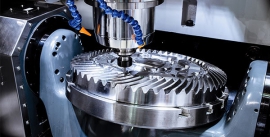
هیدرولیک و پنوماتیک (Hydraulic Vs. Pneumatics)
مایعات تراکم ناپذیرند. این خاصیت ساده اما مهم، باعث شده که از مایعات به عنوان ابزاری برای تبدیل و انتقال کار مکانیکی استفاده شود. به این معنی که شما با خیال راحت می توانید از مایعات برای طراحی ماشین ها استفاده کنید. ماشین هایی که در عین سادگی، با انرژی محرک بسیار کمی بتوانند نیروی چشمگیری را جابجا کنند.
انتقال انرژی توسط سیال دو مزیت عمده دارد: یکی قابلیت افزایش نیرو و دیگری قابلیت تغییر جهت سریع انتقال بدون ایجاد صدمه به سیستم. خاصیت انعطاف پذیر سیال در عبور از مجراها باعث ایجاد چنین خواصی می شوند.
در سیستم های هیدرولیک از یک مایع که معمولا روغن با پایه نفت خام است، برای انتقال انرژی استفاده می شود. در مقابل، پنوماتیک از سیال گازی استفاده می کند. در واقع، در این سیستم ها انتقال قدرت توسط جریان سیال پر فشار در خطوط انتقال (لولهها و شیلنگ ها) ایجاد می شود. اما انتقال قدرت در سیستم های مکانیکی سابق با استفاده از اجزایی مانند بادامک، چرخ دنده، گاردان، اهرم، کلاچ و… انجام می گرفت.
به طور کلی می توان گفت پنوماتیک در مواردی که نیروهایی نسبتاً پایین (حدود یک تن) و سرعت های حرکتی بالایی نیاز باشد، استفاده می شود. در صورتی که سیستم های هیدرولیک عمدتاً در مواردی که قدرت بالا و سرعت های کنترل شده و دقیق مورد نظر باشد، استفاده می شوند.
اما چرا به جای سیستم های سابق انتقال انرژی، بهتر است از هیدرولیک و پنوماتیک استفاده شود؟
- وجود قطعات محرک کمتر در سیستم
- امکان دست یابی به حرکت های خطی یا دورانی با قدرت بالا و کنترل مطلوب
- امکان کنترل نیروهای بزرگ خروجی را با اعمال نیرویی کم مانند باز و بسته کردن شیرها
- عدم وجود محدودیت های مکانی برای نصب این سیستم ها
- داشتن هزینه پایین به دلیل اصطکاک کم، قطعات ارزان تر و طراحی ساده
- قابلیت ایجاد سیستمی مقاوم در برابر تنش های ناگهانی با استفاده از سوپاپ های اطمینان و سوئیچ های فشاری و حرارتی
مبنای عملکرد سیستم های هیدرولیک و پنوماتیک چیست؟
بهتر است قبل از آشنایی تخصصی و مجزا با هریک از این سیستم ها، ابتدا اصول کلی عملیات آن ها را بررسی کنیم. در ابتدای مسیر انتقال قدرت با یک سیال تحت فشار (تراکم پذیر یا تراکم ناپذیر)، نیروی مکانیکی باید تبدیل به قدرت سیال شود. این تبدیل به وسیله پمپ انجام می شود.
در مرحله بعد لازم است این نیرو به نقطه ای دلخواه منتقل شود. این وظیفه را لوله ها، شیلنگ ها و بست ها به عهده دارند. پس از کنترل فشار و تعیین جهت جریان توسط شیرها، سیال تحت فشار به سمت عملگرها (سیلندرها یا موتور های هیدرولیک) هدایت می شود.
در عملگرها قدرت سیال به نیروی مکانیکی مورد نیاز (به صورت خطی یا دورانی) تبدیل می شود. اساس کار تمام سیستم های هیدرولیکی و نیوماتیکی بر قانون پاسکال استوار است. 3 اصل این قانون بیان می دارند:
- فشار تمامی نقاط سیال در حال سکون و عدم تحرک (با صرف نظر از وزن سیال) یکسان است.
- فشار استاتیکی در هر بازه بسیار کوچک زمانی در تمامی جهات یکسان است.
- در صورت تماس با سطوح، فشار سیال به صورت عمودی وارد می شود.
هیدرولیک چیست؟
از واژه هیدرولیک (Hydraulic) و ریشه آن «هیدرو» مفهوم مایع تداعی می شود. مثلاً زمانی که نام توربین هیدرولیک را می شنویم، حتما به ذهنمان خطور می کند نوعی توربین است که با آب مرتبط است. این تداعی خیلی هم از واقعیت دور نیست. سیستم های هیدرولیکی با آب، روغن یا مایعات دیگر کار می کنند.
از آن جایی که آب استعداد زنگ زدگی در سیستم را افزایش می دهد، معمولا در صنایع به عنوان انتقال دهنده انرژی کاربرد ندارد. از این رو بسیاری از صنایع هیدرولیک، روغن را ترجیح می دهند. در واقع اگر در صنعت از هیدرولیک نام برده شود، مقصود همان هیدرولیک روغنی است.
هیدرولیک روغنی و قابلیت انتقال انرژی دینامیکی و استاتیکی در آن، در حوزه مهندسی مکانیک و مهندسی صنایع برای انتقال سیگنال های انرژی و تولید نیرو کاربردهای زیادی دارند.
یک سیستم هیدرولیکی به چه صورتی کار می کند؟
در ابتدا روغن درون مخزن پس از گذشتن از صافی، از طریق لوله وارد پمپ می شود. پمپ را می توان با موتور الکتریکی، موتور هوایی، توربین گازی یا موتور درون سوز راه اندازی کرد. پس از استارت پمپ، فشار روغن در پمپ بیشتر می شود و نسبت به توانایی پمپ، فشار مورد نیاز تولید شده و به مصرف می رسد. میزان این فشار می تواند از 50 تا 500 بار برسد.
در مرحله بعد، روغن وارد شده به سیلندر با وارد کردن فشار، باعث اعمال نیروی زیادی بر میله پیستون می شود. در واقع اینجا پیستون یک مثال از عملگر است. عملگر، وظیفه تبدیل نیروی سیال به حرکت مکانیکی را بر عهده دارد. این عملگر است که کار نهایی را در سیستم هیدرولیکی انجام می دهد.
عملگرها انواع مختلفی دارند؛ مانند عملگر خطی (سیلندرها) و عملگرهای دورانی (هیدروپمپ ها). لازم به ذکر است که در انتهای فرایند، روغن برگشتی از طرف دیگر سیلندر به مخزن بازگردانده می شود.
شماتیک عملکرد یک سیستم هیدرولیکی
انواع سیستم های هیدرولیک
سیستم های هیدرولیک به دو گروه مدار باز و مدار بسته تقسیم بندی می شوند. تفاوت این سیستم ها در نحوه جریان سیال بین پمپ ها و عملگرها است. در هیدرولیک مدار بسته، جریان از پمپ به سمت عملگر (هیدروموتور) رفته و سپس دوباره به پمپ باز می گردد.
در هیدرولیک مدار باز، روغن پس از خروج از پمپ به سمت مخزن جریان می یابد و در آنجا ذخیره و خنک سازی شده و در ضمن عمل فیلتراسیون نیز روی آن انجام می گیرد تا ذرات فلز و پلیسه ها و سایر آلودگی ها از آن گرفته شود و سپس در مدار قرار می گیرد.
استفاده از روغن در این سیستم ها چه مزایایی دارد؟
بدیهی است که روغن باعث روانکاری عناصر لغزش مانند اجزای پیستون در داخل سیلندرها می شود و از خوردگی اجزا نیز جلوگیری می کند. روغن، مایعی است که در هنگام تغییر فشار ناشی از حرکت و جریان از یک نقطه به نقطه دیگر سیستم، تغییر حجم نمی دهد.
همچنین اگر سیستم به طور کامل پر باشد، سرعت و فشار آن قابل کنترل است. در سیستم های هیدرولیکی در کنار مایع، می توان از هوای فشرده یا برخی گازها و سیالات تراکم پذیر نیز استفاده کرد.
در انتخاب روغن هیدرولیک به نکات زیر توجه داشته باشید:
- خواص فیزیکی و مشخصه های جریان روغن باید عملکرد قابل قبولی متناسب با دستگاه هیدرولیک داشته باشند.
- لازم است روغن پس از به کارگیری در یک دوره زمانی بلندمدت عملکرد رضایت بخشی داشته باشد.
- سیال هیدرولیکی باید لایه ای نازک بین قطعات متحرک پدید آورد تا از سایش و اصطکاک آن ها کم کند.
- سیال هیدرولیکی به هیچ وجه نباید زنگ زدگی یا خوردگی دستگاه را تشدید و تسریع کند.
- ویسکوزیته آن در حدی باشد که بتوان آن را پمپ کرد.
- روغن اگر زیاد از حد رقیق باشد، سبب اتفاقاتی مانند روغن ریزی در سیستم می شود.
کاربردهای هیدرولیک
شاید بتوان گفت مهم ترین کاربرد سیستم های هیدرولیک عصر حاضر، در زمینه طراحی خودروهاست. این کاربردها با جایگزینی ترمز هیدرولیکی به جای ترمزهای مکانیکی کابلی و یا اهرمی آغاز شدند. در این سیستم، با به کارگیری انعطاف پذیری مایعات و با اعمال فشار به مایع، امکان انتقال نیروی ترمز به تمام چرخ های اتومبیل به وجود آمد.
امروزه از سیستم هیدرولیک به روش مشابهی در مکانیزم کلاچ خودروها استفاده می شود. البته این سیستم در دیگر بخش های های خودرو مانند جذب کننده ضربات (کمک فنر)، فرمان های هیدرولیکی و گیربکس اتوماتیک کاربردهای متداولی دارد.
به طور کلی سیستم های هیدرولیکی وقتی به کار می روند که قدرت زیاد و حرکت آهسته و یکنواختی مورد نیاز باشد و دقت حرکت عملگر ها بالا باشد. علاوه بر صنایع خودرو، دیگر کاربردهای گسترده هیدرولیک در صنایع زیر است:
- ماشین ابزار
- پرس سازی
- تاسیسات صنایع سنگین
- ماشین های راه و ساختمان و معادن
- هواپیما سازی
- کشتی سازی
- صنایع تبدیل انرژی
برتری های سیستم های هیدرولیکی
- تولید و انتقال نیروهایی بزرگ توسط قطعات کوچک هیدرولیکی که نسبت وزنی آن ها نسبت به دستگاه های سابق الکتریکی ۱ به ۱۰ است.
- سرهم بندی و نصب آسان قطعات به دلیل استاندارد بودن آن ها
- تبدیل ساده و سریع حرکت دورانی به حرکت خطی اسیلاتوری (رفت و برگشتی)
- قابلیت بالا در معکوس کردن جهت حرکت
- قابلیت تنظیم غیر متناوب نیرو، فشار، گشتاور و سرعت قطعات فعال
- عمر کاری بالای قطعات هیدرولیکی به دلیل استفاده از روغن
- هزینه های نگه داری پایین دستگاه ها و سیستم های هیدرولیکی (برای مثال توسط دستگاه مانومتر)
- امکان اتوماتیک کردن حرکات سیستم
معایب سیستم های هیدرولیکی
- افت فشار در حین انتقال مایع فشرده
- وجود خطر در هنگام کار با فشارهای قوی
- راندمان کمتر مولدهای نیروی هیدرولیکی نسبت به مولدهای نیروی مکانیکی
- امکان نشت فشار روغن و افت فشار در اثر اصطکاک مایعات در لوله و قطعات
- گرانی قطعات به دنبال بالا بودن مخارج تولید
نکات ایمنی در هنگام کار با سیستم های هیدرولیکی
نشت سوراخ سنجاق
در هنگام کار با فشارهای قوی، باید توجه زیادی به محکم جفت شدن مهره ها، لوله ها، دهانه تغذیه و مسیر کار قطعات فعال شود. یکی از محتمل ترین آسیب ها در سیستم های هیدرولیکی، نشت سوراخ سنجاق در شلنگ ها است.
توجه شود که مشخص کردن مکان این نشت ها بسیار دشوار است. افراد ممکن است متوجه مکان مرطوب، روغنی و یا کثیف در نزدیکی خط هیدرولیک شوند. اما وقتی دست یا انگشت خود را برای پیدا کردن سوراخ در طول حرکت می دهند، در صورت رسیدن به سوراخ، مایع مانند یک سرنگ به درون پوست تزریق می شود. بارها مشاهده شده که این فرد در آن لحظه احساس گزیدگی می کند. اما چند ساعت بعد، زخم شروع به درد می کند و زمانی که به پزشک مراجعه می شود، خیلی دیر شده و به دلیل عفونت زیاد، انگشت یا کل بازوی فرد باید قطع شود!
اتصال نامناسب
به هیچ وجه نباید یک پمپ فشار قوی را به سیستم هیدرولیک فشار کم متصل کرد. همچنین اتصال یک تجهیز فشار کم به سیستم فشار قوی نیز اشتباه محض است. چرا که احتمال پارگی تجهیز، شلنگ و یا اتصالات دستگاه وجود دارد.
در این راستا، در سیستم هیدرولیک یک دریچه تسکین فشار تعبیه می شود که از افت فشار جلوگیری می کند. این دریچه ها باید به طور مداوم تمیز شوند و نسبت به عملکرد صحیح آن ها اطمینان وجود داشته باشد.
نگهداری
نگهداری نامناسب یک سیستم هیدرولیک، می تواند منجر به به شکست اجزای دستگاه شود. مهم ترین موارد نگهداری هیدرولیک عبارتند از:
- بررسی دوره ای نشت روغن از شلنگ های فرسوده
- دور نگه داشتن روغن هیدرولیک از آلاینده ها و تعویض دوره ای فیلتر ها
- پوشاندن دائمی میله های سیلندر با روغن برای جلوگیری از بروز پوسیدگی
علاوه بر این موارد، در هنگام کار با سیستم های هیدرولیکی همواره نکات زیر را به یاد داشته باشید:
- ماشین آلات حتما باید در مکانی دور از دسترس کودکان قرار گیرند.
- هرگز هنگامی که موتور سیستم های هیدرولیک در حال کار است، عملیات سرویس انجام را انجام ندهید.
- سیلندرها را تا زمانی که واحدهای کاری در حالت کاملا ایمن قرار گیرند، جدا نکنید.
- در زمان حمل و نقل ماشین، قفل سیلندر را در جای خود محکم کنید.
- قبل از قطع کردن خطوط روغن، هرگونه فشار هیدرولیکی را برطرف کنید.
- برای تمیز کردن قطعات از یک حلال غیر فرار استفاده کنید.
پنوماتیک چیست؟
پنوماتیک در زبان یونانی به معنی باد یا نفس است. اما امروزه در صنعت و فناوری، به استفاده از هوای فشرده برای انتقال انرژی، پنوماتیک (نیوماتیک) می گویند. در این فرایند هوا توسط یک کمپرسور فشرده و در سیستم پنوماتیک مصرف می شود.
امروزه کمتر کارخانه یا مرکز صنعتی را می توان دید که از پنوماتیک استفاده نکند. انتقال انرژی در این سیستم به عنوان فرایندی بسیار تمیز، کم خطر و ارزان زبانزد است.
سیستم های پنوماتیکی به چه صورتی کار می کنند؟
طرز کار سیستم های نیوماتیک تفاوت چندانی با هیدرولیک ندارد، جز این که در این سیستم ها به جای سیال تراکم ناپذیر مایع از سیال تراکم پذیری مانند هوا استفاده می شود. در سیستم های پنوماتیک برای دست یابی به یک سیال پرفشار، هوا در یک کمپرسور فشرده می شود تا به فشار دلخواه برسد.
در مرحله بعد، این هوای فشرده در یک مخزن ذخیره می شود. در این جالت درجه حرارت هوا پس از فشردگی به شدت افزایش می یابد تا آن جا که ممکن است به قطعات سیستم آسیب برساند!
بنابراین هوای فشرده قبل از هدایت به خطوط انتقال قدرت، باید به اندازه کافی خنک شود. به علت وجود بخار آب در هوای فشرده و پدیده میعان در فرایند خنک سازی، لازم است از یک واحد بهینه سازی برای خشک کردن هوای پر فشار استفاده شود. بقیه فرایند انتقال قدرت، درست همانند هیدرولیک است.
چه زمانی از سیستم های پنوماتیکی استفاده می شود؟
به طور کلی زمانی از پنوماتیک استفاده می شود که نیرو و دقت بالا مورد نیاز نباشد. در مقابل اگر عکس العمل سریع عملگرها مد نظر باشد، سیستم های پنوماتیک مرجح هستند. در هر سیستمی که بتوان از سیالیت هوا و گاز کاربردی مبتنی بر انرژی دریافت کرد، پنوماتیک وارد عمل خواهد شد.
برای مثال، امروزه برای تست سوراخ نبودن بدنه هواپیما، فشار باد را میان جداره های بدنه اعمال می کنند. در صورتی که افت فشار اتفاق بیفتد، یعنی جایی از بدنه سوراخ است و نیاز به تعمیر دارد. می توان گفت کاربردهای زیر از مهم ترین استفاده های این سیستم در صنعت هستند:
- هدایت تانک نفر بر، موشک و ناوها در صنایع دفاع
- انتقال حرکت و نیرو در ماشین تراشکاری CNC و نظیر این دستگاه ها
- پر کردن شیشه نوشابه، چسب زنی و لفاف پیچی در صنایع بسته بندی
- گذراندن خمیر کاغذ از غلتک های صنایع تولید کاغذ
- اعمال فشار زیاد برای کشش آهن و یا فلزات دیگر و تخلیه کوره ها در صنایع متالورژی
- چرخاندن، برگرداندن و ایجاد تحرک در قطعات صنعتی
- باز و بسته کردن درب ها
- کنترل شیب کانوایر
دانشــنـامه کانوایر چیست ؟ کانوایر (Conveyor) کلمه ای انگلیسی به معنای حمل کننده است که به نام نقاله نیز معروف است. علم و صنعت کانوایر سعی بر آن دارد تا حمل و انتقال را با کمترین انرژی که منجر به کمترین هزینه می شود، به سر انجام برساند برای فرستادن قطعات روی آن
سیستم های پنوماتیکی چه مزایایی به همراه دارند؟
- عامل اصلی پیشبرد سیستم پنوماتیک هوا است که در همه جای زمین به وفور یافت می شود.
- هوای فشرده را می توان به وسیله لوله کشی به نقاط مختلف کارخانه هدایت کرد.
- هوای فشرده قابلیت ذخیره و انباشتگی در مخازن مخصوص را دارد. یعنی همیشه نیاز به کمپرسور نیست و می توان از سیستم نیوماتیک در مکان هایی که امکان نصب کمپرسور وجود ندارد هم استفاده کرد.
- افزایش و کاهش دما آسیبی به سیستم پنوماتیک نمی رساند. یعنی نوسانات حرارتی در عملکرد سیستم بازدارندگی ایجاد نمی کند.
- هوای فشرده خطر انفجار و آتش سوزی ندارد. از این رو تاسیسات حفاظتی خاصی نیاز نیست.
- راه اندازی قطعات پنوماتیک و اتصالات آن ارزان و ساده است.
- هوای فشرده در مقایسه با روغن هیدرولیک تمیزتر است. به دلیل این تمیزی، می توان از سیستم پنوماتیک در صنایع دارویی و نظایر آن استفاده کرد.
- سرعت حرکت سیلندرهای عملگر نیوماتیک با هوای فشرده، در حدود ۱ تا 3 متر بر ثانیه است. این سرعت در صنایع قابل قبول است و بسیاری ازعملیات صنعتی را می تواند اجرا کند.
- عوامل سرعت و نیرو در سیستم پنوماتیک قابل کنترل و تنظیم است.
- عناصر پنوماتیک در برابر تنش و بار اضافه مقاوم هستند و به آنها آسیبی نمی رسد. مگر این که افزایش بار سبب موجب توقف آن ها شود.
معایب سیستم های پنوماتیکی چیست؟
- امکان دارد به همراه هوای فشرده، مقداری رطوبت و ناخالصی نیز وارد سیستم شود. این ناخالصی ها بعضا با ایجاد واکنش هایی سبب خرابی در قطعات می شوند.
- هزینه استفاده از هوای فشرده تا حدودی به صرفه است. البته این صرفه اقتصادی تا وقتی است که فشار هوا برابر ۷ بار و نیروی حاصله با توجه به طول کورس و سرعت حداکثر بین ۲۰۰۰۰ تا ۳۰۰۰۰ نیوتن است.
- قبلا هم ذکر کردیم که برای ایجاد قدرت های بالا، مقرون به صرفه تر است که از نیروی هیدرولیک استفاده شود.
- هوای مصرف شده در سیستم پنوماتیک، موقع تخلیه از سیستم صدای زیادی ایجاد می کند. این موضوع نیاز به کاربرد صدا خفه کن را اجباری می کند.
- به دلیل تراکم پذیری هوا به خصوص در سیلندرهای پنوماتیکی که تحت بار قرار دارند، امکان ایجاد سرعت ثابت و یکنواخت وجود ندارد.
اهمیت نکات ایمنی در سیستم های پنوماتیکی
هوای فشرده ای که باعث حرکت ابزار می شود، ممکن است خطرآفرین نیز باشد. به خصوص در کاربردهایی که پنوماتیک برای کوبندگی و ضربه استفاده شود. در ادامه تعدادی از موارد ایمنی که باید در استفاده از سیستم های نیوماتیک به خاطر داشته باشید، ذکر می شوند:
- هرگز قبل از مطالعه توضیحات و راهنمای ابزار پنوماتیک از آن استفاده نکنید.
- همواره از دستکش ایمنی، عینک و سایر تجهیزات ایمنی استفاده کنید.
- استفاده از دنده ایمنی دستگاه اجباری است. این کار سبب جلوگیری از حوادث و بر طرف شدن مسئولیت از جانب اپراتور می شود.
- از عدم مسدود شدن و یا عدم پوسیدگی ابزار به طور مرتبا اطمینان کنید.
- تمام ابزار پنوماتیک را روغن کاری و تمیز کنید.
- از هیچ تجهیز جانبی که متعلق به ابزار پنوماتیک نیست، استفاده نکنید.
- از استارت سیستم و ابزار با فشار هوای بالاتر از آن چه توسط تولیدکننده مشخص شده است، خودداری کنید.
- براي جلوگیری از خطرات احتمالی، از قراردادن شیلنگ هوا در گردشگاه ها، نقطه های یکّه دار یا اشیای دندانه دار خودداری کنید.
- هنگام جابجا کردن ابزار مختلف و پس از تمام شدن عملیات، شلنگ هوا را ببندید.
- بهتر است از شلنگ هایی که مختص ابزارهای پنوماتیک ساخته شده اند، استفاده کنید. این شلنگ ها با استحکام شکست بالا ساخته می شوند و بسیار انعطاف پذیرند. (شلنگ های دارای حداقل فشار کاری 150 پوند بر اینچ مربع)
عملگرهای هیدرولیک و پنوماتیک
عملگرهای نهایی در سیستم های هیدرولیک و پنوماتیک معمولا سیلندرها و موتورها هستند. این عملگرها به کمک توانی که به دست آورده اند، میزان کار مشخصی را در سیستم انجام می دهند.
برای مثال، در یک دستگاه بالابر هیدرولیک، عملگر سیستم همان سیلندر یا جک هیدرولیک است. این سیلندر به کابین وصل می شود و آن را حرکت می دهد یا در یک دستگاه پرس ظروف که تحت سیستم پنوماتیک عمل می کند، عملگر سیستم، همان سیلندر پنوماتیکی است که قالب سنبه را بالا و پایین می برد. این حرکت قالب عملیات پرس و شکل دهی ظروف را به انجام می رساند.
در مثال بالابر، سیستم محرک، هیدرولیک است و روغن هیدرولیک نیز تراکم ناپذیر است. با این وجود، حرکت سیلندر هیدرولیک را در موقعیت های مختلف کورسِ سیلندر با دقت زیادی می توان تعیین کرد.
اگر فرض کنیم ارتفاع کورس بالابر هیدرولیک ۴ متر باشد، در ارتفاع های ۱ متری و ۲ متری و ۳ متری نیز می توان یک مکان توقف برای بالابر تعیین کرد. در این صورت کابین بالابر با رسیدن به این نقاط، دقیقاً در نقطه مورد نظر توقف می کند.
اما در مورد سیلندرهای پنوماتیک نمی توان این کار را انجام داد. چرا که هوا تا حدود زیادی تراکم پذیر است. بنابراین حرکت سیلندر پنوماتیک معمولاً همراه با نوسان و بریده بریده شدن حرکت صورت می گیرد. توقف آن نیز با کمی تأخیر انجام می شود.
بر همین اساس اگر در مثال بالابر، به جای سیلندر هیدرولیک، از سیلندر پنوماتیک استفاده می شد، موقعیت های مشخص شده را نمی توان به شکلی دقیق تعیین کرد. چون احتمالاً سیلندر پنوماتیک نمی تواند دقیقاً در نقاط تعیین شده توقف کند.
مقایسه سیستم های هیدرولیکی در برابر پنوماتیکی
جمع بندی
در این مقاله تلاش کردیم تا شما را با ساز و کار سیستم های هیدرولیکی و پنوماتیکی و استفاده های هر کدام آشنا کنیم. به طور کلی، برای صنایعی که تمیزی در آن ها اهمیت نداشته باشد و قدرت زیادی لازم باشد، بهتر است از هیدرولیک استفاده شود. در مقابل، در صنایع بهداشتی که نیروی کمی نیاز باشد، استفاده از فرایندهای پنوماتیک مرجح است.
دیدگاه کاربران