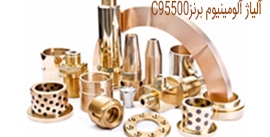
آنالیز خستگی و اجزای جوشکاری شده (E.Niemi)
Farigue Analysis of welded components
E.Niemi
شرح:
جوشکاری یکی از روشهای تولید میباشد. هدف آن اتصال دایمی مواد مهندسی (فلز، سرامیک، پلیمر، کامپوزیت) به یکدیگر است به گونهای که خواص اتصال برابر خواص ماده پایه باشد. دستهای از فرآیندهای جوشکاری هستند که در آنها، عمل جوشکاری بدون ذوب شدن لبهها انجام میشود. در واقع لبهها تحت فشار با حرارت یا بدون حرارت در همدیگر له میشوند. فرآیندهای این گروه عبارتاند از: ـ جوشکاری اصطکاکی ـ جوشکاری نفوذی ـ جوشکاری با امواج مافوق صوت. جوشکاری همچنین یکی از فرایندهای اتصال دائمی قطعات (فلزی یا غیرفلزی)، به روش ذوبی یا غیر ذوبی، با بکارگیری یا بدون بکارگیری فشار، با استفاده یا بدون استفاده از ماده پرکننده میباشد. فرایندهای جوشکاری به دو دسته اصلی تقسیم میشوند: فرایندهای جوشکاری ذوبی و فرایندهای جوشکاری غیر ذوبی روشهای متداول جوشکاری که هماکنون برای اتصال قطعات مختلف به کار میروند، از سه هزار سال پیش از میلاد شناخته شده بودند. تا قرن نوزدهم تنها روش اتصال قطعات به یکدیگر، روش فورجینگ (آهنگری) بود تا اینکه با پیدایش باطریهای الکتریکی، ژنراتورها و استفاده از اکسیژن و استیلن، فرایند جوشکاری به روش ذوبی اختراع شد و تاکنون با ابداع روشهای نوین جوشکاری پیشرفتهای زیادی در این زمینه صورت گرفته است که از آن جمله میتوان به جوشکاری قوسی بافلاکس محافظ، جوشکاری با پرتو الکترونها و جوشکاری با لیزر اشاره کرد. جوشکاری تحت پوشش گازهای محافظ با الکترود تنگستن یک فرآیند جوشکاری قوسی می باشد که قوس بین الکترود تنگستنی ( مصرف نشدنی ) و حوضچه مذاب پدید می آید. این فرآیند جوشکاری با گاز محافظ و بدون کاربرد فشار صورت می گیرد. جوشکاری قوس تنگستنی را می توان با اضافه کردن فلز پرکننده و یا بدون آن بکار برد. نام دیگر این فرآیند جوشکاری TIG ( جوشکاری تیگ ) می باشد. در این فرآیند هیچ گونه سرباره ای وجود ندارد ، بنابراین لازم است که هم الکترود ، هم سطح قطعه و هم فلز پر کننده توسط گاز محافظ پوشش داده شوند تا از آلودگی آن ها جلوگیری گردد.خستگی فلزات (Metals Fatigue) وقتی اتفاق می افتد که فلز تحت تنش تکراری یا نوسانی قرار گیرد که منجر به شکست ناگهانی قطعه می گردد. با پیشرفت صنعت و افزایش تعداد وسایلی از قبیل خودرو، هواپیما، کمپرسور، پمپ توربین و غیره که تحت بارگذاری تکراری و ارتعاشی هستند، خستگی بیشتر متداول شده و اکنون چنین برداشت می شود که عامل حداقل ۹۰ درصد شکست های ناشی از دلایل مکانیکی حین کار، خستگی باشد. به طور کلی شکست هایی که در شرایط بارگذاری دینامیک رخ می دهند، شکست های خستگی نامیده می شوند. هیچگونه تغییر واضحی در ساختار فلزی که به علت خستگی می شکند، وجود ندارد تا بتوان به عنوان مدرکی برای شناخت دلایل خستگی از آن استفاده کرد. دلیل عمده خطرناک بودن شکست خستگی این است که بدون آگاهی قبلی و قابل رویت بودن اتفاق می افتد. خستگی به صورت شکستی با ظاهر ترد، بدون هیچگونه تغییر شکل ناخالص در شکست، نتیجه می شود. معمولاً شکست خستگی از ظاهر سطح شکست تشخیص داده می شود، که از یک ناحیه همواره حاصل از عمل سایش با اشاعه ترک در مقطع و یک ناحیه ناهموار که در هنگام عدم تحمل بار توسط مقطع، در قطعه به صورت نرم شکسته شده است، تشکیل می شود. غالباً پیشرفت شکست توسط یک دسته حلقه نشان داده می شود، که از نقطه شروع شکست به طرف داخل پیشرفت می کند.
قالب بندی:pdf
تعداد صفحات :۵۶
حجم :۳٫۹۴MB
دیدگاه کاربران