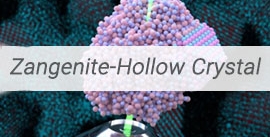
پرینت سه بعدی آلیاژهای تیتانیم که می توانند جایگزین استخوان شوند
پرینت سه بعدی آلیاژهای تیتانیم که می توانند جایگزین استخوان شوند
پرینت سه بعدی آلیاژهای تیتانیم
که می توانند جایگزین استخوان شوند
[box type=”shadow” align=”alignright” ]به گفتهی این پژوهشگران، آلیاژهای تیتانیوم، اولین انتخاب برای قطعات ارتوپدی مانند ایمپلنتهای زانو و لگن هستند. زیرا دارای خواص مکانیکی منحصربهفرد و مقاومت خوب در برابر عفونت میباشند.[/box]
[box type=”success” width=”1024″ ] ترجمه از گروه ترجمه ایران مواد
حرفه ای ترین تیم ترجمه مهندسی مواد کشور
[/box]
محققان در سنگاپور یک آلیاژ تیتانیوم-تانتالیوم پودری ساختهاند که میتواند برای ساخت جایگزینهای استخوانی زیستسازگار با استفاده از ذوب لیزری (SLM)، استفاده شود.
فلورنسیا ادیث ویریا از انستیتوی فنآوری تولید ای.استارز سنگاپور (SIMTech) و وای یی یئونگ از مرکز چاپ سهبعدی سنگاپور (SC3DP) در دانشگاه صنعتی نانیانگ برای تولید این آلیاژ جهت استفاده در فرآیند چاپ سهبعدی مشارکت داشتهاند.
به گفتهی این پژوهشگران، آلیاژهای تیتانیوم، اولین انتخاب برای قطعات ارتوپدی مانند ایمپلنتهای زانو و لگن هستند. زیرا دارای خواص مکانیکی منحصربهفرد و مقاومت خوب در برابر عفونت میباشند. اگرچه در ساخت نمونههای اولیهی زیست-پزشکی با استفاده از پودرهای پایه تیتانیوم، آلومینیوم موفقیت حاصل شده است، هنوز نگرانیهایی در مورد اثرات بلند مدت آلومینیوم روی سیستم عصبی انسان وجود دارد که باعث جستجو برای روشهای جایگزین، شده است.
آلیاژهای دارای تیتانیوم و تانتالیوم، به دلیل زیستسازگاری و برتری مکانیکی به تیتانیوم تنها، مطلوبتر هستند. اما، نقطهی ذوب بسیار بالای تانتالیوم (بیشاز ºC3000) به این معنی است که ساخت میکروکرههای آن برای جریان روان در چاپ SLM، از نقطهنظر اقتصادی، دور از انتظار است. پودرهای تجاری تانتالیوم اغلب از میکروذرات زبر و طویل، با اتمیزهکردن گازی، ساخته میشوند.
واسط لغزش
برای غلبه بر مشکل یادشده، تیم پژوهشگران، پودر تانتالیوم مضرس (زبر) را با پودرهای میکروکرهای تیتانیوم مخلوط کردند. پس از مخلوطکردن این دو ماده با یکدیگر به مدت نصف روز، پژوهشگران مشاهده کردند که مخلوط میتواند برای استفاده در SLM، به صورت بهتری پراکنده شود. آزمایشهای میکروسکوپی نشان دادهاند که شکل کروی تیتانیوم پس از مخلوط کردن، باقی میماند که اساس این موفقیت به شمار میرود.
ویریا میگوید: پودر تیتانیوم مانند یک واسط لغزش عمل میکند. این ماده پودر تانتالیوم را در مسیر حرکت با خود همراه میسازد و فرآیند SLM را امکانپذیر میکند..
پژوهشگران با اعمال یک الگوی شطرنجی که فلزات را همراه با حرکت به صورت بالا/پایین یا کنار-به-کنار برای کاهش تنشهای حرارتی، ذوب میکند، به صورت موفقی شکلهای سهبعدی تیتانیوم-تانتالیوم را با SLM تولید کردند. به صورت جالب توجه، فنآوری اشعهی X و تصویربرداری، نشان داده است که اضافه کردن تانتالیوم، همراه با انجماد سریع، تشکیل دانههای مستحکم و لایهای تیتانیوم را تهییج میکند و آن را پایدار میسازد.
پیشبینی پژوهشگران در مورد آلیاژهای تیتانیوم-تانتالیوم مبنی بر این است که آلیاژ یادشده میتواند تاثیرات “محافظت در برابر تنش” را که به علت الاستیک بودن بیشازحد ایمپلنتها و انتقال غیرکامل بارها به استخوانهای مجاور اتفاق میافتد، کاهش دهد. یئونگ میگوید این آلیاژها به صورت خاص برای کاربردهای ارتوپدی طراحی شدهاند و حتی پتانسیل نشاندادن رفتار “حافظهی-شکلی” پس از تغییر شکل را نیز دارا هستند. این قابلیت، میتواند امکانات چاپ قطعات شخصی برای بهبود درمان بیماران را فراهم کند.
[box type=”info” align=”alignright” width=”1124″ ]منبع : materialstoday.com
ترجمه : کاوه نبی [/box]
[divider]
۳D printed titanium alloy
could replace bone
Researchers in Singapore have developed a powderized titanium-tantalum alloy that could be used to make biocompatible bone replacements using Selective laser melting (SLM).
Florencia Edith Wiria from A*STAR’s Singapore Institute of Manufacturing Technology (SIMTech) and Wai Yee Yeong from the Singapore Centre for 3D Printing (SC3DP) at Nanyang Technological University collaborated to blend the alloy for use in the 3D printing process.
Titanium alloys are a primary choice for orthopedic devices such as knee and hip implants because they have excellent mechanical attributes and resist infection. While there has been success creating biomedical prototypes using titanium-aluminum-based powders, concern over aluminum’s long-term effects on human neurology has prompted a search for alternatives, the researchers say.
Alloys with titanium and tantalum are therefore desirable because they are biocompatible and mechanically superior to titanium alone. However, tantalum’s very high melting point (over 3,000°C) means it is not viable economically to turn into finely dispersed microspheres which flow smoothly for SLM printing. Commercial tantalum powders are usually made of rough, elongated microparticles that are formed via gas atomization.
Rolling medium
To overcome this problem, the team blended the jagged tantalum powder with another readily available powder of titanium microspheres. After mixing the two materials together for half a day, they observed the mixture could be spread more evenly for SLM use, which was favorable for the printing process. Microscopy experiments revealed that the titanium’s spherical shape was retained after mixing which was key to this success.
‘The titanium powder acts as a rolling medium,’ said Wiria. ‘It pushes the tantalum powder along and makes the processing by SLM possible.’
By applying a ‘checkerboard’ laser scanning pattern that melted metals in alternate up/down or side-to-side movements to reduce thermal stress, the researchers successfully produced titanium-tantalum 3D shapes with SLM. Surprisingly, X-ray and imaging technology showed that addition of tantalum, coupled with rapid solidification, promoted and stabilized the formation of strong, laminar titanium grains.
The researchers envision the titanium-tantalum alloys could reduce the ‘stress shielding’ effects that occur when implants are too elastic and transfer insufficient loads to neighboring bones. ‘These alloys are specifically designed for orthopedic applications, and even have the potential to show a type of ‘shape-memory’ after being deformed,’ said Yeong. ‘This opens up the possibilities of printing personalized devices to improve patient care.’
دیدگاه کاربران