن افزایش یابد.
ریخته گری پیوسته ؛ صنعتی ترین روش ریخته گری جهان!
امروزه بالغ بر ۹۵٫۵ درصد از تولید فولاد خام در جهان، با روش ریخته گری پیوسته انج...سری 2xxx.x
این دسته از آلیاژها قابلیت عملیات حرارتی دارند و با روش پیرسختی مستحکم می شوند. برخی از این آلیاژها همانند 238 و 242 برای ساخت سرسیلندرها و پیستون های هواپیما کاربرد دارند.
سری 5xxx.x
آلیاژهای سری 500 قابلیت ماشین کاری و مقاومت خوردگی بالایی دارند. حضور منیزیوم می تواند باعث تسریع اکسیدشدن مذاب در هنگام انجماد شود. به همین دلیل باید کنترل زیادی بر روی عملیات ریخته گری و انجماد وجود داشته باشد. اکثر این آلیاژها در قالب ماسه ای ریخته می شوند.
سری 8xxx.x
امروزه این آلیاژها تقریبا از رده خارج شده اند و مهم ترین استفاده آن ها به عنوان آند فداشونده در حفاظت کاتدی سازه هاست. به جای آن، سری 9xxx.x بر پایه عناصر آهن، مس، کروم و منگنز امروزه کاربرد زیادی پیدا کرده اند. این آلیاژها مقاومت به خوردگی، ماشین کاری و پایداری ابعادی مناسبی دارند. اما در اثر کارکرد طولانی مدت در دمای بالا دچار Over Aging می شوند و کارایی خود را از دست می دهند.
عملیات حرارتی آلیاژهای آلومینیوم
آلیاژهای آلومینیوم به لحاظ قابلیت عملیات حرارتی به دو دسته عملیات حرارتی پذیر (Heat Treatable) و عملیات حرارتی ناپذیر (Non-Heat Treatable) تقسیم می شوند. وقتی صحبت از عملیات حرارتی آلیاژهای آلومینیوم می کنیم، منظورمان آلیاژهای عملیات حرارتی پذیر یا پیر سخت شونده است. گرچه نباید این نکته را فراموش کنیم که عملیات حرارتی آنیل (تابکاری) بر روی هر دو نوع این آلیاژها برای افزایش انعطاف پذیری و چکش خواری آن ها انجام می شود. اما در آلیاژهای کارسختی پذیر، با حرارت دادن، افزایشی در استحکام آلیاژ مشاهده نمی شود.
مهم ترین عملیات حرارتی که برای بر روی آلیاژهای آلومینیوم انجام می شود عبارت است از:
آنیل (Annealing)
آنیل کردن برای هر دو دسته آلیاژ ها برای عملیات نرم کردن به کار می رود. آنیل کامل و آنیل جزئی، تنها عملیات حرارتی هستند که برای آلیاژهای عملیات حرارتی ناپذیر به کار می روند. تنها استثنا آلیاژ های سری 5000 هستند که برخی اوقات عملیات پایدار کردن دمای پایین روی آن ها انجام می شود.
آنیل کردن بسته به آلیاژ در بازه دمایی 300 تا 410 درجه سانتی گراد انجام می گیرد. زمان گرم کردن بسته به اندازه بار و نوع آلیاژ از نیم تا 3 ساعت متفاوت است. توجه داشته باشید که پس از عملیات، بیشینه نرخ سرد کردن نباید از 20 درجه سانتی گراد در ساعت بیشتر شود تا دمای قطعه به زیر 290 درجه سانتی گراد برسد. زیر این دما، نرخ سرد کردن اهمیتی ندارد.
انحلال (Solutionizing)
این عملیات برای آلیاژهای عملیات حرارتی پذیر قابل انجام است و شامل یک فرآیند عملیات حرارتی است که در آن عناصر آلیاژی وارد محلول جامد می شوند و توسط کوئنچ سریع در محلول می مانند. عملیات حرارتی بعدی در دماهای پیک، یعنی پیرسازی یا پیرسازی طبیعی در دمای اتاق به آلیاژ اجازه می دهد تا رسوب گذاری کنترل شده ای روی عناصر آلیاژی داشته باشد و باعث افزایش استحکام و سختی آلیاژ شود.
دما و زمان عملیات حرارتی نقشی فوق العاده مهم در انحلال عناصر آلیاژی و رسوب گذاری آن ها دارند. برای دستیابی به خواص مکانیکی مناسب، بهتر است که دما نزدیک به دمای یوتکتیک باشد. در این محدوده، بیشترین میزان انحلال عنصر آلیاژی در محلول جامد وجود دارد. گرم کردن بیش از این مقدار، باعث تضعیف خواص مکانیکی قطعه می شود.
سرد کردن سریع (Quenching)
کوئنچ عملیاتی است که به منظور افزایش استحکام در آلیاژهای آلومینیوم اجرا می شود. هدف از کوئنچ، باقی ماندن عناصر آلیاژی در محلول جامد تا دمای اتاق است. سرعت کوئنچ مهم است و بر استحکام قطعه نهایی تاثیر می گذارد. زمان کوئنچ وابسته به مقطع قطعه است و می تواند از 5 تا 15 ثانیه برای قطعات با ضخامت 4/0 تا 7/12 میلی متر متغیر باشد. به طور کلی، رسوب گذاری بیشتر آلیاژهای آلومینیوم از دمای حدودی 450 درجه سانتیگراد شروع می شود. بنابراین نباید به آلیاژ اجازه داد تا پیش از کوئنچ به زیر این دما برسد.
معمولا برای سرد کردن آلیاژ از آب استفاده می شود. اما در مواردی نیاز است که این کار با سرعت کمتری انجام شود که می توان از آب گرم شده تا 65 – 80 درجه سانتی گراد، آب جوش، محلول های آبی پلی آلکالاین گلیکول، پاشش هوا یا انواع روغن های صنعتی استفاده کرد. این کار برای قطعات با اشکال پیچیده مثل قطعات فورج، اکستروژن و آلیاژهای ریخته شده انجام می شود تا اعوجاج کمتری در آن ها ایجاد شود.
پیر سختی (Age Hardening)
پس از عملیات انحلال و کوئنچ، نوبت به عملیات رسوب سختی (پیرسختی) آلیاژ می رسد. سخت سازی می تواند در دمای اتاق (پیرسازی طبیعی) یا توسط یک عملیات حرارتی رسوب پذیری (پیرسازی مصنوعی) انجام شود
در برخی از آلیاژ ها مخصوصا سری 2000، عملیات کار سرد روی مواد تازه کوئنچ شده به طور چشمگیری پاسخ به عملیات رسوب گذاری بعدی را افزایش می دهد. از این پدیده برای اعمال مقدار کنترل شده ای از نورد یا کشیدن (مثل عملیات اکستروژن، کشش میله و صفحه) برای ایجاد خواص مکانیکی بهتر استفاده می شود.
زمانی که پیرسازی طبیعی آلیاژهای آلومینیوم لازم است، از 5 روز برای آلیاژ های سری 2000 تا حدود 30 روز برای آلیاژ های دیگر متفاوت است. آلیاژ های سری 6000 و 7000 به طور چشمگیری در دمای اتاق پایداری کمتری دارند و به تغییر خواص مکانیکی تا سال ها ادامه می دهند. در برخی از آلیاژها، پیرسازی طبیعی ممکن است که با نگهداری در دمای 18- درجه سانتی گراد یا پایین تر به تعویق افتاده یا سرکوب شود.
توجه داشته باشید که عملیات شکل دهی، صاف کردن یا سکه زنی باید پیش از این که پیرسازی خواص ماده را به طور چشمگیری تغییر دهد، انجام شود.
شکل دادن فلزات و انواع روشهای آن
شکل دادن فلزات امروزه شکل دادن فلزات و آشنایی کامل با انواع آن برای ساخت و تولید...پیرسازی مصنوعی، عملیات رسوب گذاری در دمای بالا و با زمان کوتاه است. دما از 115 تا 200 درجه سانتی گراد و زمان از 5 تا 48 ساعت متفاوت است. همانند عملیات حرارتی انحلال، کنترل دقیق دما و تغییرات دمای فرآیند بسیار مهم هستند و دما نباید خارج از تلرانس 7± تعیین شده باشد.
گرچه زمان هم به اندازه دما نقش تعیین کننده ای در خواص نهایی قطعه دارد. اگر پیرسختی بیش از زمان مجاز انجام شود، پدیده Over Aging اتفاق می افتد و تاثیر منفی بر استحکام نهایی قطعه می گذارد.
نشانه گذاری آلیاژهای آلومینیوم
در هنگام نام گذاری آلیاژهای آلومینیوم، به جز عدد اصلی 4 رقمی که معرف نوع آلیاژ است، حروفی مشاهده می شوند که معرف نوع عملیات حرارتی یا مکانیکی انجام شده بر روی آلیاژ هستند. برخی از این حروف برای آلیازهای کارسختی پذیر و پیر سختی پذیر مشابه هستند. اما برخی از آن ها به طور خاصی برای هر کدام از این دسته ها استفاده می شوند. در این بخش به معرفی این علائم خواهیم پرداخت.
نشانه گذاری آلیاژهای عملیات حرارتی پذیر (آلیاژهای پیرسخت شده)
نشانه های T و W برای نشانه گذاری آلیاژهای ریختگی و کارشده ای استفاده می شوند که با عملیات حرارتی مستحکم شده اند. بعد از نشانه T رقم های 1 تا 10 می آیند که هر یک نشان دهنده ترتیب عملیات خاصی بر روی محصول هستند.
علاوه بر این موارد، گاهی بر برخی از آلیاژها رقم های اضافه ای مشاهده می شود:
نشانه گذاری آلیاژهای عملیات حرارتی ناپذیر (آلیاژهای کارسخت شده)
محصولاتی که با عملیات کارسختی مستحکم شده اند, توسط علامت H نشانه گذاری می شوند که به دنبال آن دو یا چند رقم آمده است. اولین رقم بعد از H نشان دهنده نوع عملیاتی است که بر روی محصول انجام گرفته است.
اما رقم بعد از H1، H2 و H3 نشانگر درجه کارسختی است و بین 1 تا 8 متغیر است.
دیدگاه کاربران
سلام و احترام
جدولی از تناسب حد سختی ها مختلف و دمای لازمه و زمان فرایند برای آلومینیوم 7075 موجود است؟
نمودار استحکام و دمای آن به صورت اختصاصی چگونه است؟