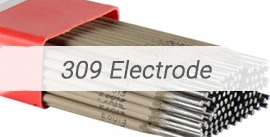
مقایسه فولاد CK45 با فولاد MO40
فولاد Mo40 چیست؟
فولاد Mo40 که تحت عنوان AISI 4140 در استانداردهای بینالمللی شناخته میشود، یک فولاد آلیاژی است که به دلیل داشتن مولیبدن و کروم، مقاومت بالایی در برابر سایش و خستگی دارد و بیشتر در ساخت قطعاتی مانند میل لنگ و شفتها استفاده میشود.
فولاد CK45 چیست؟
فولاد CK45 یا AISI1045 یک فولاد کربنی با استحکام مناسب است که برای قطعاتی که نیاز به مقاومت در برابر فشار و استحکام دارند، مانند قطعات خودرویی و ماشینآلات سنگین، مناسب است.
ترکیب شیمیایی فولاد CK45 و MO40
فولاد MO40 (AISI 4140) و فولاد CK45 (AISI 1045) هر دو فولادهای کربنی و آلیاژی هستند که در صنایع مختلف کاربرد دارند، اما تفاوتهای مشخصی در ترکیب شیمیایی و ویژگیهای آنها وجود دارد که بر روی خواص مکانیکی و کاربردهای آنها تاثیر میگذارد. در ادامه، ترکیب شیمیایی این دو فولاد و تفاوتهای آنها بهطور کامل بررسی میشود.
نوع فولاد | C | Si | Mn | P | S | Cr | Mo | Ni | Cr+Mo+Ni |
MO40 (1.7225) AISI 4140 | 0.38-0.45 | max 0.4 | 0.6 – 0.9 | max 0.025 | max 0.035 | 0.9-1.2 | 0.15 – 0.3 | Max 0.2 | – |
CK45 (1.1191) AISI 1045 | 0.42-0.5 | max 0.4 | 0.5-0.8 | max 0.03 | max 0.035 | – | – | – | 0.63 |
توضیحات:
- این فولاد فاقد مولیبدن و کروم است ولی ممکن است در مقادیر خیلی پایینتری حضور داشته باشند.
- فولاد CK45 نسبت به فولاد MO40 دارای مقدار بیشتری کربن است. این مقدار بیشتر کربن موجب افزایش سختی و استحکام کششی فولاد CK45 میشود، اما در عوض این مقدار کربن بالاتر موجب کاهش چقرمگی و انعطافپذیری آن میشود.
- فولاد MO40 حاوی مولیبدن است که موجب افزایش مقاومت به سایش، استحکام در دماهای بالا و مقاومت به خوردگی میشود. این عنصر به ویژه در صنایع سنگین و شرایطی که نیاز به مقاومت بیشتر به شوک و سایش است، اهمیت دارد. در حالی که CK45 فاقد مولیبدن است و نمیتواند به این ویژگیها دست یابد.
- مقدار کروم در MO40 بسیار بیشتر از CK45 است. کروم به فولاد توانایی مقاومت در برابر خوردگی، سختی و قابلیت سختسازی را میدهد. این عنصر همچنین به بهبود قابلیت جوشکاری و جلوگیری از اکسیداسیون فولاد در شرایط مختلف کمک میکند.
- مقدار منگنز در MO40 کمی بیشتر از CK45 است. منگنز نقش مهمی در افزایش استحکام و مقاومسازی فولاد در برابر سایش و ضربه دارد. این تفاوت میتواند به بهبود خواص مکانیکی MO40 نسبت به CK45 کمک کند.
فولاد CK45 چیست و چه کاربردی دارد؟
فولادها بهعنوان یکی از مهمترین مواد اولیه در صنایع مختلف، نقش بیبدیلی در پیشر...مقایسه خواص فیزیکی و حرارتی CK45 با فولاد MO40
خواص فیزیکی | MO40 | CK45 |
چگالی | 7.85 g/cm³ | 7.85 g/cm³ |
نقطه ذوب | 1416– 1540 °C | 1380 – 1518 °C |
رسانایی حرارتی | 43 W/m·K | 50 W/m·K |
انبساط حرارتی | 12 × 10⁻⁶ /°C | 12 × 10⁻⁶ /°C |
مقاومت الکتریکی | 0.00000062 Ω·m | 0.00000062 Ω·m |
مقایسه خواص مکانیکی
خواص مکانیکی | MO40 | CK45 |
استحکام تسلیم (Yield Strength) | 655 – 850 MPa | 500 – 700 MPa |
استحکام کششی (Tensile Strength) | 850 – 1000 MPa | 700 – 900 MPa |
طول دفرماتور (Elongation) | 20 – 30% | 16 – 20% |
سختی برینل | 200 – 250 HB | 170 – 210 HB |
چقرمگی (Toughness) | 30 J (در دمای اتاق) | 25 J (در دمای اتاق) |
مقاومت به خستگی | 250 MPa | 200 MPa |
مقاومت به سایش | عالی | خوب |
مدول الاستیسیته | 210 GPa | 210 GPa |
توضیحات:
- رسانایی حرارتی: فولاد CK45 دارای رسانایی حرارتی بیشتر از MO40 است که میتواند به بهبود انتقال حرارت در برخی کاربردها کمک کند.
- مقاومت به خوردگی: هر دو فولاد مقاومت متوسطی در برابر خوردگی دارند، اما فولاد MO40 به دلیل عناصر آلیاژی بیشتر (مانند کروم و مولیبدن) ممکن است مقاومت بیشتری داشته باشد. حضور کروم در ترکیب فولاد MO40باعث افزایش مقاومت به خوردگی آن در محیطهای کلریدی میشود. این فولاد مقاومت مناسبی در برابر زنگزدگی در شرایط معمول دارد، اما در صورت تماس طولانی با محیطهای نمکی غلیظ، خطر خوردگی حفرهای (Pitting Corrosion) وجود دارد. CK45 به دلیل نبود عناصر آلیاژی مقاوم به خوردگی مانند کروم و مولیبدن، در محیطهای نمکی مقاومت بسیار کمتری دارد و زنگزدگی سطحی سریعتر اتفاق میافتد.
- در محیطهای اسیدی MO40 (AISI 4140)مولیبدن موجود در این فولاد مقاومت آن را در برابر برخی اسیدهای ضعیف (مانند اسید سولفوریک رقیق) افزایش میدهد. با این حال، در برابر اسیدهای قوی یا غلیظ مقاومت محدودی دارد و نیاز به پوششهای محافظتی (مانند آبکاری) برای استفاده در این شرایط است. CK45 (AISI 1045) این فولاد به دلیل عدم وجود عناصر آلیاژی خاص، در برابر اسیدهای ضعیف نیز مقاومت کمی دارد و سریعتر دچار خوردگی میشود. استفاده از آن در محیطهای اسیدی بدون پوشش محافظ توصیه نمیشود.
- فولاد MO40 جوشپذیری خوبی ندارد زیرا خطر ترک حرارتی در آن بسیار بالا است. در فولاد CK45 به دیلیل کربن متوسط تا بالایی که دارد جوشکاری با یکسری ملاحظات انجام میشود.
- فولاد MO40 سختی پذیری خوب و متوسطی دارند و برای مصارف گرم تا 500 درجه مناسب هستند و میتواند در روغن سخت شود. در مقابل فولاد در مقابل فولاد CK45 سختی پذیری کمی در آب یا روغن دارد ولی سخت کردن سطحی مناسب است که پوسته سختی به این فولاد می دهد.
گریدهای معادل در استانداردهای مختلف

مقایسه فولاد MO40 (AISI 4140) و CK45 (AISI 1045) در عملیات حرارتی
فولاد AISI 4140 (Mo40) و AISI 1045 (CK45) در فرایندهای حرارتی و مکانیکی تفاوتها و شباهتهایی دارند. دمای آهنگری برای AISI 4140 در بازه 900 تا 1200 درجه سانتیگراد قرار دارد و از آهنگری زیر 850 درجه باید خودداری شود، در حالی که برای AISI 1045 این دما ابتدا به 750 تا 800 درجه و سپس به 1100 تا 1200 درجه افزایش مییابد. عملیات نرمالایزینگ برای AISI 4140 در دمای 870 تا 900 درجه انجام میشود، اما در AISI 1045 این دامنه اندکی بالاتر و بین 870 تا 920 درجه سانتیگراد است. هر دو فولاد پس از این عملیات در هوای ساکن سرد میشوند.
در آنیل (بازپخت)، هر دو فولاد در دمای مشابه 800 تا 850 درجه سانتیگراد حرارت داده میشوند و به آرامی در کوره سرد میشوند. با این حال، AISI 4140 به دلیل وجود عناصر آلیاژی قابلیت ماشینکاری بهتری پس از آنیل دارد. برای سختکاری سطحی، AISI 4140 در دمای 840 تا 875 درجه و AISI 1045 در دمای 820 تا 860 درجه گرم شده و پس از کوئنچ در روغن یا آب، عملیات تمپر بر روی آنها انجام میشود.
در تمپر، AISI 4140 دارای دامنه دمایی 550 تا 700 درجه سانتیگراد است و از دمای 250 تا 375 درجه باید اجتناب شود، در حالی که AISI 1045 در بازه 400 تا 650 درجه سانتیگراد حرارت داده میشود. به طور کلی، AISI 4140 برای کاربردهایی که نیاز به مقاومت بالا در برابر سایش، حرارت و ضربه دارند، مناسبتر است، در حالی که AISI 1045 به دلیل قیمت کمتر و سادگی فرایند، برای قطعات عمومی انتخاب بهتری است.
خلاصه و مقایسه فولادهای AISI 4140 (Mo40) و AISI 1045 (CK45)
موضوع | AISI 4140 (Mo40) | AISI 1045 (CK45) |
دمای آهنگری | 900 تا 1200 درجه سانتیگراد. جلوگیری از آهنگری زیر 850 درجه. | 750 تا 800 درجه (گرمایش اولیه) ، 1100 تا 1200 درجه (گرمایش نهایی). جلوگیری از آهنگری زیر 850 درجه. |
نرمالایزینگ | 870 تا 900 درجه سانتیگراد، سرد شدن در هوای ساکن. | 870 تا 920 درجه سانتیگراد، 10 تا 15 دقیقه نگهداری و سرد شدن در هوای ساکن. |
آنیل (بازپخت) | 800 تا 850 درجه سانتیگراد، سرد کردن آهسته در کوره. سختی نهایی: 241 برینل. | 800 تا 850 درجه سانتیگراد، سرد کردن آهسته در کوره. |
سختکاری سطحی | 840 تا 875 درجه سانتیگراد، کوئنچ در روغن یا آب، سپس تمپر فوری. | 820 تا 860 درجه سانتیگراد، کوئنچ در آب یا روغن، سپس تمپر فوری. |
تمپر | 550 تا 700 درجه سانتیگراد (اجتناب از محدوده 250-375 درجه). | 400 تا 650 درجه سانتیگراد، زمان نگهداری وابسته به ضخامت. |
مقایسه کاربردهای فولاد MO40 و CK45
فولادهای MO40 (AISI 4140) و CK45 (AISI 1045) در بسیاری از صنایع کاربرد دارند، اما به دلیل تفاوت در ترکیب شیمیایی و خواص مکانیکی، هر یک در کاربردهای خاصی برجسته هستند. فولاد MO40 به دلیل وجود مولیبدن و کروم، برای شرایط سخت و نیاز به مقاومت بالا در برابر سایش، ضربه و دماهای بالا مناسب است. این فولاد در صنایع خودروسازی برای قطعاتی مانند میللنگها و شفتها، در صنایع نفت و گاز برای ابزارهای حفاری، در ماشینآلات سنگین برای چرخدندهها و قطعات تحت فشار بالا، در تولید قالبها و ابزارآلات صنعتی، و حتی در صنعت هوافضا برای قطعات پرنده و موتورهای جت استفاده میشود.
از سوی دیگر، فولاد CK45، به دلیل استحکام و سختی مناسب و هزینه کمتر، بیشتر در کاربردهای عمومیتر و بارهای متوسط استفاده میشود. این فولاد در صنایع خودروسازی برای قطعاتی مانند میللنگهای موتورهای کمبار و چرخدندهها، در ماشینآلات صنعتی برای قطعاتی نظیر شفتها و میلهها و در ساختوساز برای تیرها و اتصالات ساختمانی مورد استفاده قرار میگیرد. علاوه بر این، فولاد CK45 به دلیل قابلیت ماشینکاری خوب، برای ابزارهای دستی مانند چکشها و پیچگوشتیها و در صنعت کشاورزی برای تیغهها و قطعات ماشینآلات کشاورزی نیز کاربرد دارد.
MO40 برای کاربردهای پیشرفته، سخت و نیازمند مقاومت بالا مناسبتر است، در حالی که CK45 به دلیل قیمت مقرون به صرفه و سادگی فرایند، برای کاربردهای عمومی و بارهای متوسط گزینه بهتری است.
صنعت/کاربرد | MO40 (AISI 4140) | CK45 (AISI 1045) |
خودروسازی | میللنگها، شفتها | میللنگهای کمبار، چرخدندههای با بار متوسط |
نفت و گاز | ابزارهای حفاری (دکلها، متهها) | – |
ماشینآلات صنعتی | قطعات سنگین (چرخدندهها، شفتها) | قطعات با بار متوسط (شفتها، پیچها، اتصالات) |
ساخت و ساز | قالبهای صنعتی و قطعات پرس | اتصالات ساختمانی، تیرها، لولهها و تجهیزات استاتیک |
ابزارآلات | قالبهای صنعتی و برش | چکشها، آچارها، پیچگوشتیها |
کشاورزی | – | تیغهها، شفتها و اتصالات کشاورزی |
هوافضا | قطعات پرنده و موتورهای جت |
مقایسه قیمت
عوامل کلیدی مانند میزان مصرف مواد آلیاژی و هزینههای انرژی بر هزینه تمام شده فولاد اثر میگذارند که در ادامه به تفصیل بررسی میشوند.
1.تأثیر میزان مصرف مواد آلیاژی:
- MO40 (AISI 4140): این فولاد به دلیل حضور عناصر آلیاژی مانند کروم، مولیبدن و منگنز هزینه مواد اولیه بالاتری دارد. هرچند این عناصر موجب بهبود خواص مکانیکی و مقاومت فولاد میشوند، اما تأثیر مستقیم آنها بر قیمت نهایی مشهود است. به طور خاص، کروم و مولیبدن که از مواد گرانتر محسوب میشوند، نقش اصلی در افزایش قیمت مواد اولیه MO40 دارند.
- CK45 (AISI 1045): این فولاد به دلیل عدم استفاده از عناصر آلیاژی گرانقیمت و تکیه بر ترکیب سادهتر (کربن و منگنز) ، هزینه کمتری برای مواد اولیه دارد. به همین دلیل، در مقایسه با MO40، این فولاد برای کاربردهایی که نیاز به آلیاژهای پیشرفته ندارند، اقتصادیتر است.
2.تأثیر هزینههای انرژی:
- MO40: تولید و عملیات حرارتی این فولاد نیازمند دماهای بالا و کنترل دقیق در فرایندهایی مانند کوئنچ، تمپر و نیتراسیون است. این امر موجب افزایش مصرف انرژی و در نتیجه افزایش هزینه تولید میشود. علاوه بر این، به دلیل نیاز به تجهیزات پیشرفتهتر، هزینههای غیرمستقیم تولید نیز بیشتر است.
- CK45: عملیات حرارتی این فولاد نسبت به MO40 سادهتر است و معمولاً به دماهای پایینتر و کنترل کمتری نیاز دارد. به همین دلیل، هزینه انرژی در فرایند تولید این فولاد به طور محسوسی کمتر است. این امر باعث میشود CK45 در تولیدات انبوه و کاربردهای عمومی گزینهای مقرون به صرفه باشد.
3.بهرهوری تولید:
- MO40: به دلیل پیچیدگی در فرایندهای تولید و نیاز به زمان بیشتر برای عملیات حرارتی و کنترل کیفیت، بهرهوری کلی تولید نسبت به فولاد CK45 کمتر است.
- CK45: این فولاد به دلیل فرایندهای تولید سادهتر و مصرف انرژی کمتر، زمان تولید کوتاهتری دارد و بهرهوری بالاتری ارائه میدهد.
4.هزینههای جانبی :
- مانند حمل و نقل و بستهبندی در فولاد MO40 معمولاً بیشتر است، زیرا این فولاد به دلیل حساسیت بالاتر نیاز به محافظت بیشتری در فرایند حمل و نقل دارد. این در حالی است که فولاد CK45 به دلیل ساختار سادهتر و عدم نیاز به بستهبندی پیچیده، هزینه کمتری در این بخش دارد.
- در نهایت، فولاد MO40 به دلیل ترکیب آلیاژی خاص و فرایندهای تولید پیچیدهتر، هزینه کلی بالاتری دارد و برای کاربردهایی که نیازمند استحکام و مقاومت بالا هستند، مناسبتر است. از سوی دیگر، فولاد CK45 به دلیل قیمت تمامشده کمتر و تولید سادهتر، انتخابی مقرونبهصرفهتر برای کاربردهای عمومی و بارهای متوسط به شمار میآید.
جمعبندی درباره مقایسه فولادهای MO40 و CK45
فولادهای MO40 (AISI 4140) و CK45 (AISI 1045) از نظر ترکیب شیمیایی، خواص مکانیکی، عملیات حرارتی، هزینه تولید و کاربردها تفاوتهای قابلتوجهی دارند. فولاد MO40 با ترکیب پیچیدهتر شامل کروم و مولیبدن، مقاومت به خوردگی، سختی و چقرمگی بالایی دارد و در دماها و فشارهای بالا عملکرد مطلوبی ارائه میدهد. این ویژگیها آن را برای کاربردهای صنعتی سنگین بسیار مناسب میسازد. از طرف دیگر، فولاد CK45 یک فولاد کربنی ساده با خواص مکانیکی متوسط است که به دلیل مقدار بالای کربن، سختی و استحکام مناسبی دارد اما مقاومت کمتری در برابر شرایط سخت محیطی از خود نشان میدهد.
عملیات حرارتی فولاد MO40 پیچیدهتر است و شامل فرایندهایی مانند کویلکاری و نیتراسیون میشود که موجب افزایش سختی و مقاومت به سایش این فولاد میگردد، هرچند که هزینه تولید را نیز بالا میبرد. در مقابل، فولاد CK45 نیاز به عملیات حرارتی سادهتری دارد و برای کاربردهایی که نیاز به سختی متوسط دارند، گزینهای اقتصادیتر محسوب میشود.
از نظر هزینه تولید، فولاد MO40 به دلیل ترکیب شیمیایی پیشرفتهتر و فرایندهای دقیقتر، هزینه بالاتری دارد و در بازه قیمت بیشتری قرار میگیرد. در مقابل، فولاد CK45 به دلیل ترکیب سادهتر و فرایند تولید کمهزینهتر، مقرون به صرفهتر است و قیمت پایینتری دارد.
از نظر کاربرد، فولاد MO40 در صنایع خودروسازی برای تولید میللنگ و محورهای سنگین، در صنعت نفت و گاز برای ابزارهای حفاری، و در هوافضا برای قطعات با شرایط سخت استفاده میشود. در حالی که فولاد CK45 بیشتر در ماشینآلات عمومی، ابزارآلات دستی و قطعات ساختمانی با بار متوسط به کار میرود.
در نهایت، انتخاب بین این دو فولاد به نیازهای صنعتی و شرایط کاربرد بستگی دارد. فولاد MO40 برای مواردی که استحکام بالا، مقاومت به سایش و چقرمگی در شرایط سخت مورد نیاز است، مناسبتر است. در مقابل، فولاد CK45 برای کاربردهایی که نیاز به هزینه کمتر و سختی متوسط دارند و شرایط محیطی معمولی است، گزینه بهتری خواهد بود. با توجه به شرایط عملیاتی و نیازهای خاص پروژه، مهندسان میتوانند از مزایای هر یک از این فولادها بهره ببرند. انتخاب صحیح فولاد نه تنها عملکرد بهتر قطعات را تضمین میکند، بلکه در کاهش هزینههای بلندمدت تعمیر و نگهداری نیز تأثیر قابل توجهی خواهد داشت.
دیدگاه کاربران