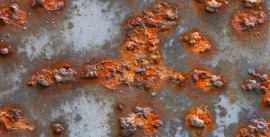
پوشش دهی توسط رسوب فیزیکی بخار (PVD)
رسوبدهی فیزیکی بخار ((PVD) Physical Vapor Deposition) یک تکنیک پوششدهی با استفاده از تبخیر است که در آن مواد از یک منبع جامد یا مایع به شکل اتم یا مولکول تبخیر میشوند و بخار در محیط خلاء، گاز فشار پایین و یا پلاسما زیرلایه را دربر میگیرد. این روش به دلیل قابلیت بالایی که در ایجاد فیلمهای نازک (Thin Films) و با خلوص بالا دارد، نسبت به بسیاری از روشهای لایهنشانی برتری داشته است.
اولین استفاده صنعتی از فناوری رسوبگذاری فیزیکی از فاز بخار مربوط به پوششدهی ابزارها در اوایل دهه 1980 بوده است که پوشــش TiN بر روی فولاد تندبر (HSS) و ابزار کاربید فلزی مورد اســتفاده قرار گرفت و با توسعه آن کاربردهای فراوانی یافت.
به طور کلی، فرآیندهای لایهنشانی PVD مبتنی بر دو روش تبخیر و کندوپاش بوده که تمایز اصلی بین این روش ها، منبع انرژی مورد استفاده است. فرآیند PVD برای رسوبگذاری پوششهای ساخته شده از نیتریدها، کاربیدها، اکسیدها و بورایدهای عناصری همچون Ti Cr ،Zr ،V و آلیاژهای بسیاری همچون مانند AlCr ،AlTi و TiSi کاربردهای فراوان دارد.
دمای فرآیند به طور معمول بین 250 تا 450 درجه سانتیگراد است. به دلیل اینکه دمای زیرلایه به طور قابل توجهی پایینتر از دمای ذوب ماده هدف است، پوششهای PVD در مواد حساس به دما کارایی پیدا میکنند. ضخامت پوششهای PVD از چندین نانومتر تا 15 میکرومتر متغیر است. مواد زیرلایه میتوانند شامل فلزات آهنی، فلزات غیرآهنی، کاربیدهای تنگستن و همچنین پلاستیک های پیش آبکاری شده باشند.
تکنیک PVD به چه صورتی اجرا می شود؟
اصول کلی روش رسوب دهی فیزیکی از فاز بخار شامل مراحل زیر است:
- تبدیل ماده تبخیر شده هدف به حالت گازی از طریق تبخیر، تصعید و یا کندوپاش
- انتقال اتمها از چشمه تبخیر به زیرلایه در فشار کاهش یافته
- رسوب این ذرات روی زیرلایه
- بازآرایی پیوند اتمها روی سطح زیرلایه
لایه نشانی به روش PVD به چه صورت هایی اجرا می شود؟
به طور کلی فرآیندهای لایهنشانی PVD مبتنی بر دو نوع تبخیر و کندوپاش است که هرکدام را مورد بررسی قرار میدهیم:
فرایندهای لایهنشانی مبتنی بر تبخیر (Evaporation)
این فرایندها میتوانند شامل روشهای تبخیر حرارتی، باریکه الکترونی، پرتو لیزر و قوس کاتدی باشند.
پوشش دهی به روش تبخیر حرارتی
فرآیند تبخیر حرارتی با بهرهگیری از فیلامان تنگستنی برای ذوب فلزاتی مانند آلومینیوم و مس که نقطه ذوب کمتر از 1500 درجه سانتیگراد دارند، مورد استفاده قرار میگیرد. پس از رسیدن فشار محفظه به محدوده 5-10 تور، از طریق الکترود مسی دارای آبگرد، جریان بالایی در حدود 100 تا 200 آمپر به بوته تنگستنی اعمال شده و موجب تبخیر مواد هدف که در داخل بوته قرار گرفته است، میشود. در نتیجه با تبخیر مواد هدف پوشش نازکی بر روی زیرلایه تشکیل میشود.
پوشش دهی با استفاده از باریکه الکترونی
تبخیر پرتو الکترونی زمانی اتفاق میافتد که ماده هدف با پرتو الکترونی که توسط فیلامنت تنگستنی تحت خلاء بالا منتشر میشود، منفجر شده و باعث ایجاد لایه مورد نظر بر روی زیرلایه شود. در این روش امکان تبخیر کلیه مواد دیرگداز وجود داشته و نیازی به حضور گاز خنثی در حین لایهنشانی نیست. به دلیل امکان لایهنشانی مواد با نقطه ذوب بالا، از این روش در صنعت الکترونیک، اپتیک، نیمههادیها و در دهههای اخیر برای اعمال پوششهای سد حرارتی (TBC) استفاده میشود.
تکنیک PLD
بر اثر برخورد لیزر به ماده هدف، در حد فاصل زیرلایه و ماده هدف، پلاسمای باریکی به نام پلامپ تشکیل میشود که اندازه آن در سرعت پوششدهی و ضخامت آن موثر است. بنابراین انرژی لازم برای تبخیر ماده هدف (Ti) توسط انرژی لیزر تامین میشود. در جریان تابش اشعه لیزر، اتمهای ماده هدف تبخیر شده و در محفظه پلامپ قرار میگیرد. با حضور گاز واکنشی نظیر نیتروژن در محفظه، امکان تشکیل لایه نازک و رسوب آن بر زیرلایه فراهم میشود.
این روش جزء روشهای موثر در لایهنشانی PVD بهشمار میرود؛ زیرا انرژی پرتوی لیزر مورد استفاده به قدری بالا است که لایهنشانی مواد دیرگدازی چون سرامیکها و مواد غیرفلزی را امکانپذیر میسازد.
استفاده از قوس کاتدی (Arc PVD)
فرآیند قوس کاتدی بر اثر تخلیه الکتریکی بین دو الکترود (آند و کاتد) در محیط خلا اتفاق میافتد. اصول کار به این صورت است که بعد از برقراری جریان بالا، سطح ماده هدف یونیزه شده و اتمهای یونیزه به سمت قطعه حرکت میکنند و در صورت حضور گاز واکنشی در اتمسفر محفظه، لایه مورد نظر بر روی زیرلایه تشکیل میشود.
روش قوس کاتدی با توجه به مزایایی همچون نرخ بالای رسوبگذاری، چسبندگی خوب به زیرلایه و داشتن صرفه اقتصادی محبوبیت بالایی جهت اعمال پوششهای سخت بر روی زمینه دارد؛ اما یکی از بزرگترین عیوب این روش، به وجود آمدن میکرو ذرات ذوب شده در پوشش است که برگرفته از مشخصات ذاتی قوس کاتدی است.
فرآیند لایهنشانی مبتنی بر پرتو یونی (IBAD)
در این روش، از یک تفنگ یونی که انرژی آن در حد کیلو الکترون ولت است، استفاده میشود. در حین فرآیند تبخیر، انرژی تفنگ یونی به اتمهای در حال تبخیر منتقل شده و سبب میشود که اتمها روی سطح زیرلایه رسوب کنند و موجب ایجاد لایه نازکی با چگالی بالا شوند. این روش بیشتر در لایهنشانی قطعات الکترونیکی مورد استفاده قرار میگیرد.
روش IBAD برای ایجاد پوششهای نیتریدی امکان زیادی را فراهم میکند. این نیتریدها نظیر TiN ،CrN ،VN و ZrN خواص شیمیایی و فیزیکی متفاوتی دارند.
فرآیند لایهنشانی مبتنی بر کندوپاش (Sputtering)
فرآیند کندوپاش شامل کندن اتم به وسیله گاز کندوپاش کننده (مانند گاز آرگون) از سطح ماده هدف و نشاندن آن بر زیرلایه است. این روش شامل مراحل زیر است:
الف) یونیزه شدن اتمهای گاز آرگون به دلیل اختلاف پتانسیل بالا بین کاتد و آند
ب) اعمال پتانسیل منفی بر روی ماده هدف و حرکت یون های مثبت آرگون با شتاب بالا
ج) بمباران ماده هدف توسط یونهای آرگون و کنده شدن مواد و پرتاب شدن آنها به سمت زیرلایه
د) تشکیل لایه مورد نظر بر روی زیرلایه
از متغیرهای تاثیرگذار در فرآیند کندوپاش میتوان به انرژی و جرم گاز خنثی (گاز کندوپاش کننده)، انرژی پیوند و جرم ماده هدف، فشار کاری محفظه و زاویه برخورد یونهای آرگون به سطح ماده هدف اشاره کرد.
با توجه به نوع پتانسیل اعمال شده و گازهای واکنش دهنده، انواع مختلفی از فرایندهای کندوپاش وجود دارند:
- DC Sputtering
- AC Sputtering یا RF
- Reactive Sputtering
- Magnetron Sputtering
کندوپاش با استفاده از سیستم DC
کندوپاش DC یک روش کندوپاش اولیه با استفاده از ولتاژ ثابت (DC) بین زیرلایه (آند) و ماده هدف (کاتد) است. معمولاً یونهای آرگون (Ar) به عنوان ذرات بمباران سطح ماده هدف استفاده میشوند. ولتاژ DC (0/5-5 کیلو ولت) اتمهای آرگون را یونیزه میکند و یک گاز یونیزه (پلاسما) تشکیل میدهد. کندوپاش DC برای رسوبگذاری مواد رسانا (فلزات) استفاده میشود. نقطه ضعف اصلی روش کندوپاش DC، چگالی بسیار کم یونهای آرگون است که نرخ رسوب پایینی را ایجاد میکند.
کندوپاش با استفاده از سیستم RF
در کندوپاش RF یک کاتد (ماده هدف) و یک آند وجود دارد که به صورت سری با یک خازن (C) بسته میشوند. منبع تغذیه یک منبع RF با ولتاژ بالا است که اغلب بر روی 13/56 مگاهرتز ثابت میشود. کندوپاش RF برای لایهنشانی فلزات و غیر فلزات مورد استفاده قرار میگیرد.
کندوپاش واکنشی
کندوپاش واکنشی از واکنشهای شیمیایی بین اتمهای سطح زیرلایه و گاز وارد شده به محفظه خلاء استفاده میکند. معمولاً اکسیژن یا نیتروژن به عنوان گازهای واکنش پذیر عمل میکنند. ماده هدف فلزی است. بخشی از گاز واکنشی در پمپها پایین میرود و بخش دیگر آن به پوشش نازک در حال رشد منتقل میشود.
کندوپاش مگنترونی
کندوپاش مگنترونی روشی برای تقویت کندوپاش DC با میدانهای مغناطیسی و الکتریکی متقاطع است که پلاسمایی با چگالی بالا تولید میکند. میدان مغناطیسی توسط آهنرباهای ثابتی که در پشت ماده هدف نصب شدهاند، ایجاد میشود. الکترونهای پلاسما در امتداد خطوط میدان مغناطیسی در یک مسیر مارپیچی حرکت میکنند و در طول مسیر خود با اتمهای آرگون برخورد کرده و یونهای بسیار بیشتری نسبت به روش DC تولید میکنند. تکنیکهای کندوپاش مگنترون یونیزه بالا اجازه رسوب پوششهای سخت را با نرخ یونیزاسیون بسیار بالاتر نسبت به تکنیکهای کندوپاش معمولی میدهند.
تکنیک PVD چه مزایایی دارد؟
پوشش دهی PVD همانند سایر روشها دارای مزایا و معایبی است. از جمله مهمترین مزایای این روش میتوان به موارد زیر اشاره کرد:
- اعمال پوششهای PVD بر روی ماده زیرلایه، باعث میشود که محصول نهایی ویژگیهایی اعم از چقرمگی شکست بالا، چسبندگی بالا، مقاومت به سایش بالا، سختی بالا، ضریب اصطکاک کم، پایداری حرارتی، خنثی بودن شیمیایی و همچنین مقاومت به اکسیداسیون و خوردگی خوب نسبت به موادی که دارای پوشش نیستند، داشته باشد.
- این پوششها اغلب قابلیت تحمل درجههای حرارتی بالا را دارند.
- پوششهای PVD خلوص بالایی دارند و امکان کنترل ساختار پوشش وجود دارد.
- با استفاده از روش PVD امکان لایه نشانی هر نوع مواد غیر آلی و بعضی از مواد آلی روی گروه متنوع و وسیعی از سطوح و زیرلایه ها فراهم شده است.
- پوششهای PVD سازگاری بالایی با محیط زیست دارند.
لایه نشانی PVD شامل چه محدودیتهایی میشود؟
- پوششدهی قطعات با شکل هندسی پیچیده در این روش امکانپذیر نیست.
- برخی از تکنیکهای رسوب دهی فیزیکی بخار به علت نیاز به محیط خلاء و دمای بالای محیط لایه نشانی، توجه و دقت بالایی را میطلبند.
تکنیک پوشش دهی PVD چه اهمیتی در صنایع مختلف دارد؟
پوششهای PVD طی سالهای گذشته توسعه روزافزونی داشته است به طوری که این فناوری در بسیاری از صنایع با تکنولوژیهای پیشرفته کاربردهای گستردهای یافته که به برخی از آنها اشاره میکنیم.
صنعت خودرو
اعمال پوششهای PVD بر روی رینگهای پیستون سهم قابل توجهی را در کاهش تلفات اصطکاک ناشی از افزایش فشار احتراق و بازچرخش گاز اگزوز ایفا میکنند. با اعمال پوشش بر روی چرخدنده گیربکس خودرو، شکست ناشی از ساییدگی به حداقل مقدار خود میرسد. در سالهای گذشته پوششهای چندلایه Cr/CrN به دلیل پایداری حرارتی و مقاومت به اکسیداسیون عالی برای لایهنشانی رینگ پیستون مورد استفاده قرار میگرفتند که امروزه از لایههایCrN ،CrCN و DLC به دلیل محدوده پایداری حرارتی گستردهتر و خواص روانکاری بیشتر استفاده میشود.
صنایع هوایی، برق و نیروگاهی
یکی از عوامل تاثیرگذار بر عمر پرههای توربینهای گازی، استفاده از پوششهای PVD است که باعث میشود مقاومت به فرسایش و خوردگی پرهها افزایش یافته و کارایی و بازده توربینها و محفظهها به حداکثر مقدار خود برسد. پوششهای سخت و مقاوم TiN ،CrN و AlCrN از جمله پوششهای مناسب برای این کاربردها هستند.
کنترل خوردگی توربین های گازی با طراحی نسل جدیدی از پوشش های کامپوزیتی
توربین های گازی دسته ای از ماشین های درون سوز هستند که از انرژی ناشی از احتراق س...صنایع ساخت و تولید
پوششهای PVD نقش مهمی در ساخت ابزارهای برش و شکلدهی (مانند هابها و شیپرهای دنده زنی) و قالبسازی (مانند قالبهای فورج، اکستروژن، دایکاست و تزریق پلاستیک) دارند. این پوششها باعث افزایش عمر قطعات شده و همچنین مقامت به سایش و خوردگی آنها را نیز افزایش میدهند.
پوششهای PVD در صنایع نفت، گاز و پتروشیمی برای ساخت سیت و گیتهای نفتی، صنایع ساختمان و تزئینی برای ساخت نماهای فلزی، کاشی و سرامیک، صنعت نساجی برای تولید سوزنهای ماشین آلات بافندگی، کشاورزی و مواد غذایی برای تهیه ابزارهای برنده محصولات کشاورزی، پزشکی و دارویی برای تولید ابزارآلات دندانپزشکی و جراحی و صنایع حمل و نقل ریلی و دریایی استفاده میشوند.
جمعبندی
رسوبدهی فیزیکی بخار یا PVD از تکنیکهای پیشرفته و پرکاربرد لایهنشانی است. این روش مبتنی بر دو روش تبخیر و کندوپاش بوده و برای رسوبگذاری پوششهای ساخته شده از نیتریدها، کاربیدها، اکسیدها و بورایدهای عناصری مانند تیتانیوم، کروم، وانادیم و زیرکونیم بسیار مناسب است. استفاده از تکنیک PVD باعث تولید محصولاتی مقاوم به سایش همراه با سختی بالا، ضریب اصطکاک کم، پایداری حرارتی عالی و مقاوم در برابر خوردگی و اکسیداسیون میشود. به همین جهت، از آن در صنایع High Tech همانند خودروسازی، نیروگاهی، ساخت و تولید استفاده میشود.
دانلود فقط با IP ایران امکانپذیر است. در صورت عدم مشاهده باکس قرمز رنگ دانلود، VPN خود را خاموش نموده و صفحه را رفرش کنید.
پسورد فایل فشرده : www.iran-mavad.com
دیدگاه کاربران
با سلام
لطفا منابع رو هم بفرمایید
سلام راهی برای دستیابی به منابع مطالب آورده شده وجود دارد ؟
سلام
لینک دانلود دیگه وجود نداره..
درود
ممنون از توجه شما
لینک مربوطه اصلاح شد.