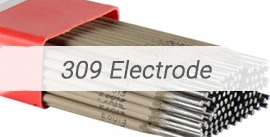
برش پلاسما (plasma cutting)
برش پلاسما (plasma cutting) یک فرآیند ساخت فلز است که با استفاده از گازهای یونیزهشده که تا دمای 20000 درجه سانتیگراد حرارت داده شدهاند، برای ذوب کردن مواد فلزی به کار گرفته میشوند. با خروج این گاز تحت فشار بالا علاوهبر اینکه منجر به ذوب مادهی فلزی میشود، مواد باقیمانده را نیز از مسیر برش دور میکند. این فرآیند تنها بر روی مواد رسانای الکتریکی مانند فولاد زنگنزن، مس، آلومینیم و سایر مواد فلزی قابل انجام است. بهعبارتیدیگر این فرآیند قادر به برش موادی مانند سنگ، شیشه و یا موادی که خاصیت رسانایی الکتریستهی ضعیفی دارند، نیست.
برش پلاسما بهعنوان روشی برای ساخت فلز (برش) مزایای متعددی نسبت به سایر روشها دارد. این مزایا شامل مقرونبهصرفه بودن، طیف گستردهی کاربرد آن بر روی فلزات، دقت بالا و تکرارپذیری است.
برش پلاسما چگونه کار میکند؟
چه نوع گازی برای استفاده در طول این فرآیند ایدهآل است؟
بر روی چه موادی کار میکند؟
چه مزایا و معایبی دارد؟
اینها عمده سوالاتی است که میخواهیم در ادامه بهطور مفصل به آنها پاسخ دهیم. پس برای اینکه این روش برایتان کاملا روشن شود تا پایان مقاله با ما همراه باشید.
فهرست مطالب
- تاریخچهی برش پلاسما
- برش پلاسما چگونه کار میکند؟
- انواع فرآیند برش پلاسما
- گاز دوگانه (Dual gas)
- تزریق آب (Water injection)
- پلاسما زیر آب (Water shroud)
- پلاسمای هوا (Air plasma)
- پلاسما با توان بالا (High tolerance plasma)
- گازهای مورداستفاده در برش پلاسما
- مواد قابلبرش در فرآیند برش پلاسما
- مزایای برش پلاسما
- معایب برش پلاسما
- جمعبندی
- منابع
تاریخچه
فرآیند برش پلاسما به سال 1957 برمیگردد. در ابتدا این فرآیند بهعنوان فرآیند جوشکاری قوس تنگستن (Gas Tungsten Arc Welding) مورداستفاده قرار گرفت. برش مواد فولادی و آلومینیمی با ضخامتهای نیم تا شش اینچ ازجمله کاربرد اصلی برش پلاسما در آن دوران بود. با این حال، الکترودها و نازلهای مورداستفاده بهدلیل گرمای ناشی از فرآیند، بهسرعت دچار شکست میشدند که تعویض آنها سبب افزایش هزینه در آن دوران میشد.
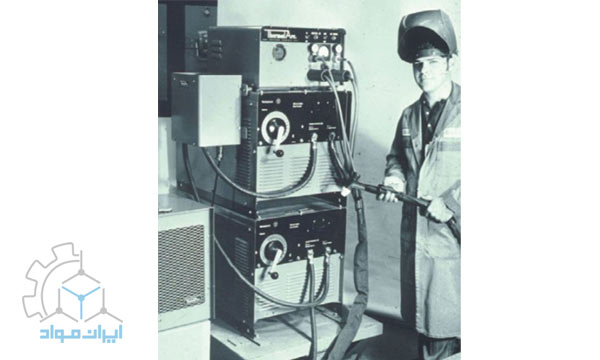
این فرآیند را با توجه به تاریخچهای که دارد، میتوان به چند برههی تاثیرگذار تقسیمبندی نمود:
- اواخر 1960: در این سالها ساخت مشعل با جریان دوگانه صورت گرفت که کمککننده در بهبود طول عمر الکترود، نازلها و همینطور افزایش در کیفیت و دقت برش بوده است.
- 1980: این دهه بهعنوان دورهی تجربهی علمی مهندسان شناخته میشود. شاید بتوان این مورد را بهدلیل طراحی برشدهندههای پلاسمایی پایه اکسیژن، ارتقا کنترل برش در سطوح مختلف و ارگونومیکتر کردن قابلیت حمل واحد برش پلاسما دانست.
- 1990 تا به امروز: در این برهه از برشدهندههای پایدار پایه اکسیژن همراه با سیستم نازل جدید استفاده شد. این عوامل منجر به ارتقا چهار برابری شدت انرژی نسبت به دورههای گذشته گردید.
از سال 1990 تا به امروز، توجه عمدهی مهندسان بر روی بهبود کارایی بوده است. آنها همچنین دقت برشدهندههای پلاسما را بهبود بخشیدند که امروزه در مدلهایی چون لبههای تیزتر با برش دقیقتر عرضه میشوند. قابلیت حمل و اتوماتیکسازی از دیگر جنبههای مهندسی برش پلاسما است که بهطور قابل توجهی بهبود یافتهاند.
حالا که در مورد تکامل برش پلاسما در طول سالهای مختلف اطلاعات کسب کردیم، در گام بعدی بهسراغ نحوهی عملکرد دستگاه پلاسما میرویم.
برش پلاسما چگونه کار می کند؟
در این فرآیند ذوبکردن فلز با استفاده از حرارت جایگزین برش، مکانیکی شده است. برشدهندههای پلاسما با ایجاد قوس الکتریکی از طریق گاز کار میکنند. این گاز از یک باریکهی محدود که به آن «نازل» میگویند به بیرون دمیده میشود. باریکهی محدود منجر به همگرا شدن گاز با سرعت خروج بالا شده که در نتیجهی آن پلاسما تشکیل میشود. از آنجاییکه پلاسما خاصیت رسانایی دارد لذا توجه به این نکته حائز اهمیت است که بههنگام برش قطعه کار از طریق میز برش به زمین اتصال داشته باشد.
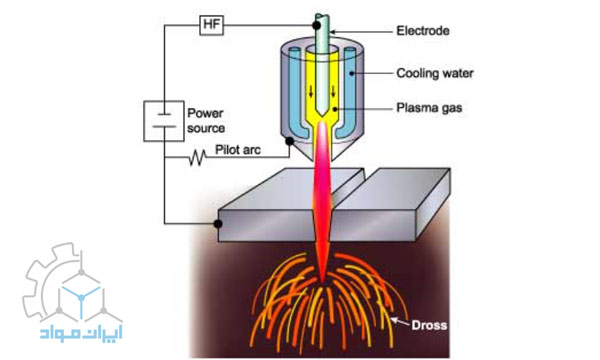
دمای پلاسما بیش از 20000 درجه سانتیگراد است که سرعت آن نزدیک به سرعت صوت است. هنگام برش، جریان پلاسما افزایش مییابد، طوریکه جت پلاسما با عمق نفوذ بالا از ماده عبور میکند و سرعت بالای آن مواد مذاب، درِ خروجی پلاسما را از سطح برش دور میکند.
این فرآیند با فرآیند اکسیدی Oxy-fuel متفاوت است. در فرآیند برش پلاسما ذوب ماده با استفاده از قوس انجام میگیرد درحالیکه در فرآیند اکسیدی، ابتدا اکسیداسیون فلز توسط اکسیژن رخ میدهد که در ادامه، گرمای حاصل از واکنش، منجر به ذوبشدن فلز میشود. بنابراین، برخلاف فرآیند اکسیدی، فرآیند برش پلاسما میتواند فلزاتی مانند فولاد زنگنزن، چدن و آلیاژهای غیرآهنی که در برابر اکسیداسیون مقاوم هستند، برش دهد. تجهیزات مختلفی در فرآیند برش پلاسما بهکار گرفته میشود که در ادامه در کنار اشاره به برخی از این تجهیزات به نکات مهمی هم در ارتباط با این فرآیند، پرداخته خواهد شد.
منبع تغذیه: منبع تغذیه موردنیاز برای برش پلاسما باید دارای افت و ولتاژ بالا باشد. ولتاژکاری برای حفظ پلاسما 50 تا v60 است که ولتاژ مدار باز موردنیاز برای شروع قوس میتواند تا v DC400 باشد.
در ابتدا، قوس پیلوت در داخل بدنه مشعل بین الکترود و نازل تشکیل میشود. برای برش لازم است که قوس ایجادشده بر روی قطعهی کار، انتقال یابد؛ درنهایت الکترود دارای قطب منفی و قطعه کار دارای قطب مثبت خواهد بود. بهاینترتیب بخش بزرگی از انرژی قوس در حدود دو سوم آن برای برش استفاده میشود.
ترکیب گاز: در سیستمهای معمولی تجهیزشده با الکترود تنگستن از گازهای آرگون، آرگونهیدروژن و یا نیتروژن برای تشکیل پلاسما استفاده میکنند. با این حال، از گازهای اکسیدکننده مانند هوا و یا اکسیژن نیز بهشرط استفاده از الکترود مسی با هافنیم (عنصر فلزی،Hf) میتوان استفاده کرد.
جریان گاز پلاسما ازجمله موارد حیاتی، هنگام برش است و باید مطابق سطح جریان و قطر نازل تنظیم شود. اگر جریان گاز پلاسما برای سطح جریان پایین باشد و یا سطح جریان برای قطر نازل بیش از حد بالا باشد، قوس به دو قوس تفکیک شده در الکترود-نازل و نازل-قطعهکار تجزیه شده که اثر قوس دوگانه با ذوبشدن نازل با فاجعه همراه خواهد شد.
کیفیت برش: کیفیت لبهی برش پلاسما مشابه فرآیند اکسیدی است. با این حال، همانطورکه در فرآیند پلاسما با ذوبشدن فلز، برش انجام میگیرد، در این شرایط انتقال حرارت بیشتر به سمت سطح بالای فلز است. بهعبارتدیگر، ذوب با سرعت بالا در قسمت بالایی فلز رخ میدهد که منجر به گرد شدن لبهی بالایی و مربعی شدن (چهارگوشهای) در لبه پایینی برش میشود.
از آنجاییکه این مسئله با درجه انقباض قوس ارتباط دارد برای بهبود انقباض قوس، از مشعلهای متعددی استفاده میشود که گرما بهطور یکنواخت در قسمت بالا و پایین برش توزیع شود.
پیشنهاد میکنیم:
تکنولوژی لیزرکات (برش لیزر)
لیزر کات یا برش لیزر یکی از فناوریهای جذاب و نسبتا جدید برشکاری است که به دلیل ...انواع فرآیندهای برش پلاسما
نحوهی عملکرد سیستمهای مختلف برش پلاسما به یک شکل انجام نمیگیرد و فرآیندهای متعددی برای بهبود کیفیت برش، پایداری قوس، کاهش نویز و افزایش سرعت برش تحت مکانیزمهای مختلف طراحی شدهاند.
گاز دوگانه (Dual gas)
این فرآیند اساسا به همان روش سیستم مرسوم برش پلاسما عمل میکند با این تفاوت که یک حفاظ گاز ثانویه در اطراف نازل قرار داده شده است. ازجمله مزیت حضور گاز ثانویه، افزایش انقباض قوس و دور کردن مواد ذوبشده از روی سطح برش است.
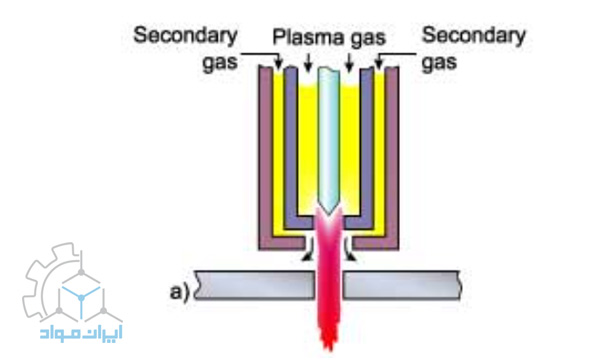
مزایای این روش در مقایسه با روش پلاسما مرسوم:
- کاهش خطر آتشسوزی ناشی از تشکیل قوس دوگانه
- سرعت برش بالا
- کاهش گرد شدن لبهی بالایی سطح برش
گاز تشکیلدهندهی پلاسما معمولا آرگون، آرگون-هیدروژن و یا نیتروژن است. گاز ثانویه با توجه به فلزی که برش داده میشود، انتخاب میشود.
ماده | نوع گاز |
فولاد | هوا/ اکسیژن/ نیتروژن |
آلومینیم | آرگون-هیدروژن/ نیتروژن/ کربندیاکسید |
فولاد زنگنزن | آرگون-هیدروژن/ نیتروژن/ کربندیاکسید |
تزریق آب (Water injection)
در این فرآیند نیتروژن بهطور معمول بهعنوان گاز پلاسما استفاده میشود. آب بهصورت شعاعی (تزریق گردابی) برای افزایش انقباض به قوس پلاسما تزریق میشود. دما نیز بهطور قابلتوجهی تا 30000 درجه سانتیگراد افزایش مییابد.
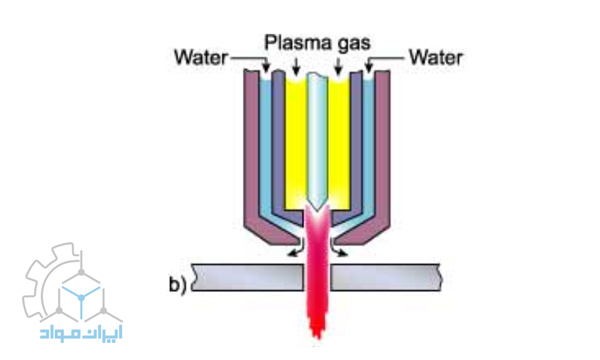
مزایای این روش در مقایسه با روش پلاسما مرسوم:
- بهبود کیفیت برش و عدم ایجاد ضایعات در زیر سطح برش
- افزایش سرعت برش
- کاهش خطر دوگانه شدن قوس
- کاهش خوردگی نازل
پیشنهاد میکنیم:
برش با جت آب - Water Jet Cutting
برش با جت آب – Water Jet Cutting برش با جت آب – Water Jet Cutting شر...پلاسما زیر آب (Water shroud)
برشکاری پلاسما میتواند در محیطی با پوشش آب نیز انجام شود. همچنین برای برش قطعه کار غوطهورشده تا 75 میلیمتر زیر سطح آب نیز مناسب است.
مزایای حضور آب در مقایسه با پلاسمای مرسوم:
- کاهش دود
- کاهش سروصدا
- افزایش عمر نازل
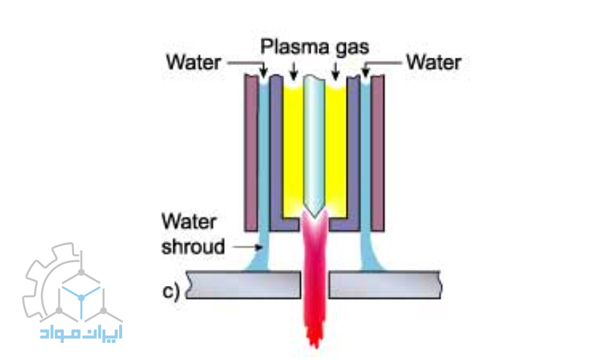
برای مثال، سروصدا حاصل از برش پلاسما مرسوم در حدود dB115، برش در محیطی با پوشش آب در حدود dB96 است در حالیکه سروصدا برش در زیر آب به 85 تا dB52 کاهش مییابد. از آنجاییکه این روش قادر به افزایش انقباض قوس تشکیلشده نیست بنابراین، لبهی برش و سرعت برش را نمیتواند بهطور قابلتوجهی بهبود دهد.
پلاسمای هوا (Air plasma)
گاز تشکیلدهندهی پلاسما، خنثی و یا عدم واکنشپذیر (آرگون و یا نیتروژن) میتواند با هوا جایگزین شود اما، در این شرایط نیاز به استفاده از الکترود خاص با هافنیم و یا زیرکونیم نصبشده در یک نگهدارندهی مسی است. هوا همچنین میتواند جایگزین آب برای خنک کردن مشعل شود. مزیت یک مشعل پلاسما هوا این است که از هوا بهجای گازهای گرانقیمت استفاده میشود. لازم به ذکر است اگرچه الکترود و نازل بعد از اتمام طول عمر مفید تعویض میشوند اما الکترودهای هافنیم در مقایسه با الکترودهای تنگستن گرانقیمت هستند.
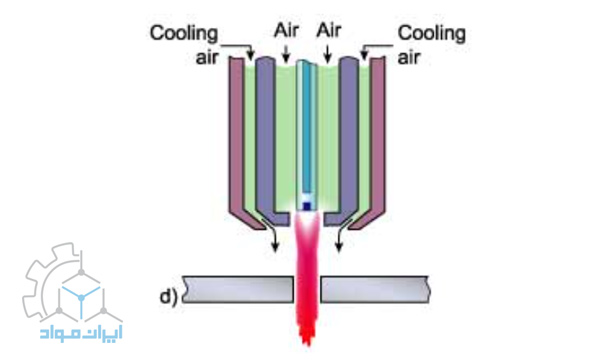
پلاسما با توان بالا (High tolerance plasma)
در تلاش برای بهبود کیفیت برش و رقابت با سیستم لیزری با کیفیت برش بالا، سیستمهای برش قوس پلاسمایی با توان بالا مورداستفاده قرار گرفتند. این روش با چرخش پلاسما تولیدشده، هنگام تزریق به روزنهی نازل عمل میکند و جریان گاز ثانویه در قسمت پایینی نازل برای حفظ چرخش، تزریق میشود. در برخی از سیستمها میدان مغناطیسی جداگانهای در اطراف قوس وجود دارند.
در تلاش برای بهبود کیفیت برش و رقابت با سیستم لیزری با کیفیت برش بالا، سیستمهای برش قوس پلاسمایی با توان بالا مورداستفاده قرار گرفتند. این روش با چرخش پلاسما تولیدشده، هنگام تزریق به روزنهی نازل عمل میکند و جریان گاز ثانویه در قسمت پایینی نازل برای حفظ چرخش، تزریق میشود. در برخی از سیستمها میدان مغناطیسی جداگانهای در اطراف قوس وجود دارند.
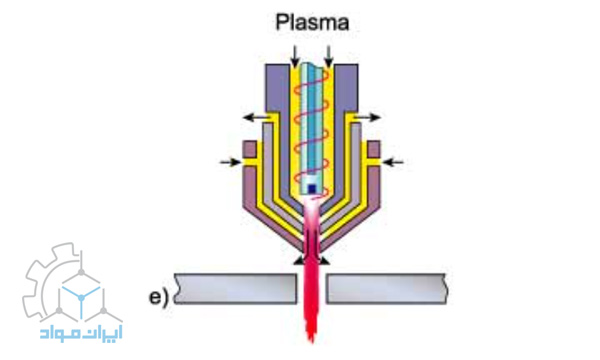
مزایای سیستمهای HTPAC عبارتند از:
- شیار برش کوچکتر
- دارای کیفیت برش بهتر نسبت به برش پلاسمای مرسوم و نزدیک به برش لیزری
- اعوجاج کم بهدلیل ناحیهی کوچک تحتتاثیر حرارت.
HTPAC یک روش مکانیزه است که نیازمند تجهیزات دقیق و سرعت بالا است. معایب اصلی این روش این است که حداکثر ضخامت قابل برش آن mm6 بوده و سرعت برش کمتر از فرآیند برش پلاسمای مرسوم و حدود 60 تا 80% کندتر از سرعت برش لیزری است.
گازهای مورداستفاده در برش پلاسما
نوع گاز مورداستفاده در برشکاری پلاسما به عواملی چون مواد و ضخامت برش و نوع روش برش بستگی دارد. این گاز علاوهبر اینکه پلاسمای موردنیاز برای برش را تولید میکند، به دور کردن مواد مذاب و اکسید از سطح برش کمککننده است. در ادامه به واکاوی رایجترین گازهای مورداستفاده برای برش پلاسما میپردازیم.
1- آرگون (Ar)
آرگون گازی خنثی با قوس پلاسما پایدار است. منظور از پایداری گاز آرگون، عدم واکنشپذیری این گاز با فلزات در دماهای بالا است. الکترودها و نازلهای مورداستفاده برای برش گاز آرگون اغلب عمر مفید طولانیتری نسبت به گازهای دیگر دارند.
گاز آرگون بهدلیل قوس پلاسمایی کم و آنتالپی آن، هنگام برش محدودیتهایی دارند. علاوهبر این در برش با گاز آرگون مشکلات سربارهای وجود دارد که این مسئله در وهلهی اول بهدلیل کشش سطحی مذاب بوده که تقریبا 30% بیشتر از کشش سطحی موجود در محیط نیتروژن است. این مشکلات ازجمله دلایلی است که باعث استفاده بسیارکم از آرگون در برش پلاسما میشود.
2- نیتروژن (N2)
نیتروژن، پایداری قوس پلاسمایی بهتر و جریان انرژی بالاتری بهخصوص با منبع ولتاژ بالا نسبت به آرگون دارد. در استفاده از نیتروژن حداقل سرباره در لبههای پایینی برش تشکیل میشود، حتی در برش فلزاتی مانند آلیاژ پایه نیکل و فولاد زنگنزن که ویسکوزیته بالایی دارند. نیتروژن میتواند بهعنوان یک گاز مستقل و یا در ترکیب با گازهای دیگر در فرآیند برش پلاسما استفاده شود.
3- هوا
هوا دارای 78% حجمی نیتروژن و 21% حجمی اکسیژن است که آن را به گاز مناسبی برای برش پلاسما تبدیل میکند. اکسیژن موجود در هوا آن را به گاز با سرعت برش بالا در برش فولاد کم کربن تبدیل کرده است. گفتنی است که بهدلیل در دسترس بودن هوا، این گزینه از جنبهی اقتصادی مطلوبی هم برخوردار است. در مقابل، الکترود و نازلهای مورداستفاده برای این فرآیند تحت این گاز عمر مفید کوتاهی دارند، درنتیجه باعث افزایش هزینهها و کاهش کارایی میشوند. البته توجه به این نکته حائز اهمیت است که برخلاف نیتروژن استفاده از هوا بهعنوان گاز مستقل با مشکلاتی ازجمله معلق ماندن سرباره و اکسیداسیون سطح برش همراه است.
4- اکسیژن (O2)
مانند هوا، اکسیژن نیز سرعت برش فولاد کم کربن را افزایش میدهد با این حال، بهتر است که از الکترودهای مقاوم به اکسیداسیون و دما بالا در برش تحت گاز اکسیژن استفاده شوند.
5- هیدروژن (H2)
هیدروژن بهعنوان گاز کمکی در ترکیب با دیگر گازهای پلاسمایی استفاده میشود. یکی از رایجترین این گازها، ترکیب گاز هیدروژن با آرگون است که منجر به تولید گازی قدرتمند در برش پلاسما میشود. ترکیب گاز هیدروژن با گاز آرگون بهطور قابلتوجهی ولتاژ قوس، آنتالپی و قدرت برش جریان پلاسمای آرگون را افزایش میدهد.
برخی دیگر از گازهایی که اغلب در برش پلاسما به کار میروند در جدول زیر بیان شده است؛ این جدول حاوی اطلاعاتی از مشخصات و خصوصیات آنها است.
ضخامت قابل برش | گاز | گاز کمکی (ثانویه) | ملاحظات |
فولاد ساختمانی 0.5 تا 8mm | اکسیژن | اکسیژن-نیتروژن/ اکسیژن/ نیتروژن | عاری از ضایعات و کیفیت برش مشابه برش لیزری |
فولاد ساختمانی 4 تا 50mm | اکسیژن | اکسیژن-نیتروژن/ اکسیژن/ هوا | عاری از ضایعات برش تا 20mm، سطح برش یکنواخت، مقاومت تا 25mm در برابر چهارگوشهای شدن لبه برش |
فولاد پر آلیاژ 5 تا 45mm | آرگون/ هیدروژن/ نیتروژن | نیتروژن/ نیتروژن-هیدروژن | عاری از ضایعات برش تا 20mm، سطح برش یکنواخت، مقاومت کم در برابر چهارگوشهایشدن لبه برش |
آلومینیم 1 تا 60mm | هوا فشرده | نیتروژن/ نیتروژن-هیدروژن | عاری از ضایعات برش، سطح برش ناهموار یا دانهدار، امکان برش عمودی |
آلومینیم 5 تا 40mm | آرگون/ هیدروژن/ نیتروژن | نیتروژن/ نیتروژن- هیدروژن | عاری از ضایعات برش تا 20mm، سطح برش ناهموار، امکان برش عمودی |
مواد قابلبرش در فرآیند برش پلاسما
فرآیند برش پلاسما قابلیت برش مواد مختلف را دارد به این دلیل که این فرآیند قادر به برش هر ماده رسانایی است. در ادامه برخی از متداولترین مواد برای این روش آورده شده است.
1. آلومینیم
آلومینیم فلز رسانایی است لذا، انجام فرآیند برش پلاسما را برای ساخت آن مناسب میکند. این فرآیند در مقایسه با دیگر روشها مانند برش لیزری قادر به برش آلومینیم در ضخامت بالا را دارد. این روش میتواند آلومینیم را تا ضخامت mm160 برش دهد. همچنین بهدلیل هزینهی برش و تجهیزات کم، روش مذکور برای آلومینیم دارای صرفهی اقتصادی است.
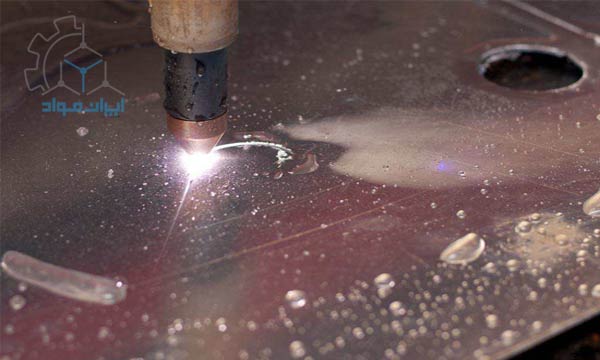
2. فولاد معمولی
فولاد معمولی (mild steel) یک نوع فولاد با درصد کربن پایین است که بیشترین مقدار آن 2.1% کربن است. این فولاد بهدلیل خواص مطلوب مانند استحکام ضربه بالا، قابلیت جوشکاری و انعطافپذیری و قیمت ارزان یکی از رایجترین فرمهای فولاد است.

3. فولاد زنگنزن
فولاد زنگنزن از آلیاژهای آهن است که مقاومت در برابر خوردگی و زنگزدگی را دارد. برش پلاسما یکی از روشهای کارآمد برای برش این فلز است که ضخامت برش تحت این فرآیند برای فولاد مذکور میتواند به ضخامت برش mm30 برسد. ازجمله گریدهای مختلف فولاد زنگنزن مناسب برای این روش عبارتند از: 304/ L304/ 316/ L316/ 321/ s310 و 317.
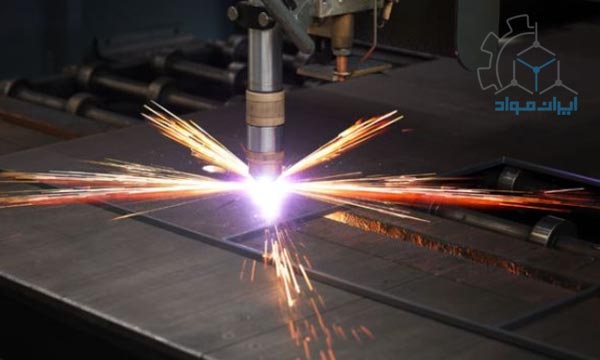
4. برنج
برنج فلز دیگری است که بهدلیل ماهیت رسانایی بالا بهآسانی میتوان با استفاده از برش پلاسما آن را برش داد. با این حال، به این دلیل که برنج دارای روی است و استنشاق دود سوختن روی برای سلامتی مضر بوده، بهتر است در محیطی با تهویه مناسب برش فلز برنج انجام شود.
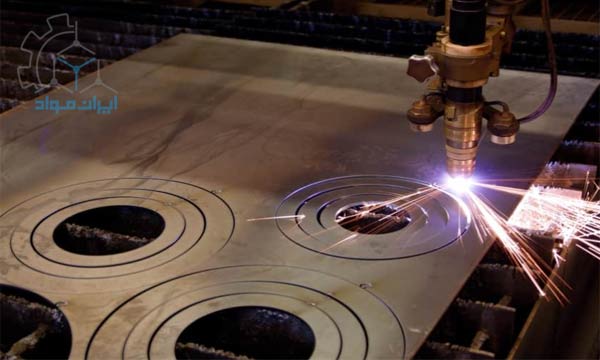
5. مس
مس از هدایت حرارتی و الکتریکی خوبی برخوردار است. همچنین دارای خواصی مانند مقاومت در برابر خوردگی، شکلپذیری بالا و قابلیت جوشکاری است. این خواص در کنار رسانایی بالای آن، مس را به یک فلز ایدهآل برای برش پلاسما تبدیل کرده است. با این حال، همانند برنج این فلز نیز در محیطهایی با تهویه مناسب باید برش داده شود.
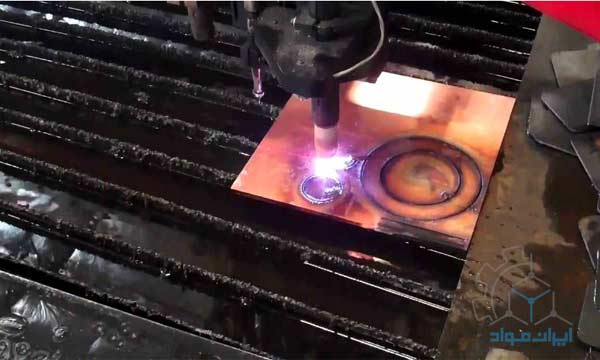
6. چدن
چدن به ارزان و انعطافپذیربودن شناخته میشود و حاوی عناصری مانند منگنز، سولفور، فسفر و سیلیکون است. چدن رسانا بوده و استحکام فشاری بالا و دمای ذوب پایین آن، این فلز را برای برشکاری پلاسما مطلوب کرده است.
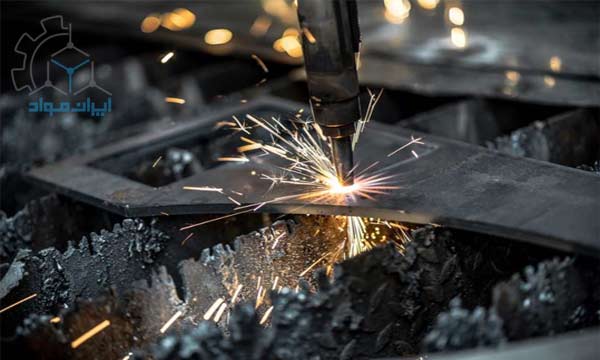
مزایای برش پلاسما
چندین مزیت در استفاده از برش پلاسما نسبت به روشهای دیگر وجود دارد که در شکل زیر، بهطور مبسوط به آن پرداختهایم.
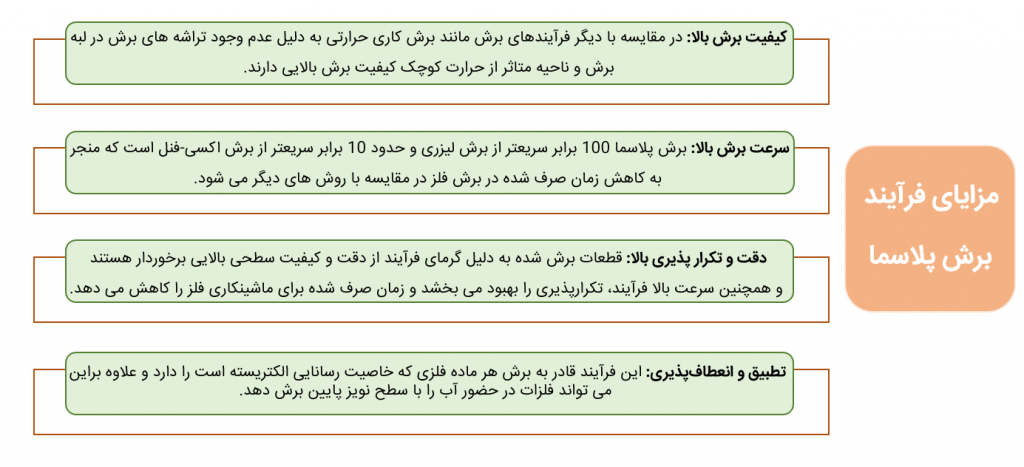
معایب برش پلاسما
اگرچه مزایای زیادی برای برش فلزات با استفاده از این فرآیند وجود دارد، اما این روش معایبی هم دارد که باید در استفاده از آن، درنظر گرفته شود.
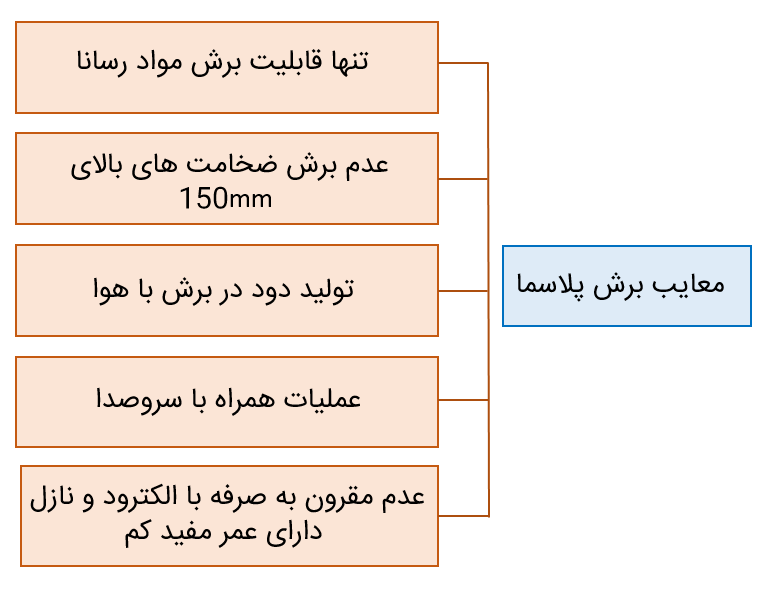
جمعبندی
برش پلاسما فرآیندی است که با استفاده از حالت چهارم ماده یعنی پلاسما، مواد رسانا را برش میدهد. در جهت بهبود کیفیت و افزایش سرعت برش، برش پلاسما در انواع گوناگونی انجام میشود که در تمامی سیستمهای مختلف، پلاسما از طریق گاز خارج شده از نازل و تماس آن با قطعه کار تشکیل میشود. این فرآیند مزایای بسیاری ازجمله کارآیی بالا، کیفیت برش و دقت بالا را دارد و بهدلیل قابلیت برش مواد رسانا طیف گستردهای از فلزات را میتوان بهکمک این روش برش داد. در این نوشتار تلاش کردیم که هرآنچه که دربارهی این نوع برش برای خواننده سوال بوده و نیاز به دانستن آن داشته را مطرح و تشریح کنیم.
دیدگاه کاربران