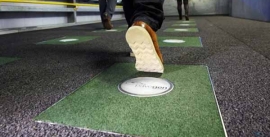
منیزیم جانشین تمام عیار آلومینیم در صنعت خودرو – همراه فیلم !!Shaping the future of magnesium car parts
منیزیم جانشین تمام عیار آلومینیم در صنعت خودرو
منیزیم جانشین تمام عیار آلومینیم در صنعت خودرو
Shaping the future of magnesium car parts
منیزیم ۷۵% سبکتر از فولاد و ۳۳% سبکتر از آلومینیوم میباشد و پس از ، آهن، سیلیسیم و اکسیژن، چهارمین عنصر فراوان روی کرهی زمین میباشد. اما با این حال تولیدکنندگان خودرو تلاشی برای بهکارگیری آلیاژهای منیزیم در قطعات خودرو انجام ندادهاند. برای استفاده از منیزیم در صنعت خودرو نیاز به استفاده از عناصر کم یاب و گران قیمتی مانند دیسپروزیم، پرازئودیمیم و ایتربیم جهت دستیابی به استحکام مطلوب است.
——————————————————–
ترجمه از گروه ترجمه ایران مواد
حرفه ای ترین تیم ترجمه مهندسی مواد کشور
———————————————————
در دپارتمان (PNNL) یک فرآیند اکستروژن ابداع شده است که پتانسیل رساندن منیزیم به استحکام کافی بدون استفاده از عناصر کمیاب گرانقیمت را داشته و در عین حال خواص ساختاری مواد را نیز بهبود میبخشد.
تحقیقات اولیه نشان داده است که این فرآیند با ایجاد ریزساختاری جدید که با روشهای تجاری اکستروژن ممکن نیست، منجر به افزایش جذب انرژی منیزیم میشود. این فرآیند انعطافپذیری این فلز را نیز بهبود میبخشد. این پیشرفتها، کار با منیزیم را سادهتر ساخته و احتمال استفادهی آن در اجزای خودرو بیشتر خواهد شد.
Scott Whalen محقق و مهندس مکانیک دپارتمان PNNL گفت:
امروزه بسیاری از تولیدکنندگان وسایل نقلیه در قطعات ساختاری، از منیزیم استفاده نمیکنند که دلیل آن قیمت و خواص آن میباشد. در حال حاضر تولیدکنندگان، آلومینیوم را به دلیل قیمت پایین برای به کارگیری در اجزای خودرو انتخاب کردهاند. با استفاده از فرآیند ما، خواص مکانیکی منیزیم بدون استفاده از عناصر کمیاب گرانقیمت، به حدی میرسد که میتوان آن را جایگزین آلومینیوم در اجزای خودرو کرد.
محققین بیان کردهاند که چرخیدن و در هم تندن ورقهای منیزیم در حین این فرآیند اکستروژن جدید، آن قدر ایجاد حرارت میکند که مواد نرم شوند و بنابراین میتوان آن را به راحتی در قالب پرس کرده و یا از آن تیوبها، میلهها و مجاری انتقالی تهیه کرد. حرارت ایجادشده در اثر اصطکاک مکانیکی منجر به تغییر فرم فلز شده و تمام حرارت مورد نیاز برای فرآیند از این طریق فراهم شده و نیازی به المنتهای حرارتی مرسوم در روشهای اکستروژن تجاری نمیباشد.
گروه PNNL این فرآیند را طراحی کرده و در ابعاد صنعتی نیز به کار گرفته است و بر این اساس دستگاهی مخصوص برای این عمل به نام دستگاه Shear Assisted processing and Extrusion(SHAPE) را ساختهاند.
با این دستگاه و فرآیند جدید اکستروژن آنها موفق به ساخت تیوبهای اکسترود شدهی با دیوارهی نازک و قطر ۲ اینچ از آلیاژهای منیزیم – آلومینیوم – روی به نامهای تجاری AZ91 و ZK60A شدند که خواص مکانیکی آنها با استفاه از این فرآیند بهبود چشمگیری پیدا کرد.
Walen در ادامه افزود: “در فرآیند SHAPE ما به ریزساختارهای بسیار ریز و گاهی اوقات ریزساختارهای نانو دست پیدا میکنیم. هرچه سرعت چرخش در این فرآیند افزایش یابد، دانهها ریزدانهتر خواهند شد که منجر به تقویت تیوب و انعطافپذیری بیشتر آن میشود. علاوه براین در این فرآیند ما برای افزایش جذب انرژی منیزیم در حد آلومینیوم، قادر به کنترل جهتگیری ساختارهای بلورین در فلز خواهیم بود.”
ورقهای آلیاژهای بالک منیزیم به لطف اعمال همزمان نیروی چرخشی و خطی توسط دستگاه SHAPE، نرم شده و در میان قالب جریان پیدا میکنند. در این روش، همزمانی اعمال دو نیرو منجر به این میشود که نیروی لازم برای انجام فرآیند اکستروژن در این دستگاه تنها برابر یک دهم نیروی لازم برای اکستروژنهای تجاری باشد. این کاهش نیروی لازم، منجر به کوچکتر شدن دستگاههای تولید و کاهش هزینهها و مخارج تولید در صنعت میگردد.
منبع: www.materialsforengineering.co.uk
مترجم : امیر اشجاری
Shaping the future of magnesium car parts
Magnesium is 75% lighter than steel, 33% lighter than aluminium and is the fourth most common element on earth behind iron, silicon and oxygen. But despite this, manufacturers have been hindered in their attempts to incorporate magnesium alloys into structural car parts. To provide the necessary strength has required the addition of costly rare elements such as dysprosium, praseodymium and ytterbium – until now.
An extrusion process developed at the Department of Energy’s Pacific Northwest National Laboratory (PNNL), has the potential to reduce cost by eliminating the need for rare-earth elements, while simultaneously improving the material’s structural properties.
Initial research found this process improves the energy absorption of magnesium by creating novel microstructures which are not possible with traditional extrusion methods. It also improves ductility –how far the metal can be stretched before it breaks. These enhancements make magnesium easier to work with and more likely to be used in structural car parts.
“Today, many vehicle manufacturers do not use magnesium in structural locations because of the two Ps; price and properties,” said principal investigator and mechanical engineer Scott Whalen. “Right now, manufacturers opt for low-cost aluminium in components such as bumper beams and crush tips. Using our process, we have enhanced the mechanical properties of magnesium to the point where it can now be considered instead of aluminium for these applications – without the added cost of rare-earth elements.”
The researchers theorised that spinning the magnesium alloy during the extrusion process would create just enough heat to soften the material so it could be easily pressed through a die to create tubes, rods and channels. Heat generated from mechanical friction deforming the metal, provides all the heat necessary for the process, eliminating the need for power hungry resistance heaters used in traditional extrusion presses.
The PNNL team designed and commissioned an industrial version of their idea and received a one-of-a-kind, custom built Shear Assisted Processing and Extrusion (ShAPE) machine.
With it, they have extruded thin-walled round tubing, up to two inches in diameter, from magnesium-aluminium-zinc alloys AZ91 and ZK60A, improving their mechanical properties in the process.
“In the ShAPE process, we get highly refined microstructures within the metal and, in some cases, are even able to form nanostructured features,” said Whalen. “The higher the rotations per minute, the smaller the grains become which makes the tubing stronger and more ductile or pliable. Additionally, we can control the orientation of the crystalline structures in the metal to improve the energy absorption of magnesium so it’s equal to that of aluminium.”
The billets of bulk magnesium alloys flow through the die in a soft state, thanks to the simultaneous linear and rotational forces of the ShAPE machine. This means only one tenth of the force is needed to push the material through a die compared to conventional extrusion. This reduction in force would enable smaller production machinery, lowering capital expenditures and operations costs for industry adopting this process.
دانلود فقط با IP ایران امکانپذیر است. در صورت عدم مشاهده باکس قرمز رنگ دانلود، VPN خود را خاموش نموده و صفحه را رفرش کنید.
پسورد فایل فشرده : www.iran-mavad.com
دیدگاه کاربران