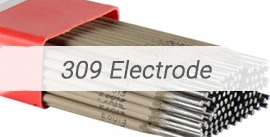
آشنایی کامل با فولاد ابزار گرمکار (سری H)
فولاد ابزار گرمکار چیست؟
این دسته از فولادها به دلیل مقاومت عالی در برابر تغییرات حرارتی و توانایی حفظ سختی و استحکام در دماهای بالا، در کاربردهایی نظیر قالبهای ریختهگری، ابزارهای آهنگری و قالبهای اکستروژن بسیار مورد استفاده قرار میگیرند. ترکیب شیمیایی خاص این فولادها شامل عناصر آلیاژی نظیر کروم، مولیبدن و وانادیم، آنها را برای این دسته از کاربردها بسیار مناسب ساخته است.
فولاد ابزار Tool Steel
بسیاری از اشیائی که در زندگی روزمره با آنها سر و کار داریم از فولادهای ابزار به...ترکیب شیمیایی: عناصر آلیاژی و تأثیر آنها
فولادهای ابزار گرمکار (سریH) شامل عناصر آلیاژی مختلفی است. این عناصر به صورت دقیق انتخاب و تنظیم میشوند تا به فولادهای ابزار گرمکار این امکان را بدهند که در دماهای بالا بدون تغییر شدید در خواص مکانیکی به کار گرفته شوند. طراحی دقیق این آلیاژها از طریق تعادل میان عناصر آلیاژی، عملکرد بهینه در کاربردهای صنعتی مختلف را تضمین میکند.
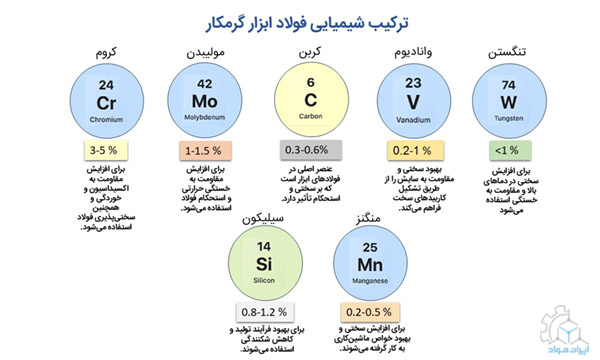
کاربردهای فولاد سری H
فولادهای ابزار گرمکار عمدتاً در ابزارهایی استفاده میشوند که باید در دماهای بالا کار کنند و همزمان تحمل تنشهای مکانیکی شدید را داشته باشند. در ادامه، مهمترین کاربردهای این فولادها همراه با مثالها و مطالعات موردی توضیح داده شده است.
1- قالبهای ریختهگری برای فلزات غیرآهنی (Non-Ferrous Metal Casting Molds)
- کاربرد: تولید قالبهایی برای ریختهگری فلزات مانند آلومینیوم، منیزیم و روی که در دماهای بالا به کار گرفته میشوند.
- ویژگیها: مقاومت به شوک حرارتی و خستگی حرارتی.
- به عنوان نمونه فولاد H13 پرکاربردترین گرید برای قالبهای ریختهگری تحت فشار است. در یک پروژه صنعتی برای تولید قالبهای ریختهگری سیلندر موتور، از فولاد H13 استفاده شد. بررسیها نشان داد که این فولاد به دلیل مقاومت به شوک حرارتی و سایش، توانست طول عمر قالب را تا 40٪ افزایش دهد و هزینههای تولید را کاهش دهد.
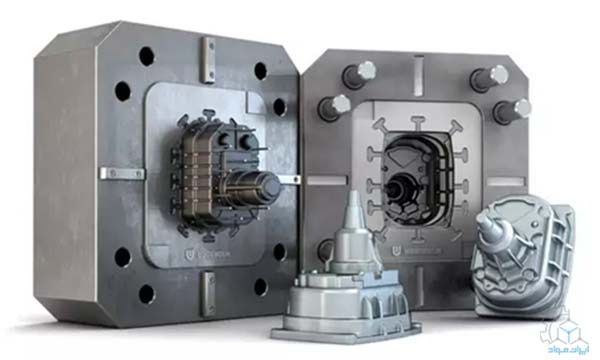
2- ابزارهای فورجینگ (آهنگری)
- کاربرد: ساخت ابزارهایی که برای شکلدهی فلزات در دماهای بالا استفاده میشوند.
- ویژگیها: سختی و استحکام در برابر فشارهای مکانیکی و حرارت بالا.
- به عنوان مثال فولاد H21برای تولید ابزارهای فورجینگ سنگین استفاده میشود. در تولید چرخدندههای صنعتی با استفاده از روش فورجینگ، فولاد H21 به دلیل تحمل دماهای بالا و مقاومت به ترکهای حرارتی توانست در مقایسه با فولادهای معمولی، تا سه برابر بیشتر دوام بیاورد.
3- قالبهای اکستروژن
- کاربرد: تولید پروفیلهای فلزی با فشار بالا، مانند لولهها، میلهها و اشکال پیچیده.
- ویژگیها: مقاومت به سایش و استحکام در برابر فشار.
- فولاد H11 یکی از موارد کاربردی برای قالبهای اکستروژن آلومینیوم و مس استفاده میشود. در یک مطالعه در صنعت اکستروژن، فولاد H11 برای قالبگیری پروفیلهای آلومینیومی استفاده شد. این فولاد با ترکیب مقاومت به حرارت و سایش، عمر قالب را به طور چشمگیری افزایش داد و کیفیت محصول نهایی را بهبود بخشید.
4- صنایع هوافضا
- کاربرد: تولید قطعات مقاوم به حرارت و سایش مانند تیغههای توربین و قطعات موتورها.
- ویژگیها: مقاومت به حرارت بالا و خستگی حرارتی.
- به عنوان نمونه فولاد H42 در تولید قطعات توربینهای گازی برای هواپیماها به کار رفته است و در مطالعات نشان داده شده که این فولاد میتواند تحت دماهای بالا و شوکهای حرارتی شدید مقاومت کند.
5- ابزارهای برش و پانچ
- کاربرد: ابزارهای برش فلزات و پانچ که در دماهای بالا و فشار زیاد کار میکنند.
- ویژگیها: مقاومت به سایش و حفظ سختی در دماهای بالا.
- مثال: در یک پروژه صنعتی، استفاده از فولاد H13 برای ساخت قالبهای پانچ منجر به افزایش دو برابری طول عمر قالبها شد.
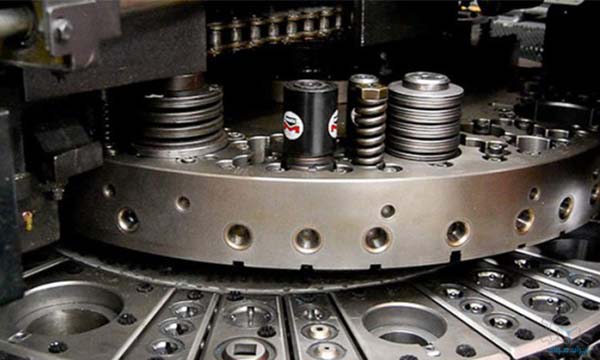
استانداردهای برخی از فولادهای سری H
Grade (AISI) | DIN (1.xxxx) | JIS | UNS | BS | GOST (Russia) | ISO | ASTM |
H11 | 1.2343 | SKD6 | T20811 | BH11 | 4X5MFS | X37CrMoV5-1 | H11 |
H12 | 1.2605 | SKD62 | T20812 | – | – | X35CrMoV5-1 | – |
H13 | 1.2344 | SKD61 | T20813 | BH13 | 4X5MFS | X40CrMoV5-1 | H13 |
H14 | 1.2714 | – | – | – | – | – | – |
H21 | 1.2581 | SKT4 | T20821 | BH21 | 4X5W2FS | X30WCrV9-3 | H21 |
H22 | 1.2587 | – | – | – | – | – | – |
H23 | 1.2885 | – | – | – | – | – | – |
H41 | 1.2716 | – | – | – | – | – | – |
انواع فولاد ابزار گرمکار
فولادهای ابزار گرمکار (سریH) به دستههای مختلفی تقسیم میشوند که هر یک برای کاربردهای خاص طراحی شدهاند. این دستهبندیها بر اساس ترکیب شیمیایی و خواص مکانیکی، تفاوتهای مشخصی دارند. فولادهای ابزار گرمکار در سه گروه اصلی قرار میگیرند:
1- فولادهای ابزار پایه کروم
این گروه از فولادها حاوی مقادیر بالای کروم هستند (حدود 4 تا 5 درصد) و معمولاً شامل عناصر دیگری مانند مولیبدن و وانادیم میشوند، فولاد H11 و H13 از رایجترین نمونههای این گروه هستند. از ویژگیهای اصلی آن میتوان به موارد زیر اشاره کرد:
- مقاومت حرارتی بالا: به دلیل وجود کروم و مولیبدن، این فولادها توانایی حفظ سختی و استحکام خود را در دماهای بالا دارند.
- مقاومت به اکسیداسیون: کروم باعث تشکیل یک لایه اکسید محافظ روی سطح فولاد میشود که مقاومت به خوردگی را افزایش میدهد.
- مقاومت به سایش: کاربیدهای تشکیل شده توسط کروم و وانادیم به این فولادها مقاومت عالی در برابر سایش میبخشند.
- قابلیت عملیات حرارتی: این فولادها قابلیت سختکاری و بازپخت دارند که امکان تنظیم سختی و استحکام برای کاربردهای مختلف را فراهم میکند.
کاربردهای فولادهای ابزار پایه کروم
- قالبهای ریختهگری: برای تولید قطعات فلزی با دمای بالا نظیر قطعات آلومینیوم و منیزیم.
- ابزارهای فورجینگ: مناسب برای شکلدهی مواد در دماهای بالا.
- قالبهای اکستروژن: برای تولید پروفیلهای فلزی با فشار و حرارت بالا.
- ابزارهای صنایع خودروسازی و هوافضا: تولید قطعات مقاوم به حرارت و سایش.
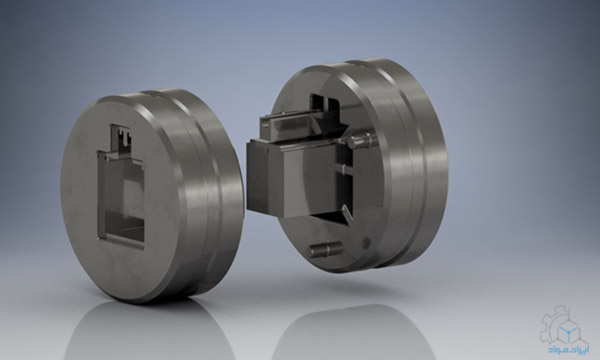
گریدهای رایج فولادهای ابزار پایه کروم
فولادهای ابزار پایه کروم به دلیل خواص مکانیکی و حرارتی برجسته خود، جایگاه ویژهای در صنایع مختلف دارند. این گریدها با ترکیب شیمیایی بهینهشده و قابلیتهای عملیات حرارتی، نیازهای مختلف صنعتی را پوشش میدهند. از میان این گریدها، H13 به دلیل تعادل عالی میان سختی، مقاومت حرارتی و ماشینکاری، پرکاربردترین گزینه در بسیاری از فرآیندهای صنعتی است.
گرید | کربن (C) | کروم (Cr) | مولیبدن (Mo) | وانادیم (V) | سیلیکون (Si) | منگنز (Mn) | ویژگی خاص | کاربردها |
H11 | 0.32-0.45 | 4.75-5.5 | 1.1-1.75 | 0.35 | 0.8-1.2 | 0.2-0.5 | انعطافپذیری بالا | مناسب برای قالبهای ریختهگری و ابزارهای فورجینگ. |
H12 | 0.32-0.45 | 4.75-5.5 | 1.1-1.75 | 0.4 | 0.8-1.2 | 0.2-0.5 | سختی و مقاومت به سایش بیشتر | استفاده در قالبهای اکستروژن و ابزارهای تحت فشار. |
H13 | 0.32-0.45 | 4.75-5.5 | 1.1-1.75 | 0.8-1.2 | 0.8-1.2 | 0.2-0.5 | مقاومت عالی به خستگی حرارتی | رایجترین گرید برای قالبهای ریختهگری و ابزارهای فشار بالا. |
H14 | 0.4 | 5 | 1.25 | 0.3 | 0.8-1.2 | 0.2-0.5 | سختی بالاتر نسبت به H13 | بیشتر در کاربردهای خاص نظیر ریختهگری دقیق استفاده میشوند. |
H19 | 0.35 | 4.8 | 1.2 | 0.4 | 0.8-1.2 | 0.2-0.5 | مناسب برای ریختهگری دقیق | بیشتر در کاربردهای خاص نظیر ریختهگری دقیق استفاده میشوند. |
2- فولادهای ابزار پایه تنگستن
این فولادها حاوی مقادیر بالای تنگستن هستند (بین 9 تا 18 درصد) که سختی فولاد را در دماهای بالا به شدت افزایش میدهد. این فولادها بهویژه در کاربردهایی استفاده میشوند که نیاز به مقاومت به خستگی حرارتی، استحکام در دماهای بالا، و سختی بالا وجود دارد. با این حال، هزینه بالای تولید و چالشهای ماشینکاری ممکن است محدودیتهایی ایجاد کند که با استفاده از تکنولوژیهای پیشرفته قابل بهبود است. نمونههای رایج آن H21 و H26 هستند و ویژگیهای اصلی آن شامل موارد زیر است:
- مقاومت عالی به دماهای بالا: تنگستن (W) به دلیل نقطه ذوب بسیار بالا، باعث میشود این فولادها در دماهای بالا، سختی و استحکام خود را حفظ کنند.
- سختی بالا: وجود تنگستن و سایر عناصر آلیاژی موجب تشکیل کاربیدهای سخت میشود که بهبود قابلتوجهی در مقاومت به سایش ایجاد میکند.
- مقاومت به شوک حرارتی: این فولادها قادر به تحمل تغییرات دمایی سریع بدون ایجاد ترک یا شکست هستند.
- پایداری ابعادی: در دماهای بالا تغییر شکل کمی دارند، که این ویژگی برای قالبها و ابزارهای دقیق ضروری است.
کاربردهای فولادهای ابزار پایه تنگستن
- ابزارهای فورجینگ: مناسب برای شکلدهی فلزات در دماهای بالا با فشارهای سنگین.
- قالبهای اکستروژن: برای تولید قطعات فلزی با دما و فشار بالا، مانند لولهها و پروفیلهای دقیق.
- ابزارهای ریختهگری: برای قالبگیری فلزات سنگین و آلیاژهای سخت که به دماهای بالا نیاز دارند.
- صنایع هوافضا و انرژی: برای تولید قطعات مقاوم به حرارت در موتورهای جت و توربینهای گازی.
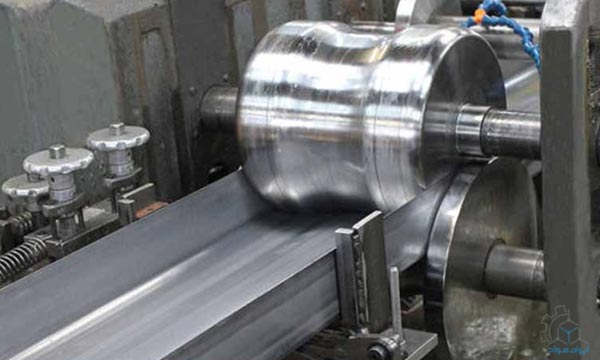
گریدهای رایج فولادهای ابزار پایه تنگستن
گرید | کربن (C) | کروم (Cr) | تنگستن (W) | مولیبدن (Mo) | سیلیکون (Si) | منگنز (Mn) | ویژگی خاص | کاربردها |
H21 | 0.3-0.5 | 8-10 | 2.5-3.75 | 1-1.5 | 0.8-1.2 | 0.2-0.4 | مقاومت به حرارت بالا و شوک حرارتی | ریختهگری و فورجینگ در دماهای بالا. |
H22 | 0.3-0.5 | 8-10 | 2.5-4 | 1-1.5 | 0.8-1.2 | 0.2-0.4 | مقاومت بیشتر به سایش | ابزارهای اکستروژن و قالبگیری تحت فشار. |
H23 | 0.35-0.55 | 8-10 | 3-4 | 1-1.5 | 0.8-1.2 | 0.2-0.4 | سختی بیشتر برای محیطهای خاص | استفاده در محیطهای سختتر با فشار و حرارت بالا. |
H24 | 0.4-0.6 | 7-9 | 5-6 | 1.5-2 | 0.8-1.2 | 0.2-0.5 | مقاومت به شوک حرارتی بالا | قالبهای تخصصی برای ریختهگری فولادهای سنگین. |
H25 | 0.4-0.6 | 7-9 | 6-7 | 1.5-2.5 | 0.8-1.2 | 0.2-0.5 | مقاومت به اکسیداسیون | ابزارهای مورد استفاده در صنایع هوافضا و انرژی. |
H26 | 0.35-0.6 | 10-12 | 9-18 | 1-2 | 0.8-1.2 | 0.2-0.5 | عملکرد عالی در دماهای فوقالعاده بالا | ابزارهای پیشرفته برای کاربردهای خاص مانند ریختهگری فلزات سنگین. |
3- فولادهای ابزار پایه مولیبدن
فولادهای ابزار پایه مولیبدن یکی از زیرگروههای مهم فولادهای ابزار گرمکار هستند که به دلیل ترکیب خاص خود، توانایی مقاومت در برابر حرارت و فشار بالا را دارند. این فولادها عمدتاً به دلیل وجود عنصر مولیبدن (Mo) شناخته میشوند که نقش کلیدی در افزایش استحکام، مقاومت به خستگی حرارتی و بهبود خواص مکانیکی ایفا میکند. این گریدها به ویژه در صنایعی که نیاز به عملکرد در دماهای بسیار بالا و تحت تنشهای سنگین دارند، جایگاه ویژهای دارند. طراحی این فولادها برای ارائه خواص بهینه در کاربردهای خاص صنعتی، نشاندهنده اهمیت آنها در متالورژی مدرن است.
ویژگیهای اصلی فولادهای ابزار پایه مولیبدن
- مقاومت به خستگی حرارتی: مولیبدن باعث افزایش پایداری فولاد در برابر تغییرات مکرر دما میشود و خستگی حرارتی را کاهش میدهد.
- مقاومت به سایش: این فولادها به دلیل تشکیل کاربیدهای مقاوم، مقاومت به سایش بسیار خوبی دارند.
- سختی در دمای بالا: مولیبدن سختی فولاد را در دماهای بالا حفظ کرده و از تغییر شکل در حین عملیات جلوگیری میکند.
- قابلیت ماشینکاری مناسب: این فولادها قابلیت خوبی برای عملیات ماشینکاری و عملیات حرارتی دارند.
کاربردهای فولادهای ابزار پایه مولیبدن
- قالبهای ریختهگری: مناسب برای تولید قطعات بزرگ فلزی در دماهای بالا.
- ابزارهای فورجینگ: برای شکلدهی مواد در دماهای بالا با فشار بالا.
- قالبهای اکستروژن: تولید پروفیلهای فلزی دقیق در شرایط کاری سخت.
- صنایع هوافضا و انرژی: تولید قطعات مقاوم به حرارت و شوکهای حرارتی در موتورهای توربینی.
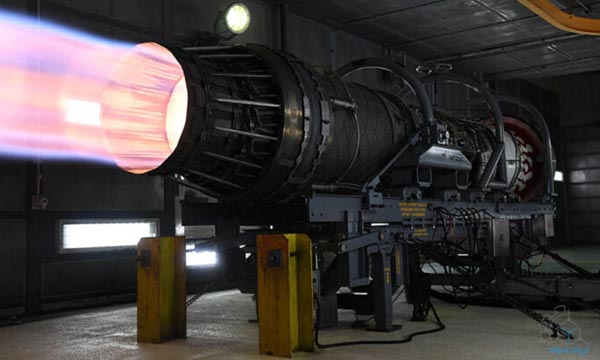
گریدهای رایج فولادهای ابزار پایه مولیبدن
گرید | مولیبدن (Mo) | کروم (Cr) | کربن (C) | وانادیم (V) | سیلیکون (Si) | منگنز (Mn) | ویژگی خاص | کاربردها |
H41 | 5.0-6.5 | 3.0-4.0 | 0.4-0.6 | 0.25-0.5 | 0.8-1.2 | 0.2-0.4 | مقاومت به حرارت و شوک حرارتی بالا | قالبهای دقیق ریختهگری و ابزارهای فورجینگ. |
H42 | 8.0-10.0 | 1.0-2.0 | 0.4-0.5 | 0.3-0.5 | 0.8-1.2 | 0.2-0.4 | مناسب برای ابزارهای قالبگیری سنگین | ابزارهای قالبگیری سنگین و تولید قطعات فلزی بزرگ. |
H43 | 6.0-8.0 | 2.0-3.0 | 0.35-0.45 | 0.4-0.6 | 0.8-1.2 | 0.2-0.5 | مقاومت به شوک حرارتی و سایش | ابزارهای اکستروژن و فورجینگ. |
H46 | 10.0-12.0 | 2.0-3.0 | 0.4-0.6 | 0.5-0.8 | 0.8-1.2 | 0.2-0.5 | مناسب برای دماهای فوقالعاده بالا | ابزارهای تخصصی برای صنایع هوافضا و انرژی. |
ریزساختار و خواص فولاد ابزار گرمکار
ریزساختار فولادهای ابزار گرمکار شامل ترکیب دقیق فازهای مختلف و کاربیدهای سخت است که مقاومت حرارتی، سختی بالا و مقاومت به سایش را تضمین میکند. این خواص به ترکیب شیمیایی فولاد، فرآیندهای تولید، عملیات حرارتی و شرایط کاری وابستهاند.
1- مقاومت حرارتی: مقاومت فولاد در برابر دماهای بالا به وجود فازهای پایدار مانند کاربیدهای کروم و مولیبدن بستگی دارد. این ترکیبات با کاهش تغییرات ساختاری و افزایش پایداری در دماهای بالا، مقاومت فولاد را در برابر شوک حرارتی و خستگی حرارتی بهبود میبخشند. برای افزایش این ویژگی، بهینهسازی مقدار مولیبدن و کروم و حذف ناخالصیها ضروری است.
2- سختی و مقاومت به سایش: سختی و مقاومت به سایش فولادهای ابزار گرمکار عمدتاً به توزیع یکنواخت کاربیدها و ریزدانههای مارتنزیت بستگی دارد. عناصر آلیاژی مانند کروم، مولیبدن و وانادیم با تشکیل کاربیدهای سخت، نقش کلیدی در این خصوصیات ایفا میکنند. عملیات حرارتی مناسب (مانند کوئنچ و بازپخت) و کاهش اندازه دانهها بهطور قابلتوجهی سختی و مقاومت فولاد در برابر سایش را افزایش میدهد.
3- توزیع و اندازه کاربیدها: ریزساختار ایدهآل فولاد شامل توزیع یکنواخت کاربیدهای مقاوم در برابر سایش و حرارت است. کاربیدهای وانادیم (VC) و مولیبدن (Mo₂C) در کنار فازهای مارتنزیتی، استحکام و چقرمگی فولاد را در شرایط کاری سخت تضمین میکنند.
4- بهبود مقاومت به سایش و حرارت: بهینهسازی ترکیب شیمیایی، عملیات حرارتی چندمرحلهای و استفاده از پوششهای سطحی مانند نیتروژندهی یا کربندهی از جمله راهکارهای مؤثر برای بهبود خواص مکانیکی و حرارتی فولادهای ابزار گرمکار است.
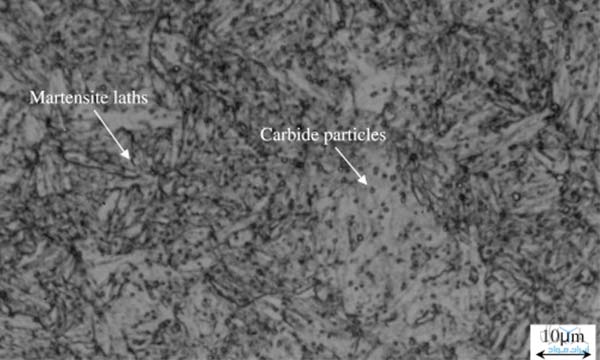
خواص مکانیکی فولاد ابزار گرمکار
فولادهای ابزار کاری گرم دارای خواص مکانیکی برجستهای هستند که بسته به گرید و ترکیب شیمیایی آنها متفاوت است. از نظر سختی (HRC)، این فولادها در محدوده 45 تا 62 قرار دارند. گریدهایی مانند H24، H25 و H26 بالاترین سختی را ارائه میدهند و برای شرایط کاری با سایش شدید مناسب هستند. استحکام کششی نیز در محدوده 1200 تا 1800 مگاپاسکال قرار دارد، بهطوری که گریدهای H21، H23 و H25 بیشترین استحکام کششی را نشان میدهند و برای تحمل بارهای مکانیکی بالا در دماهای بالا ایدهآل هستند.
از نظر چقرمگی، گریدهایی مانند H11، H41 و H42 چقرمگی بالایی دارند و برای کاربردهایی که شوکهای مکانیکی و حرارتی وجود دارد، مناسب هستند. در مقابل، گریدهایی مانند H24، H25 و H26 چقرمگی پایینتری دارند، اما این ویژگی با مقاومت به سایش بالا جبران میشود. مقاومت به سایش در گریدهای H23، H24، H25 و H26 بسیار برجسته است و این گریدها برای شرایط کاری با اصطکاک و فشار زیاد مناسب هستند.
چقرمگی چیست؟ (کاربرد، انواع، روشهای اندازهگیری)
بیایید برای لحظاتی حادثۀ کشتی تایتانیک را با هم مرور کنیم. ماجرای کلی این است که...از نظر پایداری دمایی، این فولادها در محدوده 600 تا 700 درجه سانتیگراد عملکرد مطلوبی دارند. گریدهایی مانند H21، H23 و H26 بهترین عملکرد را در دماهای بالا ارائه میدهند، در حالی که گریدهای H11 و H19 با پایداری تا 600 درجه سانتیگراد، برای شرایط حرارتی کمتر مناسبتر هستند. این تنوع در خواص، فولادهای ابزار کاری گرم را برای طیف گستردهای از کاربردهای صنعتی مناسب ساخته است.
خواص فیزیکی فولاد ابزار گرمکار
فولادهای ابزار گرمکار دارای خواص فیزیکی متنوعی هستند که عملکرد آنها در دماهای بالا و شرایط کاری سخت را تعیین میکنند. چگالی این فولادها بسته به ترکیب شیمیایی و پایه آلیاژی متفاوت است. فولادهای پایه کروم چگالی کمتری (~7.80 g/cm³) نسبت به پایه مولیبدن (~8.20 g/cm³) و پایه تنگستن (~8.30 g/cm³) دارند. این ویژگی باعث میشود فولادهای پایه تنگستن، به دلیل چگالی بالاتر، مقاومت بهتری در برابر حرارت داشته باشند و برای کاربردهایی در دماهای بسیار بالا مناسبتر باشند.
ضریب انبساط حرارتی در فولادهای پایه تنگستن کمترین مقدار (~10.1-10.5 µm/m·°C) را دارد که باعث میشود در دماهای بالا پایداری بیشتری داشته باشند. در مقابل، فولادهای پایه کروم با ضریب انبساط حرارتی بالاتر (~12 µm/m·°C)، مناسب برای کاربردهایی هستند که به تعادل در تغییرات حرارتی نیاز دارند. فولادهای مولیبدن با ضریب انبساط حرارتی میانه (~10.6-11.0 µm/m·°C)، تعادل مناسبی میان این دو گروه ایجاد میکنند.
از نظر هدایت حرارتی، فولادهای پایه کروم با مقادیر بالاتر (~24-28 W/m·K)، انتقال حرارت بهتری دارند که آنها را برای کاربردهایی نظیر ریختهگری و قالبهای حرارتی ایدهآل میکند. در مقابل، فولادهای پایه تنگستن با هدایت حرارتی پایینتر (~16-21 W/m·K)، حرارت را حفظ کرده و برای ابزارهایی که نیاز به کاهش اتلاف حرارتی دارند مناسب هستند. فولادهای پایه مولیبدن با هدایت حرارتی متوسط (~21-24 W/m·K)، کاربردهای متعادلتری را ارائه میدهند.
ظرفیت حرارتی ویژه نیز بسته به پایه آلیاژی متفاوت است. فولادهای پایه کروم با ظرفیت حرارتی بالا (~450-460 J/kg·K)، پایداری بیشتری در تغییرات دمایی نشان میدهند. فولادهای پایه تنگستن با ظرفیت حرارتی کمتر (~412-430 J/kg·K)، برای شرایط کاری با دماهای پایدار و بالا مناسبتر هستند. فولادهای پایه مولیبدن نیز با ظرفیت حرارتی میانه (~425-440 J/kg·K) برای کاربردهای متنوعی استفاده میشوند.
به طور کلی، فولادهای پایه کروم برای انتقال حرارت و تغییرات دمایی مکرر مناسب هستند، در حالی که فولادهای پایه تنگستن و مولیبدن به دلیل پایداری در دماهای بالا، گزینهای ایدهآل برای شرایط صنعتی سخت و دماهای بسیار بالا محسوب میشوند. انتخاب این خواص فیزیکی باید همراه با خواص مکانیکی در نظر گرفته شود تا بهترین عملکرد در هر کاربرد صنعتی تضمین گردد.
روشهای تولید: ریختهگری، آهنگری و ماشینکاری
فولادهای ابزار گرمکار با استفاده از فرآیندهای مختلف تولید مانند ریختهگری، آهنگری و ماشینکاری تولید میشوند. هر یک از این روشها به طور خاص برای بهینهسازی خواص مکانیکی و ساختاری فولادها طراحی شدهاند و بر اساس کاربرد نهایی، از یکی یا ترکیبی از این فرآیندها استفاده میشود.
1- ریختهگری (Casting): ریختهگری اولین مرحله تولید این فولادها است که در آن، مواد اولیه مانند آهن، کروم، مولیبدن و سایر عناصر آلیاژی در کوره ذوب شده و سپس در قالبهای مخصوص ریخته میشوند. این روش برای تولید شمشهای فولادی بزرگ یا قطعاتی که شکل پیچیدهای دارند استفاده میشود. در فولادهای ابزار گرمکار، کنترل دقیق ترکیب شیمیایی در این مرحله اهمیت زیادی دارد، زیرا ریزساختار نهایی و عملکرد فولاد در دماهای بالا به این ترکیب وابسته است. عیب اصلی ریختهگری، احتمال وجود ناخالصیها و ریزترکها است که ممکن است بر خواص نهایی اثر منفی بگذارد.
2- آهنگری (Forging): آهنگری یکی از فرآیندهای اساسی برای بهبود ریزساختار و خواص مکانیکی فولاد است. در این فرآیند، فولاد در دماهای بالا گرم شده و تحت فشارهای شدید به شکلهای دلخواه تبدیل میشود. این روش با افزایش تراکم مواد، استحکام مکانیکی را بهبود میبخشد و باعث کاهش تخلخل و حذف عیوب ساختاری میشود. آهنگری معمولاً برای تولید ابزارهایی که تحت تنشهای شدید و شرایط کاری سخت قرار دارند (مانند قالبهای فورجینگ یا اکستروژن) استفاده میشود.
3- ماشینکاری (Machining): ماشینکاری فرآیند نهایی در تولید قطعات فولادی است که به وسیله ابزارهای برش، قطعات به شکل و اندازه نهایی خود میرسند. این مرحله شامل تراشکاری، فرزکاری و سوراخکاری است و برای ایجاد تلرانسهای دقیق و سطوح صاف استفاده میشود. فولادهای ابزار گرمکار به دلیل سختی بالا ممکن است چالشهای ماشینکاری داشته باشند، اما با استفاده از ابزارهای پیشرفته مانند ابزارهای پوششدهی شده با کاربید یا سرامیک، این مشکلات کاهش مییابد. در نهایت، عملیات حرارتی پس از ماشینکاری انجام میشود تا سختی و استحکام سطحی قطعات افزایش یابد.
این سه فرآیند در کنار هم، خواص مکانیکی، حرارتی و مقاومت به سایش مورد نیاز فولادهای ابزار گرمکار را تضمین میکنند و قطعاتی با دقت بالا و عملکرد بهینه را تولید میکنند.
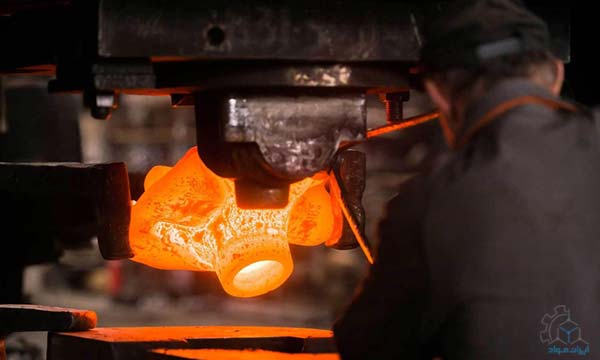
نکته ای مهم در تولید: ناخالصیهای اکسیژن و نیتروژن
ناخالصیهای اکسیژن و نیتروژن از جمله عواملی هستند که میتوانند بر خواص نهایی فولادهای ابزار گرمکار تأثیر منفی داشته باشند. این عناصر معمولاً در مراحل مختلف تولید، بهویژه در فرآیند ذوب یا ریختهگری، وارد ساختار فولاد میشوند و منجر به تشکیل ترکیباتی مانند اکسیدها و نیتریدها میگردند. وجود این ترکیبات میتواند چقرمگی فولاد را کاهش داده و نقاط تمرکز تنش ایجاد کند که احتمال ترکخوردگی و کاهش مقاومت به خستگی حرارتی را افزایش میدهد. علاوه بر این، ناخالصیهای مذکور با تأثیر بر ریزساختار فولاد، موجب رشد دانهها و کاهش مقاومت به سایش و سختی فولاد میشوند. این عوامل نهتنها بر عملکرد فولاد در شرایط کاری سخت تأثیر میگذارند، بلکه ممکن است کیفیت سطحی قطعات تولیدشده را نیز کاهش دهند. برای کاهش اثرات نامطلوب این ناخالصیها، استفاده از فرآیندهای پالایش مانند گاززدایی در خلأ و کنترل دقیق ترکیب شیمیایی مواد اولیه ضروری است. همچنین، افزودن عناصری مانند آلومینیوم و تیتانیوم که ترکیبات پایداری با اکسیژن و نیتروژن تشکیل میدهند، میتواند به بهبود کیفیت فولاد کمک کند.
اهمیت عملیات حرارتی در بهبود عملکرد فولاد ابزار گرمکار
عملیات حرارتی یکی از مراحل حیاتی در بهبود خواص مکانیکی و ساختاری فولادهای ابزار گرمکار است که به طور مستقیم بر عملکرد و طول عمر این فولادها تأثیر میگذارد. این فرآیند شامل روشهایی مانند کوئنچ، بازپخت و آنیلینگ است که با تغییر ساختار بلوری فولاد، ویژگیهایی همچون سختی، چقرمگی و مقاومت به سایش را بهینه میکند.
1- کوئنچ (Quenching): در این مرحله، فولاد ابتدا تا دمای بحرانی (حدود 800 تا 1000 درجه سانتیگراد) گرم شده و سپس به سرعت در محیطهایی مانند روغن یا آب سرد میشود. این فرآیند باعث تشکیل ساختار مارتنزیت میشود که سختترین فاز فولاد است و باعث افزایش سختی و مقاومت به سایش، بهبود قابلیت عملکرد در دماهای بالا، و ایجاد ساختاری یکنواخت که برای مقاومت به سایش حیاتی است، میشود.
برای درک بهتر این موضوع، نمودار (Continuous Cooling Transformation)CCT که اثر نرخ خنکسازی بر روی تحولات فازی فولاد را مشخص میکند، در زیر آورده شده است:
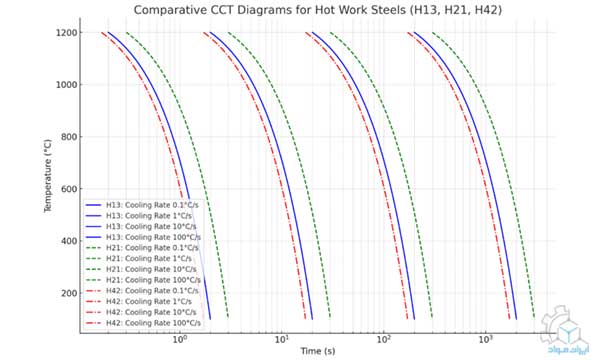
در نمودار بالا:
- H13 (پایه کروم): خنکسازی سریع مارتنزیت سخت ایجاد میکند، در حالی که خنکسازی آهستهتر فازهای نرمتری مثل پرلیت ایجاد میکند. این فولاد برای سختی بالا مناسب است.
- H21 (پایه تنگستن): تحولها در دماهای بالاتر رخ میدهند و نرخ خنکسازی تأثیر کمتری دارد. این فولاد مقاومت حرارتی بالایی دارد و برای دماهای زیاد ایدهآل است.
- H42 (پایه مولیبدن): در خنکسازی سریع مارتنزیت سخت تشکیل میشود، اما در نرخهای آهستهتر بینیت ایجاد میشود که چقرمگی بیشتری فراهم میکند.
2- بازپخت (Tempering): پس از کوئنچ، فولاد ممکن است شکننده باشد. بازپخت در دماهای کنترلشده (200 تا 600 درجه سانتیگراد) انجام میشود تا تنشهای داخلی ناشی از کوئنچ کاهش یابد و تعادل بین سختی و چقرمگی ایجاد شود. از اثرات این کار کاهش احتمال ترکخوردگی، بهبود چقرمگی برای مقابله با ضربات و شوکهای مکانیکی و بهینهسازی مقاومت به خستگی حرارتی در دماهای بالا است.
نمودار (Time-Temperature-Transformation)TTT تحول ایزوترمال فولاد را نشان میدهد.
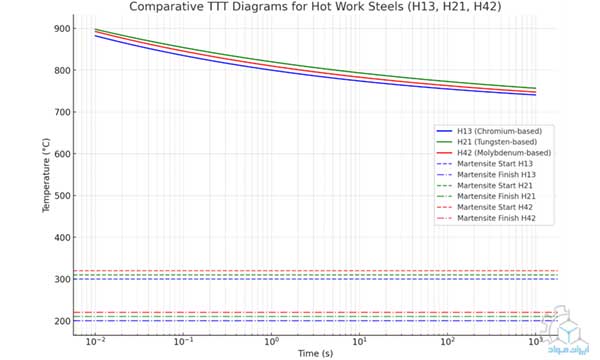
در نمودار بالا:
- H13 (پایه کروم): تحول فازها سریعتر از دو فولاد دیگر رخ میدهد و مارتنزیت از 300°C شروع میشود. این فولاد سختی و مقاومت به سایش بالایی دارد، اما چقرمگی پایینتر است.
- H21 (پایه تنگستن): تحول فازها کندتر است و مارتنزیت از 310°C شروع میشود. تنگستن با تشکیل کاربیدهای پایدار، این فولاد را برای مقاومت در برابر حرارت عالی میکند.
- H42 (پایه مولیبدن): تحول فازها بین H13 و H21 قرار دارد و مارتنزیت از 320°C شروع میشود. مولیبدن باعث تعادل مناسب بین سختی و چقرمگی میشود.
3- آنیلینگ (Annealing): آنیلینگ با حرارتدهی آهسته فولاد تا دماهای زیر بحرانی و خنکسازی کنترلشده، ساختار یکنواخت و دانههای ریزتری ایجاد میکند و باعث افزایش قابلیت ماشینکاری، کاهش تنشهای داخلی برای بهبود ثبات ابعادی، و آمادهسازی برای عملیات حرارتی بعدی میشود.
انتخاب بهترین فولاد ابزار برحسب شرایط و کاربرد
نوع فولاد ابزار گرمکار | مزایا | معایب |
فولاد ابزار گرمکار پایه کروم | قیمت مناسب، مقاومت خوب به حرارت و شوک حرارتی. | مقاومت به سایش کمتر از پایه تنگستن و مولیبدن |
فولاد ابزار گرمکار پایه تنگستن | مقاومت فوقالعاده به سایش و حرارت بالا. | هزینه تولید بالا و ماشینکاری دشوار |
فولاد ابزار گرمکار پایه مولیبدن | مقاومت عالی به حرارت و شوک حرارتی، پایداری ابعادی بالا. | هزینه بالاتر نسبت به پایه کروم و ماشینکاری سختتر. شکنندگی نسبی در برخی شرایط |
این تحلیل نشان میدهد که انتخاب بهترین گروه فولادی به نیازهای خاص هر کاربرد بستگی دارد. فولادهای پایه مولیبدن برای شرایط با حرارت بالا و شوک حرارتی مناسب هستند. فولادهای پایه کروم گزینهای اقتصادی و کارآمد برای کاربردهای عمومیتر هستند. فولادهای پایه تنگستن در شرایطی که مقاومت به سایش و دماهای بسیار بالا حیاتی است، بهترین انتخاب محسوب میشوند. این مقایسه به درک بهتر و انتخاب آگاهانهتر مواد کمک میکند.
چالشها و نوآوریها در فولاد ابزار گرمکار
فولادهای ابزار گرمکار با وجود خواص مکانیکی و حرارتی برجسته، در شرایط عملیاتی سخت با چالشهایی مواجه هستند که بر عملکرد و طول عمر آنها تأثیر میگذارد. این چالشها شامل خستگی حرارتی، ترکخوردگی و سایش هستند. به همین دلیل، تحقیقات و نوآوریهای متالورژیکی به طور مستمر برای بهبود این مواد انجام میشود. در ادامه، این چالشها و پیشرفتها بررسی شدهاند.
1- مشکل خستگی حرارتی و ترکخوردگی: خستگی حرارتی یکی از چالشهای اصلی فولادهای ابزار گرمکار است که به دلیل تغییرات مکرر دما و ایجاد تنشهای حرارتی رخ میدهد و میتواند به تشکیل ترکهای میکروسکوپی و گسترش آنها منجر شود. این ترکها باعث کاهش خواص مکانیکی فولاد و عمر مفید ابزارها میشوند. همچنین، ترکخوردگی در دماهای بالا ناشی از اکسیداسیون سطحی و تنشهای داخلی در فولاد است که در گریدهایی با آلیاژ کمتر مانند مولیبدن و کروم تشدید میشود. برای رفع این مشکلات، تحقیقات متالورژیکی پیشنهادهایی ارائه دادهاند، از جمله افزایش درصد عناصر آلیاژی مانند کروم، مولیبدن و وانادیم که با تشکیل کاربیدهای سخت، مقاومت به خستگی حرارتی را افزایش میدهند. همچنین، بهینهسازی ریزساختار فولاد از طریق توزیع و اندازه مناسب کاربیدها، چقرمگی را بهبود میبخشد و حساسیت به ترکخوردگی را کاهش میدهد. علاوه بر این، فناوریهای پوششدهی سطحی مانند نیتروژندهی و پوششهای سرامیکی نیز میتوانند مقاومت فولاد در برابر اکسیداسیون و سایش را بهطور قابل توجهی افزایش دهند.
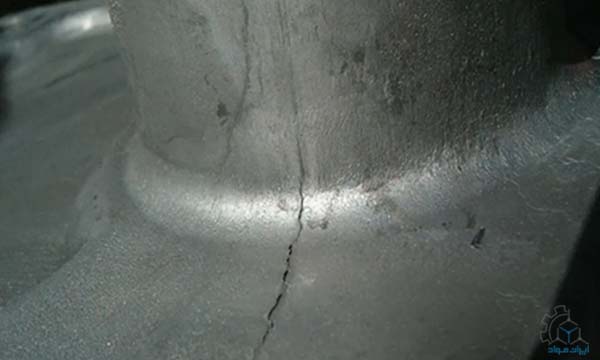
2- سایش و کاهش طول عمر ابزارها: سایش یکی از چالشهای مهم فولادهای ابزار گرمکار است که به دلیل تماس مداوم ابزار با مواد فلزی داغ رخ میدهد و بهویژه در قالبهای ریختهگری و ابزارهای فورجینگ مشاهده میشود. این مشکل منجر به کاهش دقت ابعادی ابزارها و کاهش عمر مفید آنها میگردد. برای مقابله با این چالش، راهکارهای جدیدی ارائه شده است که شامل افزودن عناصری مانند وانادیم و تنگستن میشود. این عناصر با تشکیل کاربیدهای سخت، مقاومت فولاد در برابر سایش را بهطور چشمگیری افزایش میدهند. علاوه بر این، توسعه عملیات حرارتی پیشرفته مانند ترکیب کوئنچ و بازپخت چندمرحلهای میتواند سختی سطحی فولاد را بهبود بخشیده و مقاومت آن در برابر سایش را افزایش دهد. این راهکارها بهطور مؤثری به افزایش طول عمر و عملکرد ابزارهای فولادی کمک میکنند.
3- روندها و تحقیقات آینده: روندها و تحقیقات آینده در زمینه فولادهای ابزار گرمکار بر بهبود عملکرد این مواد در شرایط سخت متمرکز است. یکی از این روندها استفاده از نانوذرات است که با ترکیب در ساختار فولاد، میتواند استحکام و مقاومت به حرارت آن را افزایش دهد. همچنین، طراحی آلیاژهای جدید با مقادیر بهینه عناصری مانند کبالت و نیکل، به منظور افزایش مقاومت به خستگی حرارتی، از دیگر محورهای مهم تحقیقات است. علاوه بر این، بهرهگیری از نرمافزارهای پیشرفته شبیهسازی برای پیشبینی رفتار فولادها در شرایط کاری مختلف و بهینهسازی ترکیب شیمیایی، به دانشمندان کمک میکند تا کارایی این فولادها را در کاربردهای صنعتی به حداکثر برسانند. این تحقیقات در نهایت میتواند منجر به تولید فولادهایی با عملکرد بهینهتر و عمر مفید بالاتر شود.
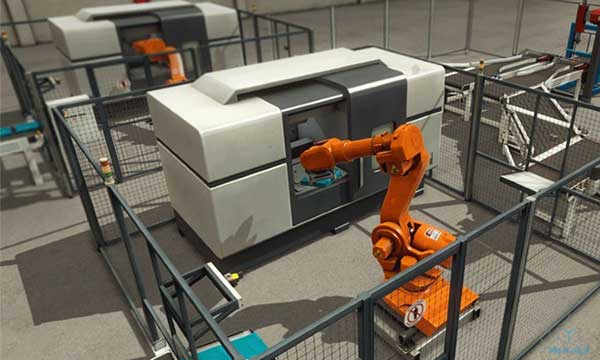
4- توسعه فناوریهای پایدار و بازیافت: با توجه به نیاز روزافزون به کاهش هزینهها و اثرات زیستمحیطی، تحقیقات به سمت فناوریهای پایدار و بازیافت فولادهای ابزار گرمکار حرکت میکنند. فرآیندهای جدیدی مانند متالورژی پودر و تولید افزایشی (Additive Manufacturing) در حال توسعه هستند که در متالورژی پودر، مواد اولیه بهصورت پودر فلزی تهیه میشوند، سپس تحت فشار و حرارت در یک قالب فشرده و متراکم میشوند تا قطعهای با ریزساختار یکنواخت و خواص مکانیکی بهینه تولید شود. در تولید افزایشی (Additive Manufacturing)، مواد بهصورت لایهلایه بر اساس طراحی دیجیتالی روی هم قرار میگیرند تا قطعات با هندسههای پیچیده ساخته شوند. این روشها بیشتر برای کاربردهایی که کیفیت و طراحی خاص اولویت دارند، مانند صنایع هوافضا و ابزارهای دقیق، استفاده میشوند و میتوانند ضایعات را کاهش داده و خواص فولاد را بهبود بخشند.
نتیجهگیری
فولادهای ابزار گرمکار به دلیل ترکیب بینظیر خواص مکانیکی، حرارتی، و مقاومت به سایش، جایگاه ویژهای در صنایع مختلف مانند ریختهگری، فورجینگ، و اکستروژن دارند. این فولادها با توانایی حفظ عملکرد در دماهای بالا، تحمل تنشهای مکانیکی شدید و مقاومت در برابر خستگی حرارتی، به گزینهای ایدهآل برای ابزارهای صنعتی تبدیل شدهاند.
با وجود چالشهایی مانند ترکخوردگی، خستگی حرارتی و سایش، استفاده از تکنیکهای پیشرفته متالورژیکی نظیر افزودن عناصر آلیاژی، بهینهسازی عملیات حرارتی و بهرهگیری از فناوریهای پوششدهی سطحی، بهطور مؤثری دوام و طول عمر این فولادها را افزایش داده است.
نگاه به آینده نشان میدهد که نوآوریهای مستمر در طراحی آلیاژهای جدید، استفاده از فناوریهای نوین تولید مانند متالورژی پودر و تولید افزایشی، و حرکت به سمت بازیافت و توسعه پایدار، نقش مهمی در پیشرفت این حوزه ایفا خواهند کرد. این اقدامات، نهتنها عملکرد فولادهای ابزار گرمکار را بهینه میکند، بلکه هزینههای تولید و اثرات زیستمحیطی را نیز کاهش میدهد.
در نهایت، فولادهای ابزار گرمکار همچنان یکی از ارکان اصلی پیشرفت صنایع مدرن به شمار میروند و بهرهگیری از دانش و فناوریهای پیشرفته، میتواند تحولی بنیادین در عملکرد و کارایی این مواد ایجاد کند.
دیدگاه کاربران